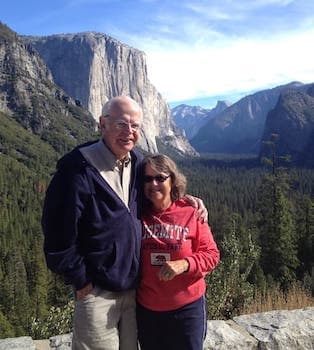
Curated with aloha by
Ted Mooney, P.E. RET
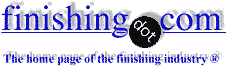
The authoritative public forum
for Metal Finishing 1989-2025
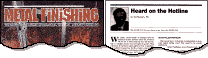
-----
Copper pyrophosphate plating bath Q&A's
Q. Copper Pyrophosphate Delaminating from Strike
Hi Everyone, I am having some difficulties with my copper pyrophosphate automated copper plating line. The parts plated are high grade aerospace materials.
On around 10% of the components that are plated using the line we are witnessing separation between the strike and plate layers on the components after they have been stoved at 195 °C for 2 hours.
We have tried disposing of all of the rinsing baths between the strike bath and the plating baths as well as replacing the sulfuric acid dip we use prior to plating but there are still issues with plate peeling from the strike. We most recently tried replacing the strike bath this weekend just gone but we have still had problems. We have also given all of our tooling and plating stations a good thorough clean on all contact points.
There is no consistent pattern on day of the week, tooling used, size of component, plating bath the parts have gone in. Although certain part numbers do seem to be more consistently affected. Has anyone got nay suggestions for anything else I can try to get to the root cause of the problem?
Thanks,
Andrew
Andrew Amor
- Yeovil, England
A. Sounds like the copper is getting passive and you need to activate the surface. You should look at a mild copper etch after the copper and before the next plating solution.
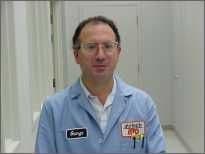
George Shahin
Atotech - Rock Hill, South Carolina
April 28, 2021
April 29, 2021
Hi George,
Thank you for the advise. We do currently use a sulfuric acid dip between striking and plating which has always historically worked successfully.
As an update we were able to isolate the problem as being caused by our internal plating anodes. We are currently trying to work out what about them is causing this to take place as they have been recently calibrated.
Thanks,
Andrew
- Yeovil England
April 15, 2021
⇩ Related postings, oldest first ⇩
Current efficiency of copper pyrophosphate plating
Q. I have a question regarding current efficiency of copper pyrophosphate bath. From literature, the efficiency should be 100%. I got a commercial bath and tried to measure its current efficiency using a pre-weighed copper foil. The c.d. was 20 mA/cm2. The temp of the bath was 50 °C. From the weight difference before and after plating, the calculated efficiency was only 74%. If this number were true, I would see bubbles out from the cathode. I did several tests and got same results. I can not figure out what the problem is. I also tested the current efficiency of one commercial acid copper bath using the same method. The result was close 100%. Any suggestions would be appreciated.
Mark Chang- Torrance, California, USA
2000
A. 74% is actually pretty good for Pyro.
"Current efficiency" includes two terms. Anode efficiency and Cathode efficiency. Instead of Hydrogen at the cathode you may see Oxygen at the anode.
For good operation you should see neither.
In many solutions (Electroless Copper comes to mind) gases like Hydrogen can bump around in solution for a while before bubbles begin to form.
PWBs - Alberta Canada
2004
A. We, too, have recently checked the cathode efficiency of a pyrophosphate copper bath, and found it to be close to 80%. We are also noticing an increase in the specific gravity of the solution, that may indicate that the copper concentration in it is rising due to the difference between the anode (presumably 100%) and cathode efficiencies.
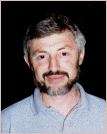

"PlaterB" Berl Stein
NiCoForm, Inc.

Rochester, New York
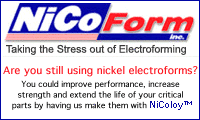
December 9, 2010
RFQ: I would need to know the name/web-site of copper pyrophosphate manufacturers in Europe /USA
Tassanee Na Ranong- Bangkok, Thailand
2005
Ed. note: This RFQ is outdated, but technical replies are welcome, and readers are encouraged to post their own RFQs. But no public commercial suggestions please ( huh? why?).
Copper pyrophosphate or non-cyanide copper as heat treatment maskant
Q. I am looking for information about non-cyanide copper plating for use as a heat treat maskant and / or info on a an alternative non-hazardous maskant for heat treat applications (i.e., selective carburization, nitriding). Anyone who can help or point me in the right direction would be greatly appreciated.
Thanks,
helicopters - Haltom City, Texas
2003
A. Copper pyrophosphate and proprietary baths are probably the only cyanide-free approaches.
adv.
Finishing.com's supporting advertiser EPI / Electrochemical Products Inc. [a finishing.com supporting advertiser] is one supplier.
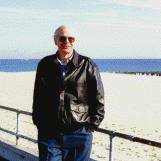
Ted Mooney, P.E.
Striving to live Aloha
finishing.com - Pine Beach, New Jersey
2003
2003
A. Pyrophosphate copper :
copper pyrophosphate.......... 110 gm
potassium pyrophosphate...... 400 gm
citric acid
⇦ this on
eBay
or
Amazon [affil links] .................. 10 gm
water........................1 lit
pH 8,5 -temp.50 C, 5 A/dm2
Tartaric copper (19.century):
add copper carbonate
⇦ this on
eBay
or
Amazon [affil links]
to solution of potassium tartrate( 100 gm/lit.water), until some carbonate remained undissolved, then add potassium carbonate to pH 10
- Cerovski vrh Croatia
A. A variety of alkaline non-cyanide copper baths are available from suppliers. Each manufacturer has baths with different properties in plating or waste treatment. Pyrophosphate baths are outdated technology unless you are trying for a "home brew".
Gene Packmanprocess supplier - Great Neck, New York
2003
A. You can use ceramic or enamel coating [as heat treatment maskant].
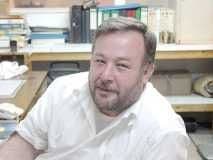
Khair Shishani
aircraft maintenance - Al Ain, UAE
2004
How to remove iron from copper pyrophosphate plating bath
Q. How do I go about removing iron from a copper pyro electroplating bath?
Kory Rodenhiser- Bridgewater,NS, Canada
August 19, 2014
A. I don't think that there is a practical method to remove iron from a copper pyrophosphate bath. In many years of involvement with copper pyro I can't recall a problem cause by iron. Except that it is important to allow sufficient potassium pyrophosphate to complex the iron as well as the copper. Think in terms of total metal: pyrophosphate rather than just copper.
May I ask what problems you have?
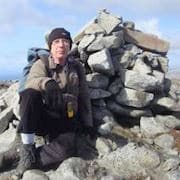
Harry Parkes
- Birmingham, UK
September 9, 2014
Q, A, or Comment on THIS thread -or- Start a NEW Thread