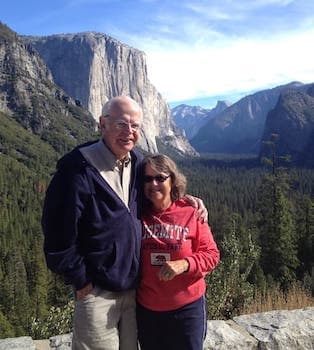
Curated with aloha by
Ted Mooney, P.E. RET
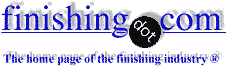
The authoritative public forum
for Metal Finishing 1989-2025
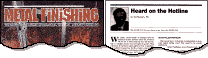
-----
Electrochemical De-burring/Grinding of Micro Surgical Knives

Q. Sir
We are manufacturing Micro Surgical knives from AISI 420 grade stainless steel material. We'd like to remove the edge grinding burr by using electro chemical machining/grinding process. At present we do buffing. Kindly suggest suitable process with diagram and technical details. Then we can develop this process. Any further more information required by you please reply here.
- Maharashtra, India
September 13, 2022
A. Hi Ashish,
adv.: If you want to acquire the electropolishing method for such 420 instruments, please contact me directly. You will be able to deburr as many parts as the capacity of the electropolishing tank allows. The processing takes only 1-2 minutes, if only burrs needs to be removed. The process is eco-friendly and full-proof, installed already in metal-finishing shops in USA and Europe.
Anna Berkovich
Russamer Lab
Pittsburgh, Pennsylvania
⇩ Related postings, oldest first ⇩
Q. Electrochemical Deburring
I'm the principal engineer for a 2nd Tier automotive manufacturing company. We manufacture high volume, high precision components for the turbocharger, and fuel systems industry worldwide. Principal machining processes are turning, grinding, light milling etc with high level of automation. Turnover £15M PA (290 employee) Growth, 10-15% PA last 5 years
Problem 1
Existing business (current 4000/wk going to 20000/wk in 12months). Component (ERL 1025) is a silicon iron turned component with 25mm OD 5mm bore with a 1.5mm slit from OD to Bore ('C' shape when looked at from end on.) We currently use glass bead shot blast to deburr the intersection of the slit and the diameters. This is ok but not ideal. As volumes increase we need to invest in more deburring equipment. We are looking for a more elegant, cleaner, consistent, better quality deburring process.
Problem 2
New business (20,000/wk) Starting June 05. 420 Stainless Steel 14.5mm OD, 8mm ID, 8mm long with 5 3.5mm holes drilled end on (longitudely) on a PCD. Deburring is required for intersections of holes and diameters. This part is currently manufactured, and chemically deburred in Japan but production is moving to Europe.
We believe Electro Chemical deburring could be a solution
RFQ I am looking for a chemical deburring company who can sell me a production machine (preferably automated) for both of these components. (potentially more components)
Thank you in advance,
Charles R [surname deleted for privacy by Editor]
Principal Engineer for 2nd tier Automotive component manufacturing company - Liverpool, Lancashire, England (UK)
2004
Ed. note: This RFQ is outdated, but technical replies are welcome, and readers are encouraged to post their own RFQs. But no public commercial suggestions please ( huh? why?).
Q. Sir
We are manufacturing Micro Surgical knives from AISI 420 grade stainless steel material. We'd like to remove the edge grinding burr by using electro chemical machining process. At present we do buffing. Kindly suggest suitable process with diagram and technical details. Then we can develop this process. Any further more information required by you please reply here.
Regards,
VAIDIYAM AMARNATH
ENGINEER - MADURAI, Tamil Nadu, India
June 13, 2008
A. Electrochemical deburring is a technology that evolved from electrochemical polishing. There are numerous patents on the subject and I am sure that one of the larger razor blade manufacturers such as Warner Lambert, Schick or Gillette may be willing to license some of their older technology to you for a suitable fee. Alternatively, you can develop and use your own process, based on electropolishing.
Trevor Crichton
R&D practical scientist
Chesham, Bucks, UK
adv.
Anybody who requires licensing such technological process, contact us. See picture attached.
Anna Berkovich
Russamer Lab
Pittsburgh, Pennsylvania
Deburring with electropolishing solution
Q. I have a 304 part with sharp teeth formed via grinding. I will use electropolishing to deburr and polish. Can some provide names of good electrolytes for deburring and also noted electropolishing equipment suppliers (Europe or US based).
Also is a high sulfuric content better for deburring. If so why?
Alan Ronan
Research - Ireland
July 25, 2011
A. Hi, Alan.
I'm not too familiar with electrochemical machining and deburring but, yes, I suppose you could try conventional electropolishing as a deburring step. The Electroplating Engineering Handbook ⇦ this on eBay, AbeBooks, or Amazon [affil links] has an excellent chapter on electropolishing of stainless steel, including a list of many different electropolishing solutions. Many work fine, but I would say don't use perchloric acid as it is horribly dangerous and perhaps illegal (see topic 9408).
Some electropolishers electropolish in straight sulfuric acid, so "high sulfuric content" is certainly doable, but I can't say it's better.
If you want people to contact you privately, let us know and we'll convert your question to an RFQ and vendor suggestions can be sent to you privately; but we can't publicly suggests brands or sources ( huh? why?)
Regards,
Ted Mooney, P.E.
Striving to live Aloha
finishing.com - Pine Beach, New Jersey
Q, A, or Comment on THIS thread -or- Start a NEW Thread