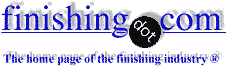
-----
Gas pits in nickel plating
Nickel plating, how much SLS for wetting agent?
Q. I'm a home hobbyist doing watch repair. Sometimes I have to strip and re-plate wrist watch cases. The cases are brass, which I first copper plate - quite thickly if there are deep pits/scratches to fill. After polishing I nickel plate using a Watts solution.
I try to keep the temperature at 60 °C, and use an aquarium air line to give vigorous aeration.
I plate about 15 microns thick - I have never been able to find out what thickness watch cases are plated in nickel.
The problem is that I am getting pin prick holes. They are not really noticeable from distance, but watches are something people tend to look at closely.
I know there are many reasons for pin prick holes. I thought adding a wetting agent - Sodium Lauryl Sulphate would help. I'm struggling to find what concentration of SLS to add - I've seen a large range of figures suggested. My guess is 0.1-0.2g/L. Is there a problem if I use too much?
- Watford UK
October 5, 2024
A. Hi Mike,
I don't know the standard, if there is such a standard, for nickel plating on watch cases, but 15 micron strikes me as quire reasonable. It is the nickel thickness suggested by ASTM B456 and MFSA for 'moderate" exposure (although those standards are for nickel-chrome plating rather than nickel only).
Yes, too much wetting agent can be a problem as related by Don Baudrand in thread 25885, for example. Your starting point sounds fine, but it's really not a question of the concentration of SLS, it's a question of its effect. People shoot for a surface tension of about 24-30 dyne/cms as described on this thread which we appended your question too.
The first step is to look at the pits with a loop and verify that they are shiny and hemispherical. If they're not, they're not gas pits. If they are gas pits, lack of cleanliness and freedom from oil might also be a problem not just surface tension.
Luck & Regards,
Ted Mooney, P.E. RET
Striving to live Aloha
finishing.com - Pine Beach, New Jersey
⇩ Related postings, oldest first ⇩
Q. I have a problem with a bright nickel bath :
nickel metal 70 gr/lt
nickel chloride 65 gr/lt
boric acid 45 gr/lt
saccarine 5 gr/lt
allyl-sulphonate 8 ml/lt
PPS 70-90 ppm
propargil alcohol 5-10 ppm
pH 4,5
temperature 60°C
surface tension 30 dyne/cm
cathodic current density 4 amp/dm2
- it's not a cleaning problem
- it's not a substrate problem
- we have this problem on the flat surfaces
- we use a double anodic cover and a 2 micron filtration system (20 turn over/hour)
- we use Venturi system
- we haven't iron or other metallic contamination
- the problem increase with a stronger agitation of the solution
- random distribution at all current density
please help me!
finishing shop - Firenze, Italia
2007
A. I don't see any wetter in your formulation.
You should use a wetter which serves as an anti-pit.


Sara Michaeli
Tel-Aviv-Yafo, Israel
![]() |
A. 24 dyne/cm will work better. ![]() Jeffrey Holmes, CEF Spartanburg, South Carolina A. Are you using any wetting agent? Also, I note that you are filtering at 20 turn overs per hour - I would consider this very high and only to be used in special circumstances. This high turn-over, coupled with the use of venturi, could cause your problems, especially if the dulling is associated with the venturi. When the electrolyte is moving too fast, the effects of additives such as brighteners are nullified. Try reducing the filtration rate to about 8-10 per hour and moving the venturi to an area where they do not impact on the workpiece ![]() Trevor Crichton R&D practical scientist Chesham, Bucks, UK |
Thank you all
we use a classic wetting agent to reduce the surface tension to 30 dine/cm
we tried to reduce it to 24 and we had no results.
Thank you Trevor
decreasing the Venturi agitation the bath works better but we need more brightener (PPS + propargyl alcohol) to obtain the same leveling effect so, by our experience Venturi increase the leveling effect
I agree with you that the problem is too much liquid movement but only STOPPING the Venturi I have no pitting and so I lose the Venturi benefits
we work on fashion accessories and we need mirror plating
so the question is :
can I use Venturi without having pitting
sorry for my English
regards,
- Firenze, Italy
A. How about seal leaking and ultra small air bubbles are pumped into the solution. I have never seen it, but there are literally hundreds of people that have had this problem.
