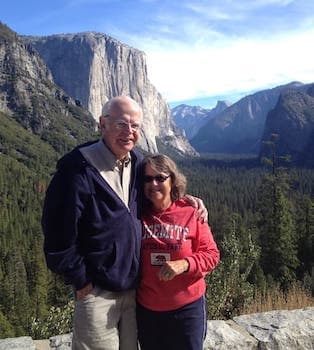
Curated with aloha by
Ted Mooney, P.E. RET
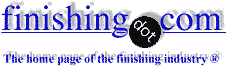
The authoritative public forum
for Metal Finishing 1989-2025
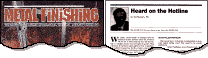
-----
Pitting in Nickel Sulphamate Solution after Adding Brightener
2003
Q. Hi,
I am conducting research on nickel electroforming in high-aspect ratio photoresist molds (plating inside 20 micron-thick by 3 micron-wide trenches), using a nickel sulphamate bath with the following constituents:
Nickel sulfamate: 500 g/L
Boric Acid: 40 g/L
Nickel Chloride: 10 g/L
Butyne diol: 0.1 g/L
Sodium saccharin: 1.1 g/L
Commercial wetting agent: 0.2 ml/L
pH: 3.5-4
I use butyne diol as a leveling agent and sodium saccharin as a stress-reducer and hardener. Before adding saccharin to the bath, the deposited surfaces are non-reflecting and have tensile stress. After adding sodium saccharin to the bath, the plated surfaces become much more smooth and bright, however, there are a lot of pits inside the narrow trenches. I almost doubled the wetting agent concentration but it did not help much. I also increased the solution agitation in front of the plated sample so that the pitting can be decreased, but this time the photoresist mold becomes destroyed due to very high agitation strength (I think the agitation must not be that strong). Also the plated surfaces have domed shape where the agitation strength is excessive.
What I observe that the surface tension of the solution increases so much after saccharin addition. The solution becomes sticky if it is dried on a surface. Does this mean I should add more wetting agent? What can be the possible problems with high wetting agent concentrations? Can the saccharin concentration be too high (If so, can I remove it by carbon filtering)?
I would be pleased if anybody can comment on the above situation and suggest a method to reduce the surface tension of the solution by some means. Thank you.
Ph.D. Student - Ankara, N/A, Turkey
I am suitably impressed that you would even try this. The most impressive work I have seen was this, in copper:
from Electrochimica Acta, Vol. 42, nos 20---- by L.T. Romankiw
It sounds like you are trying something just as about as impressive but in nickel.
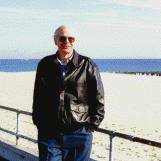
Ted Mooney, P.E.
Striving to live Aloha
finishing.com - Pine Beach, New Jersey
A. Pitting is often caused by incomplete cleaning of the surface, pits in the basis material, or organic contamination. Adding more wetting agent does not help and may act like an organic impurity. There are only a few wetting agents that are suitable for sulfamate nickel plating. (Sodium laurel sulfonate is one of the suitable surfactants) 1 gram/L saccharine seems too high to my. Try 1/2 that amount. Unfortunately saccharine is not easily removed by carbon treatment. Repeated peroxide and carbon treatment will lower the content some, and may have other benefits in terms of pitting.
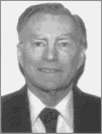
Don Baudrand
Consultant - Poulsbo, Washington
(Don is co-author of "Plating on Plastics" [on Amazon or AbeBooks affil links]
and "Plating ABS Plastics" [on Amazon or eBay or AbeBooks affil links])
Electroless plating
2003We machine rectangular grooves into silicon with a depth of about
200um and a width of about 30-50um. We want to deposit a highly conductive metal such as Gold, Platinum, Copper, Aluminum or something similar on the wafer and sloe in the grooves. We would like to have a thickness of about 200-500 nm. Does anyone know a technique to do that, which we do not have to develop ourselves?
