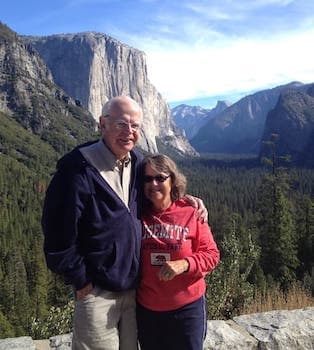
Sound technical content, curated with aloha by
Ted Mooney, P.E. RET
Pine Beach, NJ
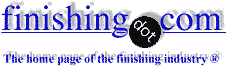
The authoritative public forum
for Metal Finishing 1989-2025
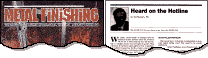
-----
Blisters in Hard Anodizing 7075 Aluminum Alloy
2001
Q. We have a problem. When hardcoating a specific job made from 7075 alloy we are getting blisters on parts.
The job we are seeing the problem with is 2 different small (1.25" long x 3/8" wide x 1/4" thk CNC machined) blocks.
We first ran a sample load for the customer of 200 pieces of each & it ran flawlessly. Next we ran another sample load of 100 pieces of each. The 100 of each were on the same rack & one style part came out with the blisters & the other did not.
I found an article in the August 2000 issue of "Products Finishing" which blames the problem on the material. It says:
"Its all about dissolved gasses found in aluminum billet. Since hydrogen gas is soluble in aluminum, it sometimes precipitates out of solution in the process of being converted from the ingot to heat treated billet. The hydrogen may come from excess humidity present during heat treatment, the presence of moisture in the casting furnace or in the aluminum "charge" used in billet casting. The precipitated hydrogen forms pores in the aluminum billet. When extruded, these pores collapse, but instead of "healing" they form an interface between the flattened pore or void & the metal around it. As the anodic coating grows inward during anodizing, these interface areas become potential sites for blistering. When the coating reaches an interface it can actually separate from the substrate, forming a blister..."
We have hardcoated 7075 aluminum for over 40 years and really never saw this problem. Last year we found it on a different job & that's when I found the article. That customer accepted the blistered pieces along with a copy of the article. The new customer / job says that while they understand the article, it is a govt job & the govt will not accept the parts like this.
Anyone else have this problem or know of a fix or minimize it?
David A. Kraft- Long Island City, New York
2001
A. Dave,
We too, have seen this problem a few years ago. The article you found is interesting. We assumed the problem was due to overheating of the parts (one of those "shot in the dark" guesses. We reduced our tank temperature to 30 °F, and it seemed to solve the problem. If the article you found does in fact state the real cause of this problem, I can't answer why lowering the tank temp solved it. As this is not SOP for us, I'm also wondering if stripping and reworking the parts had anything to do with our results...perhaps getting past the "pore, or void" that the article mentions?
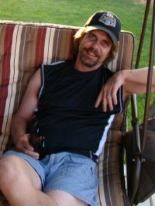
Marc Green
anodizer - Boise, Idaho
Multiple threads merged: please forgive chronology errors and repetition 🙂
Bubbles under Hard Coat
Q. A vendor is providing a MIL-A-8625 / MIL-PRF-8625 [on DLA], Type III, hard coat for aluminum parts. Some of the material exhibits a small bubble under the hard coat (looks like pepper flakes trapped under the coating). Some of the larger bubbles will flake off, appears to be some form of corrosion. The MIL standard seems only to address corrosion (pitting) on Type I & II coating, nothing specified for Type III. Is there a "best practice" criteria that would apply, i.e., none, or 'X' number sq/in?
Glenn TibbettMilitary Repair - Barstow, California, USA
2004
70xx series aluminum alloy?
Chris Jurey, Past-President IHAALuke Engineering & Mfg. Co. Inc.

Wadsworth, Ohio
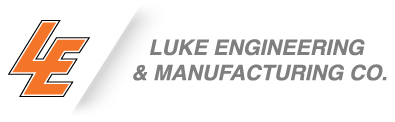
2004
2004
A. OBVIOUSLY YOUR VENDORS SURFACE PREPARATION WAS NOT GOOD. Had the parts been mechanically abused by time saving, sanding, bead blasting or such, in which case non-aluminum and hence non-anodizable matter, would have been imbedded into the surface and left to "bubble out" later. Or he did not clean, or he did not deoxidize and remove all of the aluminum oxide before applying the "controlled oxide".
