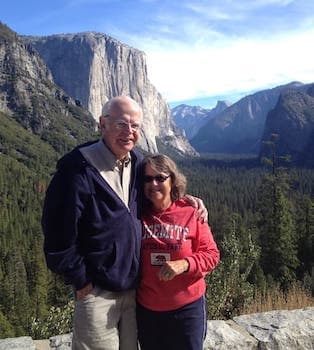
Curated with aloha by
Ted Mooney, P.E. RET
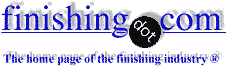
The authoritative public forum
for Metal Finishing 1989-2025
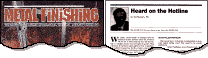
-----
Problems & Solutions in Chromic Acid Anodize of 7075
Q. I do a fair amount of Chromic Anodising on 7075 T6 material. From time to time I find that a tapped hole burns badly, destroying the threads, a very expensive problem. It has occurred with two different shaped parts. It always occurs in the hole located the highest. It normally only occurs on one part in a batch but once on 3 parts from a batch of 10. Round titanium jigs are used and the anode is circular and at the same distance from all the parts.
Willem Kleinschmidt- Strand, South Africa
2003
Q. We observed, recently, after the sealed (dichromate) chromic acid anodising of 7000 series the presence of a significant layer of "dust" on the surface of the parts. Does someone explain the reason for that? Could it be caused by an excessive hydration of the anodic layer?
Is it necessary to strip and re-anodize again the part or this dusty oxide layer can be removed in some way? After wiping the panel with water was not very efficient but the presence of the anodic layer was confirmed by electrical measurements.
TAMIRO Salvatoreaerospace - Turin, ITALY
2004
Treatment &
Finishing of
Aluminium and
Its Alloys"
by Wernick, Pinner
& Sheasby
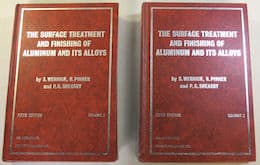
(note: this book is two volumes)
on eBay or
AbeBooks
or Amazon
(affil links)
A. Yes, according to Pinner in his latest book with Sheasby, "perfectly" sealed anodizing will have a loosely adherent powdered hydration on the surface. Elimination of this problem can sometimes be had by slightly lowering the pH, lower the temp, lower the time, and/or all of the above.
However, you may have a zinc salt film in the form of zinc acetate, zinc sulphate, or even a calcium salt film as precipitated calcium, or calcium acetate or calcium Oxide.
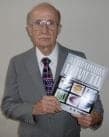
Robert H Probert
Robert H Probert Technical Services

Garner, North Carolina
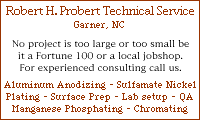
A. To paraphrase what Bob said: 7xxx series and 2xxx series alloys (more pronounced) have down-sloping anodization curves (Ohms per sq. ft. vs. time). Dissolution problems occur more readily with these alloys than for 1xxx or 6xxx series allows (up-sloping). Reducing temperature, electrolyte concentration, or time will all reduce dissolution effects.
If this is your case, you will still have the "dust" effects even if you sealed a sample in boiling water or steam, since it would have nothing to do with the sealing method. If this is what happens, you will need to use one or more of Bob's remedies to fix this.
- Columbia, Maryland, USA
Ed. note: it is our sad duty to advise of the passing of Paul Yursis in August 2005.
Here is a brief obituary by Mike Caswell.
Anodizing problems with 7075T6
Q. We chromic anodize 7075 t6 aluminium on a irregular basis and we are finding that the 7075 tends to pit very badly, especially when we double dip long lengths of it. We end for end the 7075 to get the coverage and find the pitting especial bad around the solution surface point of the material.
John Greedplating - Adelaide, South Australia, Australia
2004
A. After assuming that the alloy is right and that the zinc is not precipitated in the grain boundaries, then let's recognize that chromic acid anodizing of 7075 is very difficult. Our Lockheed specifications do not allow chromic anodizing of 7075 except for adhesive bonding reasons. Our Boeing says to only use 22 volts when anodizing 7075 T 73. So, after checking to see if there is any pitting caused by the pretreatment, then try 22 volts.
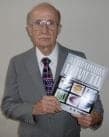
Robert H Probert
Robert H Probert Technical Services

