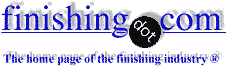
-----
Yellow Chromate Adhesion Problem

Q. I have a couple questions.
I have a small garage, I've decided to start getting into restoration type work. I bought a zinc plating hobby kit to start my experimenting and learning. I appreciate any advice.
1. I can't get nitric acid to buy, is it better to use muriatic or sulfuric acid before yellow and blue chromate?
2. Does zinc brightener affect yellow chromate adhesion?
3. how to achieve proper yellow chromate adhesion?
4. is heat necessary for curing?
- Port of Spain, Trinidad
January 6, 2021
A. Hi Joshua.
1. Neither will do any good and either may do harm, but some production shops do zinc plating and chromating without a nitric acid dip in between, so it's certainly possible to do without if necessary.
2. Absolutely. We attached your question to one of several long discussions on the subject.
3. Larry Durney answered all such questions with the same first answer "Obey the Letter of the Law" -- follow the instructions exactly, not approximately; even more important for a beginner.
4. No, heat is not necessary for curing; the parts should be dried, but anything over 140 °F (60 °C) is destructive.
Luck & Regards,
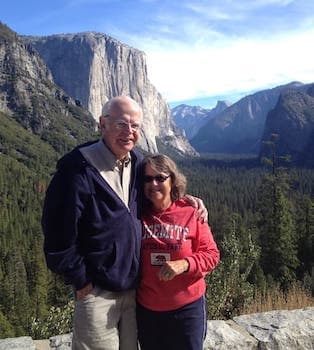
Ted Mooney, P.E. RET
Striving to live Aloha
finishing.com - Pine Beach, New Jersey
⇩ Related postings, oldest first ⇩
Q. We are experiencing a problem with the adhesion of yellow chromate film to our zinc plating deposit.
A particular product we barrel zinc plate in a potassium chloride solution is compressed in a post plating assembly process. Although prior to compression of the part the chromate film passes all 'normal' tests for adhesion, after compression the film sometimes loses adhesion and can be removed with the lightest touch in the area that the base metal has been deformed. In these cases the chromate tends to look powdery in the compressed area.
The problem occurs erratically. Often a barrel load apparently free of this problem is followed by a barrel in which all parts fail on this criteria. Variance within a single barrel load is also sometimes encountered. The plating is carried out on an automatic line - so process variance is relatively minimal.
Our efforts to link the problem to any specific process variable have so far failed.
The parameters with which we have experimented include:
1. Five different proprietary chromate dips have been trialled at various concentrations and pH.
2. Three different proprietary chloride zinc brightener systems have been trialled.
3. With and without pre-dip in a sour rinse (dilute nitric acid).
4. With and without pre-dip in a clear chromate dip.
5. Vary the heat used in the drying process.
6. Vary the pH in the post dip rinses.
7. Vary the temperature of the chromate dip.
8. Use of wetting agents in post plating rinses to negate the effect of any oily films.
We are unsure if the problem is due to variation in the composition of the chromate film or a lack of adhesion of the film to the zinc. Any ideas or suggestions would be most appreciated.
1998
A. Zinc is not ductile, which is why cadmium was traditionally used for such applications as hose fittings destined for crimping.
Still, and this is just intuition and experience, the drying temperature is probably the critical factor here. I say that simply because irrespective of the other factors you vary in the list that you gave us: let the temperature get too high and any of those chromates will dehydrate and slough off. It's a common problem.
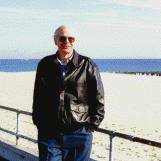
Ted Mooney, P.E.
Striving to live Aloha
finishing.com - Pine Beach, New Jersey
Ted,
Thank you for your response.
We are now drying these parts at ambient temperature, but even so this has not eliminated the problem.
We have had some success by introducing a fairly strong water based lacquer dip. Parts from within one batch which have been lacquered seem OK whilst unlacquered parts still exhibit the sloughing off problem after compression. We are not sure if the lacquer holds the chromate on or prevents the chromate film from dehydrating and becoming brittle.
A. Richard,
This is just a thought, but you might look into the possibility that your compression process is building up large amounts of heat which could be destroying the chromate film. Look closely at every step these parts take in the production process after chromate.
- Jefferson, Wisconsin
A. Dear Richard,
You may try a post-dip that improves adhesion of chromates.
Go in touch with Atotech Australia.
