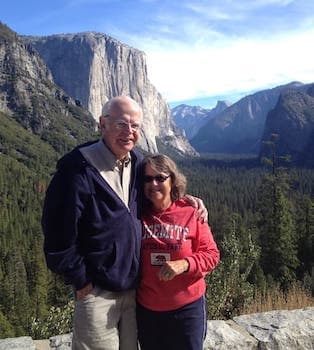
Curated with aloha by
Ted Mooney, P.E. RET
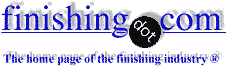
The authoritative public forum
for Metal Finishing 1989-2025
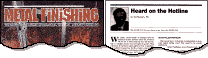
-----
Electroforms are sticking to cathode/mandrels
Egg Albumin Is Staining Nickel Electroforms
Q. Hi there, I have read through the attached thread but haven't found the help I need. I work in an electroforming lab and have been using egg white albumen to passivate nickel before forming. It works perfectly in terms of separation but I find that once separated cloudy staining appears that ruins the appearance. The egg albumen I have been using contains 2.5% citric acid. Could this be causing the staining? Or do you have any thoughts on what could be causing it?
Thanks for reading my question!
- Middlesbrough [U.K.]
October 2, 2024
⇩ Related postings, oldest first ⇩
Q. Hello,
I am a graduate student at Laval University working on my research project which is pure iron electroforming. I use type 316 stainless steel as cathode, Armco iron as the anode, and a ferrous chloride-calcium chloride solution as electrolyte.
The cathode surface is polished with SiC abrasive paper 1000 grit and immersed in Na dichromate solution (for passivation) before the deposition process. Since the process is electroforming, we do not want any adherence between deposit and substrate, however in most cases the deposit adheres to the cathode and is not removable.
Would you please advise me how to solve this problem?
Thank you for your attention,
Laval University - Quebec, Qc, Canada
2006
A. Sodium dichromate passivation is usually employed to build the separation layer. Although I have no personal experience with it, egg albumin was suggested in an article I read about videodisk electroforming if your wish to avoid hexavalent chromium.
But it sounds like the cathode surface may not be perfectly clean before passivation if you are going directly from sanding (and possible fingerprints) to passivation. Please consider electrocleaning the cathode.
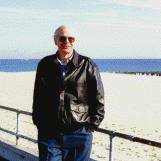
Ted Mooney, P.E.
Striving to live Aloha
finishing.com - Pine Beach, New Jersey
A. Sodium dichromate is usually OK for a passivation layer, but perhaps you are not giving it enough time. I would recommend a 2N solution at least 2 minutes dip or 20 seconds with a current density of about 35 ASF. Sodium dichromate is really becoming a no-no, what with all that Cr(VI) floating about in it, so you may want to try potassium permanganate ⇦ this on eBay or Amazon [affil links] (100-200 g/l at RT); I have used it with success.
Alternately, try 200 g/l sodium metabisulphite at room temperature and immerse the mandrel for 10 minutes in it. This will give you a very good release layer on stainless steel. Consider if the design of the mandrel is right - for instance does it have a taper and/or relief angle? Also, is the iron deposit compressive or tensile? For good electroforming it should be about zero stress. Polishing the mandrel is essential, so spend as much time on this as you can. I would suggest 1000 grit (or finer) wet'n'dry paper, followed by a good calcium carbonate (chalk) slurry scrub. One good chalk is Sturcal - its used in dental chalk formulations.
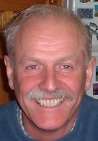
Trevor Crichton
R&D practical scientist
Chesham, Bucks, UK
A. 316 stainless is an unusual material for a mandrel, expensive and hard to machine. Try passivating in nitric acid 30+.
Assuming that you have no re-entrant angles and a reasonable draft angle on the mandrel, the problem is breaking the bond. The simplest way is thermal shock. Leave overnight in a freezer and then immerse in hot water.
