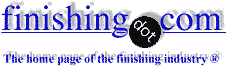
-----
Need DARK galvanising alloy. What is black galvanizing?

Q. I am having a new type of tool manufactured at a machine shop but am sending out the metal finishing jobs (anodizing, powder coating, etc.) to other finishing shops. A powder coater told me that I should consider having some of my small steel parts "Black galvanized" instead of powder coated to the the black color that I wanted. He told me that the glossy black finish was much less expensive to apply than powder coating for these parts that are going to be in hidden or inconspicuous locations. The local galvanizing shop doesn't know anything about a "Black galvanizing" process. Have any of you heard of such a finishing or coating process? Is it the same thing as applying a black oxide coating?
Thanks for your response.
Larry Loo- Clovis, California 2001
for Engineers, Shops, Specifiers
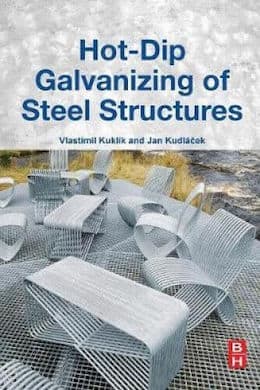
avail from eBay, AbeBooks, or Amazon
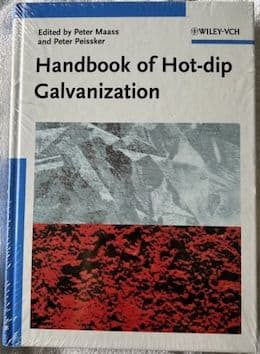
avail from eBay, AbeBooks, or Amazon
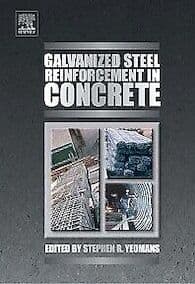
avail from eBay, AbeBooks, or Amazon
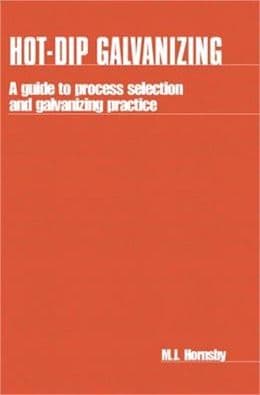
avail from eBay, AbeBooks, or Amazon
avail from Amazon
"User's Guide to Hot Dip Galvanizing for Corrosion Protection in Atmospheric Service" by NACE (1997 only rarely avail.)
avail from AbeBooks, or Amazon
(as an Amazon Associate & eBay Partner, we earn from qualifying purchases)
A. Hi Larry. People are liable to coin slang, and it's likely that your powder coater did so. Sounds to me like he meant black oxiding rather than black galvanizing. This is a process which can produce a nice-looking glossy black, of no measurable thickness, but which offers little corrosion resistance even with the required wax or oil. Yes, black oxide probably is less expensive than powder coating.
It's also possible to do "black zinc plating", which would be zinc, or preferably zinc-iron, electroplating followed by black chromate conversion coating -- also less expensive than powder coating, and probably offering plenty of corrosion resistance for interior applications. Hot dip galvanizing is probably more expensive than powder coating and is not black. Good luck.
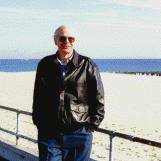
Ted Mooney, P.E.
Striving to live Aloha
finishing.com - Pine Beach, New Jersey
Need "Black Galvanizing" service
RFQ: I am looking for Companies in the greater Detroit area which have capabilities to black galvanize. I have seen this done in Europe and would like to do the same in the US. Please contact me via email.
Dieter F [last name deleted for privacy by Editor]Automotive supplier - Troy, Michigan, USA
2007
Ed. note: This RFQ is outdated, but technical replies are welcome, and readers are encouraged to post their own RFQs. But no public commercial suggestions please ( huh? why?).
A. Hi Dieter. Phrases like "black galvanizing", without specification numbers attached, seem to have rather loose meanings. Is it possible that you referring to zinc electroplating followed by black chromate conversion coating?
