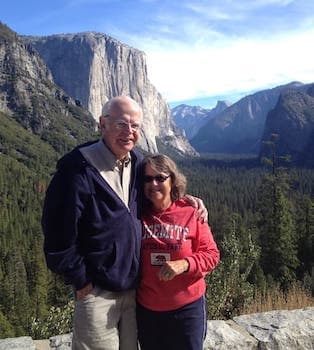
Curated with aloha by
Ted Mooney, P.E. RET
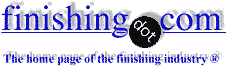
The authoritative public forum
for Metal Finishing 1989-2025
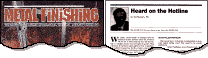
-----
Electroplating on 3D Printed & SLA models
Or see this related thread:
• Topic 59549 "Vibratory/tumble finishing 3D printed parts"
RFQ: Hi there, I'm looking for someone who can electroplate resin 3D printed jewelry. I can either cover the resin pieces with conductive copper paint, or if someone can do this step as well, that would be perfect.
I would like to get them plated in either gold or any metals that are yellow and shiny like gold, maybe brass.
- San Diego, California
September 16, 2024
privately respond to this RFQ
Ed. note: As always, gentle readers: technical replies in public and commercial replies in private please (huh? why?)
A. Hello Brian. It's not clear to me whether you are thinking of having two or three pieces plated for your personal use, or whether you are thinking of making a business of this. If business is the case, I would suggest that you just have 2 or 3 pieces plated first and see how durable they prove to be before getting into it too heavily.
Some things to remember about plating are:
• Poor thickness distribution is quite common because the plating goes where the current goes and the current takes the path of least resistance.
• You need to specify what you want: what under-layers below the gold or brass, what thickness of plating you want, what post-treatments you want such as lacquering the brass. This thread may help you do that.
Luck & Regards,
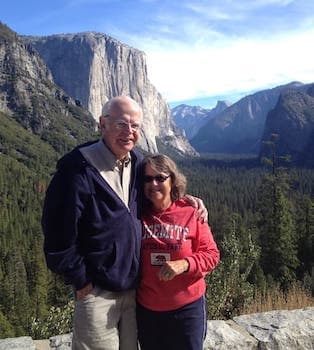
Ted Mooney, P.E. RET
Striving to live Aloha
finishing.com - Pine Beach, New Jersey
⇩ Related postings, oldest first ⇩
Q. Has anyone tried chrome plating stereolithography models?
Mike Cole1999
SLA = stereolithography
FDM = fused deposition modeling
SLS = selective laser sintering
A. Yes prototypes can be plated with many finishes including chrome. SLA usually works the best, then FDM; PolyJet and SLS not as well.
Bill Boundsprototypes - Bellingham, Washington
April 28, 2011
Multiple threads merged: please forgive chronology errors and repetition 🙂
Stereolithography and Surface Treatment
Q. I am a master student in surface finish, using stereolithography process at University Federal of Santa Catarina - Brazil. I would like to know if is it possible to use some kind of surface treatment like electroplating or sprayed metal to apply to inserts of stereolithography to obtain a rapid tool?
This surface treatment will be applied on a surface that will be in contact with the molten plastic during injection molding. Are there some surface treatments that could give the hardness and heat transfer necessary to increase this qualities more than epoxy resin that the molds are made of (Somos 7110)?
Alexandre Vilas Boas Badotti- Florianupolis, Santa Catarina, Brazil
2001
Ed. note: We've merged this inquiry with other threads which should address it for you, Alexandre. In this case, we would probably call the process "electroforming" because your goal is not so much to put a coating or plating onto your SLA component, but to use that SLA component as a mandrel from which to build an electroformed tool.
Nickel Plating vs. Chrome Plating SLA Parts
Q. I am looking to find out more about nickel plating done on stereolithography (SLA) parts. I have heard that nickel plating can increase the strength of the SLA up to three-fold. I wondered about the thickness of the nickel coat compared to a chrome coat achieved from metallizing the SLA then chrome plating it. The appearance of the SLA was also important and I wondered whether it could be polished or buffed to create a chrome cosmetic appearance.
