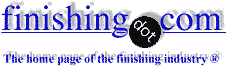
-----
Chromate adhesion and abrasion testing
Q. WE HAVE RECENTLY CONVERTED OUR ZINC BATHS TO ACID CHLORIDE AND WERE HAVING A PROBLEM WITH CHROMATE ADHESION. WE NOTICED THIS ON PARTS THAT GO TO SILKSCREEN. WE USE A CHROMATE AT A pH OF 1.6-1.8 AND CONCENTRATION OF .75 TO 1.0 %. WE HAVE TRIED PREDIPS PROPRIETARY AND GENERIC TO NO REAL SUCCESS. WOULD APPRECIATE ANY ADVICE.
KEN CLAYFlorida
1997
A. My experience with the same problem was traced to excessive brightener and the breakdown products of the brighteners. as the bath ages, carbon treatment is required. Brightener is corrected. After this is done a few times, really bright work takes excessive brightener and then it will not take chromate. The vendor, a major existing company never provided a suitable answer. we eventually had to dump and make up new. Bug hell out of the vendor for a cure would be my suggestion.
James WattsNavarre, Florida
A. The process of acidic zinc is not new so there are solutions to this problem. Usually suppliers have special chromates to acidic zinc and even special ones to chromates that come prior to painting. Ask your supplier.
Make sure that prior to chromate you have a dip of 0.5% nitric acid.
Besides, overdosage of brighteners can cause adhesion problems in the chromate.
Do you pay attention to the iron concentration in your zinc solution? If it is too high, it may also affect adhesion. You have to get rid of your divalent iron in your solution every now and then.


Sara Michaeli
Tel-Aviv-Yafo, Israel
A. Sara's comment on iron reminded me to ask how do you add peroxide. I know that there are some not so new acid zinc platers who add entirely too much, too often, and not at the correct time. Double check your technical bulletin. Since the peroxide reacts with the organic addition agents as well as any iron, it is easy to add too much, causing early contamination by breakdown products.
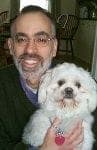

Tom Pullizzi
Falls Township, Pennsylvania
A. Ken,
Try adding 0.25 to 0.5 oz/gal boric acid to the chromate. This gets the chromate to bite rather than polish. Chloride zincs are notorious for this.
Some chemical suppliers have chloride based yellow chromates. The Kenlevel systems by Macdermid., is one such line. I have been involved in two situations where both silk screening and painting were involved. First, if there is no specification involved, look for low temperature cure inks and paints.
Secondly, although chloride zincs are really not designed to run at low brightener levels, it helps. The less amount of organics that are included in the deposit from the brightener system, the better. Organics like to expand and vaporize when heat is applied.
Finally, there is an old Northern Telecom plating spec, dating back to the 60's, that quiet clearly spells out the use of a cyanide based zinc system.
Believe me, it still works today.
Ontario, Canada
A. I recommend to you, add to your chromate sodium acetate (acetato de sodio en español) and to dry with hot air your pieces, also, don't make acceptance probes until pass 24 hours.
ING. E. RENATO VILLASE--OR MEDOZAQuerétaro, Mexico
You have received a lot of good advice. One thing I'd like to add is that an 1% add of carrier/starter (the grain refiner portion) can do wonders to improve chromate adhesion. Feel free to call to discuss the situation further.
Richard PainterCleveland, Ohio
A. Before you spend a lot of time searching out pre-dips and changing chromate, carbon treating, etc... Carefully check your post chromate procedure. Any hot water dips should be no more than 110 °F. Dryers should not exceed 140 °FF. Your problem could be that simple. Don't trust the gages...check temperatures manually with thermometers.
Mike McDonald1998
A. I had the same experience. This phenomenon is generally caused by:
- metallic (Cu, Ni, and Fe) or organic contamination of plating bath
- low pH value of chromate solution
- high concentration of chromate
- long chromating time
- insufficient surface cleaning prior to chromating
- build-up of trivalent chromium ion and zinc ion in chromating solution
- slow drying rate and insufficient dry, or inadequate chromating solution
Find the corresponding causes, then solve the problem easily.
Ling HaoGrand Rapids, Michigan
A. But there are some chromating problems specific to acid zinc solutions, which may require chromate formulations specifically for these baths.
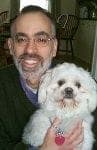

