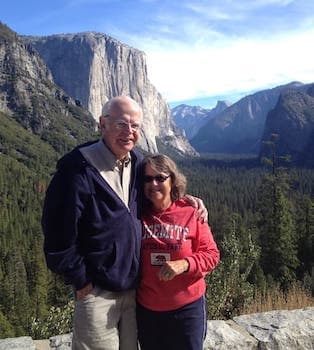
Curated with aloha by
Ted Mooney, P.E. RET
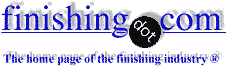
The authoritative public forum
for Metal Finishing 1989-2025
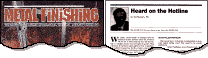
-----
Two layers of nickel for "show" chrome -- common or rare?
March 5, 2015
Q. Hi,
I need to have several pieces of cast bronze boat hardware re-chromed. I found several plating shops that operate in the auto/marine/custom refinishing niche (not big production houses). All advertise show chrome and have good reputations in the restoration business. As I try to evaluate these shops I find that while they advertise three part chroming none mentions two layers of nickel as described in your FAQ:
".. chrome-lovers believe that the key to "show chrome" is to copper plate the item first and then buff the copper to a full luster before starting the nickel plating .. at least two layers of plating follow -- a layer of nickel and a layer of chrome. But high quality plating usually requires two layers of nickel. .. The most important issue for durable chrome plating for outdoor exposure such as on a vehicle is that it should have at least two layers of nickel plating before the chrome: namely semi-bright nickel followed by bright nickel."
Is this a common practice in the industry or rare?
Is one heavy layer just as good?
Thanks
consumer - Southern Tier, New York, USA
A. Hi Wally. I wrote that FAQ, and I realize that many custom replating shops do excellent work while not doing duplex nickel plating -- so, yes, I should clarify. So let's look at two different situations, i.e., original OEM plating vs. custom show-chrome plating...
When bumpers and wheels are initially plated there may be about 6 to 20 per rack on an automatic plating machine, maybe even more. The idea is that this greatly reduces labor costs. The OEM also doesn't want to do buffing in the middle of his plating operation, but wants to rely on simple polishing before plating, and the use of self-leveling nickel plating to get the shine. Once labor costs are reduced by no buffing plus automated plating of multiple units at a time, material costs become very important to an OEM so they want to limit plating thickness (and cost) to the minimum necessary for good corrosion resistance. It has been found that two layers of nickel (semi-bright followed by bright) allows this minimization. That is because the bright nickel is sacrificial to the semi-bright nickel, so at a pinhole or porous area the surrounding bright nickel sacrifices itself so the semi-bright layer does not get penetrated and expose the underlying steel. That's the key to OEM economy and quality: minimize unit labor, don't copper plate, don't buff, and use duplex nickel to enable good corrosion protection at low nickel thickness and cost.
For the custom plater the situation is a bit different. They want the best shine money can buy, so after initial copper plating they buff the copper to a high shine before continuing the plating. There is a difference! Long ago, GM continued with this copper plating and buffing on their Cadillac line while dropping copper plating on their other lines (sorry, I don't know if any OEMs still copper plate and buff their steel parts; plastic parts are copper plated but for a different reason). After the initial copper plating and buffing, the custom shop does more copper plating, then nickel and chrome plating. Because almost all of the cost for a custom plater is labor, they are far less concerned with minimizing the nickel plating thickness than an OEM is and I believe that it is entirely possible for them to apply a single layer of nickel plating which is thick enough to offer excellent corrosion resistance. Unfortunately, you can't buy by "spec", but must rely on the reputation of the plater. I apologize that our FAQ may be read to imply that duplex nickel is a commonplace for custom platers -- it probably isn't. Best of luck.
Regards,
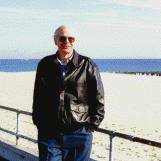
Ted Mooney, P.E.
Striving to live Aloha
finishing.com - Pine Beach, New Jersey
March 2015
A. Ted makes some good points in his reply and I agree with them. It is a pity that cost cutting is resulting in inferior plating being done. I would certainly seek out a duplex nickel plater, or a copper interlayer plater, as the quality of the finished product is superior to single layer nickel. However, it all depends on how much you are prepared to spend and how long you want your coatings to last - all else being equal, the cheaper it is, the shorter its life expectancy.
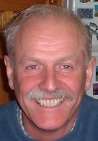
Trevor Crichton
R&D practical scientist
Chesham, Bucks, UK
March 5, 2015
A. There's actually a spec on plating thicknesses (nickel and chrome for various "service conditions," such as indoor only use. It is ASTM B456.
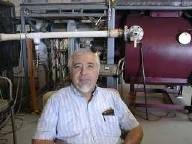
Jim Treglio - scwineryreview.com
PVD Consultant & Wine Lover
San Diego, California
March 11, 2015
Q, A, or Comment on THIS thread -or- Start a NEW Thread