Thanks for the help.
Mark VillwockStudent - Hinckley, Ohio
2004
A. The strength of the SLA part will be enhanced by electroplating it with nickel, but I would suggest you initially polish the part and then metallise it using electroless metallisation (assuming it is a resin and not a sintered metal). If it is a sintered metal you can electroplate directly onto it, as long as it is suitable for plating. I suggest you apply about 10-20 microns of low stress high leveling copper, followed by a zero stress (i.e., sulphamate) nickel, again about 20-25 microns thick. This can then be plated with a few (say 5) microns of chromium. The chromium will be highly stressed so you don't want much on there, but the two other layers should minimise the effects of this high stress.
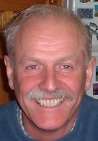
Trevor Crichton
R&D practical scientist
Chesham, Bucks, UK
Plating onto non conductive acrylic RPT prototypes
Q. Dear Sir, we have recently installed a RPT machine for producing prototypes.The output is acrylic. Some of our customers are insisting nickel or chromium coating on our parts. Please give me suggestions for achieving the same.
Thanks/Regards,
Kannan Dhandapanicamsys technologies - Coimbatore, Tamilnadu, India
2004
A. Acrylic covers a multitude of sins; some are hydroscopic and some are not so bad. You need to find out how hydroscopic your resin is and then decide how to plate it. There are standard plating on plastics techniques available that will give you the finish you require. One word of warning, my limited experience of RP parts is that they often tend to be quite brittle; plating them with metal can make them even more so.
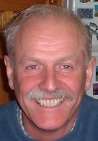
Trevor Crichton
R&D practical scientist
Chesham, Bucks, UK
How to polish ABS for Plating
Q. I work for a large consumer electronics manufacturer and am responsible for creating prototypes of potential products. In an effort to provide chrome trim, I have been machining brass parts, polishing and chrome plating.
I would like to chrome plate some machined ABS parts. Is this possible? Can or should I vapor polish before I try this?
Can I chrome SLA parts? What is the process?
These parts are cosmetic only. Any help would be appreciated.
- Framingham, Massachusetts
2006
A. Hi Tony. Virtually anything in the world is electroplateable after some sort of metallization or other (please see our FAQ: "How to electroplate flowers, leaves, animal skulls, and other organic materials"). But the principal issue usually revolves around expectations of good adhesion. First, plastics expand much faster than metals and are much more flexible, which makes adhesion of the rigid plating to the plastic difficult; second, when people see metal surfaces, they tend to hold higher expectations than for plastic surfaces.
Most of the grills of the world's automobiles are nickel-chrome plated ABS, so it is certainly possible to chrome plate ABS with exceptional adhesion. ABS has multiple polymers in it, one of which can be etched away with chromic-sulfuric acid, rendering the exceptional mechanical "tooth" necessary for outstanding adhesion. The designers usually specify "plating grade" ABS. I do not know for sure, but assume that SLA ABS will be of lower and less consistent quality, and will be harder to chrome plate reliably. Hopefully someone with experience will comment on the balance of your question, i.e., whether you will find high quality chrome plating on SLA practical, and whether it should be vapor polished or otherwise polished first. Good luck.
Regards,
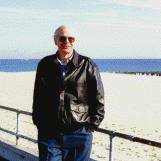
Ted Mooney, P.E.
Striving to live Aloha
finishing.com - Pine Beach, New Jersey
Vibratory Polishing of ABS & PP as prep for chrome plating
Q. Dear reader,
How can we deburr polypropylene articles with drill burrs, and light deburr ABS parts along with a mirror polish effect?
manufacturer - Surat, Gujrat, India
January 9, 2011
A. A frosted or cut edge of most plastics can be restored to clarity using mass finishing equipment with a dry organic media; however, this requires long time cycles.
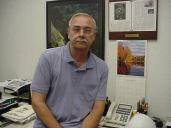
AF Kenton
retired business owner - Hatboro, Pennsylvania
Biocompatible finishing options for SLA DSM Somos Next?
