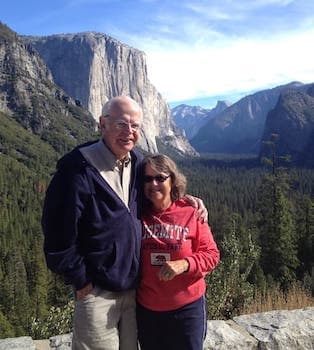
Curated with aloha by
Ted Mooney, P.E. RET
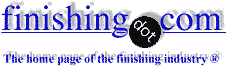
The authoritative public forum
for Metal Finishing 1989-2025
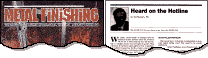
-----
Material Defect or Hard Anodizing Defect?
Q. My company sent machined aluminum rings to be anodized with a hard coat. They returned with blotches across the interior. The plater later stripped the anodize and revealed the same blotches. The plater said it is due to the material, but we did not send the rings with these blotches beforehand. The plater claims that the anodize can accentuate these blotches.
Do you have any thoughts?
Paul Buckley- Stoughton, Massachusetts
April 7, 2025
A. Hi Paul.
The appearance of the same pattern after removing the anodizing is evidence that a material defect MAY be causing the problem, but it is not proof because the etching operation by the anodizer might have caused it.
But we have appended your inquiry to previous inquires on this subject, and if you proceed as Willie suggests though, you will have quite conclusive evidence whether it is the material or the anodizer.
Thread 150/48 deals with pretty much the same subject if you want additional opinions & insights.
Luck & Regards,
Ted Mooney, P.E. RET
Striving to live Aloha
finishing.com - Pine Beach, New Jersey
A. If caustic etching is performed on 2000 series aluminum, specifically 2024, the material will freckle. That does not make it bad material but rather it is a reactive process.
Philip J. VerzalRetired - Newport, Tennessee
A. This issue is typically seen on extrusions but other manufacturing methods can show these "splotches".
It is known as coarse grain structure, and for extrusions, it is in part the heat treatment of the billet and in part the contaminants that from the shell of the billet that gather in pockets within the extruder and slowly gets dragged out towards the end of the billet.
But heat treatment alone can cause the issue, as it is a type of crystalization in the aluminium that creates these "coarse grains" in it, that can seem almost reflective under light.
The problem is, you cannot see it before surface treatment, and typically it is the etch that brings it out. We've seen a multitude of examples of this over the years and as an anodizer, there is very little we can do about it, as it is in the base material.
Given that these parts are also hard anodized, probably doesn't help either in how clearly you see it after the anodizing.
So, as you said, you didn't send them rings with splotches on them, but sadly that doesn't mean that the aluminium structure was free of coarse grain.
Information ⇨
[M. Stammerjohann provided the links to the two papers shown at right] ⇨
Production Technician - Horsens, Denmark
April 8, 2025
Thanks Phil!
Thank you M. Stammerjohann!
Paul Buckley [returning]- Stoughton, Massachusetts
April 8, 2025
A. My best guess is you are seeing the grain structure in the base aluminum. Etching and/or stripping will tend to bring it out. We had a similar problems with extruded 6061 parts. One extrusion expert told us it was due to the in-line heat treating process used by extruders. We eliminated it by re-heat treating the parts in a batch process.
Chris Jurey, Past-President IHAALuke Engineering & Mfg. Co. Inc.

Wadsworth, Ohio
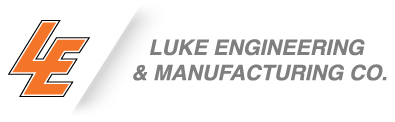
This is the procedure from our plating vendor. I am sorry I am not an expert on this stuff.
1. Vapor Degrease per Procedure WI-0018 for a maximum of 2 Hours. Step Performed: Y N
Allow parts to dry completely before proceeding.
2. Alkaline soap cleaner Ambient - 150 degrees F. 5 to 30 minutes.
3. Visually check parts to ensure they are free of all foreign substances, oxides and soils such as
greases, oil, paint and welding flux. If not, etch as needed or per special instructions on the job card.
135 - 145 degrees F for 1 - 60 seconds. ***MAXIMUM***
4. Ambient counterflow rinse.
5. Non-etch acid desmut 2 to 5 minutes.
6. Ambient counterflow rinse: Perform Water Break test per WI-005.
If test fails, repeat steps 2-6.
7. A) For 5000, 6000 series and die cast alloys - Sulphuric acid anodize, 5 minute ramp at: 26 - 34 degrees F. at 30 Amps per square foot.
B) For 2000, 7000 series and MIC-6 alloys - Sulphuric acid anodize, 5 minute ramp at: 26 - 34 degrees F. at 30 Amps per square foot.
Amps: ___________ Duration of ramp up: ___________
Immersion time (minutes): ___________ Duration of ramp down: ___________
14 8. Rinse.
