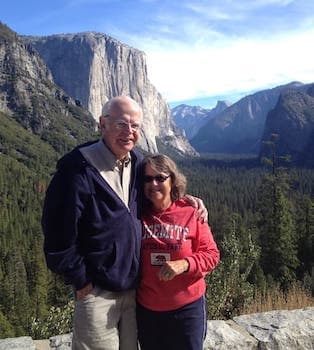
Curated with aloha by
Ted Mooney, P.E. RET
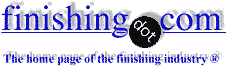
The authoritative public forum
for Metal Finishing 1989-2025
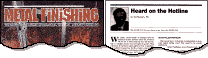
-----
Masking a rivet / pin for heat treatment
Tip: Readers want to learn from Your Situation 🙂
(little can be learned from abstract questions, so many readers skip them)
RFQ: Sir
I want to know in Chennai who is doing this copper masking and case carburizing process.
Employee in a limited. - Chennai, Tamilnadu, India
Ed. note: This RFQ is outdated, but technical replies are welcome, and readers are encouraged to post their own RFQs. But no public commercial suggestions please ( huh? why?).
To minimize lost motion, please describe your needs -- a one-time requirement for a single small item? A weekly need for thousands of very large items? Thanks.⇩ Related postings, oldest first ⇩
June 23, 2009
Q. We want to rivet a pin after heat treatment.
Now we are facing cracks in pin end during riveting.
we planned to mask that particular end by copper plating before heat treatment.
Such that, after heat treatment the pin (material EN 9), we hope , the masked end may be lesser hardness than un masked area. We hope, this will facilitate to rivet the pin end without any cracks.
Is my process method correct or not?
Someone can kindly guide me
Thanks
Product designer - India
A. Good afternoon:
I'm assuming that you are austenitizing, quenching and tempering the pins in a controlled atmosphere. If that's not correct, please provide more detailed process information.
The function of the copper plate is to prevent carbon diffusion into the surface of the steel during case hardening. If the carbon potential of the heat treating atmosphere is greater than the carbon content of the steel, the copper plate will keep the surface carbon content lower in the selective area that was plated. That should provide more ductility in the surface area of the part that was selectively plated, compared to the surface that is not selectively plated. If the carbon potential is the same or lower than the carbon content of the steel, the selective plate is useless.
One point to consider: EN9 is nominally 0.50 % carbon steel. The surface of the pin is likely to be pretty hard if you are quenching and tempering. If that is the case, you may want to consider selective induction anneal of the riveted end, or possibly a change in material selection to a lower carbon grade which will provide more ductility. If the blueprint allows it.
- St Louis, Missouri
June 30, 2009
July 8, 2009
Q. Dear Mr.Steve
Thanks for your response and suggesting Induction anneal of rivet end. We are planned to take trial on it.
Herewith I summarize my early experiment (before sending previous query) to you briefly, so you can better understand my situation and through some light for my improvement
Trial 1 :
First, I tried with boron steel grade pin in below process route
(a) Copper plating (25~38 micron coating thick)
(b) carburized (austenizing, quenching & tempering in controlled atmosphere)
Surface hardness : 760~780Hv 0.2 Kg
(c) Pin end riveting
Result : in end cracked during riveting trial
Trial 2 :
Second, I tried with EN 9 steel grade pin in below process route (as similar above)
(a) Copper plating (25~30 micron coating thick)
(b) Thru hardening (austenizing,quenching&tempering in controlled atmosphere)
Surface hardness : 643~689 Hv 0.2 Kg
(c) Pin end riveting
Result : in end cracked during riveting trial
Now I would like to clarify few points with you, for my improvement action to avoid pin crack during riveting,
(1) Is the copper plating coating thickness playing an role during heat treatment (i.e is there relationship between thickness & reducing hardness), did I want to increase coating thickness, if so how much?
(2)Can you suggest suitable thru hardening / case hardening material suitable for my application
Once again I thank you for your valuable suggestion and look forward for your co-operation
Thanks
S.Ganeshan
- India
July 9, 2009
A. Good afternoon:
I think that 25 microns, or 0.001" of copper plate is often specified as a minimum thickness for selective carburizing stop off. Not sure if increasing the thickness will be of much help. And we don't have enough information to know if selective plate is even the solution to the problem.
Material selection is dependent upon:
1- specific composition required by blueprint or spec
2- physical/mechanical properties required (surface or core hardness, tensile, impact, etc)
3- part design and application
I hope the suggestion on induction anneal is helpful. But ultimately, you will have to figure out the material and processing yourself, or work with the customer, vendor and/or consultant to do so. There are many variables involved that only you have knowledge of.
- St Louis, Missouri
Thanks for providing details about coating thickness.
- India
July 11, 2009
Q, A, or Comment on THIS thread -or- Start a NEW Thread