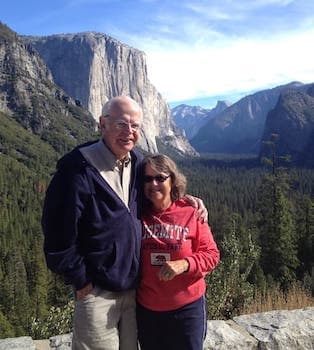
Curated with aloha by
Ted Mooney, P.E. RET
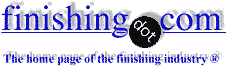
The authoritative public forum
for Metal Finishing 1989-2025
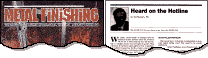
-----
Bright Dips for Copper & Brass: Chrome-free or less toxic alternatives
Q. I am looking into possibly replacing my copper bright-dip line with a more environmentally friendly product. We bright-dip our copper to obtain a chemically clean finish, cleanliness is the only concern, cosmetics is not a concern at all. Some of our copper parts are nickel plated, some are not. If anyone is aware of any products or methods I could try please let me know. I am currently trying Q-plex (part potassium persulphate) pre-plate made by Macdermid.
Dave Bernardini1998
A. Dear Dave ,
If the Q Pex pre Plate doesn't work or is too expensive and all you want to do is clean the parts prior to plating , what about a simple alkaline clean to remove processing oils and other soils then a dip in 20% sulfuric .
If you think this is not aggressive enough try one of the Sulfuric
/ hydrogen Peroxide pickles ,if a polish is required you can add up to 20 % ethylene glycol , air agitation helps to maintain the peroxide level
regards

John Tenison - Woods
- Victoria Australia
Tip: Readers want to learn from Your Situation 🙂
(little can be learned from abstract questions, so many readers skip them)
Q. How do you get copper bright?
Diane Litchy1999
Q. Due to environmental and safety issues, we stopped using chromic acid based bright dip. The mixture is chromic acid diluted in 90% by volume of water and 1% sulfuric acid. We manufactured precision swiss automatics products made of brass, copper and phosphorus bronze.
I read an article that ferric sulphate can be substituted for chromic acid. Is it possible to dilute ferric sulphate with water and 1% sulfuric acid and similar effect as the chromic acid based bright dip? Any suggestion with be greatly appreciated.
Rey Tinio- Yucaipa, California , USA
2000
A. Rey - Try using a peroxide based bright dip. These are generally 10% or so sulfuric and the rest water and peroxide. This will produce a beautiful finish on copper, brass, etc., without the nitric cloud. As an added bonus, if you're only processing copper, the major waste byproduct is copper sulphate ⇦ this on eBay or Amazon [affil links] - something you may be able to sell to a chemical mfgr. in your area.
Dan Brewerchemical process supplier - Gurnee, Illinois
Q. I already tried and tested peroxide based bright dips from four different suppliers. Peroxide based bright dips works well with brass which leaves a shiny finish but leaves white spots on our parts surface if inspected under microscope.
Peroxide based bright dips do not perform well on beryllium copper and phosphorus bronze alloys. Hydrogen peroxide also upsets our chemical treatment. It reacts with dissolved non-ferrous metals by foaming a lot in the chemical treatment. I looking for a bright dip that does not etch non-ferrous alloys.
Rey Tinio [returning]- Yucaipa, California, USA
A. Rey, you could be absolutely right that sulfuric-peroxide is not a good choice for your circumstances, and you may be right to dismiss it in your particular case. But for other readers, and the more general case, I do know of shops that successfully bright dip beryllium copper with sulfuric-peroxide; they do solvent drying, rather than water rinsing & drying, and you might want to double check that the white spots are not salt residues from water rinsing.
The next person shouldn't necessarily write off sulfuric-peroxide--I think it may be worthy of a careful second look. Best of luck!
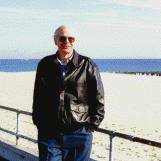
Ted Mooney, P.E.
Striving to live Aloha
finishing.com - Pine Beach, New Jersey
2000
Need "Zenith cub" product for brightening copper & brass
RFQ: I'm searching for the supplier for the product zenith cub. A nitrate-free and chromium=-free product for brightening of brass and copper.
Best Regards,
John P [last name deleted for privacy by Editor]- Sweden
1999
Ed. note: This RFQ is outdated, but technical replies are welcome, and readers are encouraged to post their own RFQs. But no public commercial suggestions please ( huh? why?).
