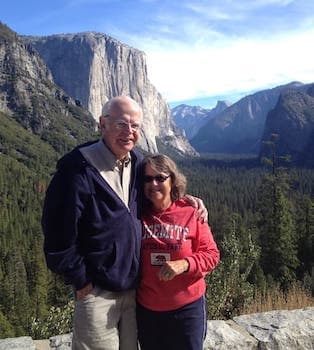
Curated with aloha by
Ted Mooney, P.E. RET
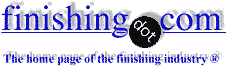
The authoritative public forum
for Metal Finishing 1989-2025
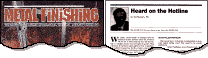
-----
Free and total acidity in phosphating

March 27, 2022
Respected readers,
I want some technical explanation on phosphating TA / FA ( why maintain it?),
Sludge formation calculation (square meter after dipping of mild steel), and
Zinc phosphating byproduct (ferric phosphate) effect after powder if sludge carry over on phosphated part and powder coating done as it is.
employee - Mumbai, Maharashtra, India
A. Hi Gautam.
1. We appended your posting to a thread which explains the meaning and effect of total acid to free acid ratio, and how to check it.
2. Sorry I'm not personally familiar with any formulas for calculating the amount of sludge formation, although minimizing sludge formation is obviously very important.
3. You cannot successfully powder coat on top of loosely adhering sludge.
As a general learning strategy for those new to phosphating (I don't know if you are or aren't), we have hundreds of threads about phosphating if you search the site with carefully selected topics of interest, but ...
Learning from a well written book where the author spent months or years arranging things in proper tutorial sequence will save countless hours compared to endless bouncing back and forth between stuff you don't yet have the background to understand and stuff you've already read a dozen times, but ...
Getting help from a reputable supplier of phosphatizing chemistry is the best approach. Today's better phosphatizing processes are quite complex, with various accelerators, inhibitors, and trace ingredients; and the technical data sheet from the supplier will tell you about the optimum FA/TA ratio, P ratio, etc. for the particular process.
Luck & Regards,
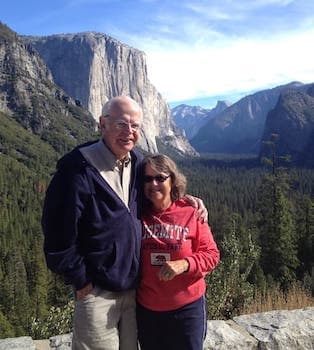
Ted Mooney, P.E. RET
Striving to live Aloha
finishing.com - Pine Beach, New Jersey
⇩ Related postings, oldest first ⇩
2007
Q. Hello,
Our pre-paint phosphating process is working at FA=6 points and TA=45 points
Can somebody tell me if these are good parameters?
The other problem is the short time resistance in salt spray test for parts that are
phosphated without oiling. the time is only 2 - 3 hours
How can I increase the resistance time? The pieces are made from metal and rubber (the rubber is sticked on the metal), I assume that some rubber components are dissolved in the phosphating bath at 72 °C and that's why the phosphating process is weak regarding anticorrosion properties
Also, please tell me if these values of acidity points are optimum for phosphating process:
FA = 6 points
TA = 45 points
thanks in advance
Tudor Silaghiindustrialist - Romania
2007
A. Without knowing the details of the phosphate that you are running it is impossible to tell you whether your operating parameters are sufficient.
What you need to let us know is what your pre-treatments are, the times, temperature and make up of your phosphate, whether it is proprietary or self-formulated and what coating weight you are aiming for plus if there are any post phosphate treatments such as a dichromate rinse.
I would not expect to get too long a life out of phosphate in salt spray, it is not designed as a corrosion resistant coating, but one that supports corrosion resistant coatings such as oils, preservatives and paints.
What I normally see quoted for unprotected phosphate salt spray resistance is one and a half hours when tested in accordance with ASTM B117.
Aerospace - Yeovil, Somerset, UK
2007
A. Dear Tudor Silaghi,
I do agree with Brian Terry that the phosphate coating is not expected to give a long life in salt spray test.
It is important to note that phosphate coating is only a pretreatment and not a finish. The corrosion resistance offered by phosphate coatings, when tested in accordance with ASTM B117, will be limited to only a few hours.
The free acid, total acid, free acid to total acid ratio and, the pH of the phosphating bath depend on the formulation and the type of surface to be coated. Excess free acid will lead to heavy metal dissolution and affect the conversion ratio.
I am not sure about the type of rubber material that you are using in your assembly and to what extent it can withstand in the phosphating bath at 72 °C.
