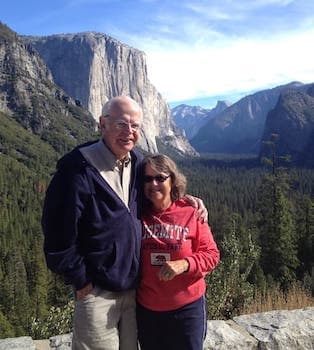
Curated with aloha by
Ted Mooney, P.E. RET
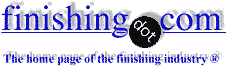
The authoritative public forum
for Metal Finishing 1989-2025
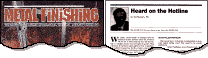
-----
Passivating Tank is Deteriorating
2007
Hi Everyone,
I'm having problems with the moving parts of the passivation tank.
They are deteriorating.
It is said to be 316SS. The manufacturer is saying that it is probably the our nitric acid is too corrosive. I am using 65-69% technical grade. The tank is @ 20-25% Nitric, 2-3% Sodium Dichromate at a temperature of 120-130 degrees F. I test my tanks regularly for concentrations.
They used a patch test to check the grade of Stainless Steel.
Our tank is pretty new (4 months).
Does anyone have any thoughts or comments? I need help. We are down more than we've been running.
Thanks in advance,
finishing company - Rincon, Ga, USA
Ed. note: See also Micheline's letter 45955 which is basically the same subject in different words and may help clarify the inquiry.
Your problem is the sodium, Stainless hates it. Try using potassium dichromate instead.
Kurt Sammons- Inman, South Carolina
2007
Kurt may be correct, Micheline, but you may also want to take a look at our FAQ on passivation. Thanks, Kurt.
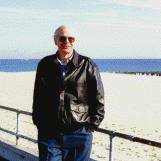
Ted Mooney, P.E.
Striving to live Aloha
finishing.com - Pine Beach, New Jersey
2007
Hi Kurt and Ted,
It's not an option for me to change, I am following AMS2700 Type
2.
Thanks,
Michy
finishing company - Rincon, Ga, USA
2007
If it is only the moving parts that are failing and not the tank, I don't really have any advice for you other than what you are already investigating. Sorry.
But if the tank is failing also, it's at or near the welds, right? If so, I'd think that your tank is suffering from chromium depletion. You should be able to read quite a bit about this with a google search. It can be avoided I believe if you specify 316L SS instead of 316, and also ensure that the tank weld area is properly passivated after welding. If chromium depletion is your problem, you might as well start over. If you want a long-lasting solution, you should go ahead and add a rigid CPVC liner or a suitable PVC-based flexible liner. I prefer the rigid CPVC, but some people like flexible liners.
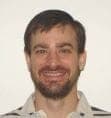
Jon Barrows, MSF, EHSSC
Independence, Missouri
2007
2007
Hi,
Can anyone give me an opinion on a patch test for Stainless Steel. How accurate?
Thanks,
finishing company - Rincon, Ga, USA
2007
Not fast enough or accurate enough for the situation :-(
I'd suggest calling scrap metal dealers and see if one can come in under contract with a handheld alloy sorter / scrap sorter ⇦ this on eBay or Amazon [affil links] XRF machine. It will almost instantly identify the various construction materials.
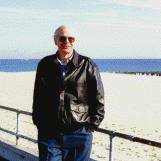
Ted Mooney, P.E.
Striving to live Aloha
finishing.com - Pine Beach, New Jersey
2007
Hi Jon Barrows
I like your comment about chrome depletion ... Please have a gander at # 19760.
The welding of some plastics, ie. PVC calls for quite a bit of experience.... top thermoplastic welders will hit over 85% of tensile, one guy, a Swiss, hit the magic figure of 100% ... this was corroborated in a German magazine but is extremely rare.
With 3l6L, one assumes that you get an overheat and that causes 'depletion'. If this can occur in a Nimonic where the Mo 'disappeared' during a weld test, one can well
imagine what happens to ordinary 'cheap' 3l6L.
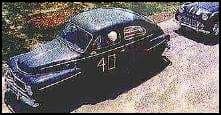
Freeman Newton [deceased]
(It is our sad duty to advise that Freeman passed away
April 21, 2012. R.I.P. old friend).
Thanks,
At closer inspection I noticed that the tank is deteriorating.
finishing company - Rincon, Ga, USA
2007
Q. Hello to all. I work in a shop that has a AMS2700 Method 1 Type 2 Nitric/Dichromate passivation bath. Unfortunately, after countless attempts to solve the issue, I can't seem to get the solution to stop attacking the tank. The tank is 316 stainless, and it develops brown rust and pits within 2 weeks of startup. The solution turns from dark orange to brown/orange to black. The solution is maintained at 20-25% by vol 42 Be Nitric Acid, with 2-3% by weight Sodium Dichromate Dihydrate. I have a teflon heater installed, maintaining 120 - 130 degrees F. I have checked out, and eliminated the usual suspects, including dirty parts, chlorides, and oils/greases. The water supply is from a DI line that services all our other processing tanks, maintained at less than 20 microsiemens/cm. And I even tried switching to an alternative DI line, from another area in the shop, that is even cleaner. After dumping, we acid pickle, and electroclean the tank back to shiny steel. My question is... Could fumes from a Sulfuric Anodizing tank next to the passivation tank be causing this problem, or should I look elsewhere? Thanks for your time and responses.
JT HettenhouserLab / Plating Technician - Park City, Utah, USA
May 3, 2012
Q, A, or Comment on THIS thread -or- Start a NEW Thread