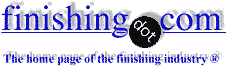
-----
How to get frosted look on metals?
Q. I have been struggling with getting a standard brushed/satin/frosted look on metals without electroplating.At Moradabad where we have our metal finishing shop, we use what can be described as a basic prototype of a sort of centerless grinding system. We somehow affix the pc.[only cylindrical] onto a wooden cutout which is mounted on a ball bearing with a handle.This is placed in front of abrasive grinder wheel rotating at 2800 RPM.Since the hand held pc. is not driven by any mechanical means it is forced to rotate by the grinding wheel albeit not at the same speed. This difference of speed causes scratches which give a matte/brushed effect to the surface. But this method is unsuitable for flat a surface also it is not accurate even for a cylinder. Are there any machine available to get this effect? What is the plating process to achieve this effect?
Thread 32950 discusses this "frosted" pattern on a Resophonic guitar ...
(photo courtesy of Bob Claborne, Eclipse Music, Garden Grove CA)
Manufacturer of metal gift items. - New Delhi, INDIA
July 29, 2009
A. Hi, Ranjan. It is hard to describe a finish in words, but glass bead blasting would be the most common way to give a metal surface a frosted matte look.
Regards,
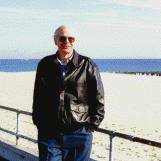
Ted Mooney, P.E.
Striving to live Aloha
finishing.com - Pine Beach, New Jersey
July 2009
A. Blasting is one way to achieve frosted look. You can also try a mass finishing using ceramic media if you have greater quantity; however, on softer metal, the appearance will be more of a galvanize appearance rather than frosted.
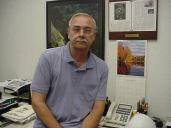
AF Kenton
retired business owner - Hatboro, Pennsylvania
August 3, 2009
A. Dear,Ranjana
Sand blasting is the best way to achieve FROSTED finish on the metal. But that finish is sensitive to finger staining. You have to apply top coat of matte lacquer.
Reg.
GULSHAN
- MORADABAD, India
September 4, 2009
A. In my industry I often use muriatic acid to etch or matte a finish on chrome moly and ordinary cold rolled steel. I just degrease the part and paint the acid on. It takes about
15 minutes to etch the part and I clean the acid off with baking soda [in bulk on
eBay
or
Amazon [affil links]
and water. The part can be heated a bit with a torch to aid the etching. (will not work on stainless and not well on chrome vanadium for some reason). The finish must be blued or coated to prevent rust.
I also use the old shazang finish. Coat the part with common grease and buff with a soft wire wheel at fairly high speed. You have to adjust the speed to the type of steel you are matting. To low a speed will not produce the desired finish. To high of a speed will dig into the material and make an uneven mess.
Note: (with stainless steel you can use a common a common chrome moly wire wheel). After buffing the stainless will be contaminated with the chrome moly from the wheel and the part can dipped in a bluing solution and it will turn a very dark grey.
Failure to grease the part to be buffed will cause the finish to have a defined grain running in the direction of the buffing. These finishes are not as dull as a bead blast but they are more resistant to scratching. Sand blasting or bead blasting gives the most even finish but it scratches easily.
Etching with acid does not seem to change the dimensions but wire wheeling (shazang) and bead blasting seams to increase the dimensions VERY SLIGHTLY!

Rod Henrickson
gunsmith - Edmonton, Alberta, Canada
September 9, 2009
Q, A, or Comment on THIS thread -or- Start a NEW Thread