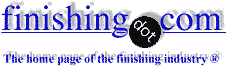
-----
Electroless nickel plating is tarnishing, turning black

Q. Parts are 6061, machined, then electroless nickel plated. We are getting discoloration and "black stains" regularly on a few parts from each lot, but not on all of the parts.
These parts look good when they leave our warehouse but a couple weeks later when they get through our customers' quality they are being flagged. The "black stains" can be wiped/polished away. Any idea what is causing these "black stains"?
- Harrisburg, Pennsylvania
April 28, 2022
⇩ Related postings, oldest first ⇩
1995
Q. We've run into a bit of a problem of nickel discoloration on some heatsinks. We build Mil-Spec high reliability computers. In one case the modules has electroless nickel on copper heatsinks. The heatsink looks vaguely like a ladder and is bonded to FR-4 multilayer circuit board (printed wiring board, or PWB). Chips straddle the rungs and are bonded down with epoxy and are soldered into the PWB using RMA rosin flux and a wave solder machine.
We installed a semi-aqueous PWB cleaning system and the heatsinks are coming out with black water spots (well, that's a bit over stated, there are water spot shaped areas ranging from clear tan to blackish). We're desperate to find out what's causing the discoloration and more importantly, how to avoid it. (Discoloration of nickel plating does not meet Mil-Spec) The cleaning process is a batch process with 4 sumps and a drying bay. The first sump is Axarel 46, a DuPont devised, now Petroferm sold hydrocarbon mixture (aliphatic hydrocarbon with dibasic esters: isobutyl glutarate, adipate, succinate and surfactant) - temperature 120 F, ~10-20 minute immersion, immersion spray agitation The second sump is an emulsion of DI water and Axarel - temperature 140 F, 5 minute immersion, immersion spray agitation Third and fourth sumps are DI water, 140 F, 5 minute immersion in each, immersion spray agitation. Final sump is hot air, 190 F, the rack is in the bay for 6 minutes, there is a slit nozzle at the top of the bay to act as hot air knife to blow surface water off. Naturally the problem is mainly showing up on product, not test coupons.
We did reproduce a mild case of the discoloration after taking a chunk of heatsink, bonding it to a PWB, putting epoxy tape on it, fluxing it, running it through the wave solder and then cleaning it. The discoloration appears to occur in the last spots water is standing after coming out of the final rinse before drying. We also tried cleaning a section of heatsink as-received, and after bonding to a PWB. Neither had appreciable discoloration. We sent the as-received and discolored heatsink section out for ESCA analysis of both discolored and non-discolored areas.
The as-received was dirtiest- ~2% Ni at the surface, 80% C, 10% O, smattering of Cu, Pb, Sn, P. Unstained area on stained heatsink - 20% Ni, 56% C, smattering of Cu, Pb, P. Stained area on stained heatsink - 18% Ni, 61 %C, smattering of Cu, Pb, P 40 Angstroms down ESCA shows as-received - 20% Ni, 60%C, smattering of Cu, Pb, P Unstained area - 70% Ni, 20%C, 7%P Stained area - 65% Ni, 25%C, 9%P Visually at 200X the stained area has a transparent brown tint versus the silver surface elsewhere. There are iridescent spots visible over all the surface, perhaps tending to slightly larger spots in the darker areas. (Possibly residual hydrocarbon? - it does have a boiling point of 350 F)
Anyone have thoughts as to what it is, how better to identify it, or how to prevent forming it? We got a suggestion that electroless typically would have an inhibitor applied to prevent discoloration, is this common? Would the cleaning process remove this?
Steven Axdal- Bloomington Minnesota
A. If your electroless nickel has 80% carbon on the surface when you receive it, I believe that is the problem. I don't think there should be any post treatment on the electroless nickel. It is not needed, I doubt you asked for it, and that is not MilSpec.
