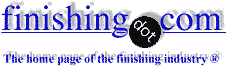
-----
2 years finishing aircraft cable, and consistency still eludes us!
February 13, 2009
I am a fabricator/engineer/inventor-type-guy for a technical theater firm. We design, build and operate systems used for theatrical flying effects, among other things.
For almost two years, I have been designing, building and testing a black oxide system for blackening 304 grade stainless wire rope (AKA aircraft cable). I was given marching orders to explore this when we could not get consistent acceptable finish from any outside firm.
I started with a proof-of-concept effort: very small amounts of finishing products from a couple of vendors using something of a mad scientist rig (turkey fryers, 14 ga stainless steel buckets, etc.) and got positive (if mixed) early results with coiled lengths of rope up to 200' long.
A much larger system was conceived and built with the goal of blackening entire spools of wire rope up to 5,000 feet long. This is made possible by means of a tiered spool that holds wrapped layers of rope about an inch apart, while the flanges of the spool are slotted to allow free flow of bath solutions/rinses/finishing oil in and out of the spool.
The problem now is that results are inconsistent. For example, two days ago, I finished 5,000' of 3/32" diameter 7X19 strand rope to a very nice, consistent black with no rub-off to speak of. Since then, I have processed 5 spools of 1/8" rope, none of which could be called successful, with varying degrees of finish consistency and adherence. For example: one spool might have rub-off in one spot, not in another, but only if you work at it. A different spool, will come out a deep gorgeous black, and then have the entire outer layer of the spool rub damn near clean off with light pressure from a shop towel. Inner layers might have better adherence.
Naturally, I am making every effort (I can think of) to control variables and maintain solution concentrations/temperatures.
This is becoming quite frustrating. Sometimes the system works perfectly, and other times it is impossible to get good results. In the middle, we have miles or rope that is good enough to send out on shows with our crews, but not good enough for sale to other firms
(and there's the rub... or rub-off, as the case may be!)
I will give some specifics:
I use [proprietary] (sulfuric acid) at 32 oz per gal for activation. The B.O. tank is [a proprietary], which the manufacturer sells as specific for stainless steel. The acid I keep at PH .75-1 and around
160 degrees F. The B.O. is mixed at 4.75 lbs per gal and I run it at
250-255. All tanks are heated by electric immersion heaters, which seem to work quite well. Rinses exchange at 6 gals per minute when running.
There are six 150 gallon steel tanks (activation tank is lined), with active tanks well insulated. One soak, one activation, one passivivation and three overflow rinses. There is also a dip tank for WD oil. Rope is spooled onto the tired spools and moved through the system via a circuit of overhead track with chain motors/trolleys doing the material handling.
I realize the tanks are probably on the small side, as one rule of thumb related to me is that the B.O. tank should have something like one gallon per sq ft of surface to be passivated. However, it should be noted that the material I am blackening drastically skews any normal basket-o-parts ratio of mass to surface area: a spool of 1/8" rope weighs maybe 160-170 lbs, but has something like 400-500 sq ft of surface area. And, whether the tanks are too large, too small, or just right, they have yielded perfect spools or black rope.
I really need some input on this. I have talked to operators of plating facilities and manufacturers of products and gotten some advice here and there, but the fact is nobody else seems to be doing this sort of product in quite this way. Despite me efforts to collect data and be dotty with this, there seems to be some mojo at work.
I NEED to know what is causing the non-adhesion -- irregular finish is passable, but not this. Some say too long in the B.O. causes this, but this stuff gets as black as it's gonna in 1-3 minutes, so how long is too long? On the other end, a guy at [the supplier] told me it sounded like I needed more activation. But, I just ran a test with three successive spools, with all other things being equal, running each a minute longer in activation that the last. The final one, which spent six minutes in a very active acid bath, had the worst rub-off of all.?!
And, again, two days ago, I ran a spool at three minutes each active bath, and it was perfect. Any suggestions? Any at all!?
(I am, of course, jumping through all hoops with EPA, the sewer and water folk, the Fire Marshall, Inspections Permits and Licensing, yada yada yada... so, no: I am not running an outlaw plating firm in some pole barn somewhere. Just thought you should know.)
Product Designer - Louisville, Kentucky
February 26, 2009
Dylan
Thanks for the unusually detailed description of your process.
The first thing that occurs to me is that although you detail the activation step, there is no mention of cleaning. Wire rope is lubricated both in drawing the individual strands and in making up the rope. The manufacturer will see no need to remove this and the spaces between the strands are ideal for trapping oil, a prime cause of failed finishing processes. Acid activators will not remove oil.
You will need an effective alkaline cleaner as the first step in the process. Following this, rinsing is important to remove chemicals before passing on to the next stage. Remember those spaces between the wires; If it is a simple immersion rinse, allow at least couple of minutes in flowing clean water. It would be good to do a water break test but on wire rope this is impractical.
