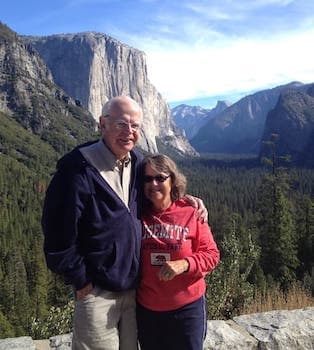
Curated with aloha by
Ted Mooney, P.E. RET
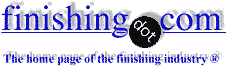
The authoritative public forum
for Metal Finishing 1989-2025
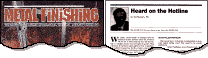
-----
Parting a difficult shape electroform from the mandrel
for Plating Shops & Engineers
Electroforming by Peter Spiro (1971)
avail from eBay or Amazon
Bureau of Standards: Electroforming of Waveguide Components
avail from AbeBooks or Amazon
Electroforming of copper for high vacuum applications
avail from AbeBooks
Fabrication of liquid-rocket thrust chambers by electroforming
avail from AbeBooks
A survey of electroforming for fabricating structures by W.H. Safranek
avail from AbeBooks
Electroforming in Restorative Dentistry
avail from AbeBooks or Amazon
Principles of electroplating and electroforming by William Blum (1949)
avail from eBay, AbeBooks or Amazon
(as an Amazon Associate & eBay Partner, we earn from qualifying purchases)
Q. I am currently researching alternatives to Dichromate passivation of copper and nickel mandrels for electroforming. I am seeking an effective method without the looming cost of expensive waste disposal. Is there a "safe" formulation for a passivating solution I can try? I plate in a nickel sulfamate bath at anywhere from 45-90 ASF.
Scott A Yox1996
Q. In our company we use electroforming for our cylinder production. In this process dichromate is used to build up a separation layer on the silver master for the following nickel plating process. Sometimes the silver surface becomes grey and the master is destroyed.
Can you give me a hint, to avoid this problem? Is it possible to use other chemicals than dichromate, because of the toxic problems of Cr(VI)?
Thanks,
Karl Poellmann- Weiden, Germany
A. Hi Scott, hi Karl. I have heard that egg albumin is not as good as a separation agent, but may be good enough. Good luck.
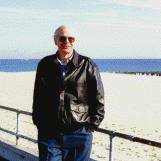
Ted Mooney, P.E.
Striving to live Aloha
finishing.com - Pine Beach, New Jersey
Q. I am trying to plate Nickel onto copper to produce a mandrel for hot embossing. So I want to uniformly plate Ni that is easily lifted off.
I can plate nickel (sulfamate bath 55 °C) fine; my problem is I either get a non-uniform plate with poor adhesion, or a great plate with far too good adhesion to the substrate to lift off. Can anyone suggest a treatment for either the plating conditions, or the surface of the substrate that will allow me to plate well and easily remove the nickel.
Phillip McMahon- Melbourne, Australia
2002
A. Hi Phillip. What you probably need for your electroforming separation layer is a solution of about 10 percent sodium dichromate. You can adjust this concentration and the immersion time up or down, but you should be able to achieve uniform moderate to good adhesion. After good cleaning, immerse the part in the sodium dichromate and things should go a lot better. Good luck.
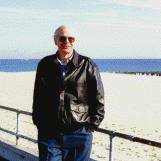
Ted Mooney, P.E.
Striving to live Aloha
finishing.com - Pine Beach, New Jersey
Q. Hello,
I am a technician who is working on a project of nickel electroforming.
In practice I am starting from permanent mandrel, represented from a iron cylinder (features above) and I have to produce a tube from this, with a thickness of 120-150 µ and hardness about 400 HV, that will be entirely removed from the mandrel, without breakage.
The bath I'm using:
Ni sulphamate 680 cc/lt
Boric acid 23 grams/lt
Ni chloride 3 grams/lt
Antipit 2.6 cc / lt
I don't use additives
15-20 A/dmq
50 °C
Cathode in rotation: 60 rpm
Nickel anodes in basketball
Mandrel features:
diameter average : 200 mm
length (average) : 1300 mm.
