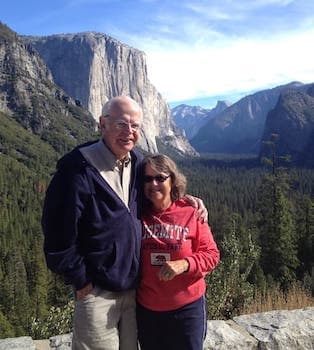
Curated with aloha by
Ted Mooney, P.E. RET
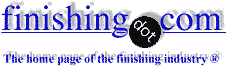
The authoritative public forum
for Metal Finishing 1989-2025
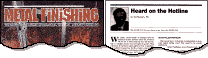
-----
What is the silvering and plating process for audio LP vinyl records?
Q. What is the wetting agent?
How should I apply it?
Normally I apply activator; I get success in small parts, but big part I get lots of black spot and white.
- dhaka bangladesh
March 30, 2021
March 2021
A. Hi Zubayer. Jay said that the wetting agent he was speaking of was "Saponin 25% or equiv. dip or spray". Google shows me a Wikipedia page on this subject plus much else. Can you be a bit more specific on that part of your question?
Luck & Regards,
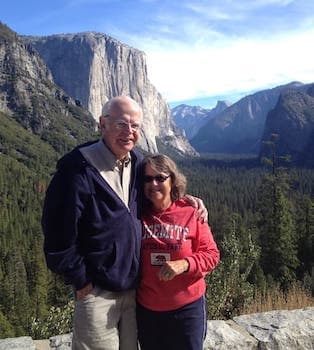
Ted Mooney, P.E. RET
Striving to live Aloha
finishing.com - Pine Beach, New Jersey
⇩ Related postings, oldest first ⇩
Q. Hello ,
I am looking for detailed information about the process use in the vinyl records industry for the galvanic process of lacquers (silvering and plating). Does anybody already did that?
Thanks for your answer.
product designer - Barcelona, SPAIN
2007
A. Hi, Yann. This takes us all the way back to the very first inquiry printed on finishing.com in 1995. In theory the process is simple: spray the lacquer master with two-part silvering solution and then electroform a stamper from nickel, and put a chrome flash on it. For higher production, where multiple stampers are required, passivate your first electroform instead of chrome plating it, and then electroform "mothers" from your first electroform, and multiple stampers from the mother, and chrome flash the stampers.
This is high enough "resolution" for vinyl records, but CDs use vacuum deposited metallizing instead of two-part silvering, and they are not chrome flashed. Good luck.
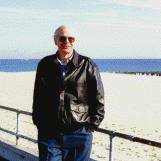
Ted Mooney, P.E.
Striving to live Aloha
finishing.com - Pine Beach, New Jersey
2007
A. Have a look at Topic No 44444 - this topic was recently covered in another enquiry. There is also a lot of history on this site about silver spraying
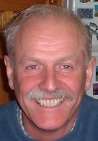
Trevor Crichton
R&D practical scientist
Chesham, Bucks, UK
2007
Q. Can you give me any figures on the 'resolution' of the silvering spray technique versus the vacuum deposition? I'm trying to decide if I can get away with spray method.
Colin Gibson- Rolla, Missouri, USA
July 26, 2011
A. Hi, Colin.
Sorry, but I don't have hard numbers for you. I do know that two-part silvering is not only used on vinyl records, but was also used for videodiscs and for super-small diffraction gratings (a technology to supplant microfilm by embossing plastic sheet with diffraction gratings, but which was itself supplanted by the digital revolution just as it was getting started).
I implied that the process does not offer enough resolution for CDs and DVDs but I didn't quite mean to, as I don't know that insufficient resolution was the driver in CDs moving to vacuum processes. While two-part silvering can be done rather casually in open air when resolution isn't critical, the resolution is high enough that the silvering must be done in a high quality cleanroom to even approach its limits. The vacuum process is probably less labor intensive.
Regards,
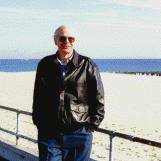
Ted Mooney, P.E.
Striving to live Aloha
finishing.com - Pine Beach, New Jersey
July 26, 2011
Thanks Ted,
It sounds like a two part silvering solution could work for me. Other than a clean room, what other consideration should I take? Will the regular two part solutions work or will I need some more complicated formulations?
On a related question is it even possible to silver, to the same resolution, through chemical or electroless deposition or is spraying the only option?
Colin Gibson [returning]- Rolla, Missouri, USA
July 27, 2011
July 27, 2011
A. Hi,
You're probably best off with a proprietary two-part silvering solution rather than home-brew, but I am only the website operator, not necessarily highly experienced in every topic that comes up :-)
I saw precision two-part silvering done only once, on a lacquer master in a cleanroom on a "spin table" (similar to what children use for "spin art").