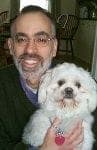

Tom Pullizzi
Falls Township, Pennsylvania
1995
Electroless nickel tarnished with rainbow colors during heat treatment
Hill-Cross Company [a finishing.com supporting advertiser]
Q. I am an electroplating jobber in Penang, Malaysia. My company provide gold, silver, palladium-nickel, tin, tin-lead and electroless nickel (EN) plating to the electronic and electrical industries.
I had lately doing some EN coating jobber that require heat treatment, the job pieces tarnished with rainbow colors in the heating chamber. What caused this? Could you share some experience with me?
After the EN coating we passivate the surface with dilute chromic acid. Then heated in nitrogen gas purging oven with the following profile:
Soak at 750 °F for 75 minutes.
60 minutes to cool down to 140 °F. Remove from oven.
Thank you and best regards,
Keat-Seng Ong- Malaysia
A. Rinsing before bake must be thorough. Consider using D.I. water.
Richard Painter- Cleveland, Ohio
1998
A. I agree with the better rinsing. Also, is the 750 °F necessary? What are you trying to achieve, higher hardness?
Robert Sachs- Canada
2003
Q. I'm putting an electroless nickel finish (approx. .0004" thick) on a machined Aluminum (6061-T6) part that is then glass bead blasted (240 grit) prior to plating. The matte finish is very attractive and consistent but highly vulnerable to tarnishing from handling (hand/finger sweat). Is there any way to alleviate this problem? What is the most effective cleaner to remove the tarnish (preferable a cloth type)?
Thank you,
Duncan Mackay- Palo Alto, California, USA
2003
A. Most chemical supply houses can offer an anti-tarnish post-dip for electroless nickel. Technic, for example, offers their Tarniban series of post-dips.
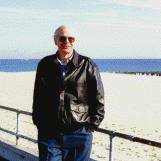
Ted Mooney, P.E.
Striving to live Aloha
finishing.com - Pine Beach, New Jersey
2003
Multiple threads merged: please forgive chronology errors and repetition 🙂
Q. Is it possible to Alodine an electroless nickel plated part (aluminum base metal)? I'm assuming the Alodine finish would lessen finger printing of the nickel and would make these unsightly marks easy to remove, probably with a damp cloth? If this is all feasible then how long should the part be submerged in the chromate solution for the best result?
Thank you.
Duncan Mackay- Palo Alto, California, USA
2003
A. Anti-tarnish compounds are indeed often applied to electroless nickel, and the composition of those chemicals might be rather similar to the composition of Alodine, which is a trade name of Henkel Surface Technology for chemical processes used in the chromate conversion coating of aluminum. But I doubt that Henkel sanctions this process being used for that purpose, and it is not good QA practice to use non-documented processes. Instead, ask them or one of your other vendors for a anti-tarnish topcoat for electroless nickel.
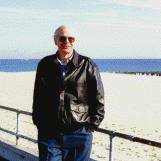
Ted Mooney, P.E.
Striving to live Aloha
finishing.com - Pine Beach, New Jersey
2003
2004
Q. Electroless Nickel Plating on Aluminium turns black with Phosphate buffer. We tested Nickel plated aluminium with Phosphate Buffer After one day nickel plating turns dark brown/ black, which cannot be removed by water. Nickel coating is around 10 um, phosphor content 8 to 10 %
Questions: ( I am mechanical engineer, not a chemist)
- is this corrosion?
- can we clean off the black deposition? with what?
- what can we do to make the coating to resist phosphate buffer (and still be electrically conductive)
- thicker coating?
-other nickel content?
- any other thin coating for aluminium, which is conductive and resists phosphate buffer?
- anything else?
Any info appreciated
Stephan SattlerMedical Instruments design - Starnberg, Bavaria, Germany
A. The black discoloration is a passivation film that forms on EN coatings in some environments. It is a nickel/phosphorus/oxide that cannot be removed chemically. It can be removed by abrasion. It is a form of corrosion.
