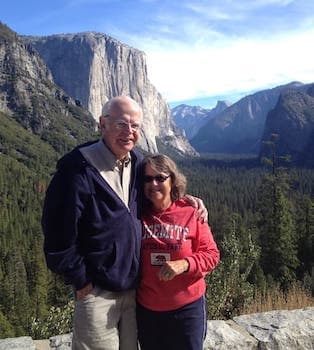
Curated with aloha by
Ted Mooney, P.E. RET
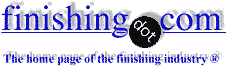
The authoritative public forum
for Metal Finishing 1989-2025
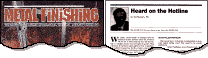
-----
EP Phosphate Coating on 1065 Steel Leaf Spring - Resolving Fatigue Reliability Issue
July 13, 2017
Q. After a year long project trying to improve the reliability of our springs on our low cost $80 prosthetic knee for poor populations in India, just a week ago we got data that made us think the EP Phosphate coating may be at least a partial cause of the breakage quality issue that has been plaguing our low cost innovation from scaling to more of those in need.
I provide background below, but I would love to know what other background information should I seek to obtain from my sub-supplier to help you all provide better advice?
Related to the background information below, my main technical asks are:
1) Is EP (Phosphate) coating following heat treatment a common cause of reduced reliability / fatigue life? Why?
2) To address these failures, is it likely we need to switch to another type of coating? Or should we first just try to improve the current process?
Regarding potential root causes I have read about, such as hydrogen embrittlement
3) Is the most likely cause hydrogen embrittlement, or something else?
4) If the likely cause is hydrogen embrittlement, how might we check this? Or test a change or addition to the process to prevent the issue in future coating batches?
6) If the most likely cause is something else, how might we verify this as the root cause, or change the process to prevent it in future coating batches?
-----
Background information
Issue: There is a set of 3 stacked leaf springs on our prosthetic knee. They serve to push the leg forward during the stride to prevent buckling of the prosthetic leg when the heel of the foot strikes the ground (decreases likely of an amputee falling when they step forward).
Actuation angle during 1 cycle: from 43.4 to 106.1 degrees.
Manufacturing process - key steps
1) Obtain pre hardened, pretempered 0.2mm thick steel coils of Japanese 1065 carbon steel. Comes in at 48.5 HRC, with tensile strength 1274 MPa (can send more specs if needed)
2) Blanks cuts via progressive die -- final geometry except for radius in step 3
3) Form large radius in Prototype Bending Die (0.76mm radius listed above)
4) EP coating - We have heard it is a phosphate coating from the supplier, and are digging in for more details now.
We tested 18 samples, prior to be drawn or EP coated, all passed. Thought we were good to go.
But, then, we repeated our test with the same material, only adding the EP coating process (for environmental protection against salt, corrosion, etc), and have seen 2 of the 18 sets of 3 springs fail through 500,000 cycles.
So there is a pretty clear difference in performance, with the only difference in processing being the coating, is why we think the cause is related to the coating process.
Any ideas related to any of the Questions 1-6 above?
engineer at non profit - San Francisco, California, USA
P.S., Flow Chart added July 14:
A. Hi Casey,
This is a high tensile strength steel, which requires de-embrittlement after any process with the potential to generate hydrogen, which phosphating will do.
At that strength I would expect the parts to be de-embrittled within 1 hour of phosphating at 375 °F (195 °C) for a minimum of 3 hours. The delay time into the oven is critical, hydrogen embrittlement is time dependent so the sooner into the oven the better. Sounds like you need to check with the treatment house to ensure they are carrying out the de-embrittlement operation.
If parts have not been de-embrittled then premature failure is very likely.
Aerospace - Yeovil, Somerset, UK
July 14, 2017
July 17, 2017
Q. Brian that is incredibly helpful advice! Thanks so much!
We are attempting to check with the supplier now on their de-embrittlement process. We know there is a 30 minute drying process at 392 °F, but it sounds like that might not nearly be long enough time duration.
1 question that come out of your feedback: We have a stock of parts that we tried to de-embrittle multiple days after the coating process, when we learned that the baking might be helpful to avoid embrittlement, but before we knew how critical it was to do right after the coating (the timing). Is there any chance these parts could have been de-embrittled via our 6 hour bake at 325 °F, and would be worth putting on the fatigue tester? Or should we scrap these without too much more thought?