Regards,
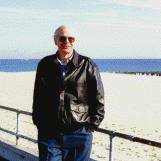
Ted Mooney, P.E.
Striving to live Aloha
finishing.com - Pine Beach, New Jersey
Multiple threads merged: please forgive chronology errors and repetition 🙂
Q. Hello world of experts.
And seasons greetings, and wishes for health and peace.
We are seeking a dark galvanised finish.
As dark as reasonably possible, ideally without using any passivation, etc. ... the application is in a seaside environment and we suspect passivate will soon degrade to leave a blotchy finish.
The steel will be a low reactive steel, but will be carefully surface prepared with a white metal shotblasted finish.
We are not aware of any suitable bath composition but this is the place to ask!
We are wondering about using magnesium, copper or even iron in the bath to produce a darker appearing finish after weathering.
Many thanks and kind regards
Designer - Swansea, UK
December 20, 2014
A. A typical galvanizing kettle contains 200-400 tonnes of zinc. It's expensive, and so any "mucking about" with the chemistry of the zinc composition is done very cautiously. It will probably be long lasting, so there needs to be a lot of sales of coating to make any change worthwhile.
I wonder what makes you want galvanizing? You say you're after a specific finish colour. Presumably you also want some corrosion protection too?
You've said you'll shot blast first, but didn't say why you take that relatively unusual step before galvanizing.
What you have done is say a little about what you're trying to achieve, and some of what you want done to get there, but seek a solution.
So, why not start with what you want the end product to be, then ask how to get there. It could be that galvanizing isn't the answer and that some other coating is better.
What are you trying to do?
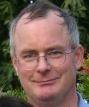
Geoff Crowley
Crithwood Ltd.
Westfield, Scotland, UK
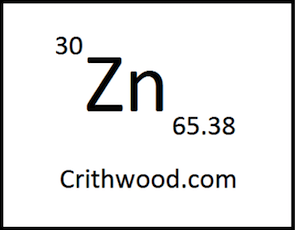
A. David,
Paint properly applied after galvanizing is likely the best answer. Chromate quench with sulfuric acid to adjust pH gives a nice golden color. Titanium in the zinc gives many colors as does a few other elements. Unfortunately as the zinc is alloyed the tendency for corrosion increases. I do not know of any commercial product.
Galvanizing Consultant - Hot Springs, South Dakota, USA
Q. Thanks,
We are proposing to manufacture a wide range of architectural products including glazing frames, roofing systems, cladding, and doors and frames.
We need a metallic finish, which will weather and take a patina, and zinc/titanium alloy roofing foil would be the closest match we have currently found.
But as you know this material has a large coefficient of thermal expansion and no structural strength nor stiffness; hence it has to be cut into relatively narrow strips and fixed mechanically to a timber substrate.
Even then it oilcans in the sun.
It also is somewhat lighter in weathered colour than we are ideally seeking ...though this is a secondary consideration.
Kind regards
David
- swansea, uk
A. If you still want steel, then a possible solution is galvanize the steel for corrosion protection, then powdercoat over using one of the metallic powders (probably in polyester).
There are a large range of metallic looks. They won't "age" to get a patina look, but you could have that right from the start.
Powder applied coatings can emulate almost any look, and you'd get 25-30 years life of the coating, and that without any deterioration of the substrate.
Such a system as above could be suitable for the list of products you describe.
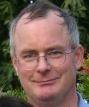
Geoff Crowley
Crithwood Ltd.
Westfield, Scotland, UK
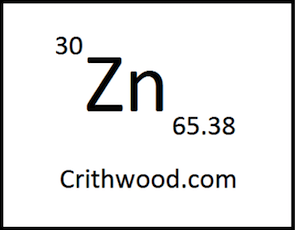
Q. Thanks again.
Paint won't cut it, I'm afraid ... it's a metal finish we are looking for definitely.
I am hearing about some new high magnesium aluminium, very low lead galvanising alloys ... is anyone in UK offering this?
The magnesium alloys also seem to be very good with chloride environments.