Hi. We're making a product out of DSM Somos Next resin (www.dsm.com/en_US/downloads/dsms/NeXt_7_10.pdf ). This product will be in constant contact with people's skin. What kind of options do we have for finishing which:
1. Preferably are certified as biocompatible or are generally recognized as safe?
2. Allow us to either change the color or prevent the yellowing that normally occurs over time by protecting the product from UV exposure?
I've looked all over the place for answers, but I really don't know enough about finishing. We've tried:
1. powder coating (material can't stand high temperatures of the oven)
2. coating with titanium (it ended up being sticky for some reason?)
3. painting (looks amazing, but I don't think there are any biocompatible paints, or even any that are generally recognized as safe?)
There are other possibilities I've heard of (like using vacuum metallization with aluminum) that might work, but I don't know enough to evaluate them.
Any help would be greatly appreciated!
Novice product designer - Pittsburgh, Pennsylvania, USA
October 13, 2011
Q.
Presently I am working in Rapid prototyping department -- jewellery division.
We are using 3d wiper SLA machine. In this machine we are using aqua amethyst resin for making a rapid prototype.
After that we find roughness on the surface of RPT. Is there any technique for reducing the roughness or any metal coating can be done on the surface?
Please do the needful.
Thanks & Regards,
- Tamilnadu, India
December 29, 2012
A. I am not familiar with your processes, but if the plastic is molded, you need to polish the mold.
If it is a machine cutting plastic blocks to shape, then the cutting tool, feeds and speeds need to be looked at. I suspect that there is too much emphasis placed on "rapid".
- Navarre, Florida
Q. We are thinking to purchase a vibratory polishing machine for ABS Plastic (for injection molded ABS plastic).
We are looking for this solution as we think that it will improve the Surface Quality (it will smooth the top layer of our product which is molded ABS plastic component). We want to improve the surface of our product because we want to METALLIZE (CHROME FINISH) our product.
I want to know if this process will help us improve CHROME FINISH on our product.
Please tell that are we on the right track.
Looking forward for your expert advice.
- Delhi, India
August 7, 2014
Metal parts via 3D printing
Q. Hi,
3D printers are receiving a lot of attention in the news these days, because they are seen to be a potential disruptive technology. However, most devices of this type are very limited in the materials they can work with, mainly fabricating models in plastics like PLA or ABS. Advanced high-end models which do work with metal (eg. Selective Laser Sintering or Electron Beam Melting machines) require a build chamber to either be under vacuum or else filled with an inert gas, in order to prevent oxidation of the metal being used to form the part/model.
Could laser-accelerated electroplating or electroforming be used as the basis for a 3D printing approach which additively fabricates macroscopic parts or models from metal? I emphasize 'macroscopic', because the method already seems to have been investigated for fabricating metal microstructures - but I'd like to know why it couldn't be used in conjunction with stereolithography to make larger metal structures on the order of many centimeters in length width and height?
Consider for a moment the 3D stereolithography printer, which can manufacture plastic models using a UV-laser to solidify a UV-curable liquid polymer. A thin layer of liquid polymer is hit from below by the lasers, causing it to solidify wherever hit, and the resulting shape is slowly pulled out of that liquid layer from above.
I was wondering if a similar approach could be taken by using the method of laser-enhanced electroplating, and substituting the UV-curable liquid polymer for a solution of metal ions. I was thinking that laser-enhanced electroplating by way of the Soret Effect might result in an electroformed metal shape which could be created and slowly pulled from the liquid layer from above.
Here is some info I looked up online in a book called 'Modern Electroplating' ⇨
"The development of laser-enhanced electroplating process offers a promising technique for high-speed and mask-less selective plating and/or as a repair and engineering design change scheme for microcircuits [300, 325-28]. For this, temperature is used to modify the position of the equilibrium potential in a localized region so that electro-deposition is driven by the potential difference between this region and the non-irradiated regions. Use of a focused argon laser beam (488nm) in an acid copper solution provided plating rates as high as 25µm/s [300]. Bindra et al [327, 328] discussed the mechanism of laser-enhanced acid copper plating and Paatsch et al [329] reported on laser-induced deposition of copper on p-type silicon. It was demonstrated that the increase in the plating rate under laser illumination results principally from photo-induced heating of the electrode surface [328]."