Tom Pullizzi
Falls Township, Pennsylvania
1998
Q. I "second source" my plating needs to an outside party and we have had an increasingly high rate of yellow chromate (applied after clear zinc) that either rubs off or comes off when applying adhesive tape and abruptly "ripping" the tape off. I have asked my plating supplier to provide me with a root-cause corrective action response, however, I quite frankly am not "up to speed" enough on this subject to intelligently ask the "right" questions of him. It would be appreciated if anyone who has experienced this problem or is educated on this subject could guide me in the right direction.
Randy Flowers1999
A. You are up to speed if you know that the chromate should not rub or peel off. Try rejecting the lot and see if your vendor doesn't return good parts. The right question is specifying the peel test in your purchase order as a requirement, and let your vendor decide if they can supply the chromate as you need it (along with any other requirements, such as minimum thickness, adhesion of deposit, etc.)
In most cases you will never find the root cause, as the problem will disappear when the vendor goes out on the floor to find out what happened. This happens when you reject the work and it ends up back on the loading dock of the vendor.
If pressed for a root cause, you will get some answer back for your paperwork, but I don't believe that this kind of activity improves the breed. Specifying what you need is what is good for your parts and for the finishing industry.
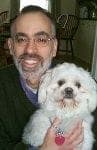

Tom Pullizzi
Falls Township, Pennsylvania
Multiple threads merged: please forgive chronology errors and repetition 🙂
Wet adhesion of zinc plated passivated film
Q. Our customers require wet adhesion of passivated film. The components are MS Tubular shaped used in the automobile industry and are plated with 8-10 microns from a warm rack Acid Zinc Bath (35 °C)( KCl-based bath) followed by full iridescent passivation using proprietary liquid passivation concentrate, chromic acid based.
As the components are bent, formed, pressed after plating the specification demands that the passivated film should not get ruptured/broken during normal handling of wet work and also during drying and transportation. The solution is being regularly analysed and the brightener additions are kept to the minimum level as stipulated and we consciously avoid excessive brightener additions.
Please advise if a post plating / post passivation dip can be used to improve the adhesion of passivated film which can withstand light mechanical working like bending / forming / pressing without quaring and also scratch resistance after drying and during storage and transport.
Mumbai, India
2000
A. Dilip I will attempt to answer your question.
First, zinc electroplate is a corrosion protective layer. Chromate (or passivate) following zinc protects the zinc from corrosion. Together they are a "sacrificial coating". Clear chromate is very thin and becomes part of the zinc. Yellow generally coats the zinc. Zinc is not an "engineered" coating designed to be stamped, crimped or machined. When you scratch the surface it destroys the chromate. Can these parts be plated following all mechanical forming operations?
When shipping parts that have been plated, if they are apt to rub against each other during transit they must be boxed to prevent this from happening.
Grand Rapids, Michigan
A. Dear Mr Dilip, Mr Hemp correctly sums up the limitations Zinc plated coatings. We all have clients making some demand or the other and one of my clients has some success in using GW's Aquaguard 300 or is it 600 (?) for a post plating crimping to which it stands up quite well. Regards,
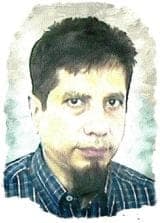
Khozem Vahaanwala
Saify Ind