Kind regards,
- Swansea uk
A. David,
when you say "paint won't cut it", you seem to be implying that you require more than aesthetics, but you haven't really said what functionality you require, that insists on metal?
There are powder applied paints that mimic many other materials aesthetically, though not functionally. For example we have in our display area a "wooden" bench -- oak -- that most people looking at it do not believe that it is powdercoated galvanized steel, until that touch it, and hit it with their fingers and hear that its metal. Similarly we have steel that looks like anodized aluminium (we're not the only ones doing these things).
Lead-free galvanizing doesn't look any different to that containing the tiny % of lead that the other has. I note you're in the UK. Currently about half the UK has moved to lead free, and no one has noticed.
Not all finishes can be simulated in powder applied polymers, and galvanizing spangle is one such.
You mention aluminium, etc., in galvanizing. These special alloy mixes are mostly used in continuous strip galvanizing (sheet metal), not in post fabrication hot dip galvanized. No galvanizer changes their metal composition lightly, and then only if a customer will take all their production capacity. It's an area of no return, can't be changed quickly and can't be changed back without enormous expense.
What actually are you trying to achieve?
Do you need the coating to do some function? If so what?
If the coating is aesthetics, why would you not use a coating that looks like what you want?
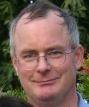
Geoff Crowley
Crithwood Ltd.
Westfield, Scotland, UK
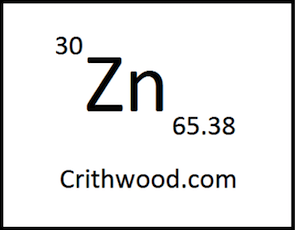
A. David,
Do you own a galvanizing plant? What is the zinc composition (Mg/Al) that you propose using for the coatings that you intend to put onto product? If the aluminum is above 0.007%, then conventional chloride containing fluxes will not work. I did an experiment with magnesium in the zinc and got "white rust" on the product.
Regards,
Galvanizing Consultant - Hot Springs, South Dakota USA
Is it possible to galvanize in black?
Q. Hi,
We supply and install gate automation systems and have been asked by an architect to produce some gates that are black galvanized. He says he has seen this done before but I can't find any information on it. Can you tell me if this is possible? If it is not is there any other type of corrosion protection that gives a black finish. He has specifically said that he does not want a painted finish.
Kind regards
James Darnell
Gate Automation Supplier - Garstang, Lancashire, UK
March 13, 2015
A. Hi James. We appended your inquiry to an earlier thread on the subject. It seems that black galvanizing is not realistic; but you could do zinc-iron electroplating followed by black chromate conversion coating (although it would not have the decades of durability of hot-dip galvanizing), or you could probably apply a black patina to the galvanized surface (see letter 20297, "Speed up the patina process on hot dipped galvanized steel"). A sample would be important as it's hard to predict what the architect would or would not be pleased with based on a verbal description.
Regards,
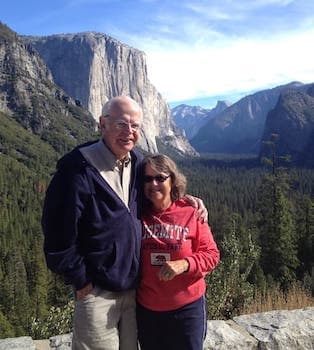
Ted Mooney, P.E. RET
Striving to live Aloha
finishing.com - Pine Beach, New Jersey
A. Polyester powdercoating over galvanizing is common, that way you can get any colour you want.
Just make sure you choose a coater with a competent pretreatment and experience in powdercoating over galv.
You're in the UK. One way to have some confidence is to choose a coater who is approved for this by a major powder manufacturer.
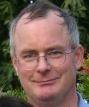
Geoff Crowley
Crithwood Ltd.
Westfield, Scotland, UK
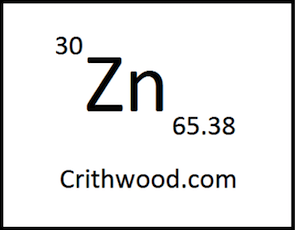
Q. Hi Geoff,
What I'm trying to achieve is a dark coloured finish that provides good corrosion resistance for an external application but does not have a uniform finish. By non-uniform I mean in the same was as raw steel, a piece of wood or a galvanised steel is not exactly the same all over. Whereas a painted finish/powder coated finish is usually the same all over. Does such a finish exist?