I think a 3D printer based on electroplating/electroforming would be cheaper than existing metal 3D printers using SLS or EBM, because it doesn't require your build chamber to be under vacuum, or filled with an inert gas. And a theoretical build speed of 25µm/s seems quite significant - that's 1mm every 40 seconds, or 1cm every 400 seconds. Theoretically, you could print a 30cm tall model made of metal in 200 minutes - put all those old pennies to good use. Even if your real-world build speed was only half that, it would still compare quite favorably with existing consumer 3D printing systems.
It seems to me that a 3D electroplating approach could bring 3D printing of metal parts into the home consumer market. After all, there are plenty of consumer-level home-electroplating kits sold to for people who plate their own jewelry, etc. So electroplating is not some exotic technology, and electroforming is just electroplating taken to greater lengths/thicknesses.
As a college-level student, I don't really know much about electroplating other than having done it in some lab classes, and was looking for a knowledgeable forum like this where I could to ask questions about it in relation to 3D printing. I was wondering about whether I could use a small diode laser of reasonable power to shine it on some electroplatable cathode, to see if it produced any noticeable enhancement in the electroplating effect at that spot. I don't know what the current modern state of the art is in electroplating/electroforming/electrodeposition technology, but I've read that electroplating can be enhanced by the Soret Effect, and that this is the basis for laser-assisted electroplating. So I wanted to find some way to test it out as a proof of concept, with an eye towards using it for 3D printing.
If anybody has any answers, I'd appreciate it. I find this 3D printing stuff fascinating, and I think it's a matter of finding new ways to do it, in order to be able to print in new materials. I feel printing metal parts by electroplating would be a great idea to explore and tinker with. Sorry if this is a long first post - I hope you don't mind - after reviewing some of the great answers on this forum, it seems to be the most knowledgeable place on the net for this subject.
Student, Hobbyist, Tinkerer - Toronto, Canada
February 26, 2013
A. Hi Sanjay. Yes, 3D printing is one of the most exciting and disruptive technologies of recent decades. While direct 3D printing in metal requires development efforts that may be beyond the resources of most plating shops, hopefully some plating shops are already taking advantage of plastic 3D printing:
Something which I haven't seen much of yet, but which seems such a natural, is electroforming onto 3D printed plastic mandrels. This would allow the plating shop to go directly from a computer file to the metallizing tank with no wasted fabrication of mandrels and their tooling.
I've also read of the fabrication of a strong metal latticework lighter than dandelion fluff created by laser forming the matrix in polymer, electroless nickel plating it, and then dissolving away the polymer (http://www.dailytech.com/New+Metal+Nanomesh+is+Nearly+100+Times+Lighter+Than+Styrofoam/article23318.htm ⇩)
Regards,
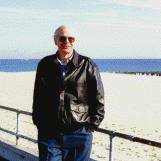
Ted Mooney, P.E.
Striving to live Aloha
finishing.com - Pine Beach, New Jersey
[Ed. update: The above link is broken. Thankfully, the Internet Archive preserved a copy here

These days information often appears on the internet, then disappears forever. If that is a concern to you please consider a donation to The Internet Archive.
A. Hi Sanjay
About fifty years ago, I was working for Kodak in the research lab on photoresists. One experiment was shining UV light into a liquid polymer to obtain a solid shape which remained when the liquid was poured off. This was long before the days of CAD drawings or computer driven printers and the project was not pursued.
About fifteen years ago, in another lab, engineers started to complain at design meetings that their new rapid prototyping kit produced wonderful 3D models that had limited use because they were too weak to handle. No problem. A quick trip to the plating shop and next day I was able to return the first models with a solid coating of copper (or nickel, whatever, you name it.) If you don't want a plated part, dissolve out the polymer and you have a perfect mould tool. As far as I know this is still standard practice, well developed, simple and cheap.
