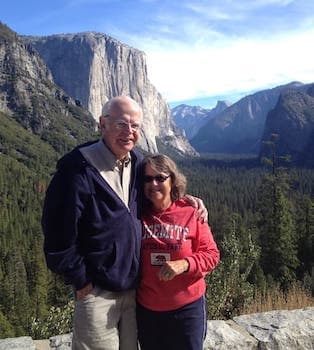
Curated with aloha by
Ted Mooney, P.E. RET
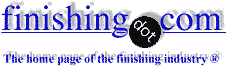
The authoritative public forum
for Metal Finishing 1989-2025
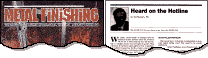
-----
Hard Anodizing Defects: stains, flow marks, color problems
finishing.com is possible thanks to our supporting advertisers, including:
Aluminum & Magnesium Finishing, with special expertise in diecastings and large parts
Readers may be interested in our "Intro to Anodizing", which explains what anodizing is, how it is done, and the various types.
Q. Brand new Kawasaki motorcycle with anodized forks...displayed a splashed on appearance. When attempted to remove...it clears then comes back 20-30 minutes later.
We feel it could be brake fluid from assembly at factory splashed down forks. Any ideas on a fix or done?
shop employee - Grand Rapids, Michigan
May 27, 2024
Tip: This forum was established to build camaraderie among enthusiasts through sharing tips, opinions, pics & personality.
The curator & some readers who publicly share their info will be less likely to engage with those who don't.
⇩ Related postings, oldest first ⇩
for Shops, Specifiers & Engineers
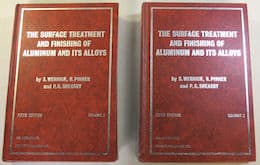
avail from eBay, AbeBooks, or Amazon
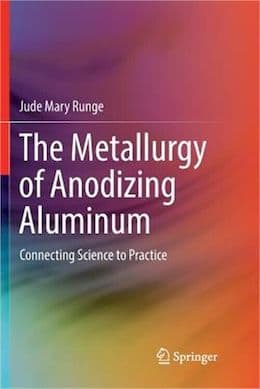
avail from eBay, AbeBooks, or Amazon
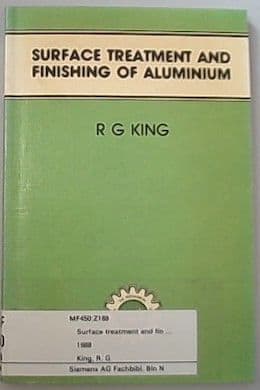
avail from eBay, AbeBooks, or Amazon
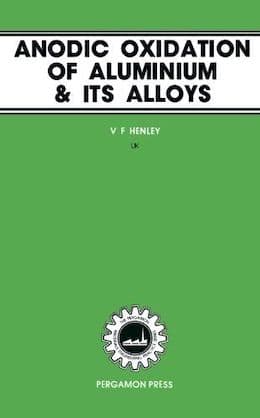
avail from eBay, AbeBooks, or Amazon
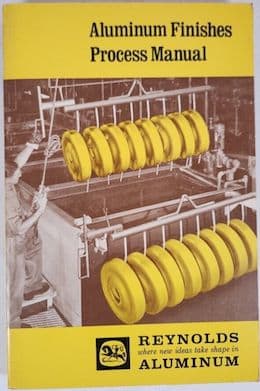
avail from eBay, AbeBooks or Amazon
(as an Amazon Associate & eBay Partner, we earn from qualifying purchases)
Q. We are having a cosmetic issue with some parts we produce for a Medical Customer. We are having an external supplier perform a Hard Anodize with a PTFE coating per AMS2482. The raw material is 6061-T6511.
Essentially what happens is that on one face (and only one face) of the component we begin to see stains below the anodize (which is dyed black). These stains only appear when the parts are held at certain angles under direct light, but have resulted in rejections from our customer claiming the parts are stained when in fact it appears the anodic layer is not compromised in any way.
