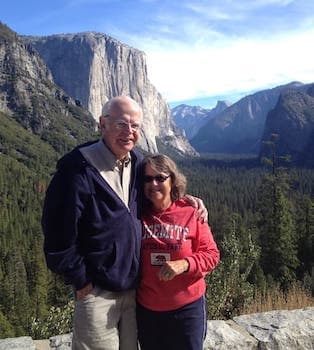
Curated with aloha by
Ted Mooney, P.E. RET
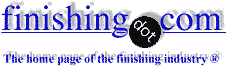
The authoritative public forum
for Metal Finishing 1989-2025
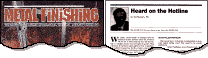
-----
Conductive Black Coatings: black zinc, black nickel, black chrome

2nd Request
Q. Hi forum,
We are supposed to select Hex bolt for fastening Tin coated Copper lugs of EV Power cables to the copper terminals (60V).The fastener supplier is suggesting Zinc Nickel black. I need to understand if the electrical conductivity is affected compared to using Zinc Nickel black instead of Zinc blue. A few references on the fastener manufacturer website says conductivity of Zinc Nickel black is superior in addition to better corrosion resistance.
s Raja
- India
November 17 & November 28, 2022
A. Hi Raja. I could be misunderstanding the question or I could be in error, but I do not believe zinc plating is appropriate for power terminals. Although the power is intended to be conducted by contact pressure between the tin-coated lug and the copper terminal, why not tin plated bolts?
Luck & Regards,
Ted Mooney, P.E. RET
Striving to live Aloha
finishing.com - Pine Beach, New Jersey
⇩ Related postings, oldest first ⇩
Q. Hello, I would like to know the different options available for treating cold-rolled steel to give it the following properties: 1. electrically conductive finish 2. visually black 3. corrosion (rust) resistant 4. at least somewhat scratch resistant.
Matt Kowitt- Sunnyvale, California
1999
A. Hi Matt. It depends on how conductive is conductive -- you would need a black precious metal coating for very low contact resistance. But otherwise there are numerous options including black chrome plating, black nickel plating, zinc plating with black chromate, and zinc-iron plating with black chromate. A black oxide coating would have very limited corrosion resistance as well as poor conductivity. Good luck.
Ted Mooney, P.E.
Striving to live Aloha
finishing.com - Pine Beach, New Jersey
Q. I am looking for a black plating finish for some zinc parts used in an antenna design. The finish should be electrically conductive and reasonably durable (similar to nickel plating). The black finish is required for cosmetic reasons. Can anyone suggest a process?
Owen Thistlewireless technologies. - Canada
1999
A. Many of the diamond-like carbon (DLC) are conducting if deposited by PVD.
Jim Treglio - scwineryreview.com
PVD Consultant & Wine Lover
San Diego, California
A. Try to find a company that can do Black Chrome. This is a durable, conductive and very black finish used on solar panels and space components. Being electrolytic it can be difficult to coat complex shapes.
Trevor Amos
coating technology shop - Southampton, UK
Q. I am looking to plate aluminum and zinc die cast parts. The plating must be flat black, or have a high emissivity, and must be electrically conductive. E-coat is not electrically conductive enough. Currently I am using black nickel without any brightener; it is has good conductivity but has a poor black/dark brown color and emissivity. Price is sensitive. Volumes are 200,000 +.
Bob Allen- Hoffman Estates, Illinois, USA
2000
A. Dear Bob,
I plate a lot of Zinc and Aluminium Diecastings with Zinc plating followed by black Chromate. It will meet all your requirements especially cost vis a vis black Nickel.
Regards,
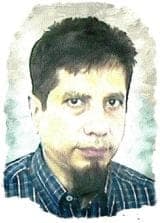
Khozem Vahaanwala
Saify Ind

Bengaluru, Karnataka, India
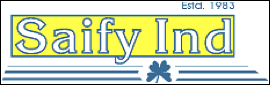
A. Mr. Bob Allen,
One solution is black chromium electroplating, after copper and, eventually, nickel plating.
Another solution may be the plating of a dark grey tin-nickel alloy.
Both have "sensitive" prices.