Full marks for the suggestion of enhanced plating but I have only heard of it applied to growing simple pillars. I would expect light scattering to be a problem in any practical solution. Add micro and macro throwing power and I think you would be looking at the thin end of a large research program.
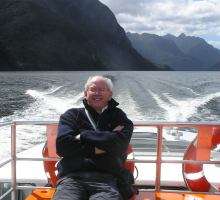
Geoff Smith
Hampshire, England
A. Hi there,
There was much work done at IBM on laser enhanced micro-jet plating in the 1980's. Use the key search phrase "jet plating" and see if that gets you the articles.
My PhD thesis at the University of Washington (Chemical Engineering) was on developing a tool we called "Electrochemical Printing". We had a rastering micro-jet electrode that could deposit (or pattern) freeform extended 2D micro-patterns of copper, nickel, gold, platinum, and rhodium. The micro-jet had an anode upstream of the nozzle opening and therefore confined the deposit to an area just near the micro-jet opening. Localized "dots" or "pixels" of metal were deposited point-by-point at locations and operating parameters (current, flow, fly-height, charge) according to those defined in custom software.
We started a company (Ionographics and later MicraMetal) on the concept but found gaining traction in the marketplace difficult. Basically, lots of people were excited about the concept but no one could justify funding the NRE to develop fully production worthy machine.
-Jeff
- Seattle, Washington, USA
A. Look up Microfabrica, they are doing amazing stuff.
steve hackLogus Microwave - WPB, Florida
May 28, 2014
courtesy of Microfabrica
Thanks Steve. Mind blowing! Complete pre-assembled machines the size of a pinhead made by electroforming.
Regards,
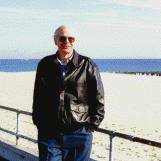
Ted Mooney, P.E.
Striving to live Aloha
finishing.com - Pine Beach, New Jersey
Q. Hey sir,
Can you please mention any process to plate 3d printed materials with ABS or PLA material using any metal finish.
- trivandrum, India
May 12, 2015
A. Hi Vineeth. You can see from this thread which we attached your question to that electroforming of copper or nickel onto ABS should be quite doable. Good luck.
Regards,
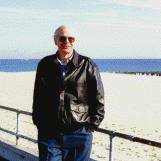
Ted Mooney, P.E.
Striving to live Aloha
finishing.com - Pine Beach, New Jersey
Etching and electroplating 3-D Printed PLA Model
Q. Hello sir,
I modeled a part with PLA plastic. Now I have many questions in mind.
* part finishing
* electroplating or giving any type of metallic touch.
Now I have tried acetone for surface finishing but it didn't work actually, or I didn't do it well. Please help me regarding accurate method for part finishing and etch process for PLA, after which electroplating or metallic finish can be given.
nsic - palwal, haryana, India
September 7, 2016
A. The Acetone treatment is for ABS 3d prints, PLA pieces will need to be processed by hand with fine sand paper to remove all of the imperfections
As for plating the piece, there are many ways to do that, electroless nickel plating is an excellent option, copper electroforming using conductive paint is another one.
- Managua, Nicaragua
Plating of 3-D Printed Plastic Parts?
Q. SIR, HOW CAN I USE VIPER RESIN PART FOR ELECTROPLATING OF GOLD OR SILVER WITH 3 MM THICKNESS . PLEASE DESCRIBE BRIEFLY.
THANKING YOU IN ADVANCE.
- MUMBAI, MAHARASHTRA, India
October 12, 2016
A. Hi Prateek. By 'use Viper Resin', I assume you mean how can you create a part by 3-D printing using this resin, and then gold or silver plate it?
Yes, you 3-D print the part, then you can metallize it with conductive ink or conductive paint or electroless plating technologies, and then you can do the electroplating. But 3 MM is very very heavy plating, about 100X typical plating thicknesses.
Obviously, each of these three steps are the subject of many threads here if you search the site, as well as books; but if you spend a few paragraphs telling us what you have experience in, and what you don't, we can start narrowing in on the things that may be most helpful to you. Good luck!