I visited the supplier for an audit to try and determine what condition was causing these stains. During processing they keep the parts entirely vertical so there appears to be no justifiable reason for the stains to appear on only one side of the component. While I was unable to get an accurate photo of the condition we are seeing in the anodized state, when we had the anodize stripped you can actually see the stains quite well.
You may view a picture of the stripped component:
I am wondering if anyone else has encountered this situation before and if they have a solid fix to prevent this issue in the future. I appreciate any help you can offer.
Consumer (Quality Engineer) - Piscataway, New Jersey, USA
2007
A. Is there any reason for these "stained" area to have been work hardened more than other areas? Is it on the same place on each part? The anodic pore structure builds 90 degrees perpendicular to the (mini) surface. If that surface is roughened, then the pores build at various random slanted angles and reflect a different light. If that surface is work hardened, then the pores build with a random pattern which looks like a "stain"
Have the parts been tumbled, blasted,or sanded, any of which leaves a uniform surface to the naked eye, but imbeds hard trash into the soft (Kleenex-like) aluminum. Also, non-uniform manual blasting looks good to the naked eye, but looks awful after being magnified by the hard coat anodic build-up.
Come back with some more info, pictures if possible, surely some of us can crack this one.
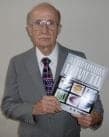
Robert H Probert
Robert H Probert Technical Services

Garner, North Carolina
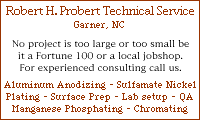
A. Jonathan
The symptoms you describe are characteristic of extrusions, although they usually appear as an "apple-core phenomenon" -- all the way through. If so, cut back on the etch time; and if permissible, dressing after anodize with a buff can help hide the flaws. Else manufacture from a wrought alloy.
- Colorado Springs, Colorado
A. Before I attribute this to material defect, I'd like to ask few questions:
1. It happens only on one side, as you said, does it happen on the same orientation? let say one part's surface A racked facing to you got this mark, another part's surface B (instead of A)facing to you got this mark too?
2. Have you checked condition of surface of the part after pretreatment but before anodizing? any abnormality?
a. if abnormal, you need adjust process (especially etching time, deox time) and method of mechanical polish.
b. if nothing wrong, then most likely it is material fault as I am sure you would find (more easier to find also) the mark after hard anodize but before black dye.
- Singapore
Q. The parts go through a brush finishing operation before going to anodize. That being said, the process is performed to all sides of the item and there is no reason for it to occur consistently on only one side.
Some responders have suggested that this might be attributable to improper quenching of the aluminum altering the crystalline structure. Is anyone aware of any screening that can be done before we go through all of the machine time and get all the way to anodize? My guess is there is no economical test that can be performed on a lot to lot basis.
- Piscataway, New Jersey
2007
"Flow lines" after black hard coat anodizing
Q. The flow lines cannot be seen with the naked eye, only under a 10X loop.
This is a military application, hardcoat black anodize under clear coat.
I do not think this is crazing due to the fact that there is no actual cracking or peeling.
I can only describe the lines as similar to a very faint pen line and every now and again the pen stopped and bled to look like a dot.It almost appears at though the solution is highlighting the imperfections in the material ... the turned finish is measured at about a 16 micro on our profilometer.
Is the plating defective?
manufacturer jobshop - Waterbury, Connecticut
February 28, 2009
A. Dean
You should consider the coating defective if it does not meet established acceptance criteria.
Is the coating failing in some manner?
- Colorado Springs, Colorado
Correct color of hard black anodizing on 6061-T6?
Q. For hard black anodize in 6061-T6, let me know the correct colour tone? Black or Dark grey colour?.
Please advise.
Regards,
Manufacturing - Singapore
July 16, 2009
A. Seems to me that black would mean black, so I would assume that if the term "black" is used, it would be implied that the coating would be dyed, as opposed to "natural".
