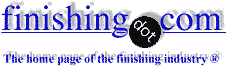
-----
White Bronze Plating: an alternative to nickel
Please see also --
• Topic 0037 "Albaloy, Miralloy, Optalloy copper/tin/zinc alloy plating"
• Topic 34483 "Imitation rhodium plating chemistry"
⇦ Tip: Readers want to learn from your situation;
so some readers skip abstract questions.
Q. Hey,
Hope! You all are doing well.
I want to know about the white bronze chemistry as I am in a research phase of my study.
If anyone could help me out. Will be highly appreciated.
student - Karachi, sindh, Pakistan
May 30, 2022
A. Hi cousin Hamza. White bronze is an alternative to nickel, often used on jewelry and similar items to provide a bright plating layer while avoiding possible exposure to nickel (which can cause the wearer to suffer 'nickel itch'). White bronze involves simultaneously depositing 3 metals -- which is a difficult trick because the metals have different electrochemical potentials so only the most noble 'wants' to plate out, the other two 'want' to stay in solution. So the metals have to be 'complexed' so that they are no free ions in solution. Some suppliers offer proprietary processes for the purpose.
This page offers a good intro to the subject and useful vocabulary and links for further research; and if you have specific questions I think the readers will be happy to try to answer them for you.
Luck & Regards,
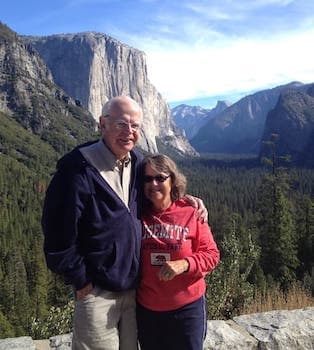
Ted Mooney, P.E. RET
Striving to live Aloha
finishing.com - Pine Beach, New Jersey
Q. Many thanks. However, I know the combination of metals but I don't know the chemicals which are used to make the water in which we use this bronze plate.
Please tell me the chemicals we use in dissolving bronze to other metal products.
Student - Karachi, Sindh
A. Hi again Hamza. Brenner's "Electrodeposition of Alloys" ⇦[this on Amazon, eBay, & AbeBooks affil links] includes 6-pages specifically on copper-tin-zinc alloys (Chapter 18.2), plus discussions on 6 other bronze-like ternary alloys, as well as more than 1300 pages on the general theory, practice, and problems involved in alloy plating. Try to get access to a copy.
I have to mention this to not mislead other readers: white bronze plating is usually done from commercially available proprietary solutions, not home-brew mixes. You're certainly welcome to pursue whatever you wish, but developing a robust white-bronze plating bath sounds like the work of many months, and possibly years. Good luck!
Regards,
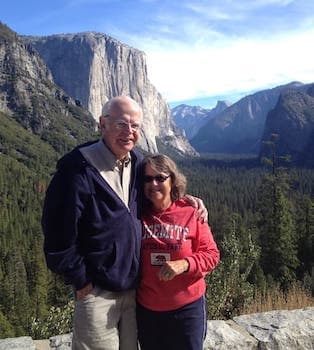
Ted Mooney, P.E. RET
Striving to live Aloha
finishing.com - Pine Beach, New Jersey
⇩ Related postings, oldest first ⇩
Q. White bronze plating is used to replace Ni for the jewelry industry, what is the plating thickness?
WY Wong- HK
2001
A. Put 0.001 inches on it, and the jewelry will show up in antique shows 50 years from now. Put 0.00001 inches on, and like Broadway Gold, it will be the first thing to turn green in the spring.
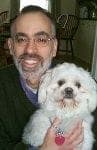

Tom Pullizzi
Falls Township, Pennsylvania
Q. Does anybody know about the corrosion resistance (in terms of ASTM B117 hours) of white bronze (with and without zinc/lead) coatings?
Best regards,
- Istanbul, Turkey
2003
Q. I'm looking for a more environmentally friendly alternative to nickel plating on brass. Would cyanide-free white bronze plating be a good candidate?
Any other suggestions would also be appreciated.
Thanks,
Intern, Production Eng - Birmingham, UK
August 22, 2008
Ed. note: This RFQ is outdated, but technical replies are welcome, and readers are encouraged to post their own RFQs. But no public commercial suggestions please ( huh? why?).