Regards,
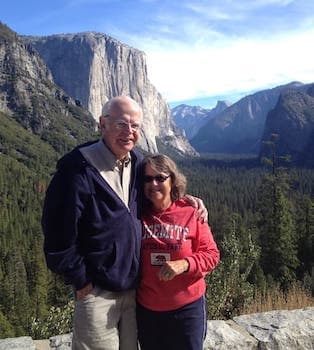
Ted Mooney, P.E. RET
Striving to live Aloha
finishing.com - Pine Beach, New Jersey
Q. Thank you Sir For Your Reply,
Sir, You Are Right about 'VIPER 3D', My thought is to build a round ring with solid elliptical shape, having diamond groove and prong for diamond placement. Then I would coat it with a thickness of 0.8 mm which is necessary for diamond holding. Finally, I would drill at bottom to remove the resin via heating. It would help me create a hollow ring which would look a huge one but with less weight.
- MUMBAI, MAHARASHTRA, India
A. Hi again. I'm not familiar with the Viper resin, but it is possible that it can be melted or otherwise dissolved away. So, if you have the 3-D printing mastered, your project doesn't sound much different than the electroforming of hollow gold jewelry, which is traditionally done on wax. Good luck
Regards,
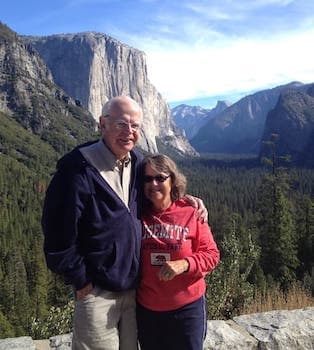
Ted Mooney, P.E. RET
Striving to live Aloha
finishing.com - Pine Beach, New Jersey
Electrodeposition for creating objects
Q. Hello, I am new to electroplating but I have done some searching (looking to get some books) and wanted to know if it was possible to create objects using electrodeposition. For instance, if I were to 3D print a mould for a specialised part for something (say, a pole. For the mould: imagine a hollow tube with a small hole at each end, one for a wire, and one for the liquid to pour into) and placed the partially enclosed mould into a bath, would I (after a long time) end up with the solid object that the mould should have contained? (the pole). This would make it possible for me to produce parts that I otherwise wouldn't be able to obtain.
Thanks for your time
Cameron
Student - Batemans Bay, NSW, Australia
October 11, 2017
Hi Cameron. It is very common to make metal parts by electroplating; when the plating layer itself becomes the "object" we often call the process "electroforming" rather than electroplating.
Examples of such stuff include hollow teardrop earrings which are made by plating gold onto a wax teardrop then melting away the wax; vinyl record stampers and CD molds made by nickel plating onto a lacquer master; miniature bellows made by plating onto an aluminum core and then dissolving the aluminum; flower and leaf jewelry made by copper plating onto nature's creations, etc.
But your problem is different in that you are trying to fill a cavity and it is very difficult to get plating to build up so uniformly, and the way you wish, as to achieve that. If you picture trying to fill that small tube by pouring in gravel instead of fine powder you'll visualize the general issue. But it is possible to plate the inside surface of a tube, so, depending on the dimensions, electroforming a hollow pole may be possible ... it's just that it would probably be much easier to do it the opposite way, plating onto a mold which matches the desired inside diameter of the pole rather than it's desired outside diameter :-)
Luck & Regards,
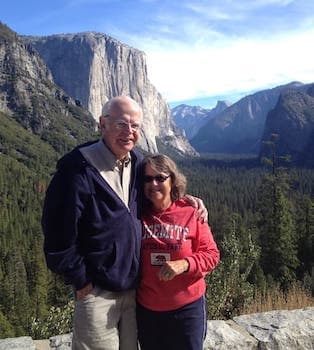
Ted Mooney, P.E. RET
Striving to live Aloha
finishing.com - Pine Beach, New Jersey
Etching SLA PR48 resin for electroless copper coating
Q. I am working on a process to electrolessly plate SLA printed parts
(Autodesk PR48 resin) with Copper .