-----
Separately, I also had a question about on the necessity of adding a coating of oil after the phosphate coating. I have read and heard from a couple places now that doing a phosphate coating without also adding oil is silly, in that you won't achieve nearly the same amount of corrosion resistance without the oil as you would with it.
I'm not sure if oil is a part of the current process. Could the lack of oil be causing the fatigue issue? Or is fatigue unrelated, and are we just not as corrosion resistant as we could be without it? I ask as I am wondering whether to request that oil be added to the next batch, or if I should wait to see if the extra de-embrittling bake solves the issue first.
Once again I appreciate any light you all can shed here!
Casey
D-Rev - San Francisco, C
A. Hi Casey. The oil is for corrosion resistance, and I doubt that it has either a positive or negative bearing on your failure issue.
Your failures and observations about them have actually been very interesting & informative to me because, while most finishers have heard of hydrogen embrittlement, we know it's worst in the processes that generate the most hydrogen (strong acids, high acidic and inefficient plating processes like chrome plating). So I hear some back and forth about whether hydrogen de-embrittlement is really necessary after phosphatizing; your experience has convinced me that it is.
By the way, what does "EP" stand for in your EP Phosphate?
As for the parts that you de-embrittled "too late", I would try to neither use them nor discard them until you are sure you are at the root of the problem, i.e., until you've convinced yourself through testing that lack of hydrogen de-embrittlement was in fact the problem. When/if you are convinced of that premise, it will probably be time to discard them.
Regards,
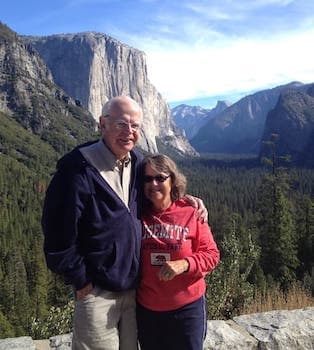
Ted Mooney, P.E. RET
Striving to live Aloha
finishing.com - Pine Beach, New Jersey
July 2017
July 22, 2017
Q. Hi Ted and team,
We talked with the supplier, and don't have a ton of new information, but here is what we do know in response to your question(s).
EP likely stands for electrophoresis. Apparently what is happening to our parts is not a coating with a phosphate conversion, but a direct to metal "e-coat" process, in which the parts are immersed in an electrified bath and coated with epoxy.
So that process as we now understand it is:
1. Ultrasonic wash in alkaline solution, PH 7 or 8
2. Wash w/ionized water
3. They use acid to bring the pH back down to 7
4. Wash again
5. EP coating - epoxy
6. Drying - 200 °C for 30 minutes
So given than this is a different process than the phosphate coating I originally thought, it is unclear to me if hydrogen embrittlement still remains the most likely root cause.
The coating supplier in China is willing to work with us to experiment on the exposure duration, bath voltage, bake time, etc. However, it is also still very unclear if the best choice is to experiment with the supplier we have, try another more reputable supplier than can perform a similar 'e-coat' process (such as PPG*, Henkel, Valspar**), or change the coating process altogether to a phosphate conversion coating, or at least to include a phosphate pre-treatment as a predecessor to the epoxy e-coat process.
Any thoughts would be greatly appreciated!
Casey
*http://www.ppgecoat.com/Products/Anodic-Epoxy.aspx
**http://www.valsparindustrial.com/en/products/Vectroguard/
D-Rev - San Francisco, California
A. Hi Casey. Your update is very interesting because now we are talking about whether electrocoating will cause hydrogen embrittlement, which is a apparently a really good question!
On the one hand we have letter 55264, "E-coat and Hydrogen Embrittlement" which says it won't; this opinion is backed up by an article from Products Finishing at https://www.pfonline.com/articles/hydrogen-embrittlement. Supporting those opinions is the fact that the Handbook of Electroplating Technology .
doesn't even discuss hydrogen embrittlement, and a Google search for "electrocoating hydrogen embrittlement" comes up empty (for me at least) except for a number of articles which comment in passing that electrocoating does not cause hydrogen embrittlement.