A. Hi, Liz. White bronze is a substitute for nickel and will often prove acceptable. And if your product is jewelry, it addresses the issue of nickel allergy (leachable nickel is not permitted on jewelry in the EU).
But "environmentally friendly" without agreed-upon metrics is an empty buzzword, and I seriously doubt that white bronze is more environmentally friendly than nickel by any metric :-)
Due to relentless environmental pressure to reduce "environmentally unfriendly" phosphatizing, the world now suffers needless multibillion dollar annual corrosion, a colossal waste of energy & resources, and a complete lack of sustainability. Millions of tons of steel is no longer phosphated although we've known for 60 years how vital it is. We now mine, smelt, roll, fabricate, paint, package, sell, use for a short time then scrap (with transportation between each step), countless tons of steel every 2-3 years instead of the 20-30 years it used to easily last when properly phosphatized. We saved a ounce of phosphate at the cost of a ton of steel.
Please try to tell us what comprises "environmentally friendly" to your mind and then we can try to answer better whether white bronze is an environmentally friendly alternative to nickel. Good luck.
Regards,
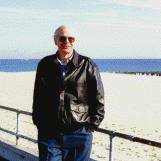
Ted Mooney, P.E.
Striving to live Aloha
finishing.com - Pine Beach, New Jersey
A. Liz, you are in the heart of the jewellery trade in the UK. There are numerous organisations within 10 minutes walk of the city centre that can answer your problems and give you a huge insight into the metal finishing industry. Try talking with the Institute of Metal Finishing on Holloway Head, or the Metal Finishers Association in Vyse Street. There is also the Jewellery Manufacturers Association (I think in Vyse Street) and there is the College of Jewellery and Design (University of Central England, NOT Birmingham or Aston!)
White bronze is being used as a barrier layer in jewellery and other parts where nickel is banned. It does work well and is very effective. However, there are other alternatives, depending on what you are trying to do. If you can tell us what you are doing, there will be more help, but tap into the knowledge of your local experts first! Sorry to be so negative, but do the groundwork first and then come back and see what we can offer.
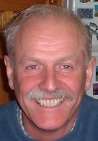
Trevor Crichton
R&D practical scientist
Chesham, Bucks, UK
Q. Hi,
Currently, we are plating brass fittings with bright nickel for identification between imperial and metric size parts (metric are plated, imperial left brass-coloured), aesthetics and corrosion resistance. But, looking ahead to REACH regulations from the EU, substances such as nickel are being restricted. This is why I'm looking for processes that will not be condemned by the EU in a few years time. I've looked at metal plating, such as white bronze, zinc, tin-cobalt, as well as dry deposition techniques, such as PVD, CVD, HVOF. What I'm looking for is something that is ideal for barrel plating large volumes of small fittings with a decorative commercial finish, typically 3-5 microns thick, but preferably does not contain nickel or compounds equally or more toxic.
Thanks,
- Birmingham, UK
A. White bronze should be a good choice because it looks like what you are currently using, Liz; and it is widely used in jewelry, so there will be ready commercial sources ... although zinc plating would be an obvious answer if aesthetic enough for you.
Many people have skin allergies to nickel, but I would not call it "toxic". Electroformed nickel is used in stints and other items implanted into the body, for example. Hopefully if you or I ever need a stint it will be reliable electroformed nickel not white bronze :-)
Regards,
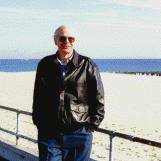
Ted Mooney, P.E.
Striving to live Aloha
finishing.com - Pine Beach, New Jersey
A. Liz, I am only trying to second guess what you really want - barrel plating is relatively easy to do, but you are limited to metals and alloys that can be electrodeposited from aqueous solutions. However, there is technology around that uses a barrel plating concept but with PVD/CVD type equipment. The people doing it in the UK are Teer Coatings Ltd in Droitwich - well worth a quick 'phone call and chat! Have a look at their website.
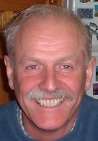
Trevor Crichton
R&D practical scientist
Chesham, Bucks, UK
Salt Spray Resistance of White Bronze
(Techni-White, Albaloy, Miralloy, Optalloy, copper/tin/zinc alloy plating)
Q. Hi,
We are plating brass parts with 200-250 micro inches of Albaloy and the plating hasn't been withstanding an intense Salt Fog test per ASTM B117. Should Albaloy plating hold up to a 40 day salt fog test? What thickness would be required to prevent any staining on the connector? Are there any alternate suggestions on plating that can withstand such a test?