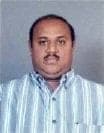
T.S.N. Sankara Narayanan
- Chennai, Tamilnadu, India
(ed.note: The good doctor offers a fascinating blog, "Advancement in Science" )
A. Two things come to mind: (1) 72 °C is not hot enough, (2) a ratio of 7.5/1 is good, however, that ratio must be determined freshly right at tank side when you are ready to put the work in the tank. You cannot titrate on Monday and phosphate on Tuesday, the free builds very fast in an empty solution. Take the burettes to the tank side, start heating, when you get to about 180 °F, titrate, adjust the T/F preferably with manganous carbonate (do not put that nasty sodium in the solution), by the time you do that the solution will be up to 195 °F, put the work in, and I do not like over 200 °F. But 72 °C (161 °F) is not hot enough.
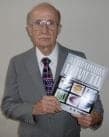
Robert H Probert
Robert H Probert Technical Services

Garner, North Carolina
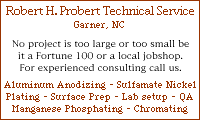
July 10, 2012
⇦ Tip: Readers want to learn from Your Situation 🙂
many readers skip abstract questions.
Q. Please tell me the role or work of toner, free acidity & total acidity in phosphating and their values, and effect if value decreases or increases.
Devi Dayal Yadavpaint shop - Rewari, Haryana, India
May 20, 2011
![]() |
! Hi, Devi. I don't know enough about this particular topic to be able to help you, but as the forum curator I've learned that you're most likely to get an enthusiastic response if you make an effort to frame your question in terms of what the responders have already said, and/or offer details of your own situation. Thanks! Regards, ![]() Ted Mooney, P.E. Striving to live Aloha finishing.com - Pine Beach, New Jersey |
Q. I am working with a five-stage alkaline cleaner for phosphating. Can someone help me with understanding the test methods for process control in terms of points? I am a professional engineer trained in water quality and I am used to working with mg/L rather than points. I am interested in the reagents for free and total alkalinity and free and total acid measurement in terms of points. I understand that the metal finishing industry uses points as controls. I know how to perform the test in terms of standard methods.
I am looking for the sample size, acid (H2SO4 or HCl) and base (NaOH) reagent concentrations in the methods to determine the concentrations in terms of points. I am using pH meter rather than indicators phenolphthalein, methyl orange
⇦ this on
eBay or
Amazon [affil links]
, bromthymol blue, etc...
Cordially,
- Roanoke, Virginia, US
May 14, 2012
July 12, 2012
Q. Good day.
I am running a proprietary manganese phosphate (Henkel Parco Lubrite 2) with specs at TOTAL ACID 11.5-12.5 points, FREE ACID) at 2.0-2.2 points and iron at 0.2-0.3%. 120 pounds/11 gallons of make-up will give total acid concentration.
My analysis is as follows;
Total acid= 2 mls, 100 mls DI, 4 drops phenol[phthalein], 0.1N NaOH
⇦ this on
eBay or
Amazon [affil links]
to pink = total acid points
Free acid= 2 mls, 100 mls DI, 3 drops methyl orange
⇦ this on
eBay or
Amazon [affil links]
/xylene cyanol to green= free acid points.
My TOTAL ACID is rising to 14 points (free acid at 2.0 points) and I wish to reduce, but all posted enquiries on this site refer to FREE ACID reduction with manganous carbonate (Letters 51028 and 26694) or slaked lime.
Henkel [representative] is of the opinion that the only way to reduce TOTAL ACID is to decant 15 % of soln. and adjust.
I think I should dump and make new.
Does anyone have any thoughts?
Salt spray at 1.5 hrs. with 0.3 g/l Cr3 is displaying a clean-rust free panel, coating weights at 32 g/m2.
To Robert Probert.
My question is how to reduce TOTAL ACID, as all writings are regarding FREE ACID reduction with manganous carbonate. I hope you can review and comment again.
Regards,
- Toronto, Canada
Q. I know the definition of free-acid and total-acid in terms of free hydrogen ion and total weak acid ion, but I would like to understand how to obtain this in "points". What are "points" and how do I get from a pH or a titration value to "points"?
Nick Fox- Pueblo, Colorado, USA
January 29, 2013
A. Hi.
I believe, in phosphating, when titrating for Total Acid (TA) and Free Acid (FA), the mls of the titrant (either 0.1N or 1N Sodium Hydroxide ) refers to the points. 1 ml of titrant = 1 point.
Good Luck.
- Penang, Malaysia
March 5, 2013
A. Hi Nick,
Not from pH, but from titration, you can measure free and total phosphate points. You use two different indicators so your "final point" cuts the titration in pH=9 (phenolphthalein
⇦ this on
eBay &
Amazon [affil links]
) or pH=4,5 ( bromophenol blue
⇦ this on
eBay or
Amazon [affil links]
). In the first one you titrate only free hydrogen (or phosphoric acid) and in the second one free hydrogen plus monobasic phosphate.