Thickness or phosphorus content will have little effect. Try either electroplated nickel or a low phosphorus EN (2-4%P).
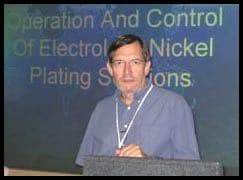
Ron Duncan [deceased]
- LaVergne, Tennessee
It is our sad duty to note Ron's passing on Dec. 15, 2006. A brief obituary opens Episode 13 of our Podcast.
2005
Sir,
We own a plating shop of Electroless Nickel plating process. We use SS 304 tank with bottom heater to heat the plating bath. At the end of 2.5 turnover of the bath life we get black colouration on components if we plate in it. But if we try with same bath solution in a glass beaker [beakers on eBay or Amazon [affil links] /plastic vat we don't get black colour on components that are plated. We passivated the tank(SS) and we even filtered the solution with activated carbon and tried plating in SS tank. But still the problem persists. We used a new plating solution in the same tank . We find no black colouration of components occurs.
Please give us a correct solution.
Nirupama Balasubramanian- Chennai, Tamilnadu, India
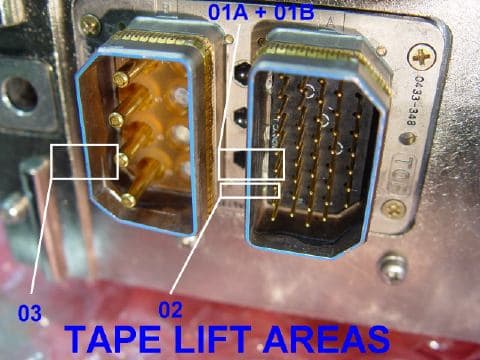
Q. We have been using an electroless nickel plated (0.2 mils) aluminum electrical connector for a number of years on a power supply. Our supplier solders wires to it, uses some RTV to hold some of the wires, fills the Tin plated, cold rolled steel box with a heat-activated epoxy and alumina, mechanically attaches the connector to the box, without sealing around it, and heats the box to 80 °C for 4-6 hours. After a few years we are noticing a black "tarnish" that seems to have "creeped" up the walls of the inside of the connector - not all the way. We also see some "white" deposits at the bottom of the connector. We are seeing: Ni, Zn, S, K, Ti, Al in these areas; none of these elements are in the epoxies. Also of note, the customer exposed the power supply to 130C coolant while not operating for two hours. Does anyone have an idea what could be happening? Our customer is concerned about long term corrosion and products of conducting material falling off.
Geoffrey M SmithPower Supply Design Engineer - Baltimore, Maryland, USA
2007
A. 0.0002 inches of electroless nickel is not thick enough to close all pores in the aluminum device. Corrosion cells start at pores and accelerate by electrochemical cells due to dissimilar metals in contact with the EN plate. A chromate passivation can be useful, but not always effective if the pores are open and the voltage generated by the couple. Don
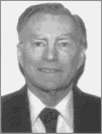
Don Baudrand
Consultant - Poulsbo, Washington
(Don is co-author of "Plating on Plastics" [on Amazon or AbeBooks affil links]
and "Plating ABS Plastics" [on Amazon or eBay or AbeBooks affil links])
2007
A. It's hard for me to see the black tarnish in your photo but we've experienced something similar to what you describe. Our connectors are also electroless nickel plated, however they are made from composite (plastic) base material. They're Class M, 38999 series III circular connectors. Our tarnish ranges from "tea stain" to very dark, opaque black; as if the parts were pulled out of a fire, sometimes accompanied with very small amounts of white powder down in the recesses of the connectors.
We've been able to associate the tarnish with a latex masking operation performed by our Parylene conformal coating vendor. The vendor had been using an ammoniated latex for masking the connector contacts and other mating surfaces. They may also have been speeding the processing time by oven baking or applying the ammoniated latex into connectors fresh out of a drying oven. In any case the tarnish corresponds to the exact locations of the masking. We've asked the vendor to use a non-ammoniated latex in the future, but due to lack of sales on this product, we haven't been able to test this out and ensure this is the cure.