Thanks and best regards,
Rob
Project Engineer - Beverly, Massachusetts
October 15, 2008
A. Hello Robert,
The corrosion resistance of White Bronze will depend on the base metal condition (Ra values) & the porosity of the brass in addition to the porosity of the Plating.
You can increase the corrosion resistance by plating two layers of White Bronze in different Chemistries, or adding a topcoat of Tin-Nickel alloy over the White bronze.
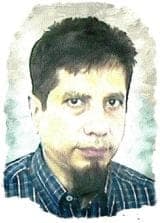
Khozem Vahaanwala
Saify Ind

Bengaluru, Karnataka, India
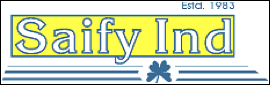
Q. Thank you Khozem. My customer is recommending that we use a Silver underplate. Does that make sense to you?
Thanks again,
Rob
- Beverly, Massachusetts
A. Hi again,
Sorry for the late response, I don't think it's necessary. I recommend a minimum 3 micron coat of bright acid copper plating directly over the brass before any other plating instead.
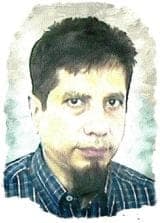
Khozem Vahaanwala
Saify Ind

Bengaluru, Karnataka, India
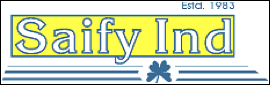
December 4, 2008
Q. Hello all.
Firstly thank you all very much for your time and effort in creating a very helpful site, I started a very basic Jewellery finishing business in Egypt 3 years ago and this site was of paramount help; even if it didn't always dish the facts on a plate, it helped me to learn what I needed to know.
At this stage of the business we wish to send goods to Europe and the USA; many goods produced here would benefit from a nickel-style undercoat before being flash/pen plated in Silver, Rhodium or Gold..
Nickel is still the primary agent used despite many people suffering allergies here too. I would like to introduce white bronze plating to Cairo. I have a basic workshop with a working budget (not a huge a one) but I have access to 10-100 amp transformers used for plating, most chemicals and common equipment. We construct the baths here, my workshop has ample ventilation and is safer than most, I take care of myself, my staff and my customers.
Any assistance into the technical requirements for a small scale white bronze plating bath solution and anode requirements would be extremely helpful, I am of course aware different people have different opinions and I will take what good I can find in them with gratitude.
Please note any further references or other insightful resources would also be well received; while I do not wish to seem too frugal, the truth is I work within a very tight frame of economics and prefer the small start up that grows as opposed to the large capital hungry business model.
Kind regards,
- Cairo, Egypt
December 13, 2012
White Bronze Plating of Zinc Die Cast Jewelry: Thickness Needed?
Q. Hello all,
I'm a young engineer working on a wearable technology product. I'm new to the world of electroplated finishes, and would appreciate some advice.
I have a zinc die cast component that sits in constant contact with the skin, like the back of a watch. The surface of the raw die cast zinc components quickly darkens in contact with the skin. I would like to electroplate a layer of white bronze to prevent this from happening, while preserving the electrical conductivity of the part (necessary for the application). I would have chosen chrome, were it not for concerns over nickel allergies.
Can I ask for some suggestions as to thickness? I have gotten a quote for a 2.5 micron layer for a price that I consider quite reasonable, but I'm wondering if that will be sufficient. My goal is for the coating to survive a year in constant contact with the human skin.
I've learned a ton from reading these forums, and would be grateful for any insight you folks could provide!
Regards,
Roger
Engineer - Cambridge, Massachusetts
September 16, 2015
A. Hello,
2.5 microns will be fine. I'm sure your plater will know what chemistry they will use that will coat and seal the surface of the Zn die-cast parts before the white bronze plating.
Process Engineer - Phoenix, Arizona USA
⇦ Tip: Readers want to learn from your situation;
so some readers skip abstract questions.
