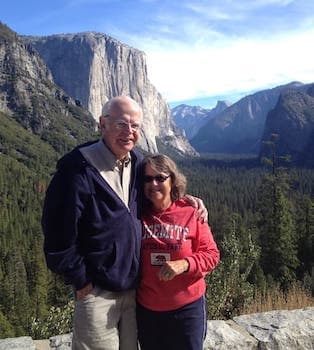
Curated with aloha by
Ted Mooney, P.E. RET
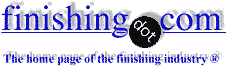
The authoritative public forum
for Metal Finishing 1989-2025
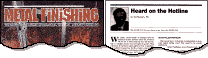
-----
Aluminium and Copper Joints
Q. Sir,
in our rectifier we are using aluminium busbar and copper bus bar.
the size of aluminium bus bar is 8inch x 1/2 inch three together
.
the copper is 4inch x 1/4 inch . The current carrying capacity 4000 Amps. dc and voltage is 24 vdc . The problem that we are facing is joints are getting heated up . There are six bolts for joining . please suggest as to what should be done in order to reduce heating effect
production - Jamshedpur, Jharkhand, India
2007
![]() |
A. Heat-up at joint area is because the bolts and nuts, I guess you use ss. John Hu- Singapore 2007 2007 A. Probably, oxide on the aluminum surface resulted in electrical resistance causing heating and further oxidation... I will presume that the 3 aluminum bars are interleaved between 4 copper bars (minimum for 4000 Amps), perhaps in a right angle connection, and that this joint is compressed together with a single set of 6 bolts. - Goleta, California ![]() Rest in peace, Ken. Thank you for your hard work which the finishing world, and we at finishing.com, continue to benefit from. |
A. Dear Kamaljit Singh Gill ,
Check the following points,
1) 8 x 1/2 aluminium will carry around 3000 amps current. You are using 3 bus bars that means capacity will be 9000 amps
2) 4 x 1/4 copper will carry 1000 amps current,so increase the no of bus bars up to 4, because you have to carry 4000 amps current so you need 4 bus bars of copper.
3) At joints there will be resistance because of air gap, ensure that all bolts are tight.
You implement this you are problem will be gayab......
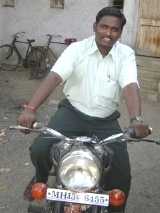
Vishwas Nangare
motorcycle accessories mfgr.
- Aurangabad, Maharashtra, India
2007
Q. Sir,
We are using mild steel nuts and bolts to hold aluminium and copper bus bars. As Mr. John Hu.
I guess it would be the cause. I would request Mr.John Hu to suggest which coated bolts I should use to eliminate the problem of AL-CU joint heating .The joint is carrying current of 3500 Amp. DC and voltage is 24 VDC.
regards
K.S.Gill
- jamshedpur,jharkhand, India
2007
A. Do as what Mr. Ken Vlach say,but I still recommend you to plate the bolts and nuts with tin too, not use ss, let alone mild steel, doing so you will greatly prevent the contacting area from oxidation or corrosion.
John Hu- Singapore
2007
A. RESISTIVITY OF ALUMINIUM AND COPPER IS DIFFERENT. SO KEEPING THAT IN MIND WHENEVER THERE IS AN CHANGE IN RESISTANCE OCCURS IN TNE PATH OF A ELECTROMAGNETIC WAVE REFLECTION AND REFRACTION OF WAVE OCCURS DUE TO WHICH CHANGE IN VOLTAGE AND CURRENT LEVEL OF CONDUCTOR OCURES WHICH CAN UNBALANCE THE SYSTEM .. (LIKE HEATING )
SO WHY WE GO FOR THIS TYPE OF JOINTING?
PLEASE GIVE CLEAR BASIC IDEA ABOUT IT.
Electrical Engineer - RAIPUR, CHHATTISGARH, India
May 24, 2008
Q, A, or Comment on THIS thread -or- Start a NEW Thread