A. Is this a live enquiry? We still supply Zenith Cub.
Moz Copestake- Birmingham UK
May 23, 2014
Q. Are there any specifications out there for bright dipping copper and brass?
Bob R [last name deleted for privacy by Editor]plating shop - Elyria, Ohio
2004
A. Here we do Bright dipping of copper Terminals which are used in Automotive batteries.
The Process Flow is as below:
1. Cleaning : By means of Kerosene and Saw Dust
2. Rinse : Rinse the material by means of Raw Water
3. Solution Make Up: Ratio of 4:1:1 (4 Parts of DM Water : 1 Part of Nitric acid & 1 Part of sulfuric acid all are commercial grade chemicals). Dip in the same for few seconds as the copper will melt in the solution its just a surface preparation for the adhesion of PASSIVATION.
4: Rinse : Raw water Rinse Twice
5: Passivation : Yellow color as per you are requirement
6: Rinse : Raw Water Dipping once
7: Drying : any type of Dryer can be used
Regards,
- Chennai,Tamilnadu .INDIA
2005
RFQ: We manufacture microwave (RF) assemblies, filters, etc. for a range of industries. Many of these are manufactured in brass & copper. Prior to processing, i.e., silver soldering or soft soldering, plating, etc., the brass & copper components are "bright dipped". Following the assembly processes the assemblies are "chromate passivated". The chemical solutions currently used are as follows.
Bright dip part number CG-674,
35% w/v max Nitric acid
Hydrochloric acid 1%w/v max
Benzotriazole 0.5% w/v max
Chromate, part number CG-675,
60-70% water
20-30% sodium dichromate
Less than 10% sulfuric acid
(Please note the chemicals and quantities are detailed as they appear on the health and safety data sheets for the above products.)
Unfortunately the company supplying / manufacturing these products has been bought out and the lines dropped. Does anyone have any advice as to suitable replacements for these products re the chemical cleaning of brass & copper and the subsequent chromate passivation, are there now safer more user / environmentally friendly options ? If someone out there could point me in the right direction as to replacing these products I would be grateful. It may be worth noting that we have been offered the above ingredients, no problem, but I do not want, nor do I have the facilities, to be mixing these solutions in house.
Many thanks in advance.
Richard Mosley, Design & Production Engineer- Thornton Dale, North Yorkshire, England
2005
Ed. note: This RFQ is outdated, but technical replies are welcome, and readers are encouraged to post their own RFQs. But no public commercial suggestions please ( huh? why?).
A. Mr Mosley
It is unlikely health data sheets disclose the full monty.
There are good companies all over that make brass bright dips.
If you wish, we can send help -- some proverbial coals to Newcastle from Delhi.
Regards
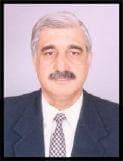
Asif Nurie [deceased] [deceased]
- New Delhi, India
With deep sadness we acknowledge the passing of Asif on Jan 24, 2016
Mr. Nurie
Thanks for your response however, I have now solved the problem. The 'recipe' from the data sheets is based on using concentrated acids. The solution I have at the moment has been made up, % volume, using commercial acids at around 60% concentration. Hence the reduced activity. With an accelerator the solution works fine.
I have indeed found numerous companies who produce bright dips but the newer products tend to run at elevated temperatures and have different effluent treatment requirements.
Again many thanks for your response.
Richard Mosley [returning]- UK
Hi Richard, glad you solved it.
Sometimes higher temperatures can help with waste issues. Back when I was with Lancy Laboratories doing metal finishing waste treatment systems, we would use sulfuric-peroxide as the bright dip and run the tank quite hot for high copper solubility, and slowly recirculate the mixture to a cooling chamber with a filter screen to catch and remove the copper sulphate crystals which would form as the solution cooled down.
Regards,
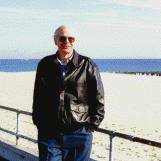
Ted Mooney, P.E.
Striving to live Aloha
finishing.com - Pine Beach, New Jersey
Q. Dear Richard Mosley
Do you mind to share your bright dip formula as we also have the same problem with copper bright dip?
Thairadiatech - Bangkok, Thailand
August 31, 2017
Q, A, or Comment on THIS thread -or- Start a NEW Thread