The surface is coppered (150 mu)and chromed (7 mu) and appears very smooth (Ra =< 0, 30).
Mandrel preparation:
degreasing at room temperature
Passivation with a solution in water of potassium dichromate at 1,25%
Rinse.
The problem I meet is after the plating, It isn't possible to remove the sleeve from the mandrel.
This problem could be because I don't use additives? And if yes, what do You recommend?
Thanks for Your answer.
- MILAN, ITALY
March 18, 2009
![]() |
A. I didn't get it clear if you are electroforming on the inside or the outside, but yes, stresses could tend to attach the electroform in either case. If stress is tensile an electroform deposited on the O.D. will tighten over the mandrel and make it difficult or impossible to extract without breakage (and vice versa). Do you use a tensiometer? Guillermo MarrufoMonterrey, NL, Mexico A. I will assume that you do not have wrap-around (edges of sleeve), because that will be too simple. I am involved with electroforming printing plates, and do not use additions. Any undercut to the engraving will cause the plate to grab those undercuts. I do not know if your mandrel has been machined, or how you achieved the surface smoothness. But any low and/or high spot can lock it on. I would first put a dial indicator on the surface. David Williams- Ft. Worth, Texas |
Q. Sorry I thought was clear: the electroforming is for outside and I do not use a tensiometer.
In any cases, my electroformed is 170 HV and those of the European competitors is 450 HV.
The cylinder have on both corners, an aluminium tape around the circumference just to define the extremes of the plate or more specifically, the pipe that will form.
The cylinder surface of copper and chrome-plated is already finished with grinding and further smoothed with extremely fine abrasive wheels. It has no holes or undercuts, is perfectly smooth.
Thanks
ERMANNO GIORGIO [returning]- ITALY
March 25, 2009
A. Ermanno
You have chosen a very difficult shape. It is relatively easy to break the bond between the electroform and the mandrel. Heat it to about 100 °C and drop it into cold water. However, you then have to remove the extremely tight fitting formed tube and it is much too thin to grip.
Suggestions:
1. If it is possible to have a slight taper on the mandrel it will be easier
2. PMA makes a good mandrel. Good surface finish and easy to silver for conductivity
3. After plating - Low melting alloy (recyclable) or wax and conductive paint
4. Plate a thicker ring (flange) of Ni at one end and use it to hold the electroform while you push out the mandrel
5. Drill a hole through the mandrel, stop it off with wax and paint with a conductive paint. Plate the mandrel and also this end to form a closed tube. Use hydraulic pressure to blow the form off. Do not use air as the possibility of a burst tube is high and use a shield in case it does. If the air does not burst the tube it will fly for many meters, be a considerable hazard (and destroy your perfect tube!)
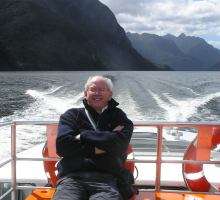
Geoff Smith
Hampshire, England
![]() |
Q. First of all, I want to thank all those who with their suggestions have worked to solve my problem. - ITALY A. Electroforming with a cylindrical mandrel should not be a problem, as long as some basic rules are followed. Firstly, your deposit needs to have either neutral or slightly tensile stress -preferably very slightly tensile. I notice you do not have any additives, so I would recommend about 0.5 g/l sodium saccharin - this will not only give you a bright deposit, but it will also make it harder and make the deposit less compressive. Secondly your mandrel needs to have a slight taper to one end of it, so you can pull your electroform off the narrower end. Thirdly, the mandrel needs to be very well polished and putting down a passive film will be useful; this can be done by giving the mandrel a dip in either sodium dichromate solution (ca 2%) for about 2 minutes, or using a sodium metabisulfite dip (200 g/l) for about 10-15 minutes; alternatively use an electrolytic dichromate dip for about 30 seconds. Fourthly, mask off the ends of your cylinder so that no metal is deposited around the ends; if it does get deposited, it will stop the electroform form coming off the mandrel. Finally, electroform your cylinder in the vertical plane and have it rotating at about 60 rpm; make sure you have sulfur depolarized nickel anodes equally spaced around the sides of your tank. ![]() Trevor Crichton R&D practical scientist Chesham, Bucks, UK |
Hi Trevor,
Thanks for your support.