The bulk of the tarnish is removable with rubber eraser abrasion but a "tea stain" appearance remains.
Are your connectors part of a circuit card assembly that is masked for conformal coat?
Does anyone know of a reaction that occurs between nickel and ammonia
⇦ on
eBay or
Amazon [affil links] or some other constituent of latex rubber?
Avionics Manufacturing - Seattle, Washington, US
2007
Q. My company plates a variety of materials with mid-phos electroless nickel. Recently, we have seen some discoloration form as the plated material ages in the form of a black tarnish that retains some of the shine on our copper alloy parts. The parts are rinsed in hot DI water post plate, as all our nickel plated parts are, and none of the other plated parts have shown this malady. Other than surface contamination and reaction in post plating processes, what would cause this to occur (what type of contamination)?
Allen ClaguePlating manager - Waynesboro, Virginia
2007
by Sha, Wu, & Keong
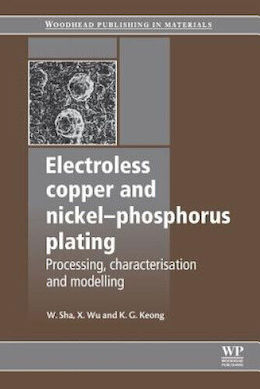
on eBay or Amazon
or AbeBooks
(affil link)
by Sha, Wu, & Keong
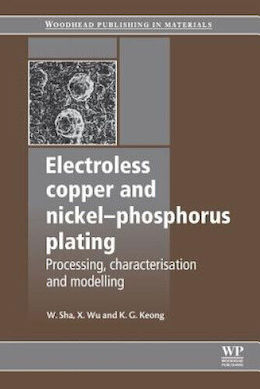
on eBay or Amazon
or AbeBooks
(affil link)
A. Not enough information. The coating may be too thin, the EN solution may have high impurity content, the environment may be too severe (sulfurous?).
The corrosion/tarnish resistance of EN can be improved by 15-60 minutes immersion in a warm (50 °C), 1% chromic acid solution -- US Patent 3,088,846 (1963).
- Goleta, California

Rest in peace, Ken. Thank you for your hard work which the finishing world, and we at finishing.com, continue to benefit from.
A. It sounds like something is bleeding thru.
Question 1: Are they all the same alloy that is being plated?
Question 2: Are you positive that the EN thickness is the same on all parts? sounds like it is thin on the bad parts.
- Navarre, Florida
2007
A. Have you checked with your EN supplier? Sounds to me that someone is using too much over the tank side stabilizer or brightener. These products typically contain divalent sulfur compounds that are known to turn dark and stain EN deposits. Again, see your EN supplier!
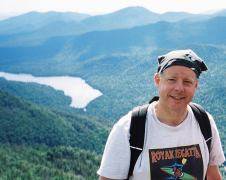
Milt Stevenson, Jr.
Syracuse, New York
2007
A. I believe Milt is correct, Stabilizer is probably the cause.
I'll go out on a limb and predict it is of the home brew nature.
Warren, Michigan, USA
2007
A. Too bad I didn't see this post sooner. If that happens again, check your EN solution for NO3- using a test strip. I had that same problem up in Boston and traced it back to nitrates that were being dragged in from the bright-dip bath. We had to add another rinse step before EN submersion and it worked out fine.