Many thanks
James
garage doors - Garstang, Lancashire, UK
Q. Hello,
I was recently in Japan and I saw this dark/black galvanized finish. It was on a heavy duty fence. I have emailed a photo of the normal (light) galvanized finish and the dark galvanized finish adjacent to each other so you can see the difference.
Can you please let me know how this dark finish is done? We would like to request the finish for a client who only allows galvanized metal work on their projects (for longevity), but we find the lighter typical finish very limiting for our design.
Thank you!
Architect - Montreal, Quebec, Canada
December 6, 2016
A. The colour is probably not deliberate, but a result of the environmental conditions. That might include pollution, chemicals or even naturally occurring substances that will discolour the zinc.
A very dilute solution of copper sulphate
⇦ on
eBay or
Amazon [affil links] might get the finish you wish.
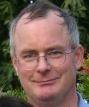
Geoff Crowley
Crithwood Ltd.
Westfield, Scotland, UK
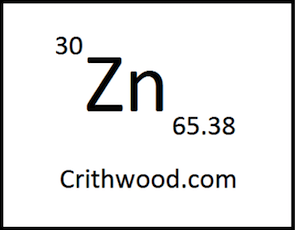
A. Hi Tyler. For once I'll have to disagree with our extremely knowledgeable galvanizer Geoff Crowley. Considering that I have never seen galvanizing anything like that color, and that it's right next to more conventional looking galvanizing, I don't think I can concur with "probably not deliberate" :-)
Regards,
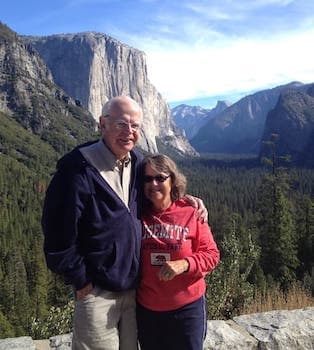
Ted Mooney, P.E. RET
Striving to live Aloha
finishing.com - Pine Beach, New Jersey
A. Mr. Tyler Rozicki,
There are two probabilities for such dark appearance:
1. I agree with opinion of Mr. Geoff that If Galvanized material is stored in polluted area (like downwind near to Pickling lines), then over a period of time the zinc coating becomes very dark.
2. It may be client requirement for dark shade to minimize shine. There are many chemicals available in the market for Dulling after galvanizing.
- Vadodara, India
A. Sirs:
I agree with Geoff that the "black galvanizing" is likely only a tarnishing of regular galvanizing, perhaps leaving the finished product in the galvanizing plant where it tarnished due to acid fumes. Perhaps the product was exposed to industrial polluted air. Only by knowing the history of the "black galvanizing" can one determine why it occurred. The photos look to me like the zinc has lead in it (big spangle). In the USA leaded zinc is becoming rare.
I disagree with Geoff in using a copper sulphate solution to darken the galvanized surface. Many years ago when colored galvanized coatings looked like a good idea, I put a freshly galvanized 2 inch x 2 inch test sheet into copper sulphate. What came out was a beautiful copper finish. I washed it off and dried it and hung it up in my office at the university. Within a few days the test piece very, very badly white rusted. Very low copper ions are well known to white rust and corrode galvanized coatings (e.g. domestic galvanized hot water tanks with copper fittings)
Regards,
Galvanizing Consultant - Hot Springs, South Dakota USA
The thing is, Tyler hasn't gone back to Japan to solve why & how some piece that he stumbled upon got blackened ... rather, he wants to deliver that look to a Canadian client :-)
I think it's possible to get that look with some post-treatment agent, possibly liver of sulfur
⇦ on
eBay or
Amazon [affil links]
or the darkening solution they sell for zinc camé ⇨
It seems that those blackeners for zinc contain copper sulphate and possibly selenious acid as well.