Bengaluru, Karnataka, India
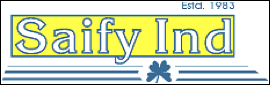
Multiple threads merged: please forgive chronology errors and repetition 🙂
Q. Is there an ASTM spec that addresses chromate conversion coatings on Zinc and Zinc Alloys (as there is for aluminum alloys ASTM B449)? I have been able to locate a MIL spec, MIL-C-17711B but surprisingly nothing under ASTM.
Secondly, why are there typically no thickness specifications for chromate conversion coatings as opposed to coating mass in grams/sq meter? Isn't the thickness measurable by eddy-current testing? Salt spray testing is appropriate for initial qualification but is not reasonable for verification lot sampling on incoming product. What method is typically used in the industry for production lot sampling to verify adequate coating is present?
Smithfield, North Carolina
2001
A. Take a look at ASTM B201-80, Darin. That's as close as the ASTM gets to a chromate conversion coating specification for zinc, as you'll note in ASTM B633 it says "the film treatment shall be in accordance with Practice B 201." B 201 refers to salt spray, to rubbing with a gum eraser for abrasion resistance testing, and a chemical spot test for presence of clear coatings. Perhaps you can modify the spot test to suit your needs.
We don't coat zinc, so I can't comment on industry tests. But we do conversion coat aluminum alloys, and since we do the coating in house we control the baths, do monthly salt spray and tape test checks, and accept parts on that basis.
Good luck!

Lee Gearhart
metallurgist - E. Aurora, New York
Testing Chromate Treatment Prior to Painting
Q. Our company manufactures windows for commercial architectures. We extrude 6063-T6 aluminum then either anodize or paint the aluminum extrusions prior to cutting the extrusions and building the window frames.
If undergoing paint, rather than anodize, these extrusions are placed onto a metal link conveyor where they pass through the chromate treating process prior to painting. The chromating process is done to permit the paint to adhere to the aluminum.
We are having some extrusions, after painting, where the paint is peeling off in the central region of the extrusion, not so much on the ends where we perform the tape and adhesion test.
My question: How can I test for proper chromate application and thickness BEFORE the paint is applied? Is there a chemical test done to the metal after chromating? Should pH of the chromator be monitored?
These extrusions are approximately 20 feet long and we are allowed to lose 3" from each end but nothing from the middle where the problem is occurring.
Thanks for your help!
Monett, Missouri
2006
A. The chromate should be very thin for a paint base. If put on too heavy the coating itself will sheer and the paint will peel off. Just get a very light yellow color.
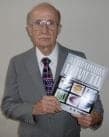
Robert H Probert
Robert H Probert Technical Services

Garner, North Carolina
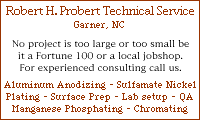
A. Hello,
There are several parameters to control chromate process, i.e., concentration, pH, temperature. And then please keep clean your parts as following until paint application because fresh chromate film is very weak.
1. Keep minimum handle or touch (do not touch surface, use edge) as possible
2. Wear clean cotton gloves when handling
3. Apply paint within about 48 hours after chromating
Busan, Korea
Thank you for your comments.
We paint the extruded aluminum rails immediately after the chromating process. So there is little time between the operations.
I will enforce cotton gloves on the line. Good advice. We will be monitoring other elements of the chromating process as well, making sure it is not applied too thinly.
Again, thanks for all of your help.
Monett, Missouri
2006
A. Before I saw your reply, my thoughts were it was too thick, or dried at too high a heat, or too soon after chromate. It is a gel and should be forced dried or let set for a day and then painted. within 2 to 3 days.
James WattsNavarre, Florida
Q. I'm in the process to document procedures to test yellow chromate plating in our facility.
I have read ASTM B449 and ASTM B571 and I could not found any item that describe how can I test the adhesion of the yellow chromate.
I have heard that I can use an eraser to find for any poor adhesion however I would like to have a solid ASTM to refer for.
Please help,
Nogales, Arizona
2006
A. ASTM B201-80(2004) "Standard Practice for Testing Chromate Coatings on Zinc and Cadmium Surfaces" has an abrasion test using a soft gum eraser. ASTM B571 tests adhesion of metallic coatings, e.g., the zinc plating.
If the chromated zinc gets painted (or if you're willing to paint test panels), try the paint adhesion tests in ASTM B449 "Standard Specification for Chromates on Aluminum." These include the wet tape & knife tests of FED-STD-141, plus a cross hatched-paint tape test.
- Goleta, California

