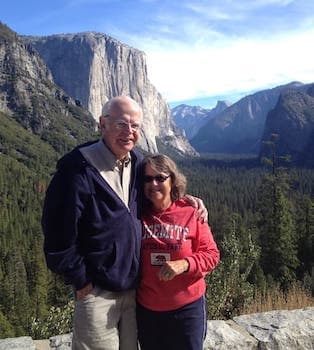
Curated with aloha by
Ted Mooney, P.E. RET
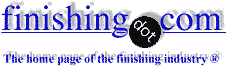
The authoritative public forum
for Metal Finishing 1989-2025
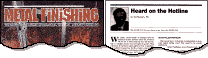
-----
Blotched areas on Clear Anodize, Material or Plating problem?
Q. We assemble a product (peristaltic pump) that requires a half a dozen or so Clear Anodized parts. These parts are on full display on the Front Panel of our pump. Sporadically the parts exhibit mottled or blotched areas. On the thin parts it appears on both sides of the part in corresponding areas. It almost appears that the indications are in the metal. The material is Aluminum 6061-T6 and the anodize process is Sulfuric Anodize Per MIL-A-8625 / MIL-PRF-8625 [⇦ this spec on DLA] Type ll Class 1. There is also an etch performed before the anodize process to give it a satin appearance. The parts are then hot water sealed at the end of the process. What can I do to assure a uniformed look. I can change material/temper but I still need a satin look. Note: These parts are not tumbled or glass beaded at any time. They are handled with cotton gloves to prevent contamination.
Jeff Cogger- Vergennes, Vermont
2002
Treatment &
Finishing of
Aluminium and
Its Alloys"
by Wernick, Pinner
& Sheasby
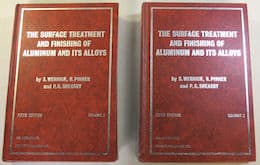
(note: this book is two volumes)
on eBay or
AbeBooks
or Amazon
(affil links)
A. Quality Control is your answer. Be sure the deoxidizer is a mixed acid system that works on 6061, be sure the dissolved aluminum in the anodizing solution is under 12 gm/L as it will occlude in the pores and give splotchy finish. Be sure there is a 5% Nitric Acid dip between the anodizing and the seal to help flush out the viscous Sulfuric Acid so that the seal can get into the pores and hydrate the pores. Be sure the seal is deionized water and that no calcium tap water has dragged in, be sure the seal pH is help in spec.
If there is zinc anywhere in the line from 7000 alloys or if there is calcium from hard water, then you may expect these elements to form compounds that occlude in the pores and/or lay on the surface and cause smears and white spots.
Take two aspirin and call me in the morning.
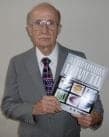
Robert H Probert
Robert H Probert Technical Services

Garner, North Carolina
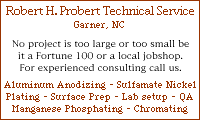
A. There are several "satin" etches that will give you the glass bead appearance without the mechanical damage that blasting can give you. We call ours "606 Etch" and it's typically used prior to black anodize to give a non-reflective, optical black coating, however, works beneath straight sulfuric anodize as well.
The advice from Robert Probert is quite good for your anodizer, however, doesn't help the parts' manufacturer much!
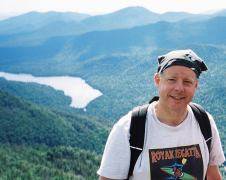
Milt Stevenson, Jr.
Syracuse, New York
Q. Thank you for your response Robert. One detail I forgot to mention is that all the indications are in the same place on each part. They are not areas that would entrap the solution or hold a drop, or dwell during drying. Moreover if you were to imagine a length of bar stock and line these parts in a row as they were machined, the blotches would run in a straight line parallel to the length of the bar. It is as though there was a soft spot running through the bar that anodized differently. It is like cutting paper dolls, all the parts have the same blotches in the same spots. Some however are worst than others. This may be a coincidence, because I get similar indications on other parts using the same process but in random areas.
Jeff Cogger [returning]- Vergennes,Vermont
2002
A. We had the same problem with a forged part on a race car, and through an aerospace customer determined that the forging process resulted in a slightly non-homogeneous material makeup, resulting in dull areas. This accounted for the consistency of the 'flaws'. Before this, we tried everything with our anodizer, as well as changing out all of our machining fluids and cleaning chemicals, which all helped us get in better sync with our anodizer, resulting in better quality parts overall. But in the end it was the forging that was causing the problems.
Josh Poertner- Speedway, Indiana
A. Oh man ... please don't get me started again on the inconsistencies of aluminum produced by the big manufacturers! See letter 14229, "Clear Anodizing - Matching 6061 and 6063". I could gripe about this for hours ...
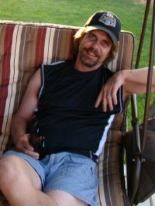
Marc Green
anodizer - Boise, Idaho
Q.
Hello Everyone,
I'm a chemist entering this new area of anodizing; I'm having some trouble. A photo of the piece is attached.
Here are the specifications.
1. Brushing with Steel wool for mechanical cleaning
2. Rinse in water.
3. Rinse in a NaOH solution 10% for 3 minutes.
4. Rinse in water.
5. Rinse in nitric acid 20% for 3 minutes.
6. Rinse in water.
7. Anodizing in H2SO4 18% (v/v), 12 volts DC for 1 hour.
8. Rinse in water.
9. Rinse in Cobalt chloride 10 grams/L for 3 minutes.
10. Rinse in water.
11. Rinse in potassium permanganate
⇦ this on
eBay or
Amazon [affil links] for 3 minutes.
