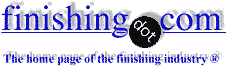
-----
Zinc manganese plating and electrodeposition of other manganese alloys
Q. Hi, I would like to know if it is possible to electroplate any of the following alloys, NiMn, FeMn, PtMn, and if so where do I get the baths from? Jim
James McGrath- Cork, Ireland
1999
1999
A. There is not to much info in the literature on those alloys you want to plate. The one reference I have is Brenner's Electrodeposition of Alloys vol. 2 lists some of the electrolytes used to produce MnNi, MnCo and MnCu. These were mostly simple salt solutions of the metals, usually sulphate.
If you do not have access to this publication I could send you the formulas listed in this book.
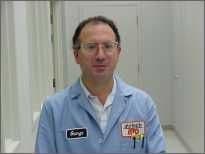
George Shahin
Atotech - Rock Hill, South Carolina
2004
A. Dear Jim,
NiMn, FeMn, are depositable from either a simple salt bath or from a complex salt bath at wide ranges of pH and temperature, preferably room temperature. They can be electroplated, or electrolessly plated from a sulphate or phosphate bath of one's formulation.
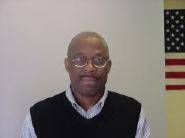
Bassey J. Udofot
Musgegon, Michigan
Multiple threads merged: please forgive chronology errors and repetition 🙂
Q. I'm an electrochemical consultant for several job platers.I'm interested in alloy Zn/Mn electroplating.I need to know the state of art of it.
Thank you
Mauro C [last name deleted for privacy by Editor]- Italy
2000
A. Several papers exist on the subject of Zinc/Manganese alloy plating. The idea is sound, and that alloy will give excellent galvanic protection to steel parts. The problem has been the variable valences of the element Manganese.
When someone finally finds a way to stabilize the valences in a plating bath, this system may find its way into use. Lab tests have been successful in plating this alloy, but under controlled laboratory conditions, such things are possible. Only when we go from the lab to the plating shop, do we really see what these baths are truly worth.
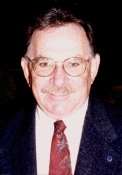

Ed Budman [dec]
- Pennsylvania
With deep sadness we advise that our good friend Ed passed away Nov. 24, 2018
2000
A. Zinc-manganese and other hard to deposit Manganese alloy films have been successfully deposited a stable gamma phase solid solution. The work has been patented and cannot be revealed for free use by the public but for technology transfer it is ready for licensing and commercialization.
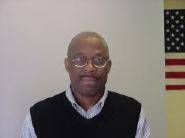
Bassey J. Udofot
Musgegon, Michigan
2003
Q. What are the concentrations and pH of the bath to deposit FeMn in the proportion around 50/50 (Fe50Mn50)? I have tried common sulphate solutions, as Mr. Udofot suggested, and the Fe composition is always much greater than that of Mn. Ex: Fe93Mn7.
José Gomes Filho- Rio de Janeiro, BR
2007
January 8, 2009
A. Dear Readers and Mr. Gomes,
As I have already demonstrated, Fe and Mn intermediate composition in alloy films of Fe-Mn are depositable from a simple salt bath without the use of complexant or metalloids. The reason you have found-deposition of Fe more than the Mn is of great interest and and has been found to cause discrepancies in the published work of other Research Scientist as published in the Abner Brenner's text volume 1 and 2. It has been generally believed that in alloy films, the more noble metal deposits preferentially than the less noble metals. If the reverse occurred, it is often explained as anomalous reaction. In simultaneously depositing of Fe and Mn from a simple sulphate or chloride salt baths, the maximum at wt % Mn that codeposited with the Fe as ductile Fe-Mn alloy films was 13 wt%. As either the pH or temperature of the bath increases, the wt % Mn codepositing with the Fe decreases whilst the Fe continues to increase in the deposition. As the temperature of the bath reaches 80° C., Mn ceases to co-deposit and only the Fe deposits as a dark, coherent, hard, magnetic ferri-ferrous iron oxide film. Similarly from a simple salt bath at pH 11.5, room temperature, only Fe deposited as bright Fe oxide film, on a substrate. intermediate composition of Fe and Mn occurred from bath of pH 1 to 2 at room or near rooms temperature ranges. The key to depositing the intermediate composition is based from good knowledge of the two materials behavior from the aqueous solution environment and their diffusion rates. Electrodeposition of Fe-Mn alloys containing P and nitrate salt from bath at pH 1.5, 50 ° C., will deposit 50 at wt % Mn and 29 at wt% Fe and the rest P. Similarly, in Fe-Ni alloy electrodeposition, Fe being the less noble metal than Ni, deposits more than the Ni. Therefore, it is not the question of nobility or lack of it that determine the preferential deposition of a metal. It has to do with freedom with which metal looses its electron to deposit on a cathode. The ability of the ionized metal to overcome the influences of Oxygen and OH- ions across the diffusion layer,to deposited on a substrate that determines thermodynamically the at wt. % metal deposition in an alloy films from bath.
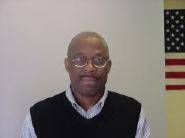
Bassey J. Udofot
Musgegon, Michigan
Electroplating Manganese on Cobalt for Conversion Coating Applications
October 18, 2011Q. First off, I am already indebted to you folks because most of my questions were answered via a search of the site. However I have a couple left, one practical and one more abstract.