Your problem will be considerably increased if there is compressive stress in the deposit. The problem will be eased if you choose a mandrel with a coefficient of expansion significantly different from the deposit.
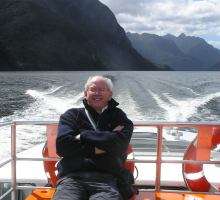
Geoff Smith
Hampshire, England
Q. Hello,
Thanks for your advice. I was trying all methods you have suggested which were unfortunately not successful.
I increased the passivation time of 2N sodium dichromate solution and also tried to passivate the substrate with potassium permanganate, sodium metabisulphite and 30% acid nitric solutions. I also did an electropolishing on stainless steel after the mechanical polish to have a perfect surface finish before passivation which did not work either. I have also tried the thermal shock without any results due to the little difference in the thermal expansion coefficients of iron and SS.
The substrate which is used for the iron electroforming is a cubic piece of SS 316 mounted in resin and therefore, the exposed surface is planar without angles.
Could you please suggest me other materials for the substrate? I am not sure if I can use aluminium or copper alloys because of the highly corrosive bath (FeCl2-CaCl2 and HCl with pH=1 at 90 °C). Do you think that nickel would be appropriate? or can I use a conductive polymer?
Thank you,
Laval University - Quebec, Qc, Canada
A. Try copper with the dichromate passivate.
The solution you are using will etch copper but if you connect the current before you put it in the bath you should avoid this.
Nickel should work - leave it to passivate naturally.
Lead is also a possibility.
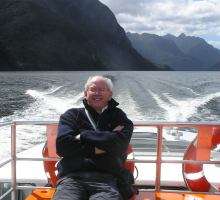
Geoff Smith
Hampshire, England
A. I wonder if you are using a three dimensional mandrel and getting a highly compressive iron deposit. Obviously if you are using just a simple sheet of stainless steel, any compressive stress will only be a problem where there is plating over the edge. If it is stress, then you can do two things; firstly reduce the stress - easier said than done with iron! Secondly, you could use a disposable mandrel made from a moulded plastic, aluminium or zinc. Then you can dissolve the mandrel to leave your free standing electroform.
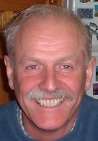
Trevor Crichton
R&D practical scientist
Chesham, Bucks, UK
A. 90 °C and such a high chloride level certainly tend to destroy a passive layer (remember how a Wood's nickel strike bath works). Maybe you could consider using a pure nickel electroform or a nickel initial E-formed layer and then the iron final shell. Nickel E-forming baths are much less aggressive with mandrels. Just an idea.
Guillermo MarrufoMonterrey, NL, Mexico
A. Hi Maryam Moravej
For electroforming Iron on stainless steel:
#1 avoid 316; Use 303. Polish with something like Blue Magic
⇦ this on
eBay or
Amazon [affil links]
, available at Checker Auto, or some other bright stainless polish, do not try to passivate the surface as this will not help.
#2 clean with a good wax remover (Windex
⇦ this on
eBay or
Amazon [affil links]
) then Simple Green as a wetting agent.
#3 rinse well, do not dry. Plate with copper solution (copper sulphate
⇦ this on
eBay or
Amazon [affil links] 150 g/l, Distilled water, Sulfuric Acid to pH<1(don't overdo it) - 10 min @ 20 ASF 25 °C.
#4 Rinse, do not dry. Plate with Iron Strike, (FeCl2 - 100 g/L, Sodium Citrate - 100 g/L (you will need to filter this solution through a good filter paper before using, yes it is dark) - 10 min @ 20ASF, 25 deg. C. The Iron Strike will give you a light grey matte pure Iron surface that is slightly ductile -- to pass bend test. At this point you can use the high temp plating bath you are currently using to complete the process.
When done, use a razor to slightly lift one edge and apply compressed air to lift off the part evenly. To remove the Copper use an Ammoniacal Copper etch. Have fun.