James Watts- Navarre, Florida
A. My favorite brightener for nickel is sodium saccharin - it takes only about 0.5-1.0 g/l to give a good brightness and it hardens the nickel as well. However I see that you also use saccharin, so it may be worth asking your supply house for a better brightener. You can also use butyne diol or coumarin.
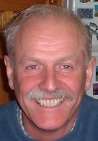
Trevor Crichton
R&D practical scientist
Chesham, Bucks, UK
2007
Q. I use much more saccarine (3-5 gr/lt) and I add propargil alcohol
(or butyne-diol) + PPS because I need a strong leveling. This is a standard range of brighteners in our application field. I have not the leveling I need with your formulation.
Have you got any other ideas ?
Thank you
- Firenze, Italy
A. Pitting is most related to Filtration because the Pump is install outside the Plating tank.
The Pipe leaks air in and get mixed in the Pump .
Test: Get a 600 to 1000 ccm beaker [beakers on
eBay
or
Amazon [affil links] , collect the Solution from the Tank and hold Quick!
Against bright light .
If any Air is mixed, the solution is like milky and take 10 to 30 seconds to clean
Into a clear Bath solution
If not milky, any fine Air going up like Champagne is a sign.
- Paderborn, Germany
Q. Yes, I checked pump filtration system and I'm sure that there isn't fine air in the solution (obviously not milky while working).
Fabio Crolli- Firenze, Italy
A. Lower your bath temperature to 55-58 degree C.
hydrolysis would happen to nickel if temperature too high.
- Singapore
![]() |
A. John, ![]() Trevor Crichton R&D practical scientist Chesham, Bucks, UK Q. I tried to take the temperature down to 58 - 55 - 50 degrease but the pitting was the same. Fabio Crolli- Firenze, Italy |
![]() |
I agree with Trevor and I want clarify that I'm using a sulphate (not sulphamate) bright nickel - Firenze, Italy ? Fabio, ![]() ![]() Sara Michaeli Tel-Aviv-Yafo, Israel |
A. I know you originally said that most of the more common causes of your problem have been eliminated, but the most common causes of pitting are: no or insufficient wetting agent; wrong pH, too little agitation; too much agitation, bath contamination, surface contamination, dust or other debris in the tank. As a long shot - check to see if your anodes are Ok; they may be producing sludge that is getting into the bath and then onto the plating surface and causing pitting. Otherwise, go back and re-check all the process parameters and the condition of the tank. What happens if you do a Hull Cell ⇦ huh? test on the bath - if it still pits, it is the solution; if it doesn't - it is the process. If all else fails, you may need to dump the bath and start again, after cleaning out the tank.
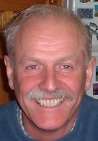
Trevor Crichton
R&D practical scientist
Chesham, Bucks, UK
A. Fabio,
We use what appears to be essentially the same bath chemistry and have the same issues from time to time. What we have found is this:
Make sure the acids in the pre-plate cycle are fresh and changed out on a regular basis, try dumping the your acids and see if this lessens the pitting problem.
The other issue may be contamination from breakdowns of the PA and the PPS these would tend to "plate out" the more violent the agitation.
The other issue is dependent on how often you add back your secondary brightener component. If you add back say 1000 mLs every 1000 amp/hours cut this down into smaller more frequent adds of 100 mls every 100 amp/hours for example. This keeps a good amount of PA in the bath at all times which is what will really give you a nice leveled deposit.
I would still do at least a heavy carbon treat (test out in the lab?) remembering that PPS breakdowns are very hard to remove.
plating shop - Hbg, Pennsylvania
A. Fabio Crolli
Do you say what the problem is only in flat surface in concave part do you have the same problem, because I have the same problem additional to this some areas it have distortion of the nickel film.
Personal - Mexico
2007
A. Jose Cordova,
If you are routinely running an electroforming bath, you must have a good book and perhaps take a course in electroforming. There are several ways to control stress in a sulfamate bath (this is the main reason to use it). Temperature, amperage and pH variations all move the stress curve. You can literally tailor your part to zero stress. Get a recent copy of the Metal Finishing Handbook or any of the "must have" books suggested here.