But on the other hand it seems rather obvious that you are having an embrittlement issue arising in your finishing process, which is either happening in the electrocoating process, or in another process which is being conducted by your supplier but is not being mentioned by them.
Regards,
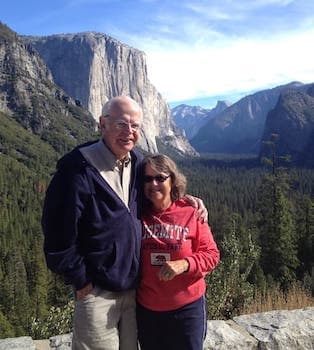
Ted Mooney, P.E. RET
Striving to live Aloha
finishing.com - Pine Beach, New Jersey
A. Hi Casey,
I'm not even going to pretend I have enough experience to comment about Electrocoatings as I have never played with them. What I will say is that looking at the pre-treatments I see an Electrochemical degreasing operation. If this operation is a cathodic clean or a cyclic anodic/cathodic clean finishing with a cathodic operation this may be a potential source of embrittlement. Electrochemical cleaning should either be anodic (generates oxygen at the part, not hydrogen) or should at least finish with an anodic cycle.
Aerospace - Yeovil, Somerset, UK
July 24, 2017
July 25, 2017
Q. Hi Brian,
Thank you so much for the response.
Cathodic operations causing hydrogen evolution was definitely something I was worried about, but I did not know it may be happening in the electrochemical degreasing operation, in addition to the EP coat step.
#1 I will contact the supplier today to see if he can experiment with anodic operations for both the EP coating and the electrochemical degreasing steps.
I am also going to ask him if we can experiment with the curing time/temperature.
#2
On one side, I think 200 °C for 30 minutes may be unintentionally affecting the heat treatment of the 1065 carbon steel, so I'd like to try a lower temperature.
#3
On the other side, I've heard longer bakes may help the hydrogen to escape, preventing hydrogen embrittlement, so I'd like to try a longer duration at the same temperature as well.
#4
I am also reaching out to other e-coaters and coaters in general to see if they have any suggestion for a bulk coating process that doesn't require such a high heat for curing/drying, and/or that might be less susceptible to hydrogen embrittlement.
Anyone's thoughts on any of these paths would be welcome!
Casey
D-Rev - San Francisco
A. Hi Casey,
Have you considered electropolishing the surface for the purpose of removing hydrogen embrittlement issue?
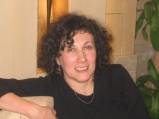
Anna Berkovich
Russamer Lab

Pittsburgh, Pennsylvania
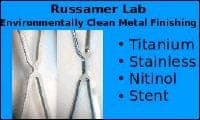
July 27, 2017
Q. Hi Anna,
I had not considered electropolishing. And I assume you mean e-polishing before, not after the e-coating process, correct?
Could you perhaps elaborate on why it would help in my situation? And what any disadvantages there might be to e-polishing?
Also -- can e-polishing be done in bulk, i.e., thousands of small parts at once?
Casey
D-Rev - San Francisco, California, USA
July 27, 2017
A. Hi Casey,
Electropolishing is done prior to e-coating. The damaged areas with hydrogen embrittlement will be repaired. The disadvantage is in adding additional step to the processing.
Bulk electropolishing is possible.
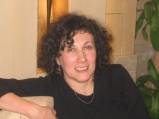
Anna Berkovich
Russamer Lab

Pittsburgh, Pennsylvania
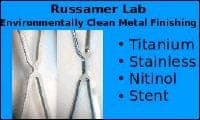
July 28, 2017
A. Hi Casey,
I think the de-embrittlement temperature is very unlikely to affect the heat treatment state of 1065 type steel. the recommended heat treatment (general) for high carbon steels is around 550-650 °C, so at 200 °C you shouldn't affect properties.
To me 200 °C for 30 minutes is too short, it should be for at least 3 hours. It is also important that the parts are de-embrittled as soon as possible after treatment, and at least within 4 hours (some aerospace specifications require de-embrittlement to start within 1 hour), minimum delay to the oven is important.
If you wish to try another temperature you could try a carburized steel de-embrittlement type cycle, this is 135 °C for a minimum of 6 hours.
Aerospace - Yeovil, Somerset, UK
July 31, 2017
Q, A, or Comment on THIS thread -or- Start a NEW Thread