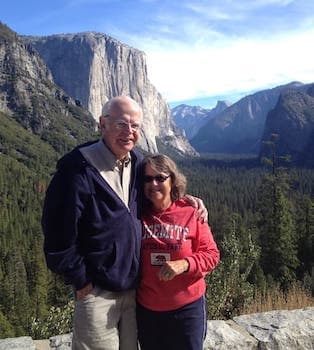
Curated with aloha by
Ted Mooney, P.E. RET
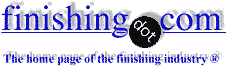
The authoritative public forum
for Metal Finishing 1989-2025
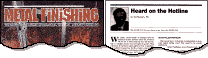
-----
Controlling Manganese Phosphate Coating Thickness
Q. I just became the engineer for our company's plating lines. We apply manganese phosphate coatings to a variety of parts, and I would like to gain better control of our coating thickness. We monitor total acid, free acid, acid ratio, and iron percentage in our coating baths. I see little-to-no correlation between any of these variables and our coating thickness. Aside from time and temperature in the baths, what other variables can be used to predict/control coating thickness? Thanks in advance for your help.
Michael CostelloPlating Engineer - Grand Junction, Colorado, USA
January 21, 2009
by Samuel Spring
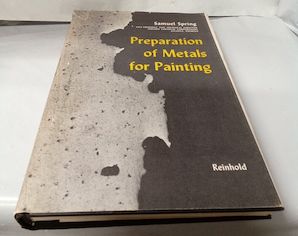
on eBay
(currently)
or AbeBooks
(rarely)
or Amazon
(rarely)
(affil links)
A. The bath chemistry. Most contain both accelerators and retardants which not only affect the rate of formation, they affect the structure. MnPhosphate is like a stack of needles. Some brands lay relatively horizontal in formation and some are nearly vertical. Dimensional measurement is significantly affected. Weight loss is the only true measure of the amount of phosphate in the coating, and measuring tools are the practical means of measuring coating "thickness".
James Watts- Navarre, Florida
January 23, 2009
A. It is necessary that you titrate for the total/free ratio just before you put the work in the tank, then if the free is too high, knock it down with manganous carbonate. When thru, let the solution cool as fast as possible, and never leave it sitting hot without a work load.
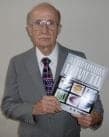
Robert H Probert
Robert H Probert Technical Services

Garner, North Carolina
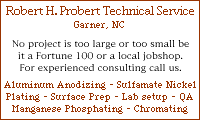
January 23, 2009
A. Dear Mr.Michael,
I have worked in Industries as a Research scientist depositing films on Automotive components and later on worked as a Lead Aerospace coating Engineer on Aerospace and Aeronautic Space Craft components. Your question is rather interesting provoking me to respond to you. Thickness of deposits is a function of time, current density, temperature and the concentration of the depositing species. pH of bath is one of the most sensitive variable factors determining thickness of electrodeposits that most people tend to neglect.
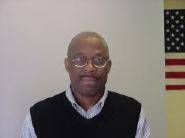
Bassey J. Udofot
Musgegon, Michigan
January 28, 2009
A. Michael, you do not have to control "current density" in an immersion process like manganese phosphate, there is no electrolysis to measure. Also, pH of a 200° F high acid manganese phosphate solution is not a factor. Start titrating the total and free when you get to 185° F; do it right at the tank side, by the time you have the T/F ratio you will be at 195° (which is hot enough). Knock out the free acid down to ratio with manganous carbonate, put the parts in, coat them. The industry talks in "coating weight" not in "thickness"; when finished, cool it down as fast as possible. Some of the compound suppliers say to use sodium carbonate ⇦ this on eBay or Amazon] to reduce the free acid; that will work, but makes more sludge which settles out on the shelves. By using manganous carbonate you are at least replenishing the manganese and making less sludge!
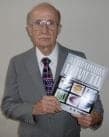
Robert H Probert
Robert H Probert Technical Services

Garner, North Carolina
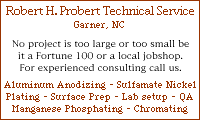
January 29, 2009
Q. Thank you all for your responses to my question. As a follow up for Mr. Probert, how cool is cool enough when the bath is not in use?
Mr. Udofot, for a manganese phosphate chemical conversion bath, what is the optimal operating range for the pH?
Thank you all again.
- Grand Junction, Colorado, USA
January 29, 2009
A. Bassey,
Manganese phosphate coatings are not electrolytic, they are immersion processes. pH is indeed critical in the reaction mechanisms of phosphate baths, but they are controlled normally by the free and total acid measurements and possibly by the iron content.
Thickness can be time dependent where a reaction does not go to completion (this is normally 5-15 minutes for most standard steels), otherwise the limiting factor is in the growth during the reaction phase.
Micheal,
There are so many factors that may affect your coating thickness as mentioned already; may I add just a couple of others:
Surface pre-treatment - if you use a process that roughens and increases the surface area this will increase your coating weight.
Grain refiners - this will create smaller crystals that compact more densely, increasing coating weight per unit area but reducing thickness.
Just thought I'd add those into the mix.
The usual way to check that you have a sufficient coating is to measure the coating weight. I would suggest you read MIL-DTL-16232 [from
DLA]
; it'll indicate how Military suppliers control their coatings.
Aerospace - Yeovil, Somersset, UK
April 18, 2009
Q. Dear All,
Please help, I need to know how to convert the following unit of measurement:
Zinc Phosphate 5 g/m2 is equal to how many micron?