Monterrey, NL, Mexico
2007
A. Hi Jose.
You've received lots of good advice from a host of experts, and since none of it has solved the problem it may be time for off-the-wall ideas. I once visited a nickel plating jobshop which did not do their own polishing, but received the product from a polishing shop and suffered periodic gas pitting. They swore that the problem was that the polishing shop sometimes overdid it and actually melted tiny dots of nylon from the scotchbrite onto the parts, which caused gas pitting. I don't give it much credence, but since you've tried everything else :-)
Luck & Regards,
Ted Mooney, P.E. RET
Striving to live Aloha
finishing.com - Pine Beach, New Jersey
Q. In the process of electroforming using Nickel Sulfamate, somebody know the methodology to the determine the concentration of the boric acid in the solution ?
Jose G Cordova- Tijuana, Mexico
2007
A. Jose, the simplest way to analyse for boric acid is to take 10 mls of the nickel plating solution and dilute it with DI water to 100 mls. Take 20 mls of the diluted solution and put it into a 300ml conical flask; add 5-10 mls of mixed indicator (which is made from 1g bromocresol purple
⇦ on
eBay or
Amazon [affil links]
mixed with 0.5g bromothymol blue in 100 mls ethanol). If the solution turns yellow, titrate it against N/10 sodium hydroxide to a blue end point. If the solution is blue, titrate it against N/10 hydrochloric acid to a yellow end point. The colour of the indicator is pH dependent, so the starting colour will depend on the bath's pH. Then add 1.5 mannitol and the solution will turn yellow. Titrate this yellow solution against N/10 sodium hydroxide to a blue end point. The amount of boric acid can be calculated as:
mls N/10 NaOH X 3.1 = gm/l boric acid
The end point can be difficult to determine, so I have often diluted the original solution by a factor of 2, so the titration is done against 5 mls of bath diluted to 100 mls. The exact end point is also quite difficult to get, so I would recommend you practise it with known concentrations of boric acid and see just when you get the end point. I also recommend you shake the solution for about 45 seconds to make sure it doesn't revert back to yellow.
I have only limited experience of using 1,4-butyne diol as a leveler in a nickel bath, but I believe when it decomposes it does not form harmful by-products - this is one of its advantages. However, I do see you are using 65g/l NiCl2. This is almost certainly the cause of your stress. The problem with nickel sulphate baths is that you need the presence of a halide to promote anodic dissolution of the nickel. Most people use chloride as it is cheap and cheerful. However, it will induce tensile stress. You have two options; firstly replace the NiCl2 with NiBr2, or secondly, convert you system to nickel sulphamate. The beauty of nickel sulphamate is that you do not need chloride present if you use sulfur nickel rounds as the anode. Hence you do not get stress. This will also allow you to reduce the amount of saccharin you put in your bath. If you really insist on using chloride, then reduce it to 40g/l and it MAY solve your problem. My personal option would be to use sulphamate; - it may cost a bit more, but it will give you better quality plating and in the long run will save you money by reducing your scrap rate.
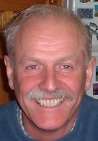
Trevor Crichton
R&D practical scientist
Chesham, Bucks, UK
Q. On the electroforming of Nickel the part it have deformation this is an effect of stress. I will like to know how reduce the stress in the plating this produce a distortion of the image.
Jose G CordovaPersonal - Mexico
2007
Q. I have a problem with a bright nickel bath: Cloudy-hazy deposition
nickel metal 70 gr/lt
nickel chloride 60 gr/lt
boric acid 45 gr/lt
saccarine 5 gr/lt
sodium allyl-sulphonate 7 ml/lt
1,4-butyne diol 40-60 ppm
propargyl alcohol 5-10 ppm
Ph 4,5
temperature 60
cathodic current density 3 amp/dm2
- it's not a cleaning problem
- it's not a substrate problem
- we use Venturi system
- we haven't iron or other metallic contamination
please help me!
Osman TURAN
- Izmir, TURKEY
October 26, 2010
A. Check your bath analysis and tell us what it is, not what it should be. I suspect the bath brighteners are out of balance.
You don't say what type of bath it is, but if it is sulphamate, I would drop the pH to 3.6-4.2 - it won't solve your problem, but it may help in the overall running.
- Chesham UK
Q. Hazy nickel deposit, I think high brightener or leveling component in brightener is too high. Run hull cell panel
"as is"then dummy the hull cell panel then run the regular
panel.
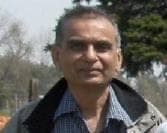
Popatbhai B. Patel
electroplating consultant - Roseville, Michigan
October 29, 2010
Q, A, or Comment on THIS thread -or- Start a NEW Thread