I want to ask the professionals here, how do you successfully etch SLA printed parts for wettability, chemically without damaging the minute details on it
My electroless solution does not seem to 'stick' to the smooth SLA surface .
I tried piranha (H2S04, H202) solution , but that was clearly too strong for the part.
I am looking at potassium permanganate
⇦ this on
eBay or
Amazon [affil links] solution, but I have no clue if that would work to etch the Printed parts
Student - Toronto, Ontario, Canada
November 15, 2017
Adding a mirror finish to SLA parts
Q. I am prototyping an concave mirror using a Formlabs 3 SLA printer. I am using their clear material and printing at 25um resolution.
I can successfully produce optically clear parts with post processing. Sanding/polishing.
I am looking to print a small 4"x6" concave mirror, post process it to an optically clear finish. Then I am looking for a process to apply a mirror finish.
I am ideally looking for a product that I can use in the lab. I believe that I could send it out for plating, however I am hoping to find a quicker process.
I don't care too much about the "brightness" of the reflection as this is only the prototype and a proof of concept for a design that will eventually be sent out for mass production.
Are there any products out there that will produce a reasonable mirror finish on UV cured plastic, if not, what would be the best/quickest process?
Engineer - nelson, BC Canada
January 15, 2020
A. Hi Rick. It sounds like you have several options:
1. Per this thread which we appended your inquiry to, it seems possible to nickel plate or nickel-chrome plate it, although this doesn't sound like something you can do yourself.
2. You could do conventional mirroring to the back surface, as is routinely done on glass mirrors, and which you could probably do yourself.
3. You could do "chrome look paint" on the front surface, but while you could do this in house, for a 'proof of concept', your first attempt probably won't be great :-)
adv.
Gold Touch [a finishing.com supporting advertiser] or G.J. Nikolas [a finishing.com supporting advertiser] can probably advise on approach no. 3.
One of our readers, Marvin Sevilla, seems to have a great deal of experience in this kind of stuff, and we'll copy him on your inquiry; with luck he may chime in :-)
Regards,
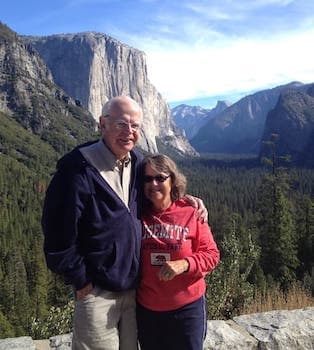
Ted Mooney, P.E. RET
Striving to live Aloha
finishing.com - Pine Beach, New Jersey
Q. Thanks Ted,
I will be sending prototypes out for plating, but I first want to do some rapid in-house proof of concepts so that I don't waste time/money on bad designs. So you have a list of companies that do one-off prototype platings?
The conventional mirror back surface does not work with the final design concept. It needs to be a primary surface mirror.
I have been looking at option 3 "chrome look paint". Do you have any specific suggestions on brand? I have been looking at [brand name deleted by editor], but they seem to get very mixed reviews.
valid manufacturing - nelson, bc, Canada
A. Hi again Rick. You can ask people to privately contact you about your commercial needs by posting an RFQ for a plating shop or a chrome-look paint supplier (or just advise and I'll attach a link here to your contact info). But, sorry, we can't publicly suggest brands or sources except clearly marked advertisements ( huh? why?). Apologies.
Regards,
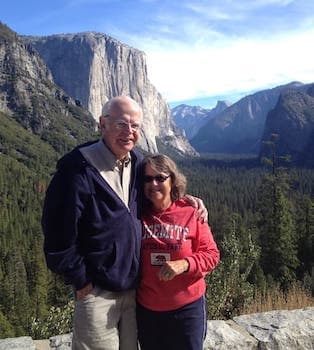
Ted Mooney, P.E. RET
Striving to live Aloha
finishing.com - Pine Beach, New Jersey
A. Hello Mr. Gostlin.
What you are trying to achieve is what is called a front surface mirror, the easiest way is to use the ready to pour silvering chemicals from angel gilding, but silver is quite delicate and will tarnish without any protective coating(which will take away the whole front surface mirror and will be like any other mirror), the other way would be to apply a Nickel or Cobalt (or Nickel/Cobalt) layer using an electroless process (electroless nickel plating), I used Angel Gilding Tin Chloride sensitizer and their Palladium Chloride activator with a third party supplier for the regular off the shelf electroless nickel chemicals (ready mixed).