Regards,
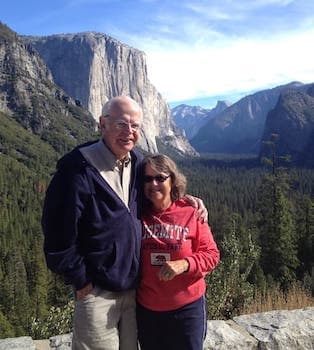
Ted Mooney, P.E. RET
Striving to live Aloha
finishing.com - Pine Beach, New Jersey
A. There's a "brew" available in the UK for treating galvanized steel before painting with Alkyd or similar paints to gain improved adhesion. It's a phosphate solution with a small amount of Copper in in order to discolour the galv. The reason for wanting to discolour it stems back to the 1960s and 1970s in the UK, the days of "British Rail" (no longer), who ran the rail network. They wanted an easy way to see if the pretreatment had been done or not. Without the copper, it was not visibly evident if the pretreatment, known as "T Wash" had been done or not. With copper added, it turned dark grey, nearly black and the huge colour contrast made telling if the job had been done very easy.
It was this I was thinking of that associated Cu and dark grey galv.
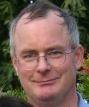
Geoff Crowley
Crithwood Ltd.
Westfield, Scotland, UK
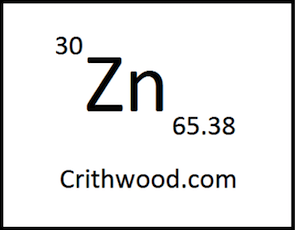
A. Sir
You need Dark Gray color Galvanized Item finish:
Zinc Bath Temp: 450. After Zinc bath dipping, Quench the job in Flux, then wash in water, then normal passivation.
This I have tried 4 times as per the clients requirement. I do not know aftereffects of it.
Galvanizers & Consultants - Delhi, India
A. Dear Mr. Dalela,
As per my opinion, it is not advisable to dip in FLUX, RINSING or Sulfuric Acid because it gives dull effect immediately but becomes reddish after some time. Ammonium Chloride reacts with zinc and top layer of zinc gets corroded.
So, it is advisable to go with specialized DULLING Chemicals which are available in market.
- Vadodara, India
Q. Hi all! I've really enjoyed reading these comments, they are very helpful! Thank you for posting them.
I work for a small landscape architecture company in Boston, we're designing a series of seating spaces, bollards, bins, lighting poles, and signage on a retail street. We would like to use Corten steel but due to cost restrictions we're looking for cheaper alternatives.
We are thinking of using a red oxidized colored galvanized steel product. Would you recommend hot dip or powder coating or are there other alternatives? Your insight would be very much appreciated.
landscape urbanism - Boston, Massachusetts, USA
December 15, 2016
A. Hi, there are many shades of dark gray that can be achieved using proprietary dulling processes after galvanizing. Such application has been used for transmission towers and poles with great success (among other components).
Regards
SAE Towers - Monterrey, Mexico
Colour tinting on galvanised finish
Q. Hello all,
Our architecture practice is designing a building with a galvanised steel brise-soleil. We specifically want the spangle look of galvanised steel, as it makes reference to the local character and history of the area. We're looking to add a subtle colour tint to the galvanised surface on different levels of the building, and I am looking for advice on how to achieve this, either during or after the galvanising process. As it is an external application, we don't want to diminish the anticorrosive properties of the gal coat. Furthermore, anything that could be done to preserve the fresh, bright metallic shine of a new galvanised finish, and prevent it going dull and grey over time (or slow the process) would be a positive.
Ideally we would be able to control the colour tightly, and get very little unintentional variation. Imagine the translucency of anodizing, over that distinctive spangled silver galvanised finish. Advice on different colours achievable, including bright metallic greys, would be most appreciated.
Architect - Melbourne, Victoria, Australia July 25, 2017
A. Hi Piers. Conventionally, galvanizing has been considered a functional corrosion-resistant finish, and whatever it looks like, it looks like. And there are good reasons for this, including the fact than a galvanizer uses a huge vat holding many tons of molten zinc and is not going to try to tweak it back and forth to make it look pretty.