You could save yourself some effort by abandoning the pH check of the activator. pH less than 1 is meaningless unless you have special electrodes. The main loss of acid will be by dragout rather than reaction. If you do not have facility for simple titration, controlling the density (SG) may be sufficient.
One last thought. You do not mention agitation. The reactions depend on chemicals getting to the surface and, importantly, being replaced when they are used up. Multi strand wire has an enormous surface area and will deplete the local concentration rapidly. The usual practice is to blow air through the solution. It must be oil free air and a separate blower is safer (and much cheaper to run) than trying to use compressed air.
Final rinsing is also very important. You do not want any trapped chemicals on anything that is associated with flying.
You would have much better control if you could set up a reel - to - reel process, but there is not space to describe this here.
Hope this helps.
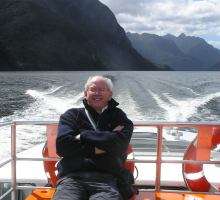
Geoff Smith
Hampshire, England
March 6, 2009
Geoff:
Thanks so much for your input!
I am indeed using an alkaline soak cleaner, only didn't mention in as I thought it was a given. I have found that I wasn't changing it often enough, though.
I looked at a reel-to-reel draw-though design, but it (at least the design I came up with) looked very involved and high maintenance. Let me know if you have a design that works and works well.
I did not know about the <1 PH issue with the activator, nor did I know that reaction was less depleting of the bath that carry-off. This will change how I maintain that bath.
I was also informed by one of my vendors that I should insulate my spools from the material handling system. I'm not sure why, as it seem to act as a "ground" for the electrochemical reaction of the stainless in the acid. Any insight on this?
Thanks again. I will be checking back here as I try new things and learn more. I need to perfect this process and quickly -- people are waiting on me!
- Dylan
- Louisville, Kentucky
Well I don't know just what to say; I did use [a different brand] for a few years and found it extremely fussy to use. I was using it on stainless gun barrels and customers tend to be mighty fussy about the bluing on their guns. I often found that I got small white specks in the bluing and some times blotching on mirror finishes. I was using varsol as my first cleaner and then boiling it in [soak cleaner] before putting it in the tanks. I was doing warranty for Remington at the time and a friend of mine there suggested that I first run it through my regular bluing solution and then move it into the [stainless steel blackener] tank. The standard bluing salts seem to etch the steel a bit and cause it to blue better. Shocking the parts helped a bit as well. (repeatedly going from the cold water to the salt tank). Another friend used a product made by [a 3rd manufacturer] and had similar problems. Just so you know, I finally gave up in exasperation and started telling customers that stainless parts were SUPPOSED to be silver or grey, NOT BLACK! After I stopped trying to blue stainless I had no more problems with it ;o) Rod

Rod Henrickson
gunsmith - Edmonton, Alberta, Canada
April 6, 2009
----
Ed. note: Thanks, Rod, but we've omitted suppliers' names ( huh? why?)
I don't have anything to add to the blackening issue, only that for a number of years we coated gun barrels with a dark gray PVD coating. Talk about fussy! We weren't making much off of them in the first place, then they had to be absolutely perfect. We finally gave up trying.
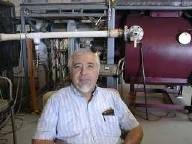
Jim Treglio - scwineryreview.com
PVD Consultant & Wine Lover
San Diego, California
April 7, 2009
September 4, 2009
Hello, all.
Following up on my previous post on this subject, the details:
For the past two years plus, I've been perfecting a process for blackening wire rope in continuous lengths of 1,200 - 5,000 ft. There are several rope configurations, but all are 304 grade. In a nutshell, we put the rope on a tiered spool which keeps successive layers separated about an inch. Spool flanges are slotted for crossflow. The entire length of rope is moved through the tanks (soak, rinse, activation, rinse, bo, rinse, oil) and put back onto the spool it came from.
Generally, this has been successful. Finish tends to be consistent with minimal rub-off. There is some smut occasionally, but this is not a huge problem for our application (theatrical flying).
But I continue to have problems with one rope configuration: 1/8" 7 X 19 strand. The rub-off is significant, even ridiculous on some spools. Nothing I try satisfactorily rectifies this. I theorize there is something about the size of the wires in the strands that makes it do this: it must have just the right size spaces inside it to give it a wicking property, holding in lubricants, making it hard for active solutions and rinses to get in and back out. It has to be something like this, as ropes of the same material but different configurations (both larger and smaller diameters/strands) get much better results.