I am not sure if it will help, as the problem you describe very much depends upon the mechanical and physical conditions during further processing of the plated article.
regards,
- Hong Kong
Multiple threads merged: please forgive chronology errors and repetition 🙂
Q. We are attempting to set up a yellow-chromate on acid rack zinc plate. We have read that it is better on alkaline zinc as oppose to an acid zinc due to chromate adhesion issues with the acid zinc. What can we do to eliminate chromate adhesion issues and problems on acid zinc . Thanks
Nathamiel Adekoya- Binghamton New York
2000
A. It is not true that one picks the zinc plating process based on reliability of chromate application. Rather, one picks alkaline zinc for difficultly shaped work because the throwing power is much better, and acid zinc where full brightness is required (if we disregard economic and wastewater treatment issues that also affect the question).
Each process utilizes organic brighteners that can discolor the chromate or cause poor adhesion, and most suppliers of proprietaries will offer chromates with somewhat different formulations depending on which brightener residue you are dealing with. Usually, making allowance for a nitric acid dip between the zinc and the chromate offers the required flexibility in the cycle.
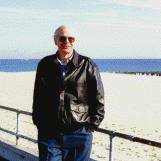
Ted Mooney, P.E.
Striving to live Aloha
finishing.com - Pine Beach, New Jersey
A. A very common problem is too much brightener. It will cause terrible adhesion and a nitric dip does virtually nothing when it is excessive.
James Watts- Navarre, Florida
A. Hi Nathaniel , The problem with Acid Zinc solutions is that the resultant Zinc plate contains a lot of Occluded "Brightener & Wetter" on the surface and if you do the conventional thing and use a pre - dip of Nitric acid it will often send that brightener Film Hard, the answer is to use a pre - dip of Hydrochloric acid and a yellow chromate specially designed ( Built around Hydrochloric acid ) for use after Acid Zinc. You can use yellow chromates based on acetic acid ⇦ on eBay or Amazon [affil links] , but then you would use a pre-dip of acetic acid. Process sequence should be similar to :-
- Acid Zinc Plate
- Air Agitated Static drag - out
- 2.5% Hydrochloric acid
- Air Agitated Cold water Rinse ( double Counterflow preferred)
- Yellow Chromate
- Air Agitated Cold Water rinse ( double counterflow preferred)
- Warm Water rinse ( not above 55 °C )
- Dry
Best regards

John Tenison - Woods
- Victoria Australia
A. The deposit from an alkaline cyanide free deposit will provide better chromate adhesion as compared to an acid chloride deposit. This is due to the superior brightness and excellent grain refine of the acid chloride process.
Typically, a plater should consider the following suggestions to improve yellow chromate adhesion:
- Operate the bath at optimum or slightly above optimum Carrier/Wetter/Makeup levels to improve solubility of the aldehyde based Brightener
- Operate the bath at minimal Brightener levels to avoid over brightening of the deposit
- Treat the bath "as needed" with activated carbon or potassium permanganate ⇦ on eBay or Amazon [affil links] to remove dragged-in organic contaminants and excessive brightener content
- Use a yellow chromate that is specially formulated to provide good receptivity/adhesion on acid chloride plated work
- Brunswick, Ohio
Multiple threads merged: please forgive chronology errors and repetition 🙂
Q. We have part with Zinc plating (8-13 mic) and yellow chromate passivation. The passivation comes off when an label with adhesive is stuck on the part and taken out. This is repeated with scotch tape also. Please help in areas to look at to improve the plating/conversion process.
Thanks,
Auto component manufacturer - Chennai, Tamil Nadu, India
2004
A. You have not mentioned the Zinc Plating Process being used? Is it Acid Chloride Based Zinc plating process as this process has some problems related to adhesion of the chromate, You must use special proprietary chromates for Acid Chloride Zinc process. The Alkaline Cyanide Free Zinc plating process is also the best process to use for good yellow chromate adhesion. Post plate rinsing (use multiple rinses of good water) and Nitric Predip can play a role, please look into this area as well.
Best of Luck,
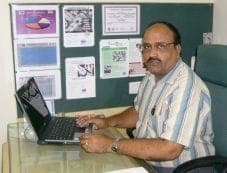
P. Gurumoorthi
electroplating process chemicals - Chennai, Tamilnadu, India
? Mr Murali,
Please do try and provide the following details .
1) The type of bath used. Cyanide. Acid. Alkaline zinc.
2) The type of chromate.. Hexavalent or Trivalent.
3) Do you have sufficient water supply for continuous flow in the rinses ?
Let me know the above. We can be of help.
Regards,
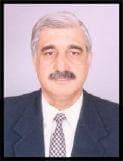
Asif Nurie [deceased] [deceased]
- New Delhi, India
With deep sadness we acknowledge the passing of Asif on Jan 24, 2016
Readers: If you don't yet see your situation, and don't wish to post, you can try --
• Topic 40069 "Chromate adhesion and abrasion testing" or
• Topic 45598 "Chromate rubs off of zinc plating" or
Q, A, or Comment on THIS thread -or- Start a NEW Thread