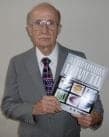
Robert H Probert
Robert H Probert Technical Services

Garner, North Carolina
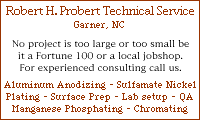
A. WE HAVE HAD THE SAME PROBLEM, THE BUBBLES COME FROM TRAPPED HYDROGEN THAT FORMS IN THE MANUFACTURE OF THE ALLOY (7075). AS THE HARD COAT FORMS IT TRAPS THE GAS IN THE ALLOY,WE ONLY HAD THE PROBLEM WHEN WE DYED THE HARDCOAT AFTER PREPPING IT FOR 3 MINUTES IN NITRIC ACID DEOX BATH. I THINK THAT THE DEOX WEAKENED THE COATING AND ALLOWED IT TO BUBBLE WHEN IT WENT INTO THE 140 DEGREE BLACK DYE. IF THE PARTS WERE NOT PREPPED AND DYED THERE WAS NO PROBLEM WITH BUBBLES.
GOOD LUCK,
LARRY COHENANODIZING - WACO, TEXAS
2004
Hard Anodize Coating Blisters On 7075
Q. We are experiencing blisters in 7075 after hard Coat. Does anyone know why this happens, and how to avoid/eliminate them.
Joel A. Lipof- Paterson, New Jersey
2006
2006
A. 1. With time and temperature, and especially with heat treating, the zinc migrates to the grain boundaries, when you anodize over these grain boundaries, it flakes off.
2. Work Hardening from dull tools or tumbling or blasting. When you anodize completely through a work hardened surface, stress flake the coating off.
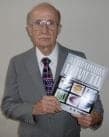
Robert H Probert
Robert H Probert Technical Services

Garner, North Carolina
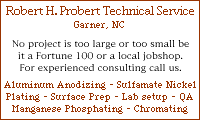
2006
A. Blisters aka pimples are caused by intermetallic particles which block anodize growth into the metal. A particle holds up an area of anodizing which becomes detached from the metal as anodize growth continues in surrounding areas. Looks like an incipient volcano. Stresses create cracks radiating outward from the center into the uplifted anodize (actually, surrounding anodize has moved downward) through which acidic electrolyte enters and creates white sulphate corrosion. The undercut anodize & corrosion products can detach & get swept away, after which the bare metal area some 500 microns in diameter can begin anodizing anew.
In SEM analysis back in 1997, I found particles of primary solidification phases FeAl3 and Cu2FeAl7 at the core of developing blisters. These are coarse particles up to 25 microns in diameter which should not be present in wrought microstructures; they are not the sub-micron particles formed by heat treatment.
Re preventing blisters: Shot peening breaks up the intermetallics within the near-surface Al matrix to a small enough size so as to not blister the subsequent hard anodizing, and is a common procedure for helicopter manufacturers. personal discussion, Leah Markowitz, Senior Engineer, HR Textron, 1998 SUR/FIN conference. See also "Hard Anodic Coatings on Aluminum Alloys: Evaluation and Control of Porosity," L. Markowitz, Metal Finishing, p. 19-24 (December 1992).
As MIL-A-8625 / MIL-PRF-8625
[on DLA]F, paragraph 3.3.2 could be interpreted as prohibiting shot peening, note: "Aluminum parts which have been peened with metallic shot shall be chemically cleaned" prior to anodizing. MIL-S-13165C [ed. note: or AMSS13165], paragraph 3.3.10.2 and MIL-P-81985, paragraph 3.5.2.1. Typically, this cleaning is a light etching followed by a nitric acid-type deoxidation.
The problem can also occur with Al 2024. The University of Illinois has developed an electrochemical process for removing intermetallics from the surface of aluminum alloys. Probably useful for applied coatings and chem film but not hard anodizing:
http://www.otm.uiuc.edu/attachments/T98002-092.pdf
- Goleta, California

Rest in peace, Ken. Thank you for your hard work which the finishing world, and we at finishing.com, continue to benefit from.
