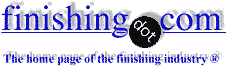
-----
Barrel chromium plating

Q. Can anybody help me on detail process, chemical, equipments source for chromium plating in barrel operation for smaller parts? What precautions should be taken for this process over that of conventional Rack operation?
DR. D. SEN- Calcutta, INDIA
2000
A. If it were commercially feasible, the equipment and process would be sold by every company that could legally break a patent.
James Watts- Navarre, Florida
A. Chromium passivates nearly instantly, such that make-and-break contact causes laminar plate. Hexavalent chromium therefore cannot be robustly barrel plated in the conventional sense.
When I started my career way back in the 1960's the company I worked for already had an ongoing research project on the subject; so strong interest has been present for many decades. Our unsuccessful approach for mass plating of small parts was sort of a shaker conveyor.
On the other hand, there was a local plating shop barrel commercially chrome plating the clips for PaperMate pens in conventional polypropylene plating barrels. The "rub" was that their success rate, even after all their optimization efforts, was under 20%. This meant very careful 100% inspection and sending more than 80% of the parts back for chrome stripping and another try. So, yes, it was a commercial process, but one which probably would be scorned today.
In the intervening years some special equipment has been offered and used for the process -- for example, barrels that rotate at very high speed to keep the parts pressed in place via centrifugal force). I'm not versed in their success and practicality but it seems that the approach never took the world by storm..
Some vendors have substituted trivalent chrome or tin-cobalt barrel plating and claimed some success. Unless you have years and millions for a major development effort, I don't think hexavalent chrome barrel plating will prove at all practical.
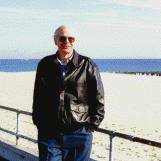
Ted Mooney, P.E.
Striving to live Aloha
finishing.com - Pine Beach, New Jersey
A. Dr.D.Sen,
You may consider the plating of bright tin-nickel alloy which has the same corrosion resistance as chromium, a hardness of 650 HV and can be very well plated in barrels.
E. Popesco- France
----
Ed. note: Dr. Sen and readers may want to give a listen to "The Lost Art of Tin-Nickel Plating"
A. Dear Mr Sen, You can try tin cobalt plating it is a barrel process and finish is very close to chromium plating.
Varun Bhalla- Delhi, Delhi (INDIA)
----
Ed. note: For further info on tin-cobalt plating, please see:
• Thread 47247, "Chrome Plating Alternative and Substitutes"
• Thread 47866, "Tin Cobalt plating problems Q&A"
Multiple threads merged: please forgive chronology errors and repetition 🙂
Q. Dear Ted,
Firstly, many thanks to you and your sponsors for finishing.com. I visit it almost daily.
Next, my question:
I presently plate a layer of tin/cobalt over nickel (watts) but due to market demand, there is a need for Hexavalent chrome. I am considering Hexavalent barrel chrome plating in my plant. Apart from what I gather at finishing.com, I need further advice concerning :
1) Barrel Design
2) What is Fluosilicate and what type shall I add? (I believe fluosilicate comes in solution form).
Thanks, SK CHEAH
SK Cheah- Hong Kong
2000
A. Hi Cheah. It is not completely impossible to do hexavalent chromium plating in a barrel, but it's close enough to impossible that you should not consider it until you fully understand the issue of make-and-break contact in chrome plating: the instant the contact breaks, the chromium plating passivates -- so the chrome will deposit in poorly adherent laminar layers.
Some special machines were built for the purpose, and consisted of multiple barrels on a single frame, sort of like a ferris wheel (Fuji Platerite Ltd). The idea was that they could maintain the G's so the parts did not break contact; I can't tell you how successful they have been except to say that I haven't seen them advertised for decades.
I will tell you that it will probably be less expensive to rack plate the parts than to plate them in a conventional plating barrel, and that if you do barrel plate them you will need to process very small loads, include careful 100 percent inspection, and you must plan on an enormous reject rate even after are very good at it.
Fluosilicate is a catalyst used in SRHS (self-regulating high speed) chromium plating baths. As you may know, hexavalent chrome plating will not take place unless there is a precise ratio of chromic acid to catalyst; too much or too little catalyst and the plating stops. The idea here is that you can keep an excess of fluosilicate precipitated out in sludge at the bottom of the tank, and the dissolved portion of the fluosilicate will act as the required catalyst. As it is dragged out or consumed, additional amounts will go into the solution from the sludge to achieve automatic regulation of the catalyst ratio. You can go to most plating process suppliers for fluosilicate catalyzed hexavalent chrome plating solution.