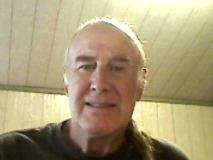
Edward Perry
- Sedona, Arizona
Dammit, Jim, we're printers, not chemists! /Dr. McCoy voice
Q. We are a printing company that has developed a holographic printing division over the years. After a recent visit from the state Dept. of Health and Env., we are looking at alternatives for potassium dichromate that we use in the production of holographic printing plates. We use the dichromate to 'passivate' nickel. Since I have looked at the archives on this and other sites, I realize that passivate means different things in different situations, so I will describe our process.
1) starting with a holographic image on resin on glass
2) we paint the resin image with silver
3) after cleaning and preparing the silver, we grow nickel on silver electrolytically to 5-10 mm in a nickel sulfamate bath; this becomes the electroforming master
4) [Step of interest] we 'passivate' the nickel surface by spraying it with potassium dichromate-- this is done at room temperature, and the dichromate is left on for a minute or less. The reason for this step is so that the duplicate image(next step) will peel off the master.
5) rinse dichromate off with D.I. water
6) grow a mirror image of the master electrolytically in same nickel sulfamate bath to about 3-6 mm. This becomes the printing plate that is used to impress the holographic image onto end stage plastic or foil.
I hope any suggestions could note how much change is required from the current procedure, as we are change averse, because, like I said, we are not chemists, and when things are going well we would prefer not to change anything (but in this day and age, getting rid of hexavalent chromium looks like a good idea).
Commercial Printer - Topeka, Kansas, USA
March 11, 2011
A. Hello George
Nickel passivation can also be done with a 10% solution of NaHSO3 dip. I'm not sure if it will work for hologram, but it is used e.g. for the manufacturing of electroformed foils for razors. I would nor recommend spraying it as there may be some SO2 coming from the solution, which smells strong and not really healthy also. Good luck.
- Zug, Switzerland
A. I do nickel electroforming of printing plates. I use (as little as possible) potassium dichromate. There is a product by Fisher called Egg Albumin powder that works. You mix it so it can be poured. You did not mention how the hologram plate is racked. If you use silver solder around the edge, the Egg Albumin will react with the solder. If this is the case, do not use the Egg Albumin.
Dave KiminkiSecurity Printing - Ft. Worth, Texas
A. I'm not sure if this will produce the desired result, but nickel is easily passivated electrochemically by making it anodic in an alkaline cleaner.
Lyle Kirmanconsultant - Cleveland Heights, Ohio
Q. Greetings all,
Recently I was hired as a chemical engineer at a company that uses nickel sulfamate electroforming to produce optical tooling. I've been using this site and the past letters to really gain a lot of knowledge, so thank you all for being such great sources.
A want has arisen to investigate replacing our current method of post-forming passivation with potassium dichromate. This is obviously a health-related issue, so we're looking into any options that would be safer but still allow the nickel electroforms to be removed from the mandrel without too much difficulty.
I've been referred to electrochemical passivation as a possibility, but I'm trying to gather as many possibilities as I can before starting comparisons and trials for our specific needs. Are there any specific alternatives people have previously used with success?
Thank you all in advance for your suggestions.
Electroforming chemical engineer - Rochester, New York, USA
May 1, 2012
A. Eric, you do not say what your mandrel is. If you use stainless steel (304 or 316), it doesn't always need passivating, as it has an inherent layer of chromium oxide on it. In the past, I have used passivation treatments based on 200 g/l sodium metabisulphite, and these work well. I have also used potassium permanganate (20-50 g/l) and have heard of citric acid dips being used. However, it is all horses for courses and dependent on the peripheral chemistries you are using.
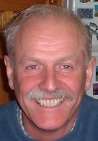
Trevor Crichton
R&D practical scientist
Chesham, Bucks, UK
Thanks Trevor. The mandrels we typically use are nickel as well, or at least the "functional" side I should say.
