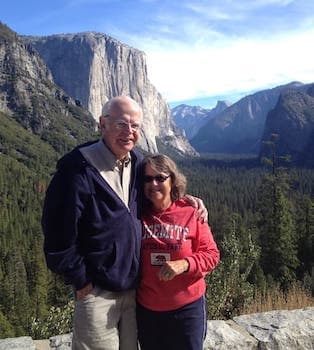
Curated with aloha by
Ted Mooney, P.E. RET
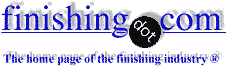
The authoritative public forum
for Metal Finishing 1989-2025
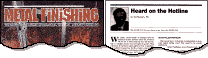
-----
Ematal Process, Opalizing
Q. I'm looking after the meaning of "opalescence" or "opalizing" of Aluminum. I think it is a kind of "hard anodizing" of Aluminum, but I'm not sure.
Can somebody help me find more information about this way of anodizing?
- The Netherlands
1997
A. I did some anodizing of 3003 aluminum in 15% oxalic acid with a 3003 aluminum cathode. The results were very interesting. When the sample was rotated by about 45 degrees, in one angle it showed green, in the other angle it showed a reddish color. Many of my anodizing samples look opalescent.
Dave Fairbourn- Sandy, Utah
1997
A. Opalizing is a process invented by Philips in the early sixties. It is a kind of a hard anodizing process with a very specific color.
The color is caused by the combination of the material composition and the composition of the anodizing bath.
The main constituent of the anodizing bath is oxalic acid but there are some other elements involved as well.
The process is called "opalising" because the coating is not transparent (looks like enamel).
A similar process is a German process called Ematal.
Philips galvanotechniek - Eindhoven, Netherlands
1997
Q. To: Gijs Gerlagh
Would you be kind enough to give us more information regarding the Philips and Ematal process?
Much thanks
- Hong Kong
1998
Q. I'm looking for the right name or process for an aluminium coating that we had used back in Switzerland on all our tight tolerance aluminium parts: It was called : "ematalieren" It's supposed to be a similar coating as hard coat. It allows to coat parts within very small tolerances.
Best regards,
Georg
Illinois
1999
A. There is a section (pg 452-456) in Vol 1 of The Surface Treatment and Finishing of Aluminum and Its Alloys by S. Wernick, R. Pinner, P.G. Sheasby about the Ematal process, it say's Originally oxalic acid acid solution containing salts of thallium, zirconium or titanium, there are also a number of formulations given for the original version and later versions of the solution
Regards,
- Lowestoft, U.K.
1999
2000
Q. In our subsidiary company "Alphasem", located in Switzerland, we daily use an Aluminum treatment called " Standard Ematal". I would like to use this technique here as well, but it seems that this treatment is unknown. Is it really? Characteristics:
- -titanium penetrated anodizing
- -hardness 350 - 550 HV
- -high abrasive resistance, excellent sliding quality
- -smooth, crack free,pore free surface
- -grey - grey/brown
- -coat thickness: 8-18 micron
- Binghamton, New York
A. Hi Roman,
Ematal process has been commercialized for a couple of decades in Europe and Japan. It is true that the process could not gain significant market share in the North American anodizing market. This process uses an electrolyte comprising mainly titanium salt and oxalic acid instead of sulfuric acid. Of course, the operational parameters are different those employed in conventional sulfuric acid anodizing and hardcoat anodizing.
High quality Ematal coating gives rise to a white/greyish white color, depending on alloy. If brown color occurs, it means likely that the electrolyte has become deteriorated. Since your subsidiary company has the process, you should be able to get it easily. Regards, Ling
- Grand Rapids, Michigan
2000
2001
Q. Dear sir:
We have to start Ematal Anodizing, but we have some problems with our chemical solutions. P.T.O. 10 g/ltr. citric acid 10 g/ltr. chromic acid 10 g/ltr. 40 to 100V at 50 °C temp. We want solution on this. Our solution did not offer long life.
Yours faithfully,
- India
A. Hello, you write P.T.O. Are you really using Potassium- Titanium- Oxide- Oxalate-2-H2O?
We have good experience without Cr and the solution will last at least several months.
If I shall help you, please tell me your questions.
Regards
- Nussbaumén, Switzerland
2003
Need Hard Ematal plating, preferably on 6061
I am familiar with Hard Ematal plating being applied to 5083 aluminum. I have a batch of 6061 aluminum plates I would like to have coated with Hard Ematal. Are there any compatibility issues to be aware of using Hard Ematal on 6061? Also, are there any sources for Hard Ematal plating in the United States?
Thank you!
Lanco Assembly Systems, Inc. - Westbrook, Maine, USA
2005
Ed. note: This RFQ is outdated, but technical replies are welcome, and readers are encouraged to post their own RFQs. But no public commercial suggestions please ( huh? why?).