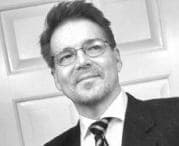
Randall Fowler - Fowler Industrial Plating, LLC
Cleveland, Tennessee, USA
January 3, 2008
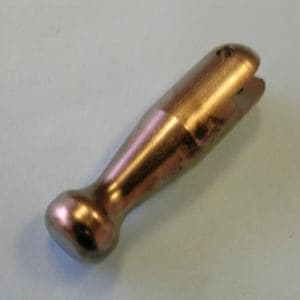
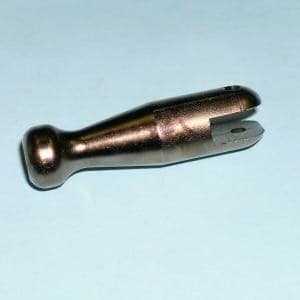
Tarnish of electroless nickel over brass or alum. when ultrasonic aqueous cleaning
We have thousands of parts Electroless Nickel plated and often they look fine before cleaning in a multi-stage ultrasonic cleaner. However, after processing in the ultrasonic cleaner (two stages of ultrasonics, one rinse, one dry --cleaner is Blue Wave Detergent #25-I, 4 parts purified (Seattle city water through filters) deionized water to 1 part liquid detergent). Many of the parts come out with brownish to blackish spots of irregular shapes. They kind of look like the variation you would get with water spots. Strangely, if we don't turn on the ultrasonics, we don't have this staining issue (though we have to soak them longer to get fingerprints, etc. off of them). We are trying to get them clean for oxygen service. The brownish/blackish spots can be buffed off but that is labor intense and thins the surface.
Ed Huncovsky- Kirkland, Washington
May 7, 2009
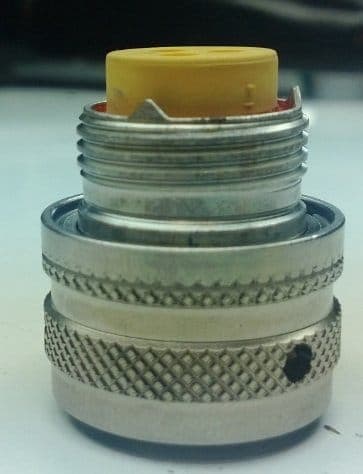
Black patches on Nickel plated aluminium parts
Q. Hi,
We are facing black patches in High Phosphorous nickel plating on Aluminium parts.
We do plating twice, first time 25 to 30 micron electroless nickel, then Copper band soldering, then electrolytic nickel plating 3 to 5 microns.
What would be the root cause for this. Please help.
Quality analyst - Bangalore, Karnataka, India
May 21, 2014
Q. A medium phosphorous electroless nickel plated 17-4 PH stainless steel part on one of our handheld devices becomes tarnished very quickly. It is mainly a aesthetic problem but we would like to prevent this from happening.
Are there alternative finishes that look similar to electroless nickel that do not develop this problem or are there other options out there to prevent the electroless nickel finish to tarnish?
- Phoenix, Arizona, USA
January 18, 2017
Ed. note: This RFQ is outdated, but technical replies are welcome, and readers are encouraged to post their own RFQs. But no public commercial suggestions please ( huh? why?).
A. Hi Dominik. Nickel-chrome plating would not tarnish, but it's hard to suggest what finishes would be appropriate without knowing anything else about the application. There may be a very good reason that electroless nickel is used instead of nickel-chrome plating.
It's fairly common to apply chromate-based tarnish preventers (Tarniban, for example) to electroless nickel plated components, but this is becoming less environmentally accepted; and without knowing what this handheld device is, it's hard to say whether it would be problematic from a human exposure perspective.
Regards,
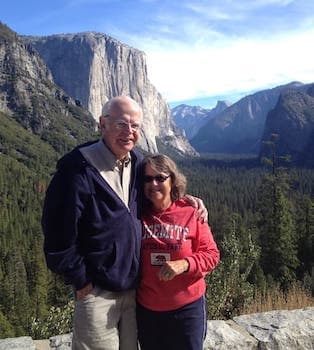
Ted Mooney, P.E. RET
Striving to live Aloha
finishing.com - Pine Beach, New Jersey
January 2017
February 6, 2017
A. Hi Dominik,
I've used anti-tarnish post-treatment dips on silver but I don't have experience using the dip on EN therefore I would recommend a 2-part PU clear coat.