I had heard of the sodium metabisulfite and I have begun working with it, though it did "color" one of my test parts. Because we're working with optics, the cosmetics are extremely important, so this is a bit concerning. I am in the process of restarting my testing due to some tooling issues that I believe were giving me false positives, so I will try it again just in case.
I also have plans of trying citric acid as well as the egg albumin that have been mentioned in the past. The permanganate is new information to me, so I will have to look into that as well.
Thank you for your information. Should I come up with something interesting, I will be sure to share.
- Rochester, New York, USA
A. Eric, if you are using a nickel mandrel, is there any opportunity for you to use one that has been electrocoated with bright nickel? The reason for this is that nickel electrodeposits that contain high organic loadings, such as sodium saccharin, are notoriously difficult to achieve good adhesion of any over-layers, especially nickel.
I agree that sodium metabisulphite will cause a discoloration at the interface of the electroform and the mandrel, but it should not discolor the outer surface, but that may not be of any practical use to you. The discoloration is nickel sulfide and it may well be removable with a quick dip in a suitable acid, such as sulfuric. Egg albumin is a well established release agent that has been around for many decades. Another release agent is sodium dichromate solution (about 10%) - this can be done either by a 2-5 minute dip or by a 10 second electrotreatment, both at room temperature. The only drawback is having to use Cr(VI).
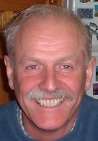
Trevor Crichton
R&D practical scientist
Chesham, Bucks, UK
Trevor,
Q. That's exactly where the metabisulfite discoloration appeared. Unfortunately, that is a show-stopper due to the resulting electroforms being used for either solar applications or reflective product manufacturing. A "cleaning" dip afterwards may be a possibility, but I'm hoping to find a drop-in replacement and not have to change our current system too severely.
I'm working on an egg albumin recipe now while I make a few more "disposable" mandrels for testing.
We currently use potassium dichromate for the process, which of course works great, but hex chrome replacement is the whole catalyst for this experiment. I know that trivalent chromium is a possibility as well, but with the jury still out on on whether the hexavalent state reappears or not, I'm trying to avoid that route.
These replacement attempts aren't exactly required as we haven't had any issues at all, we're just trying to make it a little safer around here if possible. So if nothing can match the dichromate for our operation, then we'll likely stick with it for the time.
- Rochester, New York, USA
Brown streaks on nickel electroforms from permanganate passivation
Q. Hi Everyone,
Recently I have been doing a lot of work developing a potassium permanganate passivation for our nickel electroforms to replace our use of dichromate. In general, it has worked very well. However, we occasionally get some brown streaks across the tools, which considering they are optical pieces is somewhat of a problem. I am able to treat the tools to remove the stains, but I'd rather try and attack this problem at the source. Does anyone have any idea what could be causing these stains?
CEF, chemical engineer - Rochester, New York
November 4, 2013
A. Hi,
I've never used potassium permanganate in this application. But, I wonder if the brown streaks are manganese dioxide. Manganese dioxide is formed by the chemical reduction of pot permanganate in neutral or alkaline solutions. The reduction is the opposite side of the chemical equation to the oxidation by permanganate - you can't have one without the other, as the old song goes!
I would look at the pH of the passivating bath. Also improve rinses both before and after the treatment. In my experience, good rinsing, both in terms of time and agitation, is vital to to prevent cross contamination.
Any comments?