2007
Q. Dear sir,
I am having problem with the ematal bath.I am using 10 g/l potassium Titanium Oxalate Acetate, 10 g/l citric acid and 10 g/l chromic acid. Temperature at 50 °C.
My problems are:
1. What is the correct current density used?
2. The deposit is soft. The deposit will peel out when cut with a sharp aluminium part. How to make it hard as the hardness of quartz?
3. What is the deposition speed (micron/minute) when apply certain current density, e.g., 3A/dm2?
4. Please advise on the ematal bath ingredients e.g the chemicals and their concentration.
5. What is cathode material used?
Thank you very much in advance.
Plating shop - Penang , Malaysia
Q. I am looking for a vendor in the region near Singapore who can do Ematal process for Aluminium.
Joe Siewservice provider - Singapore
March 6, 2009
Ed. note: This RFQ is outdated, but technical replies are welcome, and readers are encouraged to post their own RFQs. But no public commercial suggestions please ( huh? why?).
Pitting of 2024 Aluminum with Standard or Ematal Anodizing
February 14, 2019Q. Hello, I'm working as a R&D mechanical engineer in Switzerland, I have problems with anodization of machined parts made of aluminium 2024 T3... ;-)
We machine the aluminium parts, using standard cutting fluid (we also machine stainless steel with the same cutting fluid of the same machine). After machining, we clean them with warm water, then with isopropyl alcohol and then we dry them in oven at about 212 °F (100 °C).
Then we send the parts to our subcontractor for anodizing. For some parts we don't specify the treatment, for some other we ask for a treatment called EMATAL (it is made in a special electrolyte (oxalic, boric and citric acid , potassium oxalate-titanium).
When we get the parts back from anodizing, we can notice dark pitting on the surface (with both treatments, but more pronounced on standard treatment).
But the main problem is that the insulation resistance of the anodized surface is not reliable (on both treatment). As we need a good insulation resistance for our application the failing parts must be discarded...
I was wondering if another type of cleaning after machining, or if another type of anodizing could improve this problem?
Does anyone have some advice or experience to share?
Best reagards
Yves
- Rossens, Fribourg, Switzerland
A. I cannot comment on the oxalic process but here are two thoughts that come to mind: (1) If the cutting fluid is loaded with stainless steel then it may imbed steel particles in the aluminum, plating away towards the end of the anodic cycle and leaving a pit, however (2) the "pits" are elongated and that appears to be from having been "cold drawn", in which case there is nothing you can do.
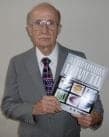
Robert H Probert
Robert H Probert Technical Services

Garner, North Carolina
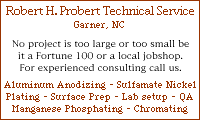
February 14, 2019
![]() |
A. Hi Yves, Aerospace - Yeovil, Somerset, UK February 15, 2019 A. Yves - Green Mountain Falls, Colorado February 18, 2019 |
February 20, 2019
Thank you so much for your answers and advice!
It seems to me that pitting is more present on 2024-T3511 (which goes through a stress relief process by stretching) than on 2024-T3.
This may be linked to the "cold drawn" mentioned by Mr. Probert.
The problem is more than 10 years old, there are difference between batches, but we could still manage to get acceptable quality.
If machined with isopropyl alcohol (conventional machining) and sandblasted (+ handling with cotton gloves) before anodizing, the pitting is well reduced.
But this method it too time consuming.
The suppliers are "ISO 9001..." but we do not have access to any information about their process.
We already changed suppliers several times. But the problem comes back.
We should at least specify a standard thickness and try a corrosion preventative before sending the part to the supplier.
It is probably the sum of several of the mentioned factors that creates this situation.
I'll let you know how it all goes.
Best regards
Yves
- Rossens, Fribourg, Switzerland
A. It is important to examine the quality of the raw and ematal parts. 2024 is not optimal for the Ematal process. But it can also be caused by corrosion during processing. A process optimization is possible. Why do you need 2024? There are better variants / materials for a compact, insulating layer with Ematal.
The lot differences could be investigated, 2024-T3511 does not generally have a different texture to 2024-T3. The cold drawn is only small. A comparison of the certificates would be interesting.
- Hallau, SH, Switzerland
February 28, 2019
Q. Dear anodizing specialists!
I'm trying to provide the ematalizing process in my anodizing line in Ukraine, so need help.
Here are the questions:
When using Potassium titanium oxalate electrolyte solution with boric & citric acid - what is the concentration of components?
What is the cathode material? Aluminium, metal or titanium?
For how long does this electrolyte will last?
- Kyiv, Ukraine
June 2, 2020
Q, A, or Comment on THIS thread -or- Start a NEW Thread