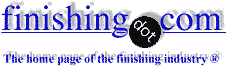
-----
Decorative Etching on Nickel Plate
Q. We restore musical instruments. What I need is a non-exotic way to do a decorative frosted etching on nickel plate. The desired effect would be similar to that obtained on glass by using Hydrogen Fluoride. Is ferric chloride going to do the trick or will I have to go with some sort of Nitric solution? I would need to know solution strength and working time in any case.
Thanks,
Bob Clabornemusic - Garden Grove, California, USA
2004
A. Hi Bob,
You may possibly be able to do a passable job of this via abrasive blasting and some practice; I don't think there's any way to do it chemically.
Satin nickel can be reliably done by either abrasive blasting before plating or with special additives in the plating bath.
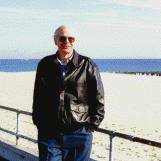
Ted Mooney, P.E.
Striving to live Aloha
finishing.com - Pine Beach, New Jersey
Q. Ted,
Thanks for the response. I understand what you said but a "satin nickel" finish is not what I'm after. This instrument is nickel plated (a smooth polish) with a floral pattern etched on the nickel. It was not beadblasted on _prior_ to plating as one can observe (what you would otherwise call) "overspray" outside the boundary of the design.
This certainly could be beadblasted on the nickel but the look of this "overspray" together with the uniformity and texture of the design would seem to indicate a chemical process; but, I defer to your expertise. Any further comment?.
Bob Claborne [returning]- Garden Grove, California
A. Hi Bob. I don't want us to get off-track based on semantics -- there is endless confusion/disagreement over what 'brushed nickel' vs. 'satin nickel' vs. 'pearlescent nickel' vs. 'matte nickel', vs. 'xxx nickel' looks like because there is no standards-setting body defining them, and slang runs every which way :-)
So, whether a finish that you describe as "like frosted etched glass" would be the same or different from what I describe as "satin nickel" isn't clear. Maybe a satin lacquer is playing a role? Please send a photo of it if you can.
What I'm saying is that I haven't personally ever heard of chemically etching nickel plating to an appearance anything like that, and I personally don't think it's promising. Hopefully another reader will differ.
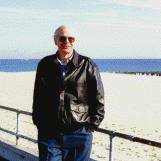
Ted Mooney, P.E.
Striving to live Aloha
finishing.com - Pine Beach, New Jersey
Q. Ted,
Thanks, again, I'll defer to your expertise on whether satin nickel or otherwise. I can say that it is not a satin lacquer or other coating over the nickel. Here is a photo--
Thanks again.
Bob Claborne- Garden Grove, California
A. From the picture, I will give a high probability that it was blasted with something like 200 grit aluminum oxide (not glass bead) using a rubber mask to protect the non etched areas and then plated afterwards. Nice work on it, done by a professional with experience. Pressure, insert size, angle and distance from the part all have significant influences. I will guess that it was an average size insert, slightly lower pressure and nozzle nearly 2 feet away from the part at very close to a 90 degree angle.
James Watts- Navarre, Florida
Q. Thanks for responding James. Blasted before plating... I guess I'll find out for sure when I have it stripped. This could present other problems. The blaster may have been a pro with experience (they turned out hundreds of these per week) but did a pretty sloppy job particularly with holding the mask down as (it may be difficult to see) there are elements run together and plenty of poor edge definition (overspray, for lack of a better word). If that blasting is deep in the brass, may not be able to polish it out and remask the design.
Any chance it was blasted after plating (I'll send you a high rez photo if you wish)?
Thanks,
Bob Claborne [returning]- Garden Grove, California
2004
A. I agree with Ted and Jim and would only like to add that there are finer sand grits that can do a more gentle and uniform etch. I would go for something like 320 or even 400 grit. Distance, angle and pressure are more forgiving when using such finer grades and the stencil is more likely to hold up.
Guillermo MarrufoMonterrey, NL, Mexico
2004
A. I hate to let Ted down, but I have to agree with him. The best way of doing what you want to do and from where you already are, is for the nickel to be shot blasted with very fine alumina powder. This can easily be done through a suitable mask and it will give you a good finish if done carefully. However, be warned, the technique is very non-forgiving and it is easy to overdo it, especially if the nickel is thin. If you were not at the stage you now are and were starting from scratch, I would suggest the abrasive route followed by a nickel plate; then any errors and any neatening up can be done by polishing prior to plating.
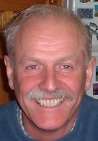
Trevor Crichton
R&D practical scientist
Chesham, Bucks, UK
2004
Q. Trevor,
Thanks for your advise. As to "where I am now"... What you see in the picture is the factory finish. What you cannot see are the sides of the instrument which have corroded. So, lamentably, the whole thing must be stripped and replated (unless someone thinks the sides can be stripped and replated by themselves). I'll be using the services of a pro plating house for sure.
I believe you recommended that the design be blasted prior to plating if possible. At the end of the day, reproducing the original look is key. I know it may be hard to tell from the picture, but which method do you believe was used by the factory; blast then plate or blast on the plate?
Thanks again,
Bob Claborne [returning]- Garden Grove, California
A. It is impossible to tell what process has been used from just a photograph. However, it is a thing of magnificent beauty and I can understand your desire to renovate it. If the other side has corroded as much as you say, it will be a complex job, so I would look for a truly professional restoration company; I would expect the corrosion pits will have to be filled in and then repolished to give a really smooth finish. Looking at the patterns, I would suspect it has been done with an abrasive powder blast, but using a well fitting mask. Anyway, a chemical based satin nickel didn't become commercially available until the late 1960's so if it predates that, it must be a mask process. Good luck!
Forgot to add something. I would expect the blasting to be done before plating so any faults can be rectified before the final coat goes on.
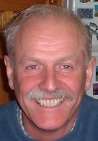
Trevor Crichton
R&D practical scientist
Chesham, Bucks, UK
A. Dear Bob!
Check it with magnifying glass(10X)! Etched surfaces are totally different than blasted!
Goran Budija- Cerovski vrh Croatia
The Sounds of the Great Slide & Resophonic Instruments"
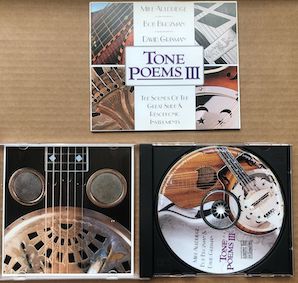
on eBay or
Amazon
(affil link)
Trevor,
Well, you are spot-on.
Here's the update...
I was fortunate to be able to contact someone in the Resophonic Guitar industry who you could say was indisputably, in a position to know.
These designs are essentially glass bead blasted to a mask on the polished brass, then nickel plated.
Mystery over. Now I can get to work.
I want to thank everyone who chimed in and helped me out with this. You guys are the best.
Bob Claborne [returning]- Garden Grove, California
Q. HELLO SIR,
I WANT TO ACID ETCHING ON A PRODUCT FINISHED WITH NICKEL PLATING, AND THEN CHROME PLATING WILL BE DONE. WHICH ACID SHOULD I USE FOR THIS PROCESS?
BALBIR
- Dehradun, Uttrakhand, INDIA
May 19, 2012
A. Hi Balbir.
We appended your inquiry to a thread which may answer it for you. Blasting would probably be better than chemical etching.
Regards,
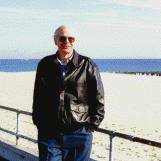
Ted Mooney, P.E.
Striving to live Aloha
finishing.com - Pine Beach, New Jersey
Q, A, or Comment on THIS thread -or- Start a NEW Thread