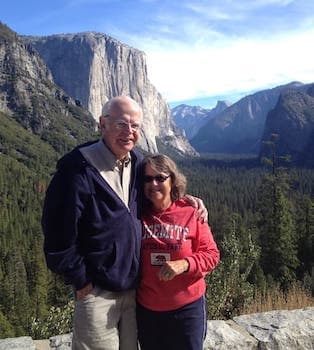
Curated with aloha by
Ted Mooney, P.E. RET
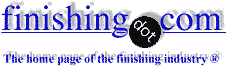
The authoritative public forum
for Metal Finishing 1989-2025
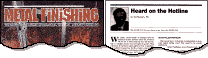
-----
Shot Peening & Anodization to Maximize Fatigue & Corrosion Resistance of 6082-T6

Q. Hi There,
I'm looking to replace a 316 stainless part in a marine application with aluminum for weight savings. The parts are currently CNC machined from a round bag and passivated.
The two main factors where the SS is helpful is in fatigue strength and corrosion resistance. Our part is subject to fairly high/irregular cyclic torsional loading. It is also threaded for stainless steel hardware, these areas are not strength critical but I mention due to the corrosion factor.
I want to give our replacement aluminum solution the best possible chance of surviving field trials, we are a small and rather new company so many rounds of testing are not practical and there is not much data I have found on torsional fatigue behavior of various alloys.
My plan is to try 6082-T6, CNC to shape, shot peen the area under highest load, hard anodize (Class III?), and finally seal the surface...
Would love to hear if I'm on the right track and any specifics on the treatments I should be requesting to optimize fatigue and corrosion resistance. Probably more importantly would be recommendations on experienced suppliers that would be willing to work with orders of ~100 parts at a time.
I've got a great machinist in Indiana (Abell Tool & Die) but don't know where to start with shot peening and getting the very best anodization.
Also all ears if anyone have any alternative methods I should consider!
- Lyle Washington
March 23, 2024
Q. Hi guys, just wanted to bump this up the list!
Thanks,
- Lyle Washington
privately respond to this RFQ
Ed. note: As always, gentle readers: technical replies in public and commercial replies in private please (huh? why?)
A. Hi Greg,
While I can't help you with your supplier situation, I can offer you a few bits of advice in terms of material and finish selection.
To start with, I think you should be aware of two very important things about anodizing aluminium:
1. If you are thinking of shot peening or bead blasting a part selectively (only some areas) and then anodize the whole part, it will result in a highly uneven anodize thickness and a poor aesthetic appearance. The uneven thickness will also seriously affect corrosion resistance.
For some reason, the peened/blasted areas have completely different electrochemical properties compared to the rest of the part and anodize very differently, as if they were made of a different alloy entirely, no doubt due to some microstructure transformations resulting from the peening process.
2. Anodizing, by itself, DECREASES fatigue resistance somewhat. And the thicker the anodize layer, the worse it gets (for reference, hard anodize is very thick!).
This happens because anodizing inevitably roughens the underlying aluminium substrate due to the nature of the process, and the roughness causes localized stress concentrations decreasing fatigue resistance.
The only exception to this is if corrosion performance is a significant factor, since if the part corrodes heavily in service this will lower the fatigue resistance even more than an anodize layer would; again the roughening of the surface is the main culprit there, so there is clearly a compromise between losing fatigue life due to corrosion vs. losing it due to a heavier anodize layer.
Considering the above mentioned issues, in my opinion this suggests the following alternatives for your part's finish:
You can either specify a thin paint pretreatment anodize (such as BSAA or phosphoric acid anodizing) and paint the part with a quality organic coating of some sort.
Parts with very complex shapes (ie. deep recesses) can be successfully coated with electrophoretic lacquers, for example.
Either way, pretreatment+painting will have very minimal effect on fatigue resistance and the paint will hide the inevitable anodize blemishes caused by shot peening.
Or you could try a heavy coat of electroless nickel (EN), for a marine application you would probably need at least 30-50 micrometers to have acceptable corrosion service life.
As an added bonus, this would prevent any serious galvanic corrosion issues between your part and the attached stainless steel hardware.
But EN as a choice of finish will not work if the coating could conceivably get heavily worn away or gouged in service, as then massive galvanic corrosion between the highly noble nickel layer and the very un-noble exposed aluminium would quickly ruin the entirety of the part.
PS: last but certainly not least, you might want to consider specifying a 2000 series alloy for this part, since they have superior strength and hardness in a T6 state compared to 6000 series.
2000 series anodizes worse with reduced corrosion resistance, but this is hardly relevant if you would be painting the part instead of relying on a heavy anodize for corrosion resistance.
2000 series alloys are also effectively impossible to hard anodize, but again you probably shouldn't be even considering that as a finish specification due to the fatigue issue here.
- Częstochowa, Poland
May 23, 2024
Thanks PH, that is super helpful!
Q. Since mechanical abrasion is a matter of in and not when for these parts so the pretreatment + paint sounds like a better option. Would this combination be more susceptible to wear and eventual exposure of the raw surface than a hard anodized counterpart? The part has a mating surface that relies upon a friction fit of a CFRP component so my concern would be galvanic corrosion should the coating wear down.
The reason I have not looked much at 2000 (and 7000) series Al is that the surface of the parts will be scratched during use so eventually the bare metal will be exposed.
- Lyle Washington
A. Given that strength is not an issue but corrosion is, have you considered glass reinforced polymer (GRP)? It has comparable properties and price to aluminium alloys and is an insulator so corrosion is not an issue. Fatigue may be an issue but that is something your engineers should be able to evaluate.
Andrew Speer- Ballarat, Australia
Q, A, or Comment on THIS thread -or- Start a NEW Thread