Q. Sir, can you say how much voltage used in white bronze?
Sunny vallechaShree rhodium - East Delhi, India
March 26, 2018
A. Hi Sunny. The voltage required for electroplating is primarily related to the solution resistance, which in turn is primarily determined by the anode-cathode spacing and whether you are doing rack or barrel plating. For jewelry plating 3 volts may be enough, whereas 12 or even more might be required for high production barrel plating.
Regards,
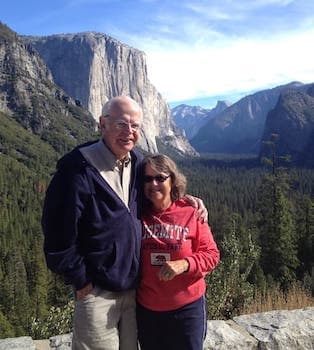
Ted Mooney, P.E. RET
Striving to live Aloha
finishing.com - Pine Beach, New Jersey
April 2018
Q. We are doing white bronze plating. We see some white precipitation in the bath, which we guess may be tin.
Bath temperature is 60 °C and pH is 11.5
I have the following questions:
- when does tin deposit in white bronze bath?
- how can it be redissolved?
Any suggestion will be highly appreciated.
- shiraz, iran
December 22, 2019
A. Hello niloofar
I hate to be the one to tell you, but typically once the tin drops out of solution in alloy plating, the bath is most likely considered dead. The tin drops out of solution because it oxidizes. Once oxidized the solution is [un]able to redissolve it easily without destroying other components within the bath.
The most common reason tin drops out of solution is through aeration. This is usually through the use of air agitation in the solution (don't use air; use eductors for solution mix) or the pump is pulling in air and mixing it with solution.
There are a wide range of other reasons for tin to drop out however that is dependent on the chemistry of bath you are running.
Hope this helps!
Amphenol Aerospace - Sidney, New York USA
January 3, 2020
Q. Hi everyone,
As I mentioned in my previous question, we own a small plating shop where white bronze plating is carried out.
It is a while we have faced an opaque white cloudy coating. Bath has been analyzed thoroughly and we have replenished the bath but it did not help.
Any suggestion or comment as well as introduction of any useful reference will be highly appreciated.
Temperature is 60 °C and pH= 12-13
Base material is brass.
Thanks in advance,
- Shiraz, Iran
February 23, 2021
(to provide context, hopefully helping readers more quickly understand the Q&A's)
A Hull Cell ⇦ huh? is a tiny laboratory-scale plating tank. From a bird's eye view it is trapezoidal, with the sample panel very close to the anode at one end and very far from the anode at the other end. Thus a single test panel displays what happens all across the current density range from very slow and thin plating to very fast and thick. The difference in appearance across the range can very often hint at what is wrong. Please search the site for more info.
A. Hi Niloofar. Despite the bath being analyzed, metallic or organic contamination seems very likely to be the cause. If you can e-mail a pic of a Hull Cell panel to mooney@finishing.com for posting here, readers can often make a highly educated guess as to the problem. Good luck,
Luck & Regards,
Ted Mooney, P.E. RET
Striving to live Aloha
finishing.com - Pine Beach, New Jersey
Q. Can I use my White Bronze make up for using Pen plating?
Dhirav Joshi- Kolkata WestBengal
September 11, 2020
A. Hi Dhirav
Tank plating solutions are usually too drippy and watery for proper pen plating. Do a couple of lab experiments, thickening the solution with barium sulphate or maybe fumed silica to see if the solution still looks good and is thick enough. I'm not sure whether you can get the right alloy to deposit or not.
Luck & Regards,
Ted Mooney, P.E. RET
Striving to live Aloha
finishing.com - Pine Beach, New Jersey
Q. Hello everyone.
There are black marks on the components which we are plating with white bronze.
If anyone knows I will appreciate it.
Thanks. Omar adel
- Egypt cairo
March 1, 2021
Q. Black or brown marks appear on the surface of plated parts after (copper_tin_zinc) alloy (white bronze electroplating ...
Chemist - Egypt
January 13, 2022
A. There will be black spots because the alloy is not correct. Look at your alloy. Try high amperes first. The stain will disappear.
nihat derin [via translate.google.com]- istanbul, Turkey
June 21, 2023
Q, A, or Comment on THIS thread -or- Start a NEW Thread