Now I'm using the sulphamate bath (680 cc/lt. 9,5 gr/lt Nickel chloride. 23 gr/lt boric acid. 2,6 cc/lt antipit) with 2 gr/lt of saccharine.
The pH is a little too high (4,8)
DDC: 12-20 A/dmq
The hardness is around 380 HV and the deposit is very brittle.
I have modified the temperature at 40-43 °C to avoid some detachment during the electroforming from the mandrel in some areas. This effect is similar to bubbles and appears with very smooth surfaces and when the temperatures begin to be at 50-53 °C.
The use for printing process doesn't allow even a slight taper.
The mandrel surface is very well polished.
I have treated the chrome surface with a solution at 2,0 gr/lt of potassium dichromate for 3 minutes at room temperature according to your suggestion.
The ends are masked and protected with aluminium tape to avoid nickel deposition and to define the width of the sleeve.
The cylinder is rotating at 60-80 rpm in horizontal plane, and the basket with nickel anodes (not S) are equally spaced.
In these conditions, the parting from mandrel is often difficult and impossible to use in production; need a nickel plating less attached to the base or to break (or increase?) the stress.
- ITALY
A. This sounds exactly like what we do. The easiest way is to coat your smooth mandrel with PMMA by immersion and then slowly pulling it out. This makes it even smoother than before and puts down a layer about 5 microns thick. Then, you evaporate a thin layer of gold about 300nm thick, this is your conductive surface. Next you electroform at nearly zero stress. You have to mask the ends so it does not overlap the ends.
Next, once it is electroformed, Immerse it in liquid nitrogen for maybe 10 minutes. The mandrel will contract more than the tube allowing it to easily release.
Next, you use a cyanide gold stripper to remove the gold leaving a tube with very smooth interior surface. Rinse in
acetone
⇦ this on
eBay
or
Amazon
[affil links] Warning! highly Flammable!
to remove any PMMA before stripping the gold. The mandrel should be washed in acetone
⇦ this on
eBay
or
Amazon
[affil links] Warning! highly Flammable!
to remove PMMA and then re-used.
We can make very small tubes this way.
- Tallahassee, Florida
A. Ermanno,
I think you need to use a stress reliever. Ask your chemical supply house for a recommendation. One of the nice things about sulphamate nickel is that it does not need chloride, which can induce stress, but if you use a chloride free bath, you MUST use S nickel as the anode, otherwise you will have issues with anode dissolution.
David has also given you some pretty neat ideas too, so they may be worth a try. You can also consider using either aluminium as a mandrel and treat them as either permanent or disposable - you can dissolve aluminium in sodium hydroxide. Have you considered using wax?
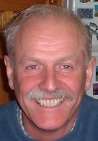
Trevor Crichton
R&D practical scientist
Chesham, Bucks, UK
This is a late reply. However, if the goal is to make a smooth straight tube, using a precision smooth roll and not to pick up any printing impressions from it (which would themselves be undercuts and not permissible) then there are several options to apply thin and dissolvable coatings. One coating as suggested earlier is to PMMA via a dilute solution, but surface tension and non-uniform evaporation could induce slight non-uniformities. The dichromate coating is uniform if the cylinder is rotated and anodes disposed all around it as suggested earlier. Egg albumin as a stearic coating is also suggested. I am wondering why can't soft pure graphite by rubbed as a conductive lubricant and parting film ?
