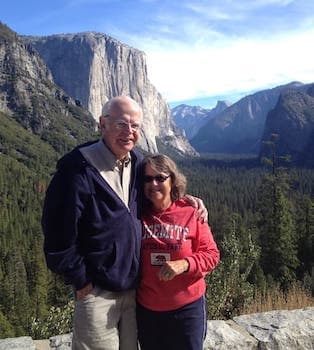
Curated with aloha by
Ted Mooney, P.E. RET
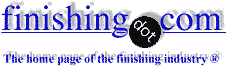
The authoritative public forum
for Metal Finishing 1989-2025
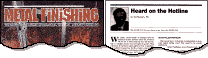
-----
Passivation of Stainless Steel
In my company we are planning to perform a passivation (with citric acid solution)of water system pipes. Could anyone suggest a method (with details, if possible) used to evaluate whether the passivation is complete.
My company is planning to passivate the piping of pharmaceutical purified water distribution system.
Thank you,
Iveta Vilcane- Riga, Latvia
Iveta:
You should download ASTM A967. This will give you many of the test methods for passivation. For help in Europe you may want to contact MKK GmbH in Germany. They can tell you the best procedures.
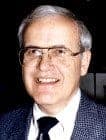

Lee Kremer
Stellar Solutions, Inc.

McHenry, Illinois
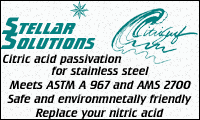
I need to know how I can do the passivation of the stainless steel (304, 316, 316L, etc). Thank you.
Albert Garcia- Barcelona, Spain
2000
2000
Your question is a bit too general, Mr. Garcia. There are MIL specs (QQ-P-35C [from DLA] ), ASTM specs (ASTM A967), AMS specs (QQ-P-35C (canceled) [link is to free spec at Defense Logistics Agency, dla.mil]) and other specs. The traditional nitric-acid based processes are sometimes being supplanted by newer citric acid passivation processes offered by Stellar Solutions [a finishing.com supporting advertiser], and electrolytic passivation processes offered by Global Stainless Technology, and by electropolishing.
A good starting point could be our FAQS on the subject. Good luck.
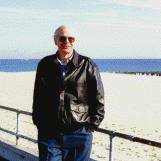
Ted Mooney, P.E.
Striving to live Aloha
finishing.com - Pine Beach, New Jersey
Albert:
We manufacture excellent and safe chemistry for your application. We manufacture in Germany, and can have our representatives there contact you if you need help.
Please contact us by email.
Regards,
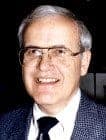

Lee Kremer
Stellar Solutions, Inc.

McHenry, Illinois
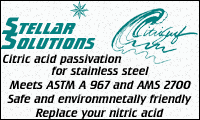
2000
Thought everyone may be interested in this article from Modern Machine Shop magazine. It is about passivation of stainless steel, a confusing subject.
http://www.mmsonline.com/articles/100304.html
We braze 304L stainless steel assemblies. The braze furnace is run at around 2000 degrees F, and has a highly reducing atmosphere. Any protective oxides are wiped out in this process. We have data that shows a brazed stainless part will show a lot more rust in salt spray than stainless before braze. This is normal, and does not usually cause problems, but recently we've had rejections for rust on production parts. We've been looking into this and think moisture in our dunnage may be at fault. In our research, we also found the above article. Any comments?

Tim Neveau
Rochester Hills, Michigan
2003

this text gets replaced with bannerText
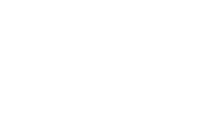
Q, A, or Comment on THIS thread -or- Start a NEW Thread