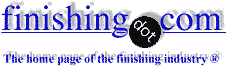
-----
Will hard anodized aluminum castings be corrosion resistant?
Q. We have a few products that have DI water and/or wet hydrogen running through them that are either 6061 or 6063 aluminum. We hard anodize to MIL-A-8625 / MIL-PRF-8625
[⇦ this spec on DLA], Type III, Class 1 to prevent both corrosion of the aluminum parts but more importantly to prevent the aluminum and its alloys from leaching into the DI water or wet hydrogen as contaminants.
We are planning to move to a cast aluminum manifold but I haven't been able to find much on anodizing cast aluminums. I have heard that Aluminum A356 is anodize-able but don't know how well and if there are any other grades that are.
Any assistance would be appreciated.
Manufacturing Engineer - Richmond, BC Canada
2007
2007
A. Anodized appearance of A356 is gray due to many Si inclusions and is rated 4 on a scale of 1 (best) to 5 (worst). Corrosion resistance is rated 2, very good.
Aluminum casting alloys rated excellent for both anodized appearance and corrosion resistance include the Al-Mg alloys 514.2, A514.2, 518.2, 520.2, 535.2 ['Almag 35'] and the Al-Zn alloy C712.1. From Casting Kaiser Aluminum
[on
Amazon affil links], 3rd Edn. (1973); some alloy designations have since changed a bit.
>From the Annual Book of ASTM Standards, vol. 02.02 (2001):
ASTM B26/B26M, 'Standard Specification for Aluminum-Alloy Sand Castings,' lists 514.0, 520.0 & 535.0 as excellent for anodizing and corrosion resistance.
ASTM B85, 'Standard Specification for Aluminum-Alloy Die Castings,' lists 518.0 as excellent for anodizing and corrosion resistance.
ASTM B108/B108M, 'Standard Specification for Aluminum-Alloy Permanent Mold Castings,' lists 513.0 and 535.0 as excellent for anodizing and corrosion resistance. Alloys 705.0, 707.0, 711.0 and 713.0 are excellent for anodizing and very good for corrosion resistance.
Note: the alloys best for anodizing and corrosion resistance are rather poor in castability.
- Goleta, California

Rest in peace, Ken. Thank you for your hard work which the finishing world, and we at finishing.com, continue to benefit from.
Q. Thanks for the response. In your 1 (best) to 5 (worst) scale, what is the criteria? I don't care about appearance at all. The purpose of anodizing is purely to protect the DI water that will be flowing through the manifold from pulling contaminating ions from the cast metal.
Avi Feinberg [returning]- Vancouver, BC, Canada
2007
Treatment &
Finishing of
Aluminium and
Its Alloys"
by Wernick, Pinner
& Sheasby
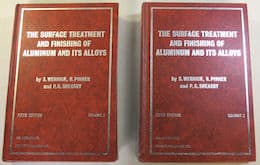
on eBay or Amazon
or AbeBooks
(affil link)
A. The Surface Finishing and Treatment of Aluminum and Its Alloys, 6th Edn., page 432.
gives a chart with additional anodizing characteristics for BS 1490 cast alloys. Ratings are E (excellent), VG (very good), G (good), M (moderate), "U" (unsuitable). No cast alloy is rated E in any category.
Alloy LM25 (~356A) is rated G for protective anodizing, M* for dyed appearance, "U" for bright anodizing. *dark colors only.
Alloy LM5 (~514.0), is rated VG, VG and G.
The only other casting alloys in this table having VG ratings for protective anodizing are 99.5% Al and LM10 (~520.0), both probably less popular with the foundries than LM5 (514.0). Also, LM10 must be fairly homogeneous for good anodizing; a bit difficult with 10% Mg!
Anodize appearance correlates fairly well with corrosion protective. The anodizing on A356 is dark due to many Si inclusions which disrupt the continuity and hence protective value of the anodizing. Use another alloy such as 514.0.
- Goleta, California

Rest in peace, Ken. Thank you for your hard work which the finishing world, and we at finishing.com, continue to benefit from.
2007
Ken,
Thank you for your responses. Much appreciated.
- Vancouver, BC, Canada
2007
356-T6 Sand Casting Anodizing Issues
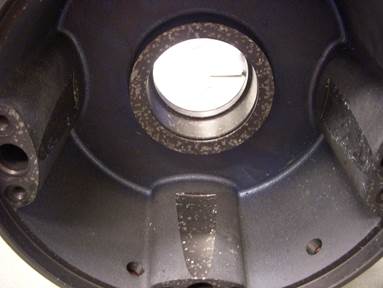
Q. 356-T6 Castings continually shows signs of non-conformance related to blooming & pitting. Is there a specification for the casting, cleaning or plating processes I should refer our vendors to in order to achieve a specific quality part?
Josh HolmerQuality Manager - Westlake, Ohio
May 8, 2017
Ed. note: This RFQ is outdated, but technical replies are welcome, and readers are encouraged to post their own RFQs. But no public commercial suggestions please ( huh? why?).
A. Hi Josh,
Anodising castings can be a real pain in the proverbial! The casting more than likely will have a level of porosity, which is the probable source of your problem.
A couple of things you can do to mitigate the problem are Hot Isostatic Pressing (HIP) and/or impregnation, normally with either sodium metasilicate
⇦ on
eBay
or
Amazon [affil links]
or a resin (designed to fill up the holes from porosity). If the porosity is bad even these techniques will not help and you will need to look at how to reduce the porosity during manufacture of the castings.
After anodising I would strongly recommend that you go through alternate hot and cold rinses, at least two cycles, but three, four or even five are no unheard of for really poor castings. This is to try and remove residual sulfuric acid from the pores, which is more than likely the cause of your blooming.
Aerospace - Yeovil, Somerset, UK
May 10, 2017
Q, A, or Comment on THIS thread -or- Start a NEW Thread