Emmanuel PopescoChennevieres, France
Ed. note: Readers may wish to listen to "The Lost Art of Tin-Nickel Plating"
Multiple threads merged: please forgive chronology errors and repetition 🙂
Q. Can I use black zinc coating on screws made of carbon steel, if I need a good electric contact?
Thanks in advance,
Wolfgang Krause- Dresden, Germany
2002
A. Questions about black metal coatings which have very good electrical conductivity come up often at this site. I do not know of any dark coating which offers low contact resistance. But if you are torquing a screw, you should not have any problem making ground since the locking washer usually has sharp edges which cut through into the zinc.


Tom Pullizzi
Falls Township, Pennsylvania
A. In general, the darker the chromate, the higher the contact resistance, thus, black is probably the worst! However, Tom is also correct in that any amount of torque will break down the resistance and ground to the zinc.
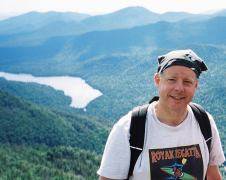
Milt Stevenson, Jr.
Syracuse, New York
Tip: Readers want to learn from Your Situation 🙂
(little can be learned from abstract questions, so many readers skip them)
Q. I have thread rolling screws that are zinc plated and black chromate finished. I'm curious to know if this finish is electrically conductive?
Tom S [last name deleted for privacy by Editor]- Elkhart, Indiana, USA
2002
A. The zinc plating is conductive, Tom; but the black chromate is usually not very conductive. It is so thin that it's certainly not to be used as an insulator, but not a reliable conductor for low voltages either. Please see Mil-C-5541 for a discussion of Class 1 vs. Class 3 coatings, which may be of some help.
Please tell us why you are "curious", and give some background and we may be able to offer you more satisfying answers . Good luck!
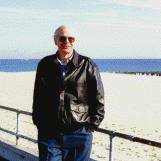
Ted Mooney, P.E.
Striving to live Aloha
finishing.com - Pine Beach, New Jersey
Electrically conductive finish in black
Q. Does a process/product exist that both provides both a nice surface finish (in this case Black) and is electrically conductive? My idea was to combine the now- separate conductive coating step (chromate?) and then painting outer surface with one process that would achieve both.
By the way: could someone clear-up the confusion over: Iridite (trade name?) Iridite / Alodine (trade name?) (yellow) chromate Many thanks from a grateful Electrical Engineer. Firms may feel free to contact with sales info.
Mark JohnsonAl enduser w/ electr. equip. appl. - Riga, Rigas Rajons, LATVIA
2004
Ed. note: This RFQ is outdated, but technical replies are welcome, and readers are encouraged to post their own RFQs. But no public commercial suggestions please ( huh? why?).
A. I don't know of any really good conductive black coating for aluminum. Black nickel plating is somewhat conductive, but far more expensive than chromate and somewhat difficult to apply uniformly over large areas.
The chromate nomenclature question is easy: The Iridite® brand belongs to Macdermid. Alodine® belongs to Henkel Surface Technologies. Chromates approved for MIL-C-5541 coating of aluminum are listed in QPL-81706
[⇦ this spec on DLA], available at ASSIST: http://assist1.daps.dla.mil/quicksearch/
Black chromates for zinc or cadmium usually include silver. For aluminum substrates, yellow chromate can be dyed black. Talk to your local chromate distributors and metal finishers.
Chromate coatings lack abrasion resistance. Sealants and waxes improve corrosion resistance and general durability, but greatly reduce conductivity. Chromated parts are frequently painted (after protecting any electrical grounding areas with temporary masking).
Ken Vlach [deceased]
- Goleta, California
Finishing.com honored Ken for his countless carefully researched responses. He passed away May 14, 2015.
Rest in peace, Ken. Thank you for your hard work which the finishing world, and we at finishing.com, continue to benefit from.
Q. I find the discussions on conductive black finishes interesting and informative. We have been struggling with this problem as well. We have a need to produce parts in Aluminum and steel with a black finish while addressing electrical conductivity issues. We have often used the undesirable method of masking in the past. We have used black oxide on our steel parts but we don't like the oily finish or the cosmetics. The weak conductivity is also a negative. We are currently seeking to find a solution and are trying to find out if black zinc, black chrome or some other process might work for us. Any information would be greatly appreciated.
Walter W [last name deleted for privacy by Editor]network test equipment manufacturer - Utica, New York
2004
Conductive Black Zinc Cobalt onto Aluminum
Q. In searching for a conductive black finish for aluminum, we have tried black zinc chromate (basically nonconductive, though color is acceptable) and black nickel (somewhat better conductor but too bright and reflective a finish for our night vision cameras). Have found that Amphenol (U.K.) has a conductive black zinc cobalt finish available for their connectors. Is this finish commercially available in the U.S. and is it considered at least as good as MIL-C-5541 chemical conversion coatings at corrosion protection for aluminum?