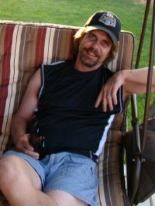
Marc Green
anodizer - Boise, Idaho
A. Because of it's naturally dark color, many people mistakenly assume that hardcoat anodize is dyed. Because of this confusion and to insure that they are getting hardcoat and not clear commercial anodize, often "black" hardcoat is specified. We always clarify this with our customer. Natural hardcoat on 6061 will appear dark grey to black (Class 1). To get a deep black, a secondary dye step is required (Class 2).
Chris Jurey, Past-President IHAALuke Engineering & Mfg. Co. Inc.

Wadsworth, Ohio
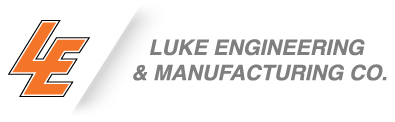
Q. We have started getting some staining on our solid parts we anodize. We only anodize to esthetics. Occasionally we get this stain and haven't been able to really determine what it is. All of our anodizing tanks are circulated from one mother tank. It is isolated to one anodizing tank so we don't think it's any other pre-treatment issue.
Solution:
Sulfuric 200 g/l
Aluminum 12 g/l
WM75LA 1%
Thanks in advance
pots & pans & trays - Spokane Valley, Washington, USA
June 18, 2013
A. I will guess that the rack hangs slightly different (3-axis) or the solution flow is not the same or the temperature varies in this tank more than the others.
James Watts- Navarre, Florida
Q. We hard anodize some parts for a customer of ours. They are turned 6061-T6 aluminum with a tight bore through the center and some set screw holes thru to the tight bore. The set screw hole and the bore both get plugged prior to hard anodizing.
The past couple of runs we have been getting the parts back from the plater with a white crust that is building up around the plugged holes. Is this caused by the plater not washing the parts? If not what is causing this and how can we fix the problem so we don't have to wash every part by hand. Thanks.
Ross Braastad- Ham Lake, Minnesota, USA
December 30, 2013
A. Hi Ross,
Most of the staining or salt build-up I have experienced in finishing operations generally is due to residual acidity or alkalinity or hard water rinsing mainly because of poor post rinsing.You may introduce a de-mineralized water rinse preferably hot before drying besides the usual counter-flow or cascade rinses.This may help avoiding corrosion or water mark after processing.
Good luck!
Ramajayam
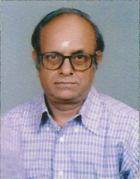
Subramanian Ramajayam
consultant - Bangalore, India
January 9, 2014
![]() |
A. Obviously the plugs are leaking, then, as Rama said above, alkali bleeds in, then acids bleed in, then salts bleed out. ![]() Robert H Probert Robert H Probert Technical Services ![]() Garner, North Carolina ![]() A. HELLO ROSS. - GUADALAJARA, JALISCO, MEXICO |
Cloudy stained hardcoat anodize
Q. I recently picked up a batch (72) parts from my local metal finisher. I specified:
Hard Coat / Black w/Teflon .002 (do not exceed .2672" on shaft / .2665" min.) (.2672/.2665) Rack with 4-40 threaded hole in stem 'only'
The raw material is 6061 and I hand deburr and polish these parts to soften the edges more. As a result of the polishing, the part has a nice clean shine. They were then cleaned in the ultrasonic cleaner, rinsed in clean water and hand dried before placing them in the parts box.
When I picked them up at the plant, I did a quick inspection. I found the parts to have cloudy staining and some even had finger prints on them. I brought this up immediately. They told me that was the PTFE. They tried to remove it and failed. And told me the only way was to buff it off. I don't think it was and feel there was something wrong in the process. I am a one-man shop and these parts are serious loss due to cosmetics.
What could have happened here? Is there any resolution?
Bill MilashiusOwner. - WHITE BEAR LAKE, Minnesota USA
November 2, 2018
Ed. note: This RFQ is outdated, but technical replies are welcome, and readers are encouraged to post their own RFQs. But no public commercial suggestions please ( huh? why?).
A. The water dip PTFE is a very expensive product and requires extreme care. Obviously floating soil has messed up the clarity of the coating, probably because of too many parts drag-in along impurities. What can you do? You need to contact the supplier of the PTFE for advice on how to recover, I cannot post his name here. I tell my clients to filter the top of the tank frequently with cheese cloth to keep the solution surface clear.