I am working with the degradation of solid oxide fuel cells for my graduate work, and a key way they usually fail is the interconnects, which electrically connect individual cells together, corrode away. This kills both the conductivity, and poisons the catalyst. To fix this coatings are generally applied, and in true academic fashion this is often performed using completely non-industrial methods. However, more recently people have begun to look at coatings that can actually be performed in a job shop. More specifically electroplated CoMn coatings that convert to a dense, conductive oxide.
I'd like to study the transition between the electroplated metallic coating and the converted oxide coating. To do that I need to electroplate Co and Mn. Electroplating the alloy seems to be tied up in patents, so my intention is to plate the layers, and use a reducing furnace to diffuse the metals together and then begin investigating the conversion process.
My practical problem is this: I cannot get the manganese to stick, cobalt was no problem. But try as I might, no manganese will stick to the cobalt layer. The recipe I used is below. I know that manganese is a tough one, but is there a book I should get, a recipe to try, or any other direction to go?
Recipe:
150 g/l ammonium sulphate
⇦ on
eBay or
Amazon [affil links]
200 g/l Manganese sulphate
Sulfuric acid added to pH 3
Balance Distilled water
Temp: ~25-30 C
Current density: 30mA/cm up to 250 mA/cm
My abstract question is this: What does "activation" do in the electroplating process. As I understand it, the surface must be cleaned, the surface oxide must be removed, and then there is a mystery step of "activation." What exactly is happening here.
Thanks in advance, I can answer any more questions if necessary.
Graduate Student - Troy, New York, USA
A. Look on page 469 of "Modern Electroplating" edited by Lowenheim
[on
AbeBooks,
eBay, or
Amazon affil links]
.
This page is from the 3rd edition.
It has a reference among others for plating nickel-manganese alloy.
Cobalt and nickel are nearly identical so you can substitute cobalt for nickel interchangeably.
It is a source book for plating references.
- Navarre, Florida
October 19, 2011
I have looked at Modern Electroplating, and the recipes they give are based from the ones in Brenner's book "Electrodeposition of Alloys" which I have also looked through. The key differences I found were the that the NiMn baths were run at a neutral pH and the CoMn baths tended to be at a very low pH. However, Brenner discussed that most of these baths do not work very well.
After spending a great deal of time working through Brenners book, and others I have been able to get CoMn to codeposit, using a sulphate/citrate based solution similar to those shown in Brenners book, acetic acid
⇦ on
eBay
or
Amazon [affil links] for pH control, and a carbon electrode. At this point I'm working to improve the composition control and reduce the amount of hydroxide and oxides present in the coating. Metallic Co seems to plate out nicely whereas the codeposited metal often includes a large amount of oxides. Hopefully, better pH control, better solution mixing, and current control will fix these problems. Thanks for the all help I appreciate it
- Troy, New York, USA
November 1, 2011
Q. Hi,
in electrodeposition of NiMn alloy sulphate single bath, what
concentration of each element is needed to get 50% of Ni and Mn?
Regards
- Tebessa, Algeria
June 12, 2012
A. My use of Cyclic Voltammetry to study metal alloy deposition shows that, thermodynamically, Mn can co-deposit with Ni at a negative cathode potential of -1.18 electron volt, nearer that of Mn to form Ni-Mn alloy having a non-equilibrium at weight composition. As the depositing potential of the system became less negative, more Ni than Mn was found to deposit at a potential of -0.25 electrode volt. However, for kinetic reason, particularly because of their cathode potential difference and tenacious oxide stability on their surfaces, alloy co-deposition of intermediate composition of 50 % weight Mn with 50% weight Ni is not possible. The only method to co-deposit Mn and Ni from aqueous solution of simple salt is to add increased concentration of Phosphate in the Nickel-Mn salt bath. More P concentration in the bath, more Mn and Nickel close to 50 % at wt %, each would co-deposit as an alloy of Mn-Ni film. Alternatively, the two metals when dissolved and ionized to diffuse to deposit at the same speed, Ni will inhibit Mn and itself deposit preferentially a chosen target than Mn unless their accelerations to reach the intended target are controlled. Controlling their rate of acceleration to diffuse to their depositing target will ensure intermediate at weight composition of the Mn-Ni alloy films.
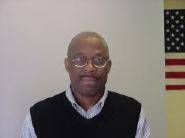
Bassey J. Udofot
Musgegon, Michigan
December 15, 2012
Q. Hello
I was wondering if anyone has any experience or suggestions for electroplating the Heusler alloy Ni2MnGa? I have been thinking of electrodepositing this alloy from a common bath, any advice?
- Zurich, Switzerland
September 11, 2013
Electrodeposition of Manganese nanowire
Q. Hello gentlemen,
My name is fatemeh, I am an undergraduate student, and I currently did an experiment about preparation of Fe_Mn nanowires and am studying the effect of Mn addition on their magnetic properties.
But I have a problem: result of edx showed with addition Mn (80%) and Fe (20%) in solution just 4.5% of Mn was electroplated on nanowires (Fe_Mn).
I know voltage of Mn (_1.14V) < Fe (_.04V)
Could you help me how I overcome this problem? I need to electroplate a higher percentage of manganese in the nanowire.
Thank you so much, I really appreciate your answer.
fatemeh ranabi- hamedan, iran
September 23, 2019
----
Ed. note: Readers may also be interested in topic 28617 "Manganese Electroplating"
Q, A, or Comment on THIS thread -or- Start a NEW Thread