Stephan
research engineer - Erlangen, BA, Germany
2003
Said, you are working very close to the limit of conventional electroforming technologies. The dimensions you give us are in the micron region, so you are literally in the realms of micro engineering. If you go much lower, you will be in nano-engineering and it is here that things start to go really strange. The technology you are trying to use is very similar to LIGA, as developed by the Institut Fuer mikrostrukturetechnik in Germany in the late 1980's and later modified and improved by Bell Laboratories as SCALPEL. In recent years there has also been a development called "Soft Lithography". You may well find it useful to look at the electroforming techniques used in these technologies.
My first comments on your problems are based on cleanliness; you say you are getting pits in the narrow trenches - these are only 3 microns wide, so the thing causing the pits is, at most, only slightly more than 2 microns wide. What is your filtration system? Can it remove such small particles? I would suggest you use sub-micron filters.
Secondly, are you using a Clean Room environment? If not, then you run the risk of contaminating your bath with atmospheric dust particles. It is even possible that your use of wetting agents could be making the effects of particulate contamination even worse, as you are providing a solvent sheath for them!
You do not give any details of the wetting agent, so the concentration details are almost irrelevant. I would perhaps suggest you use sodium laureth sulphate or sodium laureth sulphonate based systems. Sodium lauryl sulphate will give you lots of foam on the surface of the bath, so this may help keep any particles out of it. However, it is best to discuss this with your chemical supplier.
I note that you do not mention the operating temperature of the sulphamate bath. I would suggest, if possible you operate at as near to 70 °C as possible. If you exceed this temperature, the sulphamate will start to decompose into ammonia
⇦ this on
eBay or
Amazon [affil links] and sulphate and this will increase your stress. However, to obtain the lowest possible viscosity, which you may well need to get into these small grooves, you need to have as higher temperature as possible. The bath is leveled by butyne diol; this is a good system, but should be operated at about 8mM/L; higher concentrations can adversely affect the throwing power of the electrolyte. This will cause problems getting a good deposit down the bottom of the grooves. Other levelers include coumarin and Thiourea
⇦ this on
eBay
or
Amazon [affil links] , but both can be difficult to use and decompose to produce chemicals that adversely affect the properties of the deposit. Sodium saccharin is an excellent stress reducer and hardener when used properly, but (it is claimed)it is only effective as a leveler when the thickness of the deposit is over 150microns; below this it has detrimental effects.
You are clearly going for a compromise between hardness and stress, for a level of 1.1g/L should give you almost maximum compressive stress for your current density whilst offering a hardness of about 500Hv. I would not be concerned about this level, as I have used baths with more than that in it! However, you may want to consider using cobalt as a hardening agent.
I too have seen strange agitation effects and have noted that too high agitation can not only distort the deposit, but it can stop the additives working in the way you may expect. I have seen baths that usually give excellent lamellar deposits produce fully columnar deposits when the electrolyte flow rate is too high. These effects are caused by the Helmholz Double Layer being reduced to levels where the additives are unable to work in the way they are intended. You may well be better off reducing the degree of agitation. If the pits are due to gas bubbles, you should consider the orientation of your mandrel; try to have the depositing surface facing upwards, so any depositing gas bubbles can be easily released; you can perhaps enhance their release by careful agitation of both the workpiece and the electrolyte; also try using adductors to give more general agitation in the bath.
As far as Stephen's question is concerned, I would suggest he look at deposition techniques such as sputtering, PVD or CVD. These are all well tried and tested with the metals mentioned and are well within the range he requires.
I apologize for the length of this, but hope it is of some help.
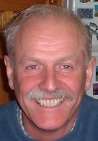
Trevor Crichton
R&D practical scientist
Chesham, Bucks, UK
adv.
"The Sulfamate Nickel How-To Guide"
by David Crotty, PhD
& Robert Probert
published Oct. 2018
$89 plus shipping
Q, A, or Comment on THIS thread -or- Start a NEW Thread