Douglas Wylie Fowler- Santa Clara, California
2005
A. Hello Douglas,
I'm sure a search of the Jobshops of finishing.com will put you in touch with many platers who will positively have this service in your country. Yes the coating will work much better than your MIL spec.
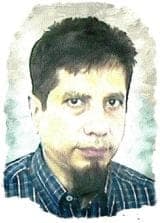
Khozem Vahaanwala
Saify Ind

Bengaluru, Karnataka, India
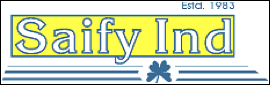
Q. Hi,
I am trying to confirm that the Black Zinc trivalent coating that I have applied to a steel chassis is conductive. We have not applied any other coatings to provide salt spray protection. I also need to be able to refer to a standard, preferably MIL, that would provide proof to our customer that this coating is suitable for ground bonding.
Also, I have heard that this coating may turn white with time. Is this true?
Any help would be greatly appreciated.
Thanks,
Integration Engineer - Pickering, Ontario, Canada
2007
A. There is such a variation of products being sold in the plating industry as "trivalent black chromate" or "non hexavalent chrome conversion coating" that it is impossible to make any statement. To the best of my knowledge (someone correct me if I am wrong) the Mil Spec only recognizes hexavalent processes. Most all trivalent or non hex processes use a sealer or top coat which is generally non conductive so that the thicker this coating the less conductive the part will be but generally the greater the corossion resistance of the coating. You should specifically state to your vendor what your requirements are and let the plater tell you if he and his suppliers can deliver what you want. The answer here is communication first.
Gene Packmanprocess supplier - Great Neck, New York
A. Yes there are a lot of decent processes with Trivalent Black and with some black trivalent topcoats as well. I have checked with the one I'm using and there is no drop in conductivity across the surface by using a thick topcoat.
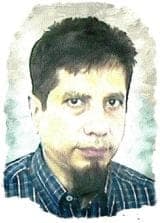
Khozem Vahaanwala
Saify Ind

Bengaluru, Karnataka, India
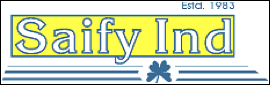
Zinc cobalt black plating (acidic) isn't conductive enough
Q. Dear Sir,
We are facing problem in zinc cobalt black plating . Customer require good conductivity over black passivation. To protect passivation layer we are using sealant. but electrical conductivity poor due to this. after baking same components for 150° C 30 min. excellent conductivity found. But same components out of 1000 /50 rejected at customer end for white corrosion and pitting marks.
We have tested with 95 % humidity test with 65° C. TEMP. ON SECOND DAY WE FOUND WHITE CORROSION. SO WE PUT SOME COMPONENTS WITH SEALANT THEY ARE O.K. TILL DATE.what will the cause for this corrosion?cAN You THROW SOME LIGHT ON THIS PROBLEM
PRODUCT DESINGER - PUNE, MAHARASTRA, INDIA
August 22, 2008
Ed. note: This RFQ is outdated, but technical replies are welcome, and readers are encouraged to post their own RFQs. But no public commercial suggestions please ( huh? why?).
A. Dear Mr. Bhatt,
50 pieces out of 1000 (5%) can sometimes be taken as operational problem as your system is manually operated.Products treated with sealant did not show failure after humidity test. That means sealant is advantageous.
I think you may have to take care while processing(during passivation and top coating.
regards,
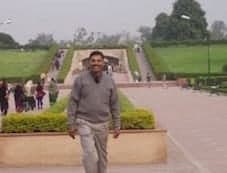
T.K. Mohan
plating process supplier - Mumbai, India
A. If you are getting corrosion that fast, try putting on a thicker coating and make sure that it is uniform. That way, you may be able to not use the sealant. Also, is it possible to put on a thinner coat of sealant and still have it pass both tests?
James Watts- Navarre, Florida
Q. Hello folks, I work in Test Equipment and we have a similar situation. We want to have a black finish on our aluminum chassis for aesthetics and engraving purposes, but it must also be electrically conductive. All in one step would be preferred. Anodizing is not a very good answer for this, because we have many, all-aluminum parts inside, and depend on chassis ground throughout the units. If anyone has a Black colored RoHS compliant Chem-film answer, it would be greatly appreciated.