But weighed against this is that when people want something enough they eventually get it. I've read on these pages for 22 years why it's not possible to get consistent color anodizing on aircraft grade aluminum ... then Apple decided that their iPhones would be made of aircraft grade aluminum and proceeded to build millions of identical parts. And there are many examples of exotic finishes.
The first direction I would look is some sort of clearcoat of partial wavelength thickness, whether created by anodizing the zinc, or by a PVD process, or applying a silicate or zirconium finish, or an organic. I think you could get the desired consistent color tint as from anodizing of titanium, or an iridescent that changes shade from different viewing angles, or a rainbow appearance like carnival glass. I am confident that at least initially it would retain the metallic and spangled look, and be a cool looking building feature, and that somebody is going to do it eventually :-)
I don't actually know how to do it, and am only talking theoretically, and don't know if your project can support the development effort though. Permanence might be a problem for metallic dyes, but they are certainly available and ought to offer consistency.
Regards,
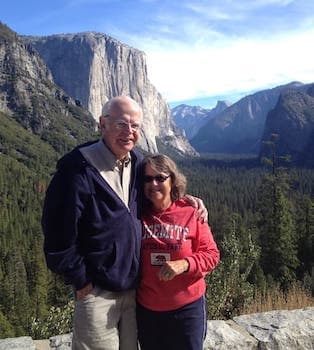
Ted Mooney, P.E. RET
Striving to live Aloha
finishing.com - Pine Beach, New Jersey
A. The problem here is that the dull colour you wish to avoid is the very thing that makes zinc protect steel. Bright shiny zinc corrodes faster than steel (that's why its called sacrificial). Without forming that dull layer of zinc carbonates and zinc oxides, the protective quality of galvanizing doesn't exist.
To preserve the shine, of you added a clear coat of something else, then that is what would be doing the protecting, not the zinc, so why have the zinc at all? And getting a clear coat of anything to stick to shiny zinc without some pretreatment or conversion coating is impossible. And that same pretreatment will discolour the zinc!
If you want aesthetic, use an aesthetic coating on top. For example, galvanize for protection, then powdercoat on top. Powder can simulate almost any finish these days, colours, metallics, textures. We have done powder applied coating that from a viewing distance of 1 meter cannot be distinguished from... anodized aluminium, leather, rusty steel, bright zinc plating, and many more.
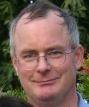
Geoff Crowley
Crithwood Ltd.
Westfield, Scotland, UK
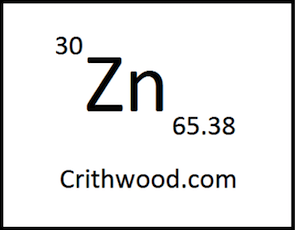
Black Zinc or Black Zinc Oxide over already galvanized lag bolts?
Q. We have a new product and the install kit requires 4 inch galvanized lag bolts.
We already have the gray galvanized lag's. I'd like to make them black with at least a semi gloss finish that can handle an impact socket. Wondering what I should use? I'll be doing thousands of them.
Thanks!
- Springfield Oregon
October 9, 2017
A. Hi Bryan. Black oxide is a process done on steel, not zinc, so I don't think that would be applicable. Black zinc plating is usually done on steel substrates, but ...
Although I can't seem to get any galvanizers to agree with me, I would think that is is possible to lightly activate the galvanizing in very dilute acid and then electroplate it with zinc-iron and apply black chromate.
Regards,
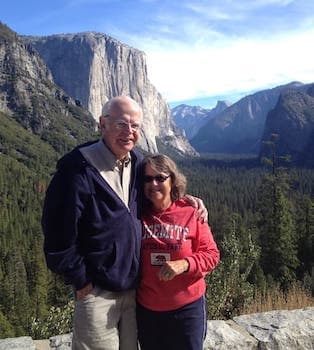
Ted Mooney, P.E. RET
Striving to live Aloha
finishing.com - Pine Beach, New Jersey
Q, A, or Comment on THIS thread -or- Start a NEW Thread