Hope I could clarify something! Regards,
- Cañuelas, Buenos Aires, Argentina
March 14, 2013
Q. Sir,
I am not good in chemistry, so I would like to know more about zinc Phosphating. We are preparing the solution by mixing 16 ltr of zinc phosphate solution with 200 ltr of water and heating the mixture; my question is:
1) what is the relation between free acidity and total acidity in that mixture?
2) what are the ranges of these levels and what are the additional steps taken for another titration?
student - India
March 20, 2016
A. Hi Vijith. You are a student and in the learning process, so it is important that we not mislead you. Practical and effective phosphatization requires more than zinc phosphate and water; and people usually buy their phosphatizing solutions from specialist formulators rather than trying to mix their own.
As a good experiment for you then, can we suggest that you attempt to determine the free acid and total acid in the mixture you have on hand, and then people can go deeper into this for you. Get the solution to 180-195 °F as Robert tells you, and perform the free acid and total acid titrations following Eric's or Daniel's instruction. If it is unclear to you how to do those titrations, please request clarification on the specific issues that are still unclear to you.
9th Edition, Vol. 5
"Surface Cleaning, Finishing & Coating"
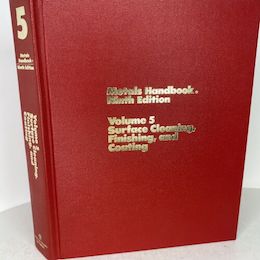
on AbeBooks
or eBay or
Amazon
(affil links)
If it's a bit of a struggle to clarify the vague areas, try your library for a book covering the subject. Biestek & Weber's "Conversion Coatings" or the ASM Metals Handbook Vol. 5.
have quite clear instructions.
Reading a chapter of a book, where the author has spent countless days working out exactly how to best present the subject in sequential, cogent, tutorial fashion is usually far less frustrating than surfing the web, drowning in a suffocating mix of snippets of stuff that you don't yet have the background to understand yet, thoroughly mixed in with stuff you've already read a dozen times. Biestek & Weber make it clear in minutes that dissolution of metal drives the precipitation of phosphate coatings, and the importance that free & total acid thus play in this. :-)
Luck & Regards,
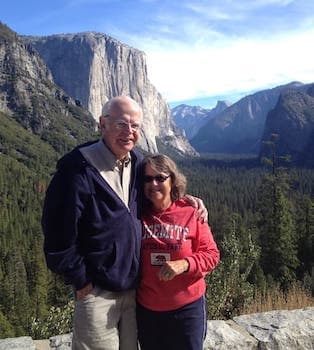
Ted Mooney, P.E. RET
Striving to live Aloha
finishing.com - Pine Beach, New Jersey
March 2016
Q. I am working with four tank process of iron phosphate. Please tell me the what/why are checks for total acid & free acid for iron phosphate tank or bath?
Describe the details free acid and total acid.
- Pune, Maharashtra India
March 20, 2018
by Biestek & Weber
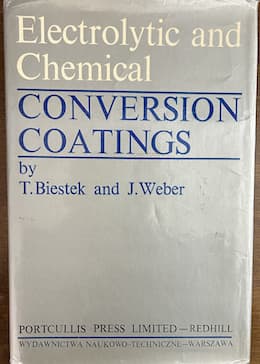
on AbeBooks
or Amazon
(affil links)
A. Hi Sarang. The "why" of free acid vs. total acid checks is ... (quoting Biestek & Weber)
"Primary divalent iron, zinc, and manganese phosphates are readily soluble, whereas secondary phosphates are insoluble in water, except for sparingly soluble zinc phosphate. Precipitation of these phosphates at the metal surface results in the formation of a coating insoluble in the medium"
I'm not implying that I fully understand the fine details of this reaction and the required balance of free vs. total acid -- only that the overall principle is that dissolution of a small amount of metal from the surface consumes acid, thus changing the balance and causing insoluble phosphates to form.
Regards,
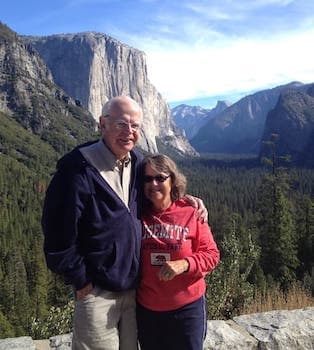
Ted Mooney, P.E. RET
Striving to live Aloha
finishing.com - Pine Beach, New Jersey
March 2018
Q, A, or Comment on THIS thread -or- Start a NEW Thread