If your substrate is copper or brass rather than plastic, you may be able to do immersion silvering instead of two-part silvering (see our FAQ, "Silver Plating at Home").
If the substrate is non-metallic and you are trying to metallize it, I think you are limited to vacuum metallizing, two-part silvering, or conductive paint. I'm not denigrating the conductive paints like the Aquadag series, but I do think that even fine specialty paints will have significantly less resolution than two-part silvering. I suppose electroless copper or electroless nickel plating is a possibility, but I haven't heard of it as a general metallization strategy. If you can tell us what you are trying to do, maybe better answers can result. Good luck.
Regards,
Ted Mooney, P.E.
Striving to live Aloha
finishing.com - Pine Beach, New Jersey
A. Hi Yann, Colin,
I have been looking at alternatives to the 2 part silvering spray method of processing lacquer master recordings as well. So far, the 2 part silvering system works the best in a high volume production style of manufacturing regarding ease of use and repeatability. Vapor deposition in a bell jar or sputtering can subject the lacquer to higher levels of heat which causes concern as to the stability of the original groove geometry being retained during the process.
In the two part silvering process for the lacquered master it starts out with a good cleaning using a mild soap that leaves no residue. 50% liquinox works well. The next step is an application of a wetting agent (Saponin 25% or equiv. dip or spray) to reduce the surface tension of the lacquer surface. This is critical as the next step is the application of stannous chloride solution (10 grams stannous crystals/20 ml hydrochloric acid/3 liters DI water). The stannous will lay down a layer of molecules along the surface of the lacquer that will react like a binder with the silvering spray solution. If the wetted surface of the lacquer is repelling the water (breaking like a waxed car)then the stannous will not adhere well to these areas and those areas will have poor silver adhesion as well. The stannous dip can be around 15 seconds or so. A light DI rinse and then the lacquer is mounted on a rotating upright spin table. The lacquer is lightly rinsed one more time with DI and the silver solution is sprayed onto the lacquer using a special dual head spray gun. The silvering solution (Peacock Labs Formula) is kept separate from the reducer solution in different bottles and fed into each head of the gun separately. The sprays will mix in mid air approx. 3-6 inches in front of the lacquer. The silver is dropped out of the spray solution and combines with the stannous chloride on the surface of the lacquer to make a layer of silver. The silvered lacquer is removed from the spin table, rinsed with DI and put into a special nickel sulfamate pre-plate tank. The pre-plate tank is kept around 95-100 °F pulling approx. 10-20 amps over 30 minutes to allow a layer of nickel to build up on top of the silver layer to give it a more rigid backbone. The low temp/amps helps to keep the lacquer from temp expansion and possible distortion of the groove geometry. Once the pre-plate layer is thick enough the part is transferred to a production nickel sulfamate tank 12 oz pg/[pH 4.0 usually around 130-140 °F and the rest of the plating to full thickness will occur here. This will make the MASTER or FATHER over the course of many hours. Once the MASTER is formed, the part will be cleaned, passivated, and plated to form a MOTHER, repeat process to make a SON. The SON will be cleaned, sanded, center punched and formed into a finished stamper to be used in the record press to make the vinyl record.
I hope this helps,
Jay
Record Manufacturing - Canoga Park, California USA
August 31, 2011
Wow, Jay, what a thorough exposition. Thanks!
Regards,
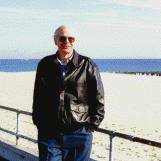
Ted Mooney, P.E.
Striving to live Aloha
finishing.com - Pine Beach, New Jersey
Electroless Nickel Solution as alternate to Two-part Silvering
Q. We are a vinyl record pressing plant partnered with a record plating facility. There was an electroless nickel spray solution used in the first step of record plating in the Cincinnati, Ohio area during the late 1980's until around 1992, when most record pressing plants were closing.
The company that made this solution was based in Indiana. However, they are out of business, and we cannot seem to find any documents with a person or company name on them.
I am hoping that someone on this forum may either know the company, or even better, have been someone who worked for that company. Or, someone who is familiar with the record plating process who would be interested in discussing electroless nickel solutions which may work for it. We would like to begin purchasing a nickel solution like that one that was briefly in use in this industry during the aforementioned time frame. Any help would be immensely appreciated.
- Columbus, Ohio, USA
September 18, 2013
A. Hi Matt. Unless you know for sure to the contrary, I'll suggest that the spray solution was probably a two-part silvering compound rather than electroless nickel.
But if you're sure that it was electroless nickel, then there had to be some way of metallizing the plastic first, such as a dip into a palladium chloride solution.
Regards,
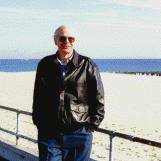
Ted Mooney, P.E.