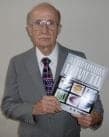
Robert H Probert
Robert H Probert Technical Services

Garner, North Carolina
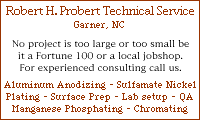
November 5, 2018
Q. I have contacted the manufacturer of the PTFE. They said it was water soluble and should come off with hot soapy water. That didn't work. Neither did soaking the part in MEK for an hour. I did put it in the ultrasonic and it pulled the dye out, but still had the staining. The maker said if a piece of tape would stick to the part, their product was not on this part. I did this and the tape stuck.
Could this be a result of poor contact with the part while anodizing" Or a gradual loss of contact with the part over the process time?
- White Bear Lake, Minnesota
November 7, 2018
A. Hi Bill- Oh man what a mess, that is a huge bummer after putting so much time into your parts. Couple things to chime in here. There's more than one issue.
The fingerprints- If you were wearing gloves while handling and buffing your parts at all steps, I'd look at the plater's racking staff not wearing gloves- a big no-no on cosmetic parts, even more so when it's a highly polished finish. Usually it's not as big a deal on parts to be hardcoated since most of the time they will be caustic etched before processing, and lose enough thickness to get through fingerprint residue- chlorides and oils on the surface, neither of which you want going into an ano tank on parts - but you buffed and then ultrasonic cleaned yours before shipping to the plater, so they should have a clean surface. Based on your description of your prep steps, if you did not handle those parts without gloves at any time, IMVHO it is on the plater to remedy this.
Is a total strip and replate an option considering your dimensional requirements?
Also, were parts handled by any operator between hardcoat and PTFE dip, and how do they guarantee that the Sulfuric acid is completely removed from parts before immersion in the teflon tank? Water based PTFE suspensions are sensitive to pH and operate ideally at pH 9-10.
Gonna have to agree with Robert here that waterborne PTFE tanks are a very delicate thing. They attract soils and greases like moths to a porch light! I skim ours by hand regularly, let the skimmed off material settle out in a bucket, and literally throw away the top layer. It's just too twitchy to take any risk of oil contamination with that stuff, and it doesn't take much to cause problems! Those little bubble patterns around one of the features in your pics make me very suspicious of grease.
It might not be a bad idea to send out a couple test or scrap pieces- Same material, same deburr and buff process, same cleaning steps, same handling protocols- and ensure that the plater is in fact capable of running this process correctly before committing to a whole load of good parts. Even a few 6061 test panels polished to the same standards and sent out in pristine condition will tell you SOMETHING ...
Good luck!
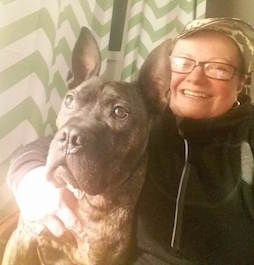
Rachel Mackintosh
lab rat - Greenfield, Vermont
November 7, 2018
Anodize defect or material (forged wheel)
Q. We are currently anodizing 6061 forged motor cycle rims. Parts are machined out of a forged billet and then polished. After gold anodize the rims look great, once the customer attempts to mount the tire a pattern appears. It goes away on some rims, but stays on others. The seal has been tested and is good.
anodizer - Minneapolis, Minnesota USA
February 27, 2020
A. Check for the thickness of the coating in the affected area, we suspect that the thickness may be low due to either (1) air (gas) gap, or (2) air agitation hitting that spot and displacing anodizing solution. Then, how do you test the sealing, is it ASTM B136?