Dubpernells's Electrodeposition of Chromium from Chromic Acid Solutions
⇦[this on
Amazon affil links] includes this rather cryptic note, early on:
"About the only exception is in barrel chromium plating where the current densities and temperatures are quite low in the complex fluoride catalyzed solutions used, and a ratio of about 110-115 appears optimum." -- but the volume later includes 3 pages of info about the formulations. Best of luck.
Readers: take a trip in the time machine: click on the graphic to read "Chemical Balance", a poem about SRHS chrome -- probably the plating industry's only well-known poem.
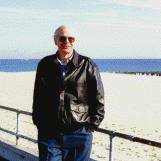
Ted Mooney, P.E.
Striving to live Aloha
finishing.com - Pine Beach, New Jersey
Multiple threads merged: please forgive chronology errors and repetition 🙂
Q. Dear All,
We have Nickel-Nickel-Chrome plating process in our existing production (Jigging type). In order to save labor and cost, I was assigned to consider barrel chrome to replace the existing jigging process, especially for small components.
Queries:
1) I was told that barrel chrome process is "close to impossible" :( Is it true? If so, what are the difficulties and impossibilities of Barrel Chrome?
2) What are the important factors and constraints I need to notice during the initial stage of design?
3) Any idea of increasing cathode efficiency of Chrome plating?
4) Any conventional barrel chrome process to refer?
5) Any further information that I can gather?
Thanks for advice and suggestion.
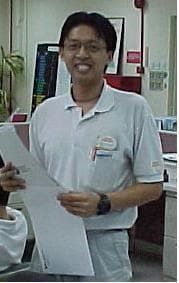
Chee Hong, Lee
- Singapore
2001
A. Dear Mr. Lee,
I have heard a self regulating mix catalyst bath containing Silicofluoride and sulphate gives somewhat higher current efficiencies as compared to a conventional chromium bath. There are proprietary chemicals out there and easily available in Singapore.
Regards,
SK Cheah [returning]- Penang, Malaysia
A. Barrel plating chrome is virtually impossible, but if you search the archives you will find someone that swears it can be done with his special equipment. Consider switching to electroless nickel. It will be a lot cheaper and easier if it can be used as a substitute.
James Watts- Navarre, Florida
A. Hi. Decades ago I visited a shop in Newark, NJ which specialized in hexavalent barrel chrome plating of components for Papermate pens. They simply used very small loads in conventional plating barrels, but did not reveal what rotation speed or other tweaks they employed. They were by far the best in the area, yet the percentage of rejects after 100% inspection was something like 20%. It's not so much that the theory is impossible, but that employing it as a practical production process with a manageable percentage of rejects has proven virtually impossible :-)
There are shops today who do barrel chrome plating (Whitaker Finishing in Ohio, for example), but their sales information does not reveal whether it is hexavalent or trivalent chrome. Please, no comments pro or con about that shop or any other finishing shop; please keep the discussion technical and non-commercial ( huh? why?). Thanks.
Regards,
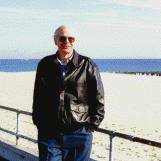
Ted Mooney, P.E.
Striving to live Aloha
finishing.com - Pine Beach, New Jersey
Multiple threads merged: please forgive chronology errors and repetition 🙂
Q. We have gone through your web site and tried our best to locate Bright Barrel Chrome Plating system. Unfortunately the above said system is not included in your web site. Presently we are doing only barrel Bright Nickel plating on our parts. We are interested to improve the quality of the system. Would you like to guide us in this respect?
Thanks and Regards,
Ishtiaq Hussain SiddiqiElectroplating Services - Karachi, Sindh, Pakistan
2003
Q. Hello. I want to know if barrel chrome plating is really possible or not? We plate small iron rivets with Ni and Cr with old methods of binding with copper wires to suspend in the bath. But barrel plating may be the easier way and save time & manpower. Is there anybody who really can do it? If yes, then can you help me to understand the mechanism and procedure of barrel chrome plating? I'll be very thankful to you.
GURMEET S [last name deleted for privacy by Editor]plating shop - LUDHIANA, Punjab, INDIA
2003
A. Hi Ishtiaq, Hi Gurmeet. Reliable chrome plating in a barrel has been sought for decades. Some specialized machinery like high centrifugal force barrels have been sold for the purpose. Equipment manufacturers have tried multiple approaches.
The state of the art 45 years ago when I started in this industry was to carefully develop a semi-workable procedure based on using standard plating barrels with very small loads, fully expecting a huge percentage of rejects, and then hand sorting to find the good ones. I believe the state of the art today is essentially the same :-)
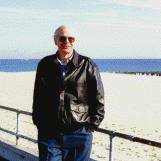
Ted Mooney, P.E.