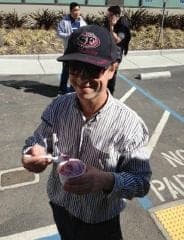
Blake Kneedler
Feather Hollow Eng. - Stockton, California
Ground electroless nickel plating is turning black
Q. Hello Sir/Madam,
I am from India. Past 2-1/2 years I am working in Electroless Nickel Plating Shop. Here we use PMD chemicals.
After Completion of Electroless Nickel Plating (40 - 45 µm) and heat treatment (400 °C at 1 hour), after cooling, I moved the finished job to Grinding section; they cut half of the plating from the job (20 - 22 µm). Then the job moved to Packing; they packed immediately and moved to the Customer. My customer uses this part at any time. Sometimes they store my job in stores and use after 5 or 6 months*.
I received a complaint from customer "your job is fully black and I cannot accept this lot". Actually my final job is Fully silver white colour. How did this Job Change into Black? Please Help and give some suggestions to avoid this problem in future.
Arul MuruganPlating Company - Chennai, Tamil Nadu, India
March 30, 2017
----
Ed. note: * -- Because this posting is about inadvertent blackening of electroless nickel, we moved it to this thread. Arul originally posted under the topic "Electroless nickel plating on cast iron parts", so we assume his parts are cast iron.
EN Staining Issues Niklad 847 Mid-phos chemistry
August 16, 2017Q. Hello all,
Before I get into asking questions, I would first like to thank Finishing.com for being the resource it has been to me thus far. As a 26 year old just getting my feet wet in the world of metal finishing, I have to say that you guys have been a huge help from day one. With just at 1 full year of experience, I am realizing quickly how much depth there is to metal finishing. With that being said, I would like to also mention that I've primarily been working with chromate conversion coatings (III and VI) as well as NDT (FPI/etch and MPI).
Although I've worked around EN almost everyday, supporting my shops platers with tank adds and titrations, etc., I find that questions I often have don't seem to be as easily answered as I would think. I've recently started learning how to plate aluminum components and have what I feel is a pretty good understanding of the pretreatment process -- zincating and what not -- but when it comes to the EN bath itself and troubleshooting issues, I am a little overwhelmed.
Trying to transfer "best practice" processing techniques that I picked up learning conversion coatings doesn't seem to always be "best practice" with EN (thorough and CLEAN rinsing, precise timing in baths for repeatability, accurate bath management, drying, etc. ), which leads to a question I have that is driving me crazy ...
Has anyone used MacDermid Enthone's Niklad 847 midphos EN? We were using the 807 Niklad before I started plating and recently switched. Of all the ideas I have had about my particular issue, the actual chemistry is the only thing I can think of that is potentially causing problems. The issue is the presence of light brown, to almost black staining on the surface of the freshly plated aluminum parts as they are coming out of the EN bath. I've tried everything I know how to do to alleviate this, but have had no luck and have not been able to find a solid answer as to why this is happening.
As far as technique is concerned, the bath is well under the maximum amount of metal turns so zincate contamination and other particulates are pretty much out of the question. We run the bath constantly through 2x 1-micron filter bags. The bath was made new today after the tank was passivated overnight. I flushed with RO water and made sure there was nothing in the tank whatsoever before preparing a fresh bath. When I plated the parts, the rate was consistent and timing was dead on for .0006" of thickness. I rinsed thoroughly with RO coming out of the bath, and went into a brand new RO dead rinse. Agitated the rack of parts manually, very vigorously. The rack is freshly coated. No bare areas or anything for solution from anywhere to be trapped. I hose rinsed out of the dead rinse (RO) and went into a fresh, heavily agitated RO counterflow rinse for a ridiculous 5 minutes. I hose rinsed with RO coming out of the counterflow and finished in a hot RO rinse (150 °F) before a quick air hosing and into a 170 °F dryer.