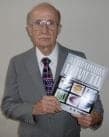
Robert H Probert
Robert H Probert Technical Services

Garner, North Carolina
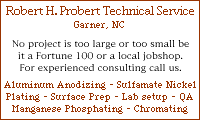
February 28, 2020
![]() |
A. Looks like something was sprayed on it, run down, collected and dried, if I had to guess - they pressure washed the wheels at some time and used the stuff meant to lift dirt up on painted surfaces - like brake dust on powder coated wheels on cars for instance, those liquids will damage anodized parts, won't be the first car wash to screw up bike parts like that Janis Ziemelis- Riga, Latvia March 1, 2020 A. Tom - GREEN MOUNTAIN FALLS, Colorado March 1, 2020 Q. We are using the blue dye stain test. The rims are ran on an automated line with hundreds of loads ran daily. We tested other product throughout the plant and nothing had this appearance. anodizer - New Hope, Minnesota USA March 2, 2020 |
A. We should separate source of problem;
1-during anodizing
2-during service
1-If your sealing bath or inorganic gold bath's pH balance out of limit and if you add ammonia
⇦ this on
eBay or
Amazon [affil links] to these bath during a bar inside of bath you may see this appearance. My advice: check the pH values often and not to add any chemical if there is a bar inside of bath ,you can add chemicals to bath empty times.Also these additions should be diluted.
2-anodizing layer is robust between pH 4 and pH 8. If you use some chemicals which out of these values like high alkaline detergent derivatives for washing, cleaning you will see the similar appearance as other contributors mention. Also, oily chemicals causes similar appearance.
Good luck
- TURKEY,sakarya
March 3, 2020
Q. Hello
I have a part that is made out of 6061-T6 Aluminum.
Before it went out to coating it looked uniform and smooth. After Hard coat black anodizing it looks faded in the center with swirls almost like tool marks. I do not know what is happening, because there is a second part that was made at the same time that looks fine. Is it the metal?
The finisher said it is a material issue.
Any help would be appreciated we have been wracking our brains here.
Josh Torres- Rochester New York
August 24, 2021
A. Seems the second part made good contact and the first part broke contact and partially chewed away. Tell us the anodic coating thickness on each part.
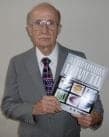
Robert H Probert
Robert H Probert Technical Services

Garner, North Carolina
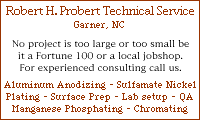
A. Hi Josh,
Yup that's a defect that is impossible to have come solely from the anodize process... it just makes it more obvious as the caustic etch prep bares the sins of the mill. I always strongly encourage our customers, and anyone working with extrusions, to remove the outer mill layer mechanically prior to sending for anodize, whether through blasting, machining, or even sanding to the desired finish with alox grit. It might take some experimentation tp determine how deep the surface defect goes. Granted, some stock has defects deeper than a quick once-over will remove, but it looks like you could get serious improvement from a little extra prep.
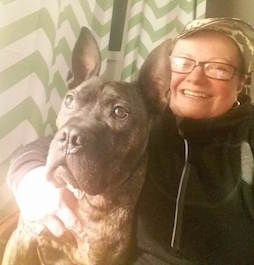
Rachel Mackintosh
lab rat - Greenfield, Vermont
combo magnetic & eddy-current coating thickness tester

on eBay or
Amazon
(affil links)
![]() |
Q. Our Print calls out for .025 mm build up and then Teflon coating. - Rochester New York A. Josh - Green Mountain Falls, Colorado |
Q. These are photos of finished parts --
They were fly-cut on the main flat surface and exhibited zero cosmetic issues. Subsequent to being type III anodized, these marks appear, erratic from part to part. The tapped holes on that surface are thru. Plater blames the foundry and vice versa.
Any help would truly be appreciated!
- Webster, New York
January 24, 2024
A. I am guessing that these are castings. If so, this is likely porosity which is exposed by the etching and/or hardcoat process.
Chris Jurey, Past-President IHAALuke Engineering & Mfg. Co. Inc.

Wadsworth, Ohio
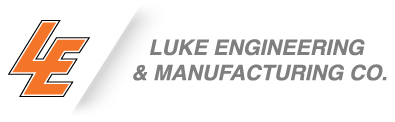
January 26, 2024
Q, A, or Comment on THIS thread -or- Start a NEW Thread