Striving to live Aloha
finishing.com - Pine Beach, New Jersey
September 24, 2013
Q. Yes, it was definitely a nickel solution - not silver. There was a cleaning agent used on the lacquer immediately before spraying the nickel solution.
The company that made it had developed it as a dip for other industries. But, because spraying was the practice of the record business, they were able to convert it to a spray solution.
it was successfully used by a few (possibly only one) pressing plants for a period of 3-5 years. Around 1992, when most of the existing pressing plants closed, the remaining plants with plating facilities did not buy into the electroless nickel process. Therefore, the few existing record plating facilities in the U.S. today (including ours) rely upon silvering. But, the people who were involved with this electroless nickel process in the early 1990's describe it as a much better process than silvering.
One more follow up -- to clarify, this is not spraying onto plastic. This is spraying onto a nitrocellulose lacquer- coated aluminum disc.
Matt Earley [returning]- Columbus, Ohio, USA
September 24, 2013
February 24, 2019
A. I would like to reply to Matt Earley from Columbus, Ohio, USA(yeah I know late reply, but I recently found the process he was looking for).
Yes, Spray On Nickel process was used briefly around the 90's as replacement for Silvering LP Vinyl record masters.
The advantage of this process was the stability of the solution when stored(not explosive), Nickel sulphate is many times less expensive than Silver Nitrate and the deposited Nickel metal is much stronger and durable than Silver. The drawback at the time(and even more so now) was the expensive Palladium Chloride activator.
The solution was a room temperature Electroless Nickel chemestry(the usual EN solution with sodium pyrophosphate added to lower the temperature required, many expired patents are available dating from 1960's).
The process is quite similar to the silvering process and is now being actively advertised as a replacement for other spray on silvering process like the spray on chrome process.
The process is: Lacquered aluminum disc is treated with Stannous Chloride Sensitizer, rinse, Palladium Chloride Activator, Rinse and then Electroless Nickel solution is sprayed on the disk and a Nickel layer is form on the disk, the disk is rinsed and electroform by usual means. Another advantage of the solution is that it can be reused for later(unlike the silvering solutions that once activated they hava a very short shelf life and once in contact with the reducer they are reduced to elemental silver and can't no longer be used)..
I've built a small proof of concept system using off the shelf EN solution from a provider that was not aware that I was going to use the solution that way and I must say the results are very promising and I am sure if someone on the Vinyl record industry would like to use such process they could get in contact with known EN providers and request a solution made just for that process instead of a generic EN solutions.
- Managua, Nicaragua
Q. This thread is very informative. I see the recipe for the stannous is posted, I was hoping someone could fill in the gaps with a non proprietary method for making the reducer and silvering solutions.
Lee Clark- Brisbane, qld, Australia
February 22, 2019
A. Hi Lee. Trevor tells us that he's given us a formula for the silvering solution and reducer on topic 44444. Threads 31604 and 23536p2 touch briefly on reducing agents. If you google Brashear process, Martin process, or mirror silvering you'll find info on the various potential reducing solutions which, as I understand it, can be based on (carcinogenic) formaldelhyde, NaoH & NH4OH, or certain sugars. Thread 0415 offers info on all of the processes. We will be happy to post references to published info or answers from people well known to us, but we can't directly post formulas from largely anonymous posters for fear of them accidentally or deliberately revealing trade secrets.
Presumably you are well versed in safety protocols, but we remind readers that this forum is like a one-room schoolhouse or a library where you may overhear or read stuff that they may not be trained to safely work with, and fulminating silver is definitely not for the untrained or inexperienced, as highlighted in previously mentioned threads.
Regards,
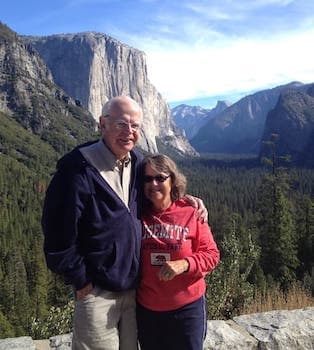
Ted Mooney, P.E. RET
Striving to live Aloha
finishing.com - Pine Beach, New Jersey
February 2019
Q. I've been set with the task to find some information on the process of silvering vinyl and came across this site. The information I've gathered just from here has really helped me realize how extensive this process can be. What I'm mainly interested in (and what I'm having the most difficult time finding) is how the waste from this process is being contained, i.e. do you need to have some type of air flow/filters to trap the chemicals that don't attach to the vinyl and how are you containing the contaminated DI water, sanitizer, the silvering, etc.
Jonathan Meyer- Charlotte, North Carolina, USA
November 5, 2017
Q, A, or Comment on THIS thread -or- Start a NEW Thread