The least expensive way will be to use a "Mirror Like" Spray paint, there are only two available in the market (not named chrome paint) I have tested both and both produced outstanding results, if I had to chose one I would say the one with the brand name starting with K is the best one you can get (google diy mercury glass and you will see many tutorials) but since it's made to go on glass surfaces you will need to make sure the surface of the piece is glass like(as in gloss and solvent resistant). so that means that coatings or surfaces that get affected by the solvents in the spray paint will need to be solvent resistant(so no lacquers, no enamels) I have used automotive grade 2k Urethane clear coat on top of a base coat, luckily for you they are available in spray cans too(the black matte base coat and 2k Urethane coat), leave the piece curing for at least 48 hours before attempting to spray painted with the mirror like (looking glass) paint.
Marvin Sevilla- Managua, Nicaragua
Q. Hello, my name is Ben Awes. I am an architect in Saint Paul, MN. I have a commission for a cross at a local church and am pursuing 3D printing in metal. The cost of 3D printing will determine what metal I use, either 316L stainless, aluminum, bronze, or a "steel" alloy of 60% 420 stainless + 40% bronze.
The most likely is the steel alloy because of cost and the capacity to do much larger prints.
My question is, can I plate this alloy after printing? I know very little about plating and I can find a lot about plating individual metals, but nothing about plating strange alloys.
It might be helpful to know that the process is one where stainless powder is used with a glue binder in the printing process, and then the glue binder is removed and replaced with bronze in an infusion process. It's not actually an alloy.
Any thoughts or experience with this?
Thank you,
Ben
- Saint Paul, Minnesota
February 5, 2020
A. Hi Ben. I don't have specific experience in that, but the two possible issues you may face is the difficulty of plating onto two different substrate materials, and the possible porosity since I doubt that the bronze infusion process is 100%.
An alternative you might consider is electroplating or electroforming onto a 3D printed plastic substrate (basically we call it electroplating if the plastic is providing the structural integrity, and electroforming if the plated metal is thick enough that it provides the mechanical structure).
3D printed metal came too quickly for me; I no sooner realized how great a technology electroforming onto 3D printed plastic would be, than it already had a competitor.
Regards,
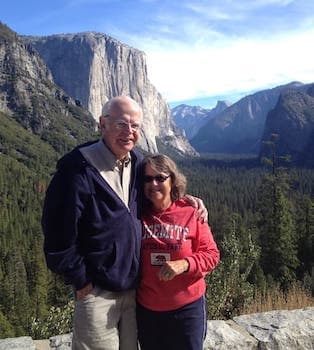
Ted Mooney, P.E. RET
Striving to live Aloha
finishing.com - Pine Beach, New Jersey
Hi Ben,
The people I know who have done it mostly work with smaller parts (jewellery / model railway type) but have you considered using lost wax (investment) casting with 3D printing in a polymer (or directly in wax)?
This would allow you to cast in a metal which is easier to plate - it's a really nice technique and may well be cheaper than directly printing in metal.
I think this video gives a decent overview of the process:
www.youtube.com/Un3dpy9Og5Q
- Gloucestershire, UK
Ed. update: Unfortunately that video is no longer available.
Q. Dear Geoff Smith, first of all: Thank you to you and all other participants for posting so actively, openly and constructively on this very nice forum! Your comment made me wonder which polymer and metal combination you are referring to here. For the case of copper as the electroplated metal I have been having trouble to find a 3D-printable material that can be properly dissolved away. I am referring to SLA/DLP-type 3D printing here. Do you happen to have any pointers?
Andreas FrölichEngineering / RnD - Karlsruhe, Germany
June 5, 2022
Q, A, or Comment on THIS thread -or- Start a NEW Thread