Striving to live Aloha
finishing.com - Pine Beach, New Jersey
2004
A. Barrel Chrome plating has been accurately described by Mr Mooney. The system remains imperfect, with a great sensitivity to small factors which, as you know better, are all labor oriented aspects. If you wish to finish barrel Nickel Plated components with a Chrome finish there are three possible options
1) Wire the components which you are doing then Chrome.
2) Use a Barrel Centrifuge Chrome system as described by Mr Mooney.
3) The Third alternative is interesting:
This is an alloy of Tin and another metal. The Work after plating acquires a chrome look. It is plateable in the barrel. It has been done on a number of small articles where the hardness of chrome is not a major issue and where appearance plus ease of plating in a barrel is the major factor. Timings and operations are nearly similar to running Nickel Barrel operations. If Regards,
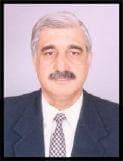
Asif Nurie [deceased] [deceased]
- New Delhi, India
With deep sadness we acknowledge the passing of Asif on Jan 24, 2016
2004
Multiple threads merged: please forgive chronology errors and repetition 🙂
Facility for Hard Chromium Barrel Plating Equipment
RFQ: We are manufacturers of Hosiery Knitting Needles made out of Spherodized Annealed High Carbon Steel having carbon contents 0.5%. Kindly let us know as to whether we can do hard chrome barrel plating on our product.
Secondly, suggest names of manufacturers of such Barrel Chromium Plating equipment along with raw material suppliers. This may be treated as MOST URGENT and revert back IMMEDIATELY.
VIKRAM KUMARPlating Shop - Ludhiana, Punjab, India
2004
Ed. note: This RFQ is outdated, but technical replies are welcome, and readers are encouraged to post their own RFQs. But no public commercial suggestions please ( huh? why?).
![]() |
Barrel chrome plating with trivalent chromeQ. Fellow finishers, It's nearly impossible to chrome plate (Hexavalent) using the barrel, has anyone out there tried using trivalent electrolytes? Some proprietary trivalent electrolytes boast of improved or excellent covering and throwing power, non-sensitive to white staining and more tolerant to break in contacts. What would be the strength and weaknesses in using trivalent electrolytes for barrel plating? Thank you. SK Cheahconsumer electronics mfgr. - Hong Kong, PRC 2003 Q. I am also interested in this line of possibilities and have read that the hexavalent chrome is very difficult. But what about the trivalent chrome systems? General literature seems to treat it more like nickel plating with good throwing power and no burning and nickel plating can be very successful in a barrel. Is anyone barrel plating trivalent chrome? Eric EricksonElectroplating - Spokane, Washington 2005 A. Hi, Cheah; hi Eric. You are right, if you want to chrome plate the parts in a barrel, you are pretty much limited to trivalent chrome (and I've heard no specific success stories), or a chrome substitute like tin-nickel or tin-cobalt. Regards, ![]() Ted Mooney, P.E. Striving to live Aloha finishing.com - Pine Beach, New Jersey Q. Does the use of this alloy [that Asif mentions] provide the strengthening that results from applying chrome to mild steel? Reuben Loganmetal finishing - Cicero, Illinois August 13, 2009 A. Hi, Reuben. Decorative chrome plating is millionths of an inch thick and contributes no mechanical strength; it is too thin to contribute much hardness. Aesthetics & corrosion resistance are its "strength". The aesthetics and corrosion resistance of the substitutes are not equal to chrome; the customer must judge whether they are good enough. Good luck. Regards, ![]() Ted Mooney, P.E. Striving to live Aloha finishing.com - Pine Beach, New Jersey Q. My customer is not specifying the reason for the chrome plating and did not allude to a decorative issue. Where can I learn more about the process mentioned by Mr. Nurie? Reuben Logan [returning]metal finishing - cicero, illinois August 14, 2009 A. Hello again, Reuben. All major suppliers of plating processes offer their own sorts of "chrome substitute", whether it be trivalent chrome, cobalt, or tin based. Any local plating process distributor will have at least one brand of substitute to offer to you. Obviously, no substitute can ever offer all of the properties of what it is replacing :-) Good luck, ![]() Ted Mooney, P.E. Striving to live Aloha finishing.com - Pine Beach, New Jersey August 2009 |
Solution composition for barrel chromium plating
by George Dubpernell"
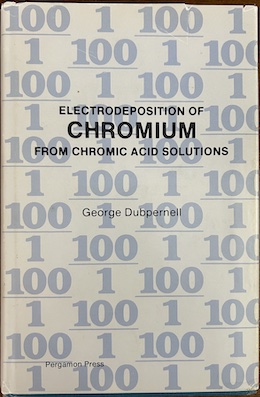
on eBay or Amazon
or AbeBooks
(affil link)
Q. I WANT TO DO BARREL CHROME PLATING. WHAT ARE THE MAIN REQUIREMENTS OF BARREL CHROME PLATING, AND WHAT IS THE MAJOR DIFFERENCE WITH RESPECT TO COMPOSITION IN BARREL AND RACK CHROME PLATING.