Q. I have been having problems with blisters forming on 7075. This is very rare I know and I have torn our operation apart and can't seem to find anything that we may have missed. I have seen delamination before but this is a new one. I have done a matrix of experiments to prove out our process. I keep coming back that there is something that is not right with the metal that we are trying to anodize. The problem is that it is very intermittent. I expect it to come back because we have not done anything to end the problem. What I can say is that we have processing 7075 for many years and consider it not that hard to anodize and have a long track record of success. I have been told by many that this could be a hydrogen outgassing problem. A problem that is created when the billet of aluminum is 1st made. What I would like to do is prove this with the data and move on with life. Any ideas how I could go about that?
Mike RobergAnodizing Operations Manager - Minneapolis, Mn, USA
June 7, 2009
![]() |
June 15, 2009 A. In heat treated or "old" 7075, the zinc has migrated out of alloy and into the grain boundaries as molecular zinc. If it is near the surface and you anodize though to it in some spots, the anodizing flakes off. ![]() Robert H Probert Robert H Probert Technical Services ![]() Garner, North Carolina ![]() A. Mike, - Belgaum, Karnataka, India June 16, 2009 |
Q. I work at an manufacturing plant where we make parts for aircraft that require many sealing surfaces. We have been running a part made of 7075 (more specifically 7075-T73511) for years now. The part has a large sealing surface that has been continually rejected by our customer for scratches that don't even have a depth to them. The problem we are having is the scratches only appear after anodizing but never before. 100% visual is done at all steps throughout the process even at the anodizer. We have gone through our process as well as our anodizing supplier and have not found where the scratches are originating from. We lap the surface before anodizing and suspect that something is being impregnated into the material that doesn't show up until the anodize process brings it to the surface.
Josh Bugni- Valencia, California, USA
January 17, 2012
A. Hi Josh,
It will help if you can post some pictures of the part with the defect.
- India
January 18, 2012
Measles on Hard anodized 7075-T6
Q. We are having problems with Hard anodizing of 7075-T6 parts.
It appears that the coating produces multiple small bumps at the surface. These bumps are poorly attached to the base material as I could chip them off using a knife. See picture attached. The part on the image is about 2 inches high.
Any insight about what caused the problem and how to resolve / avoid it ?
Thanks,
- Quebec, QC, Canada
May 9, 2012
A. Typically, that is Zinc precipitate in this particular alloy.
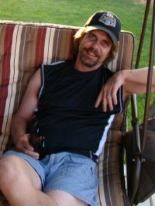
Marc Green
anodizer - Boise, Idaho
May 12, 2012
Q. OK about the zinc precipitate, but is there anything I could do to successfully anodize the parts anyway?
Benoit Gilbert [returning]- Quebec, QC, Canada
May 16, 2012
A. First things first, is that if you have SEM capability at your facility, I would analyze one of the blisters to confirm that is indeed the issue. I only have one part that I anodize that is made from 7075, and to date, I've never had issues. I know we're very careful about using Alcoa aluminum in this part that we manufacture. We use a HNO3 based de-smut, which may, or may not help you out, depending on how bad the precipitate is (if that is your issue)
If you do a search on this site, I know this particular question has arisen many times. You should be able to find numerous posts about this problem, and perhaps a solution from others who anodize this alloy more frequently than I.
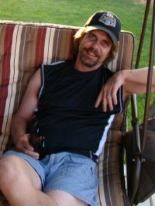
Marc Green
anodizer - Boise, Idaho
Treatment &
Finishing of
Aluminium and
Its Alloys"
by Wernick, Pinner
& Sheasby
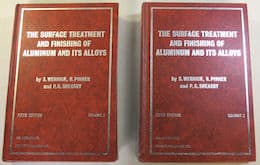
(note: this book is two volumes)
on eBay or
AbeBooks
or Amazon
(affil links)
Q. I am having a problem with 7075 aluminum blistering after black hard coat anodize. We have run several loads with no problems and all of a sudden the last 2 loads have had blisters. I have checked the parameters of my tank and everything is where it should be. We rack only on Aluminum racks, no titanium. Does anyone have any suggestions?
Paula Stablewski- Batavia, New York, USA
Q, A, or Comment on THIS thread -or- Start a NEW Thread