Rest in peace, Ken. Thank you for your hard work which the finishing world, and we at finishing.com, continue to benefit from.
Q. I am a worker in a small zinc plating shop and we buy chromate conversion coating in 10 kilo package. after several dipping parts in solution it becomes weak and unusable. I want to know the complete ingredients and the percentage of them and the pH value and the exact temperature should be used. Yours sincerely,
Peenory pianyTehran, Iran
2007
A. Hello, Peenory. In Western countries only proprietary chromate conversion coatings are used these days for many reasons. Some of those reasons are the need to move to hex-free formulations for consumer safety and to comply with RoHS requirements, to eliminate the cyanide traditionally used in older formulations, to comply with Qualified Product Lists in specifications, to insure ISO compliance, and so that there is an advanced laboratory that can issue technical data sheets specifying the optimal temperature and pH for the particular formulation.
So no one will tell you the secret formulations that they worked so hard to develop. If you want to make your own home-brew chromates to older formulas, the best source is probably expired patents. Good luck!
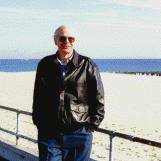
Ted Mooney, P.E.
Striving to live Aloha
finishing.com - Pine Beach, New Jersey
Q. My chromate supplier swears that there is a tape test spec for adhesion of yellow chromate over zinc. I am aware of the spec that references the eraser test but cannot find any thing that specifically addresses yellow chromate over zinc. My customers customer has decided to start testing chromate adhesion with duct tape :) thats a joke I hope. They are using tape and your help would be appreciated.
Michael Patrick LowdenEugene, Oregon
2007
A. The tape test is normally used for select plating adhesion. The MIL spec for that calls out for a tape that used to be made by 3M. I would expect that specs of chromate would come off with most duct tapes and all of it come off on chromate that is less than 24 hours old.
Ask him for a reference. Just using any old tape for a QC test is not smart. Plan on seeing lots of trouble in the future over this. Check the Mil and the AMS specs for the QC on the chromate after the plate. Also check to see if there is a QPL for the chromate. That will have some stringent tests that might not be in the plating spec.
Navarre, Florida
A. I believe the tape is 3M #250. You have to make sure you get a cert with the tape to verify the date of Mfg.
Jeff ChewMilpitas, California
July 8, 2011
Q. My question is, with zinc plating we have yellow, black, blue chromates, etc.. Is there a standard for tape testing the chromate colors? And if so how long after plating and what type of tape, i.e. scotch, masking etc.
R. K. JOHNSON, PRESIDENT,PORTLAND, Oregon
July 28, 2009
Q.
Dear Sirs,
Please guide us for the standard method of checking hexavalent yellow chrome adhesion over zinc plating.
Pune, India
November 5, 2012
Screen printing on zinc plated and chromated surface peeling off
Q. I'm working as a production executive in an engineering company and currently, there is a requirement of doing screen printing on trivalent blue zinc-plated metal. The ink is peeling off from the surface after conducting a tape test. May I know what is the root cause of this? Thank you.
Micheal WongMalaysia
March 5, 2020
A. Hi Micheal
It sounds to me like maybe the chromate is coming off and taking the printing with it. So I'd suggest step one is test the chromate before the screen printing. Please study this whole thread -- it has great info. Good luck.
Regards,
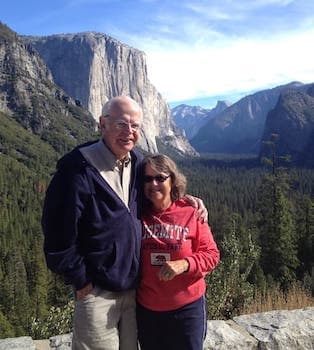
Ted Mooney, P.E. RET
Striving to live Aloha
finishing.com - Pine Beach, New Jersey
Chromate Delamination of Zinc Chromate from Zinc on Steel
Q. What is the best way to investigate the source of zinc chromate delamination off zinc on steel from edges or holes?
James Heaps-NelsonFremont, California
May 14, 2020
Q, A, or Comment on THIS thread -or- Start a NEW Thread