UMER FAROOQ- LAHORE, Punjab, PAKISTAN
2003
A. Hi Umer. Your question is somewhat abstract in that you haven't told us what you know about the main problem of current break. Nonetheless, barrel chrome plating is more a laboratory curiosity than a proven industrial process. I have known people who have spent their life at it and never achieved a remotely acceptable reject rate. The composition is probably not the central issue, it's how you are going to avoid breaking current. Still, as mentioned higher up in the thread, Dubpernell has some suggestions about solution composition. Further, Weiner & Walmsley's "Chromium Plating" .
discusses the possibility of cold chrome plating in a barrel, and also includes a 3-page section on "Articles in bulk; automatic plants". Good luck.
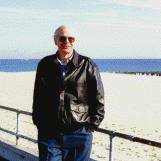
Ted Mooney, P.E.
Striving to live Aloha
finishing.com - Pine Beach, New Jersey
Spiral type barrel plating equipment
Q. I need chrome barrel suitable to plating 1 inch square articles. We have come to know about the spiral type barrel for chrome plating; my queries are below:
1- How does it work?
2- What is source of current inside the barrel during chrome plating to the objects being plated?
3- What is ratio of chemicals and other organic compounds and current density?
4- Please give us the information about the designing and size of required barrel.
Manufacturing - Ali pur chatta, Punjab, Pakistan
A. Hi Amjad. How did you come to know of it, and what did you learn about it? And what patents are extant -- people cannot help you violate patents if what you are speaking of is a patented machine. Although there have been many attempts at hexavalent chromium plating in a barrel, all have enjoyed only limited success.
If you will entertain proprietary trivalent chromium plating, then George Shahin's article "Barrel Chromium Plating from a Trivalent Chromium Electrolyte", published in the August 1992 issue of Plating & Surface Finishing, should answer most of your questions. And it also briefly describes seven early designs of barrels for hexavalent chromium plating. British patent 351,168 (1930) sounds something like what you are describing. Best of luck.
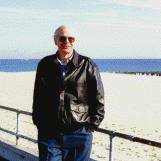
Ted Mooney, P.E.
Striving to live Aloha
finishing.com - Pine Beach, New Jersey
Is hexavalent or trivalent barrel chrome plating more promising?
Q. Gentlemen,
I've read your posts about the challenges of chroming in a barrel. I understand one company in Ohio has proprietary means to accomplish this, though I believe they are performing hexavalent if that makes any difference compared to trivalent. Is altering the inside of the barrel with strategically positioned danglers part of the equation?
I am attempting to barrel plate steel padlock assemblies with a trivalent black chrome recipe and haven't yet chosen a vendor for the chemicals, hoping to get their insight for a process that works with their recipe. My current assemblies are rack plated with black hexavalent chrome. I will install a complete new line for the process based on the requirements that will best give the plating consistency. (If I have to rack I will do so begrudgingly).
Alternatively, I've seen photos of black zinc nickel that look promising but as these are hardware items subject to both aesthetic and mechanical requirements, the chrome layer has a positive edge.
This is a greatly informative website. Thank you for your advice.
Owner - Hazel Park, Michigan, USA
February 10, 2014
A. Hi Patrick. Although you've read some posts here about chroming in a barrel, we have recently consolidated many threads into the dialog you see, so you might give it another quick glance and check if anything here that you didn't see before helps.
Earlier on I mentioned seeing hexavalent chrome plating being done in a very conventional polypropylene horizontal barrel, with very small loads and atrocious reject rates, but it was so long ago that I can't swear the barrel had danglers as opposed to some sort of button contacts.
If you can't use a proprietary chrome substitute like tin-cobalt, I think trivalent chrome simply HAS to be more practical than hexavalent because it simply can't be less :-)
Regards,
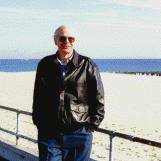
Ted Mooney, P.E.
Striving to live Aloha
finishing.com - Pine Beach, New Jersey
Q, A, or Comment on THIS thread -or- Start a NEW Thread