15 9. Nitric acid post dip if casted part or MIC-6. 10 to 15 seconds.
- Stoughton, Massachusetts
April 9, 2025
⇩ Related postings, oldest first ⇩
Q. Hi! All,
Been facing some serious problems of late with 6061-T6 Aluminium extruded material. Please see if any of you can offer me some advice -- will be grateful for any inputs.
We have successfully churned out this same grade for the last few years. We anodize to MIL-A-8625-F, 80 microns. We get a uniform dark grey almost black shade - Type III Class 1.
Of late with some batches we are facing the following defects:
- Golden colored spots randomly distributed over the cross section of the plate that we machine.
- Also, wrinkled or wavy texture on the face and also the outer diameter surface - on some of them we can actually touch and feel its waviness! The strange thing it is entirely UNDETECTABLE until after it comes out of hard anodizing! Even checked the surface right after machining and then after the pre-cleaning De-Ox solution before anodizing - but there is nothing detectable at all. I am baffled! At the outset, it appears like a raw material defect but just want to be sure that it has nothing to do with our anodizing. Attaching some pics. If anyone needs anything more in the form of details, please ask. Need to sort this one out asap ... Thanks in Advance,
Ravi
- India
September 18, 2012
A. Ravi
It looks like a material related defect.
To confirm, I would strip and examine, and then re-anodize to see if it re-appears in the same spot. Then strip, take a skim cut (~.003") off the face and re-anodize. Another option is to have one of your competitor friends anodize it. If all options show the defect in the same location(s), I would consider that conclusive.
- Colorado Springs, Colorado
Q. Dear Willie,
Thanks for your kind response.
In fact I already tried all that you have suggested and the defect still appears. Also renewed all the solutions in the process and reconfirmed that the culprit was not the anodizing process.
It does appear to be a material defect - something related to either the heat treatment or the liquid metal solidification stages during the manufacture. Have initiated the matter with the mill and await the findings. Will post findings when they report something.
- India
A. Ravi
In a past life, we had a customer who purchased large lots of extruded aluminum, and they would slice a sample off the end of each bar and have them anodized to see if a similar flaw was present. This minimized the number of parts exhibiting the noted condition.
- Colorado Springs, Colorado
Thanks Willie,
Q. Tried that too, unfortunately, no pattern emerged, the rods inside had the defects even if the ends did not exhibit any.
- India
A. Hi Ravi.
That part sounds a bit strange because extruded aluminum, as far as I know, is continuous extruded and then sawed to length. So some phenomena that occurs near the middle of a sawed off length, and not at the ends, seems to me to lack cause-and-effect, although I suppose it could have something to do with straightening rollers or something like that.
Regards,
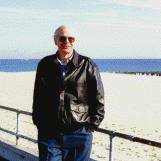
Ted Mooney, P.E.
Striving to live Aloha
finishing.com - Pine Beach, New Jersey
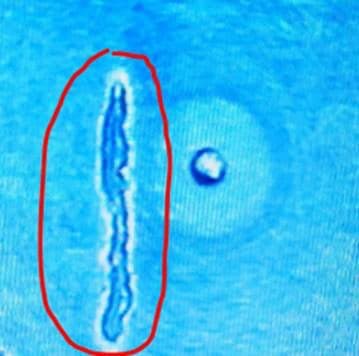
Q. Hello, our hard-coated parts were rejected due to the accumulated deposit on the coated surface.
The part's dimension is 3 mm x 3 mm and is made from Aluminum 8000 series.
When we asked our coating subcontractor about the deposit, they claimed that it's impossible for excessive deposit to develop on hard-coating.
Is it true? What are other possible causes for the formation of excessive deposit on hard-coating?
- Johor, Malaysia
September 17, 2019
A. Hi Al. Hopefully a manufacturer of similar parts will recognize your picture and understand; sorry, but I have no idea what that photo is or means :-(
Regards,
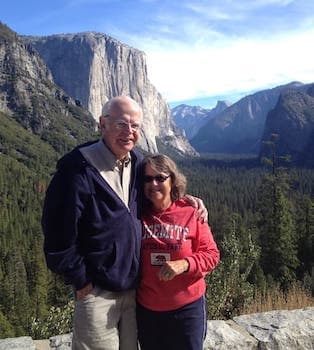
Ted Mooney, P.E. RET
Striving to live Aloha
finishing.com - Pine Beach, New Jersey
Q. Hi Ted. Thank you for responding, anyway :).
The photo only shows the surface of the hardcoated part. The area circled in red is what I thought excessive deposit from hardcoating.
But, as mentioned previously, our subcontractor claimed that the area circled in red is due to the flaw in raw material and not caused by hardcoating process.
They claim that it is impossible for excess deposit to ever occur on hardcoating process.
Is it true, though? What are other factors that could contribute to the bulging area?
- Johor, Malaysia
Q, A, or Comment on THIS thread -or- Start a NEW Thread