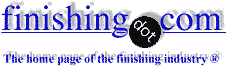
-----
Need help on hard chrome plating

Quickstart:
'Hard Chrome' means a thick, wear-resistant plating of chrome, usually directly onto the substrate, rather than the very thin layer of chrome over nickel plating which is typical of decorative chrome plating applications. Readers may wish to review our "Chrome Plating Introduction & FAQS".
Q. I have a problem in the hard chrome process, specifically trying to apply this process on crankshafts.
1.- I don't get the thickness that I need.
2.- there are areas in the crankshaft that have shadows.
3.- there are little holes in the deposition.
Please help me (sorry about the English).
Regards,
general manager - SANTA CRUZ, BOLIVIA
2004
A. I think that conforming anodes is the only way to get uniform coverage on crankshafts. It also allows faster plating because of the closer anode to cathode spacing. Done with great care, you can nearly plate to size, reducing the grind time and cost.
James Watts- Navarre, Florida
1. I agree, conforming anodes are the way to go. You will find if designed correctly, the thickness distribution will be a lot more even, reducing subsequent grind time.
2. Again, conforming anodes will solve this.
3. The porosity in the deposit can be attributed to probably one or a combination of 3 things:
- if the crankshafts are cast iron, it is inherently porous, allowing ingression of pretreatment chemicals that seep out during plating, contaminating the surface, and not allowing the plating to adhere.
- lack of circulation in the bath. The solution should be circulated over the job constantly.
- poor precleaning technique. Use a reverse etch of sulfuric/hydrofluoric acid (30 g/l ammonium bifluoride, 450 g/l sulfuric acid) before transferring to the chrome bath. A black smutty surface should appear on the parts if reverse etched correctly.
Aircraft component manufacturer - Melbourne, Victoria, Australia
Prepping polished cast iron for hard chrome plating
Q. I have a client that wants to hard chrome plate polished cast iron parts for an industrial application. Since cast iron poses a number of preparation and plating problems I am looking for a fail-safe pre-plate cycle. Your help in providing a cycle that works will be very much appreciated.
Raymond HolfordSales to the metal finishing industry - Minneapolis, Minnesota, USA
May 6, 2010
A. Hi, Raymond. I wouldn't claim it was fail-safe, but the only acceptable process for cast iron is vapor blasting, rinsing, plating per Guffie.
Regards,
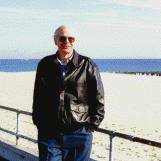
Ted Mooney, P.E.
Striving to live Aloha
finishing.com - Pine Beach, New Jersey
A. Hi,
I suggest Sargent chrome solution and maybe a copper strike.
Regards
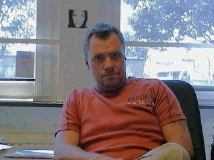
Anders Sundman
4th Generation Surface Engineering
Consultant - Arvika,
Sweden
Cast Iron Dies Won't Re-Chrome
Q. We recently received a press part die from our customer to be hard chrome plated. The die had existing chrome plating on it, so we de-chromed it using Hydrochloric acid. Due to higher concentration minor pitting has occurred on the casting and it turned blackish.
We have tried to plate is multiple times now, however hard chrome is being deposited on high current density areas (10% of the entire die). What can be done to revive the die and re-chrome plate the same.
Kalpesh Dagliya- Mahasrashtra Pune
May 7, 2024
for Shops, Specifiers, & Engineers
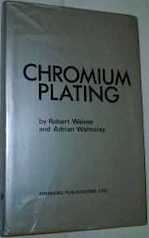
by Weiner & Walmsley (1980)
avail from eBay, AbeBooks, or Amazon
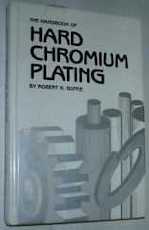
by Robert K. Guffie (1986)
avail from AbeBooks, or Amazon
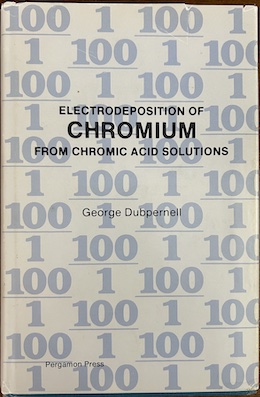
avail from eBay, AbeBooks, or Amazon
"Hard chromium plating: A Handbook of Modern Practice"
by John David Greenwood (1971)
avail from eBay
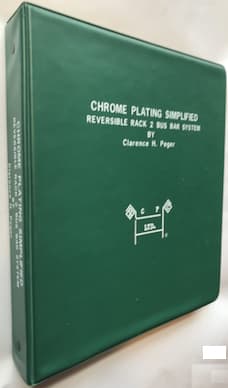
very rarely avail from Amazon
but copies are available in a few libraries)
"A Chromium Plating Bath With The Fluoride Ion"
by Alfred Perlenfein (2013)
avail from eBay, AbeBooks
(as an Amazon Associate & eBay Partner, we earn from qualifying purchases)
A. Hi Kalpesh.
You probably know 10X as much about hard chrome plating as I do, but without understanding what you know and what you don't know, I don't want to miss the obvious :-)
You do already realize that it is entirely normal for chrome to deposit only at high current density? Are you able to estimate the current density on the areas that are not plating?
Is it possible that these components simply have more surface area than other items you plate and your rectifiers cannot provide sufficient current to reach the necessary threshold in the low current density areas?
Luck & Regards,
Ted Mooney, P.E. RET
Striving to live Aloha
finishing.com - Pine Beach, New Jersey
A. Kalpesh,
Check chrome tank concentration and temperature and rectifier.
Analyze chrome thickness at dark spot against bright spot.
Maybe need to change rack design or too many parts on rack-reduce parts on rack.
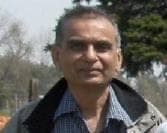
Popatbhai B. Patel
electroplating consultant - Roseville, Michigan
Q. Hi,
So nice to hear from you almost immediately. Yes, I am aware that plating chances are more on HCD areas. However generally we are able to plate around 95 percent of the dies with some female radius left without plating. In this case, because of over degradation of the casting due to high exposure in hcl, some inherent properties of the casting have changed which is giving us issues. The rectifiers are of 15000 amps, so I am pretty sure that's not a problem. Sharing some dies that we have chrome plated recently for your reference.
Now let's talk about how to prevent this going forward. Do you know a better solution to strip chrome rather than using hcl. If we use hcl, what is the concentration that should be used so that it does not affect the die casting.
One of my operators had an interesting observation. When we are stripping the chrome off a casting using low concentration HCl, we have to increase the time required to strip the chrome. But this is more dangerous as low concentration of HCl also affect the inherent base material faster.
Instead when higher concentration when used, strips the chrome plating faster and there is less damage to the casting as the time of exposure is minimized.
I still have to test this hypothesis, but could you validate or add your valuable inputs on this?
- Maharashtra India
A. Hi again,
I think most shops strip hard chrome from iron and steel in an anodic alkaline stripping tank (essentially an anodic electrocleaner). This has the disadvantage that it creates hexavalent chromium, but the advantage that it does not etch the iron or steel. What is your experience with that?
Luck & Regards,
Ted Mooney, P.E. RET
Striving to live Aloha
finishing.com - Pine Beach, New Jersey
Q, A, or Comment on THIS thread -or- Start a NEW Thread