Scott A Smithaviation systems - Grand Rapids, Michigan
January 21, 2010
Q. Hi, We manufacture electrical products consisting of sheet metal parts and weldments, and electrical components. Because we must maintain an aesthetic aspect with our products we typically use black screws for the assemblies and grounding purposes. Recently we've switched to black zinc from black oxide to improve grounding between parts as we found black oxide to be problematic. However we've also found the black zinc screws vary from vendor to vendor, which in some cases causes grounding issues again. Is there a plating or conductivity standard we can specify for our screws?
David Black- Bridgeport, Connecticut, US
April 4, 2017
A. Hi David!
You can try black nickel process, or black zinc-iron or zinc-nickel process. Both zinc-iron and zinc-nickel don't require a sealer to withstand good corrosion resistance, maybe black nickel does. I know one or two people here in Argentina do zinc+ blue chromate + black paint as "black zinc" in order to meet black color and not use black zinc passivation (it's expensive and not really "black").
If you try any of these three possibilities, maybe you can solve your problem. I would try the cheapest ;)
Regards,
TEL - N FERRARIS - Cañuelas, Buenos Aires, Argentina
Q. We are using a black chromate finish on some of our fasteners. In some applications these need to offer a conductive earth path.
We have tested our current supply at 0.02 Ohm resistance or less against a requirement (by standard) of 1 Ohm.
A bit of research indicates that:
* Only coating (zinc plating) done with cyanide process would become insulative when black chromated (not sure of why this occurs, research paper)
* a RoHS/REACH compliant coating would not use such a cyanide process (manufacturer statement)
The question... how would we properly specify the coating to preclude the wrong coating being applied?
... this ensuring the conductivity requirement.
According to this research paper the type of zinc plating can affect this:
"For certain applications of galvanized steel protected with conversion coatings it is important that the surface is electrically conductive. This is especially important with mating surfaces for electromagnetic compatibility. This paper addresses electrical conductivity of chromate conversion coatings. A cross-matrix study using different zinc plating techniques by different labs showed that the main deciding factor is the type of zinc-plating bath used rather than the subsequent chromating process. Thus, chromated zinc plate electrodeposited from cyanide baths is non-conductive while that from alkaline (non-cyanide) and acid baths is conductive, even though the plate from all the bath types is conductive before conversion coating. The results correlate well with the microscopic structure of the surfaces as observed with scanning electron microscopy (SEM) and could be further corroborated and rationalized using EDX and Auger spectroscopies."
https://www.researchgate.net/publication/248193590_Electrical_conductivity_of_chromate_conversion_coating_on_electrodeposited_zinc
- Liverpool UK
July 28, 2022
A. Hi John.
I am pleasantly surprised that you've been able to achieve 0.02 ohms. The conclusions in that research paper are surprising and interesting, but I don't think that one paper from 16 years ago (perhaps before the widespread use of differing proprietary top coats over trivalent chromates), is sufficient to offer confidence.
I haven't bought the paper, only seen the abstract, but if you intend to rely on it, obviously you need to read the full text if you haven't. There are many different zinc plating processes, operated under different conditions including temperature and current density, many different black chromate solutions, silver-based and non-silver, trivalent and hexavalent, preceded or not preceded by a nitric acid dip of varying concentrations, thin chromates with top coats, things poorly rinsed or well-rinsed, etc., and there could be important exceptions mentioned in the text but not the abstract.
I don't think you are yet in a position to write a specification that will insure good conductivity short of specifically including the requirement in your specification. I think you'd need to work with one or more plating shops, advising them what is known, and requiring regular testing of conductivity until you have a much fuller data set. Alternately, the process suppliers do a great deal of in-house research, and if you are willing to limit yourself to one proprietary zinc plating process and one proprietary black chromate process, it may be that they can offer you a robust solution.
Luck & Regards,
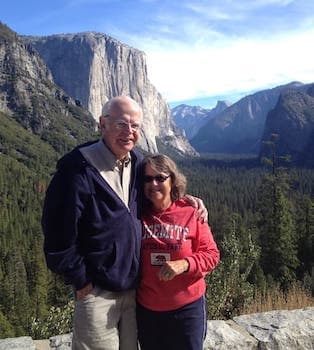
Ted Mooney, P.E. RET
Striving to live Aloha
finishing.com - Pine Beach, New Jersey
Q, A, or Comment on THIS thread -or- Start a NEW Thread