Sure enough the parts were stained. The parts themselves have threaded holes that I solvent cleaned and dried prior to masking with silicon plugs that fit quite snug. Bleedout from acid seems a little extreme to me. Especially since there are no bare areas or blisters around the plugs. The parts are only about 2 inches by inches, very light, threaded holes very small. It just doesn't seem likely that bleedout would occur in a way that would make this happen so consistently. I agitate parts in pretreatment rinses 3-5 minutes usually. I focus my hose rinsing on these areas as well. I feel like any small amount of potential bleedout should be mitigated by the cleaning and pH of the EN bath and the rinsing that follows it.
I can't even find the 847 solution on the Enthone website or internet period. I assure everyone this is definitely a MacDermid EN chemistry. DI water for rinsing is out of the question unfortunately. Does anyone have any insight or suggestions? Any advice would be much appreciated. Thanks!
Brandon MascoeMetal Finishing shop processing technician - Indianapolis
A. Hello Brandon,
Can you confirm if the stains are appearing out of the EN process tank or out the first rinse tank? Secondly, is it only this specific part that is staining? Are the stains coming from the holes, in recessed areas, or on the face of the parts?
My gut reaction is you have some nitrate contamination. Flushing the tank with RO after a passivation is not usually enough. I'd reach out to your vendor for recommendation tank stripping practices. They'll probably recommend flushing the tank, and then neutralizing the tank with dilute ammonium hydroxide, and then flushing two or three more times with clean water. Make sure you're running these solutions through the pumps. I would recommend buying some nitrate test strips and dunking one in your makeup water before adding your makeup components. It does not take a lot of nitrates to cause black streaks on part.
Side note: long, thorough rinses are great in most process lines but not so much with EN over aluminum. The extra pretreatment steps are there to keep oxides off the surface before the EN tank, and five minutes in a rinse tank will undo those efforts. The spray hose is good for the blind holes, but be cautious of rinse times over a minute between pretreatment process tanks
- Springfield, Massachusetts USA
August 17, 2017
A. I AGREE WITH JAMESON, STAIN COULD BE NITRATE CONTAMINATION
YOU CAN CHECK NITRATE PPM BY DIP THE STRIP.THE NITRATE PAPAER STRIP AVAILABLE VWR,COLE PARMER OR KOCOUR COMPANY.
TRY TO FIND OUT NITRATE PPM CONTAMINATION. GOOD LUCK.
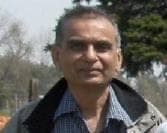
Popatbhai B. Patel
electroplating consultant - Roseville, Michigan
September 14, 2017
Electroless nickel bright dip / anti-tarnish
Q. We're microphone manufacturers. We use medium phosphorus electroless nickel plating on many parts for decorative/anticorrosion reasons because it plates well in holes and other details.
What I want to insure is that the finish stays bright and untarnished, particularly since the microphones are handled a lot.
I have heard of a post plate trisodium phosphate
⇦ on
eBay
or
Amazon [affil links]
dip but can find no details of the chemistry. Does this form a conversion coating?
Also is there a bright dip for removing darkening or tarnish from electroless nickel?
Thanks in advance.
Chief Engineer - Tiger,Georgia, USA
August 17, 2017
October 10, 2017
A. EN is getting tarnish/yellowing just like electrolytic Nickel.
That is why bright Nickel is coated with chromium.
The nickel and EN are oxidized with time.
The best proprietary process is an electrolytic process in a diluted chromic solution.
IT IS NOT A CHROMIUM COATING,
IT DOES NOT CREATE A CHROMIUM LAYER.
Yet it protects the EN from oxidizing and getting yellowish.
Ask your supplier.


Sara Michaeli
Tel-Aviv-Yafo, Israel
• Please see also thread 42907, "Black/Brown stains on electroless nickel plating"
Q, A, or Comment on THIS thread -or- Start a NEW Thread