Garner, North Carolina
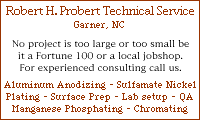
2004
Chromic anodizing 7075-T7351 aircraft propellers
Q. In order to manufacture a propellor for a light aircraft, I need to know if there are any problems in chromic anodizing 7075-T7351 plate in accordance with MIL-A-8625 / MIL-PRF-8625 [⇦ this spec on DLA] Type 1B, Class 2, Black, or will it provide a satisfactory surface protection.
Victor Shribman- Kiryat Ono, Israel
2006
A. Para 3.4.1 eliminates 7075 "unless otherwise specified" because at 11.13 % non-aluminum it exceeds 7.5 % non-aluminum. Lockheed list 7075 as unacceptable, but acceptable for adhesive bonding. Boeing says to anodize 7075-T73 by the 22 volts process.
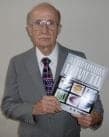
Robert H Probert
Robert H Probert Technical Services

Garner, North Carolina
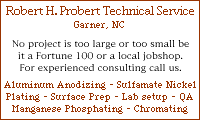
2006
Q. Recently we have been having a problem with Type I chromic acid anodize on 7075 alum alloy.
Certain areas on the parts after processing display small burnt hollow spots where the metal has been displaced - They are not rack marks. We have no problems with any other alloys such as 6061 or
2024. Could it be the distribution of magnesium or zinc in the composition of the alloy creating hot spots and buring?
Anodizer - Kenilworth, New Jersey
2007
![]() |
A. Tony - Colorado Springs, Colorado 2007 2007 A. No experience with chromic acid anodizing, but I've traced blisters in sulfuric acid anodized 7075 to Cu- and Fe-containing intermetallics; see letter #42961. - Goleta, California ![]() Rest in peace, Ken. Thank you for your hard work which the finishing world, and we at finishing.com, continue to benefit from. |
![]() |
A. sulphate is a problem child in type 1 anodizing. James Watts- Navarre, Florida 2007 A. The zinc in 7075 with time and/or temperature, migrates to the grain boundaries, then that left on or near the top, will "de-plate" when made anodic in sulfuric acid, and leave behind "pits". Find out the heat treat, heat, and time history of your metal and come back to us. Meanwhile, try ramping up slower. ![]() Robert H Probert Robert H Probert Technical Services ![]() Garner, North Carolina ![]() 2007 |
Q. What would cause SOME parts in a load of 7075 forgings to get attacked in a chromic acid solution and others not? The parts that are attacked are not attacked in the fixture areas and they look like random areas of the surface just exploded and have a black appearance.
Bob Bramson- Kenilworth, New Jersey
January 17, 2013
Q. Does anyone know what the high limit of sulphates would be in chromic acid anodize? If sulphates were the problem, would it not affect all the parts?
Robert Bramson- Kenilworth, New Jersey, USA
January 19, 2013
A. Boeing specs say then upper limit is 500 mg/L, that is 1/2 gram per liter. Experience is that if you are over this limit you fail salt spray.
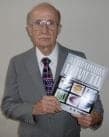
Robert H Probert
Robert H Probert Technical Services

Garner, North Carolina
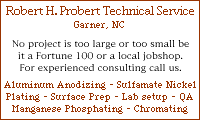
January 22, 2013
Q. I had sent some work pieces made of aluminum 7075 for chromic acid anodising but the finished product which I received were all of different shades. Some were darker than the others and some were darker at certain regions then the rest.
The Vendor tells me it's because of buffing manually and it wouldn't happen if it were completely machine buffed.
- Bangalore, India
July 7, 2020
finishing.com is made possible by ...
for Chromic Acid Anodizing [Detroit, MI]
Q, A, or Comment on THIS thread -or- Start a NEW Thread