Best wishes
Harry
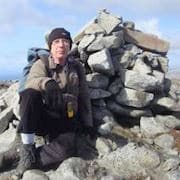
Harry Parkes
- Birmingham, UK
![]() |
A. Harry is right. I have tried using permanganate as a dichromate substitute and generally been successful, although it is not as good as dichromate. The brown streaking is due to reduced permanganate to a manganese oxide or hydroxide. I would not like to say which oxidation state the manganese is, but it will be the lower ones. I suggest that the passivation time is too long, so try reducing it. Also, it is possible that the permanganate solution is old and has a lot of lower state oxides building up in it, so try using a fresh bath. I have also found that using an electrolytic permanganate bath works well at room temperature and you can get away with very short passivation times - perhaps as low as 15 seconds. An alternative passivation solution is 200 g/l sodium metabisulphite - this works on nickel and stainless steel and (I believe) copper mandrels. It gives a very dark film that is excellent for nickel separation. The immersion time should be about 2-5 minutes at room temperature. When it is spent, you can use it the reduce Cr(VI) to Cr(III)! ![]() Trevor Crichton R&D practical scientist Chesham, Bucks, UK
- Rochester, New York |
Q. Trevor,
The solution is quite fresh. The sodium metabisulfite route doesn't work for us due to our high-precision optics, I tried it before the permanganate.
Currently our passivation time is 1 minute, though we haven't tried anything less yet. So far so good with the sodium silicate solution though.
- Rochester, New York
November 13, 2013
A. Eric, I have never used silicates, but I may have a slight concern about bath contamination with any silicate that soaks off. Have you found any problems yet? One other thought is to use egg albumin - an old technique, but it worked!
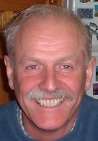
Trevor Crichton
R&D practical scientist
Chesham, Bucks, UK
Q. We are electroforming copper using a non-cyanide alkaline bath onto 304L stainless mandrels. We had previously used an orthophosphate bath, and the stainless surface was electrocleaned and then passivated cathodically with a sodium phosphate bath. We never had any problem with adhesion to the SS using the orthophosphate bath, although we did sometimes run into trouble removing the electroform from the mandrel.
After switching to the non cyanide alkaline, we had big problems with adhesion. I was told that a Woods nickel strike would be required to get decent adhesion, so the mandrels were struck at ~15ASF for about one minute in a standard Woods bath. They were then rinsed thoroughly and cleaned. After the plating, we have found it impossible to remove the electroform from the mandrel. I have read of different release agents, including dichromate and egg albumin, but I was wondering if maybe there was a different process for activating the stainless that did not offer such a degree of adhesion.
Thank you.
Tech - Tucson, Arizona USA
February 26, 2014
![]() |
A. Hi Chris, ![]() Harry Parkes - Birmingham, UK
- Tucson, Arizona USA |
Staining on Nickel Mandrels
Q. Hi,
I am working at a nickel electroforming factory and we are having an issue with repeated use of our mandrels.
We use mandrels made of Nickel and after about 15-20 cycles, the mandrels begin to develop a staining (either brownish in color or white in color).
Our process for cleaning the mandrels involves anodic electroclean, sulfamic acid dip and sodium dichromate coating with DI water rinsing after each process.
Anyone have any experience with this that could point us in the correct direction for things we should be looking into? This appears to be some type of oxidation but we cannot identify where it is coming from or what is causing it. We want to increase the number of uses before replacing a mandrel so this has been a troublesome issue for us.
Thanks in advance for your help.
September 18, 2014
R&D Engineer - Bismarck, North Dakota
Q. Hello at all,
We're using potassium dichromate solution for doing a passivation layer on copper or nickel. After nickel plating on that, the parts can divided without any problems.
Are there any alternative solutions to substitute the chrome-VI ?
Thanks and all the best,
Frank
- Berlin Gemany
May 3, 2023
A. Hi Frank.
It's been a long time since this topic has come up, but it was discussed at length -- with egg albumin and sodium permanganate offered as ideas, as well as techniques like electrolytic treatments or natural aging ... so we appended your question to that discussion. Please review it and get back to us with progress or follow-up questions.
Luck & Regards,
Ted Mooney, P.E. RET
Striving to live Aloha
finishing.com - Pine Beach, New Jersey
----
Readers: We have several other threads on similar subjects, including
Letter 40125 "Electroforms only partially stick to smooth mandrels" and
Letter 51609 "Parting a difficult shape electroform from the mandrel".
Q, A, or Comment on THIS thread -or- Start a NEW Thread