When I take the piece from this solution, it is already visible the spots.
12. Rinse in water.
13. Rinse in sealing solution of Nickel.
The color is pretty irregular and I don't know what's wrong. The aluminum piece is 6063 alloy.
Any suggestion will be of great help. Thanks in advance.
Hobby - Sao Paulo, Brazil
November 22, 2013
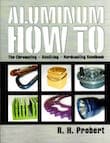
Aluminum How-To
"Chromating - Anodizing - Hardcoating"
by Robert Probert
Also available in Spanish
You'll love this book. Finishing.com has sold almost a thousand copies without a single return request :-)
A. Alexandre
Use a synthetic abrasive pad in lieu of the steel wool.
- Colorado Springs, Colorado
Q. Okay, but do you think the conditions of the experiment are okay?
Alexandre Barros [returning]- Sao Paulo, Brazil
A. Alexandre
What is the purpose of your experiment? Can you expand some on your post-anodize process parameters, i.e., time & temperature?
- Colorado Springs, Colorado
A. Hi, Alexandre. I am not personally familiar with that process sequence and don't off-hand understand the reason for your cobalt chloride and permanganate steps. But if you can tell me where you read of that process sequence, or what those steps are supposed to do, I may be able to comment.
It's tricky when you present something unknown to me, which seems to introduce extra complexities, and ask whether it will work. Instead of guessing about this sequence's suitability, I'll suggest that if you truly are entering a new area as a beginner, please consider following simpler more typical sequences, perhaps consulting introductory books like Probert's "Aluminum How-To". Good luck.
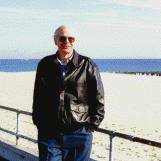
Ted Mooney, P.E.
Striving to live Aloha
finishing.com - Pine Beach, New Jersey
Patchy spot on 6061 material
Q. Hi! I found patchy spot on 6061 material randomly in a same batch of part (as photo attached) after Type II anodizing and color dyed.
I did inspect the bare part's surface and didn't really notice any patchy spot. But once it came off from etching and desmut baths the spot will become barely noticeable. Can this be something wrong with my pre-treatment processes? Or can it be the raw material problem?
Or could it be due to the poor coolant maintenance of our customer's CNC machine?
Thanks in advance for any advice and information sharing.
- Malaysia
February 25, 2016
? Good day Sun.
Why are you etching 6061 (1% Mg)? Are these parts heat treated?
Regards,
Aerotek Mfg. Ltd. - Whitby, Ontario, Canada
![]() |
Q. Hi Eric, - Selangor, Malaysia ? Hi Sun, - turkey, sakarya |
A. According to the images I think the material is an extruded profile or bar. The surface problem is a material problem. I suppose that there are coarse grains in the surface zone (big grains). No direct influence of surface treatment. With an investigation (Metallography, grain) you can confirm this.
An improvement in press conditions / Press Quality is necessary.
AluSolutions- Hallau, Switzerland
Q. Hi Alaattin,
1) The chemical composition as below.
Al - 95.8 - 98.6%
Cr - 0.04 - 0.35%
Cu - 0.15 - 0.4%
Fe - Max 0.7%
Mg - 0.8 - 1.2%
Mn - Max 0.15%
Si - 0.4 - 0.8%
Ti - Max 0.15%
Zn - Max 0.25%
2) The defect rate is around 30% and mostly the patchy only appears on some surface of the part (not all over).
Hi Joerg,
Thanks for your comments and advice.
- Selangor, Malaysia
A. Joerg is absolutely right. It is also well known as PCG problem, i.e., Perirhoral Coarse Grain, and generally it happens during extruding low extrusion ratio profiles, or shapes. If these areas are examined metallurgically (as suggested by Joerg) then there will be a clear indication of recrystallized grains which occurs during extrusions. I don't think these materials can be salvaged. However, extruders should be aware of it and elimination can only be done at extrusion stage by selecting the right process parameters. Moreover, this alloy is more prone to have this problem. Extruders should be consulted to avoid this problem.
Good luck,
Emirates Global Aluminium, U.A.E. - Dubai, U. A, E.
March 12, 2016
"Mottled" surface of anodized EN AW 6061 parts
Q. Hi all,
We are a mid-sized plant focusing on CNC machining. Part of our production is aluminium parts for aviation. These parts are anodized (outsourced).
Recently we are having some problems with anodized parts of 6061. The surface color is not constant, you can see those spots and "marble like" structure. In one of the pictures you can see standard sample of our customer right next to the spotted anodized part.
Does anyone have experience with this problem? Thanks.
- Czech Rep.
November 10, 2017
A. If the anodizing shop is using straight NaOH to etch the parts, and the parts are left in the etch for a very long time (let's say 2+ minutes at 60 °C and ~30 gr/l concentration), then some materials tend to show this pattern, usually it is much more noticeable if the parts are reworked (because of some sort of problem during 1st time they were anodized), then the operator might have kept the parts for too long in the etch bath just to be safe that all previous anodizing has been removed, and it leads to this crystallization pattern to show (I'm guessing that is what it is), it is very noticeable on flat milled surfaces, not so much if the surface has been sanded or tumbled prior to anodizing.
Also it this might be very noticeable on one geometric surface, but not on a perpendicular one, which suggests it has to do with structure of the material itself - I'm not saying it is caused by the material, the cause is the long etch time and particular etch type, that is my opinion.
And another point, if the etch batch is not sufficiently hot, the parts that need to be reworked have to be kept there for much longer time that "normal", which might also compound the issue.
- Riga, Latvia
Q, A, or Comment on THIS thread -or- Start a NEW Thread