I keep coming back to the cleaning step as the culprit. 1/8" results are marginally better with longer, hotter soaks and longer rinses, and two or three soak/rinse cycles seems to do better as well (again, other rope sizes are not as finicky here -- 1/4" rope, for instance, even in a dirty-ish bath with only a quick rinse drains freely and shows no rub-off to speak of). I think I need a non-viscous, non-sudsy cleaner of some kind (I'm currently experimenting with automatic dishwasher powder at 180 degrees!). Sadly, they won't let me have a huge open vat of acetone, for some reason :-)
Also, I notice gas bubbles coming out of the 1/8" rope in the post-activation rinse for some time. I assume this is trapped residual acid salts still liberating oxygen, which probably is no good going into the BO tank -- a bit like putting a humidifier and a dehumidifier in a basement and letting them fight it out. Longer rinse? Mild alkaline additive (bleach?) to neutralize?
Suggestions? Questions? Derision?
Product Designer - Louisville, Kentucky USA
Ed. note: For those who didn't understand the satire, Dylan can't have a huge open vat of acetone for the same reason and can't have a huge open vat of gasoline :-)
![]() |
Dylan, are you sure that the rope you have trouble with is in fact the same material as all the other ropes? Is it made by the same manufacturer? Have you had independent verification of the material in both the problem and the satisfactory ropes? Very difficult to see how differences in the lay of the strands could affect your process, but easy to see how differences in material could wreak havoc. ![]() Bill Reynolds [deceased] consultant metallurgist - Ballarat, Victoria, Australia We sadly relate the news that Bill passed away on Jan. 29, 2010. Just a stupid question here. What exactly is rubbing off? Is it the bluing or something that is left over from the bluing process? ![]() Rod Henrickson gunsmith - Edmonton, Alberta, Canada |
September 8, 2009
All the rope is ANSI 304 austenitic stainless steel (18% chromium,
8% nickel). I'm sure there are minute metallurgic variations of the kind CSI:Miami might build a sub-plot around, but as far as I know
(hope) somebody much smarter than I am further up the supply chain has already made sure all this stuff is pretty much the same before it leaves the mill.
The black oxide finish itself is what is rubbing off. There are a few patterns of rub-off I have come to identify when pulling the spool from the final rinse tank. First is a spot rub-off, where small patch or two or three will rub-off more or less readily. Another I call
'wet paint rub-off because it comes off just like that -- in large swaths. There is also a more acceptable version, which I will here term 'dry paint rub-off' where the finish is mostly adherent, but odd flecks will come off here and there almost like flaking dried paint
-- this makes no sense to me considering BO is not supposed to be a
'coating' which is what this looks like.
It has been my experience playing with this rig and blackening all sorts of other things that every BO finish has rub-off: if you sit there and rub at it hard enough and long enough, it will shine. I just need to get it to a bare minimum. Since posting this update, I have had a couple come out significantly better by spacing the rope out over more tiers and using longer hotter soak cycles and longer rinses. May be moving toward an acceptable process. I still want to know if anybody has good ideas about how to clean parts with extremely broken up or hard-to-get-at surface areas without spending ridiculous amounts of time in soak and rinse repeats.
- Louisville, Kentucky
September 9, 2009
I re-read your initial post and something you said struck a nerve. I think I may have seen this before! If I am right I may not have an instant solution for you but knowing what the problem is may help you find a solution.
(you wrote)
(Since then, I have processed 5 spools of 1/8" rope, none of which could be called successful, with varying degrees of finish consistency and adherence. For example: one spool might have rub-off in one spot, not in another, but only if you work at it. A different spool, will come out a deep gorgeous black, and then have the entire outer layer of the spool rub damn near clean off with light pressure from a shop towel. Inner layers might have better adherence.)
Many years ago a luthier wandered into my shop with a box of frets that he had gotten a machinist to cut out on a laser CNC. I have seen laser cut parts before and the cuts are generally quite nice but theses things were a thing of beauty. This guy must have messed with that CNC for hours to cut those parts out. They were about.040 thousandths thick .200*3.00 inches. They were absolutely perfect. No burs and the cuts looked as though they had been polished to a 600 weight finish. There were about 200 of them and I received them in a small card board box.
I cleaned them in the usual fashion and put them in the tank. Only about half of them blued. I went back and forth from the cleaning tank to the bluing tank all day but to no avail.
In the end I examined them under a 50X jewelers loope and light scraping with a dental probe revealed that some of the parts were coated with a thin layer of plastic. To make a long story short the parts had been cut out two years previously and had been oiled and put into storage. Over time the oil had dried out and polymerized.
I dumped all of the frets into a glass sealer, filled it to the top with lacquer thinner
⇦ on
eBay
or
Amazon
[affil links] Warning! flammable!
and left them over night. In the morning I checked the sealer and found that the frets all looked like itty bitty elephant men covered with a thin wrinkled skin. I left the parts a couple more days and then rinsed them and ran them through the tanks again. They blued perfectly.