Yannoush Greek- Athens, Greece
March 23, 2011
for Artisans, Jewelry, Crafts
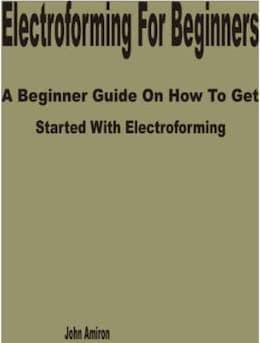
avail from eBay, AbeBooks or Amazon
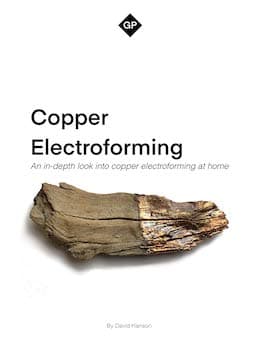
avail from Amazon
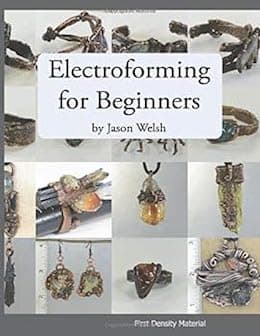
avail from Amazon
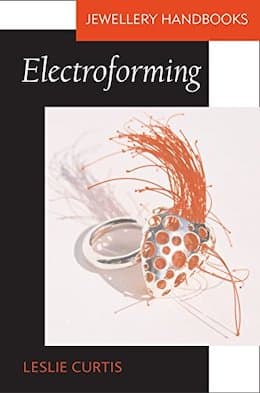
avail from eBay, AbeBooks or Amazon
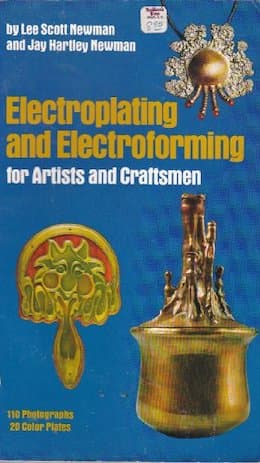
avail from eBay, AbeBooks or Amazon
(as an Amazon Associate & eBay Partner, we earn from qualifying purchases)
Q. How can I proceed for precision electroforming? What are the best methods to make mandrels with limited available resources?
Vaibhav Mishra- India
October 22, 2017
A. Hi Vaibhav. People have spent their whole careers in precision electroforming, decades of study & experience. You can't simply ask, in a few words, "how do I do it?" :-)
Please introduce yourself, tell us about your experience & knowledge level, and what resources you have actually have available (where in India are you?), and what you want to build and of what metal (hollow gold earrings, nickel bellows, copper wave guides), then people can probably suggest a next step. Good luck!
Regards,
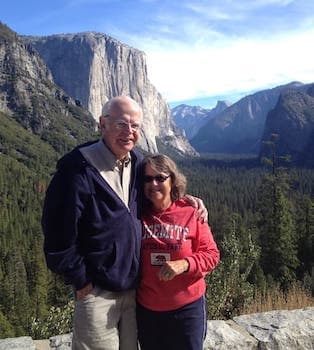
Ted Mooney, P.E. RET
Striving to live Aloha
finishing.com - Pine Beach, New Jersey
Q. Sir I am doing my project at undergraduate level. I tried electroforming on PCB substrate and used potassium dichromate for parting purpose whereas the solution didn't work out properly and discontinuous electroforms were obtained. I am using Watts Bath for electroforming.
Can you suggest me the solution for passivation to be used?
- Ahmedabad, Gujarat, India
November 15, 2017
A. Hi cousin Vaibhav. The toxicity of dichromate might be a reason to try to use something else, but dichromate is the simplest, most widely used, most effective, and most reliable parting agent. Don't turn away from it, or blame it, for the fact that your first attempt at electroforming wasn't fully successful.
"Didn't work properly" and "discontinuous electroforms" are probably not giving us sufficient info to help you. Please send a picture, describe in what way they didn't work, and what you mean by 'discontinuous'. We assume that PCB means printed circuit board, but I think we need more info than that about the substrate and exactly what you are trying to do. Thanks!
Regards,
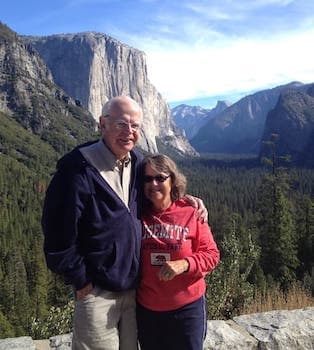
Ted Mooney, P.E. RET
Striving to live Aloha
finishing.com - Pine Beach, New Jersey
----
Readers: We have several other active threads on similar subjects, including
Letter 40125 "Electroforms only partially stick to smooth mandrels" and
Letter 42447 "Parting/passivation Agents to Keep Electroforms from Sticking to Cathode/mandrels".
Q, A, or Comment on THIS thread -or- Start a NEW Thread