Manganese Phosphate 1500 mg/ft2 is equal to how many micron?
Thank you in advance for your kind attention.
Regards,
Hary
Manufacturer - Indonesia
A. Conversion parameter is 0.7
x gr/m^2 * 0,7 = y micron
Example 6 gr/m^2 weight is equal about = 4.2 micron thickness
Regards,
Ilker,
Freelance - TURKEY
March 15, 2012
Q. Dear Mr Ilker,
Can you help me, where do you get this calculation - reference specification.
Thank you
Fasteners Manufacturing (Oil And Gas) - Johor Bahru,johor and Malaysia
October 17, 2016
Hi cousin Soul. The MIL specs don't discuss this conversion factor. Certainly it's just an empirical estimate derived from trying to measure the approximate thickness of these spikey, granular coatings, then stripping and re-weighing and comparing the weight loss to the estimated thickness. The more interesting question is why do you would want to know!
Are you trying for a precision fit and thus concerned about thickness, or has someone erroneously specified coating thickness instead of weight, or do your empirical results vary too far from this for comfort? People are drawn to answering questions only when they grab their interest, and an abstract discussion of conversion factors probably won't, but you may be confronting a potentially interesting issue that people would love to discuss.
Regards,
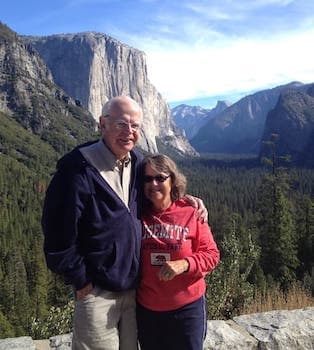
Ted Mooney, P.E. RET
Striving to live Aloha
finishing.com - Pine Beach, New Jersey
Q. I want to ask about zinc phosphate. Actually, exist or not thickness for phosphate? But, what I have been told, after phosphate process the parts will appear roughness -- right? Then, how we can measure the thickness (exact). This is quite confusing me. Thanks for any response.
NORA Azma- Johor bahru, Johor, Malaysia
November 8, 2013
A. Hi Nora. As you see, we appended your inquiry to a thread which answers it. You are correct that "thickness" is not the appropriate way to express the quantity of coating, for the reason you mentioned, so it is expressed in coating weight.
Regards,
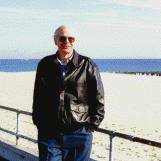
Ted Mooney, P.E.
Striving to live Aloha
finishing.com - Pine Beach, New Jersey
November 8, 2013
Magnesium Phosphating Crystals Are Too Big
Q. Actually I have done all the rinsing processes,
pickling,
activation and phosphating with the temperature maintained
-- but still am getting bigger crystals than normal.
Please help.
- uae
July 8, 2017
A. Carefully check the bath ratio. The balance of concentration (total acid) to activity (free acid) is critical to controlling the crystal size and maintaining uniformity. Consult your data sheets to get your optimum range and make adds accordingly.
Jameson Grout- Agawam, Massachusetts, USA
July 10, 2017
Q. How to reduce coating thickness in case of manganese phosphating? Our specification is 0.4 to 1.0 micron but we are getting about 3.0 micron.
Please help in this regards.
Walton Hi-Tech Industries Limited - Dhaka, Bangladesh.
October 24, 2017
A. Hello Kamrun,
Manganese phosphate tends to deposit more than 1 micron thickness (it's 1.3 g/m2). We could help you maybe if you give us more data:
- Which kind of materials you process.
- How is your process composed.
- Working parameters: TA, FA, accelerant, temperature, time...
Maybe with more data we can assist you out of this problem.
Regards!!
TEL - N FERRARIS - Cañuelas, Buenos Aires, Argentina
October 29, 2017
Q.
Dear Daniel Montañés, Thank you very much for your response.
Please find the data you inquired about:
01. Crank Shaft (Cast Iron -- EN GJL 250);
Piston (Sintered iron C<0.4%, S<0.3%, MnS<0.5%, others<1.5% & rest Fe);
Connecting Rod (Sinter iron C=0.3-0.6%, Cu=2.5-3.5%, S= 0.3-0.5%, Mn<0.08%, others<.5% & rest Fe).
02. Actually we are using commercial grade chemical from Chemital, India. The compositions are unknown to us (a mixture of manganese, nitric acid, phosphoric acid etc.)
03. TA : 33 - 37, FA : 3.6 - 4.6, Accelerant : sodium nitrite, Temperature : 92 - 96 °C, Time : 4 min.
Walton Hi-Tech Industries Limited - Dhaka, Bangladesh
A. Hi Kamrul,
You could try lowering a bit your concentration to lower both FA and TA, and trying to keep your FA high (a little higher is possible, as you can go as far as your TA/FA ratio is OK in your technical bulletin).
Thickness is given by three parameters:
Total Acid, Temperature and Time. You go higher in one of these three parameters, and you get more thickness. Lower one of these, and you get less thickness. You can play with these three and see if you get some results.
In the middle, you can expect: rough parts, uneven phosphate coating (if time is not enough to react evenly with the part or if TA/FA is too high), and not coated parts (if you went too far lowering something). I can't predict how it can go but the path is clearer now than before!
Hope you get to some good result! Keep us posted!
Best regards,
TEL - N FERRARIS - Cañuelas, Buenos Aires, Argentina
Q, A, or Comment on THIS thread -or- Start a NEW Thread