Try looking at the un-blued areas of your cable with a high powered glass and scrape at it with a pin, especially in the nooks and crannies between the wires. It's possible that the smaller sized cable is not as popular and has been sitting in storage for two or three years. If it is indeed old dried out oil I can tell you right now that regular solvents are not going to work. You are going to have to use a very strong solvent or a paint stripper to break it down.
I think in little bags of nuts and bolts or firearms. Not huge rolls of cable but understanding the problem is always the first step in rectifying a problem. :o)

Rod Henrickson
gunsmith - Edmonton, Alberta, Canada
There is another option. You might try a molten salt bath. According to a friend of mine it is nothing more than a 50/50 mixture of sodium nitrate
⇦ on
Amazon [affil link]
and potassium nitrate. This procedure uses no water. The salts are taken to about 485 degrees Fahrenheit at which point they melt. The temperature is taken up until the test part turns black, at which point the bath is held at that temperature and the rest of the batch is run.
He claims that even stainless can be blued by taking the temperature up to 800 or 900 degrees Fahrenheit. It all seams a bit dangerous to me but he has been doing it for years and claims it's no more dangerous than deep frying French fries.
I have watched him do it but I have never messed with it myself. He claims that the only thing you have to remove before going into the bath is surface rust and water. Pretty much everything else gets cooked off. Did I mention that he is a bit nuts?

Rod Henrickson
gunsmith - Edmonton, Alberta, Canada
September 10, 2009
October 6, 2009
800-900 degrees is not possible with the system as it is.
Polymerization of oils has already been identified as one of the problems. Some rope is received so clean, you can't even detect any oil on it at all, even though you know there is some trace amount at least. We have even processed some like this without cleaning/rinsing and had it come out BETTER than the cleaned stuff (we presume the rope is holding cleaner and oil like a wick, giving worse outcomes than when the activator/bo have only to contend with a micro thin film of oil. But then some is so oily and has been obviously sitting so long it smells like an old machine shop, and is polymerized into a sort of waxy plastic. This stuff doesn't come clean in my 200 degree soak tank no matter how long you leave it. Even acetone doesn't get it all out. This is a variable we can't really control: we get rope from different manufacturers who probably use different oils/sealants, stored in different conditions, etc. I guess we need one cleaner that does it all, whatever that might be. Regardless, the best so far seems to be the one I can mix the lowest concentration
(least viscous) and run at the highest temp.
- Louisville, Kentucky
First of two simultaneous responses --
Dylan,
As this thread has developed, it's become increasingly evident that the problem is removal of oily/waxy/polymerised/old/etc coating.
Can you add a high-power ultrasonic bath to your processing? That would greatly accelerate solvent action, and also movement of solvent into and out of confined spaces in the rope lay.
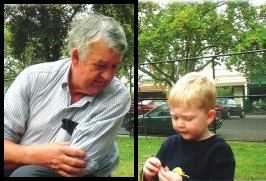
Bill Reynolds [deceased]
consultant metallurgist - Ballarat, Victoria, Australia
We sadly relate the news that Bill passed away on Jan. 29, 2010.
October 7, 2009
Second of two simultaneous responses -- October 7, 2009
Well my friend I'm kinda at my wits end here. You kind of admitted in your last post that polymerized oil is part of the problem. I had suspected that was so.
To be quite honest even some of the razzle dazzle, get some disposable employee cleaners like carbon tetrachloride are not really going to help you too much. That kind of gunk generally requires one of three things to break it down.
Solvents like acetone or lacquer thinner
⇦ on
eBay
or
Amazon
[affil links] Warning! flammable!
which you don't seem to be allowed to play with. Brute friction which is not an option because it won't clean between the strands, and lastly heat.
You don't seem to be willing to change over to a molten potassium bath so some other form of heat may work. Now 304 is a Chromium-Nickel steel with very little carbon and there for should not be heat treatable. So it may be possible to use brute force and apply enough heat to break down the polymer that has formed on the outside without screwing with the hardness too much.
Burning the crud off might not work so well as you might just be leaving a carbon deposit that is harder to get off than the polymer itself. As an experiment try heating some short lengths over a common stove element or a paint stripping gun until it begins to smoke and run those test samples through your system. If it works you can get heating coils that you can run the cable through which should give you the same affect. I have seen neon sign makers use these coils and they will heat glass tubes to red hot in just a few seconds.
Short of that take a few samples to some one doing molten potassium bluing and see how that works. If it does, and I suspect it probably will, you May have to just source out the bluing to a shop that specializes in that. Or convince your company to set up for that type of bluing. Short of that, I got nothing.

Rod Henrickson
gunsmith - Edmonton, Alberta, Canada
Q, A, or Comment on THIS thread -or- Start a NEW Thread