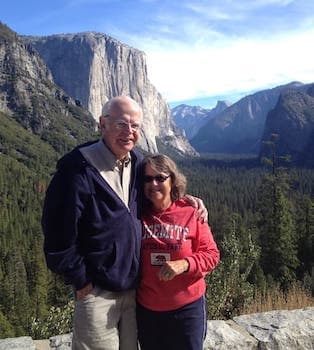
Curated with aloha by
Ted Mooney, P.E. RET
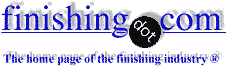
The authoritative public forum
for Metal Finishing 1989-2025
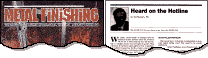
-----
Dissolved Aluminum in Anodizing -- How Much, Analyze/Titrate, Correct/Adjust
(to help readers better understand the Q&A's)
For the anodizing process to function properly, a proper balance of the ingredients in the anodizing solution is required. One of those ingredients is dissolved aluminum.
But the anodizing process continually dissolves aluminum. So it can be necessary to monitor the dissolved aluminum and take measures to reduce it. One of those measures is often to regularly remove and treat or discard a portion of the solution, replacing it with fresh acid/water.
Current question & answers:
August 11, 2021Q. I'm the new and only lab tech at my job (Chemist fired). I have been tasked with figuring out how much of what to add to bring this tank back to life.
I have a 790 gal hard coat anodize tank which we would like to decant but still maintain a 6 g/L Aluminum content. My free sulfuric acid content would like to be at 160 g/L but the range is 140-190 g/L.
My last titration results are as follows:
261.66 total acid
152.88 free acid
19.98 g/L Al (range is 3-20)
2.11% b.v. AANF
I know that we figure 19 gal/inch and 3.79 L/gal, but after that I'm lost
I've read many of your answers/explanations and was hoping you could help me? You [ed. note: Tina is addressin Rachel Macintosh] seem to not just answer but explain the why's and how's and it just makes sense when I read your interpretation.
Thank you!
TinaMarie
- Blairsville Pennsylvania
⇩ Related postings, oldest first ⇩
Q. Dear Sir /Madam,
It has been said that higher Al content (German belief: 12 g/L , American thought: 20 g/L ) in sulfuric anodizing bath has detrimental effects i.e. Higher required Voltage (at the same current density ), softer anodic oxide and nonuniform coloring. We performed anodizing on 1100 & 6064 in 24 g/L sol. with subsequent inorganic coloring in the lab, but saw no above-mentioned bad effects on colored specimens (No microscopic examination was done). Are there really any bad effect on oxide characteristic and uniformity of colour (excluding aluminum sulphate deposition on specimens)? What is the Al content upper limit and why?
BEST REGARDS,
Amir Koorosh Zarrabi- Isfahan, IRAN
2002
A. Hi
I think 12 g/l Aluminium sulphate is the maximum. Above this the solution loses conductivity and more voltage is needed to compensate for this. Also for colouring purpose we have to keep the aluminium sulphate under control.
- Auckland, New Zealand
May 3, 2011
A. Hi Amir. While there may well be Americans who think 20 g/L is good, I don't think that's the prevailing thinking. Just going by what I hear on these pages, 8 is about ideal, and more than 12-15 is thought to be problematical. Good luck.
Regards,
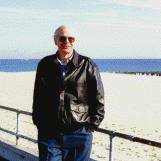
Ted Mooney, P.E.
Striving to live Aloha
finishing.com - Pine Beach, New Jersey
January 2014
A. Amir
We optimally run between 6-12g/L Al, because the higher your Aluminum content the more current you will have to apply to see anodize on the actual part not in solution. As you can see by my titration results, the Al content was almost 20g/L causing necessary decant and tank overhaul
My maths are getting confused so I asked for help with amounts to decant and start anew with ~6g/L Al.
lab tech- Blairsville Pennsylvania
August 20, 2021
Multiple threads merged: please forgive chronology errors and repetition 🙂
How to titrate for dissolved aluminum
Q. Could someone please advise their method for titrating the anodizing bath? The method that we have used for years seems very subjective to me, especially the aluminum content portion of the test.
Thanks in advance for any help you can give.
Regards,
Rick Watson- Greenville, South Carolina
2000
A. You are right, the aluminum results derived by calculation from free versus used acid titrations do not give repeatable and accurate dissolved aluminum results. Depending upon how you are controlling the bath and the frequency of additions the range of free acid versus used over time, etc. it may not matter, particularly if your processes depend upon a range of say 8-12 g/l of Al. One shop I worked at where we had tight process controls, we had AA performed weekly. Interestingly enough, they never matched the dissolved aluminum results reached from titration. Wet bench chemistry has an error of ± 5% right off the bat, depending upon the technique and the technician.
Ward Barcafer, CEFaerospace - Wichita, Kansas
2000
A. We recommend the same procedure as everyone else. SG measurement with a titration of the H2SO4. Plotting this on a graph yields the aluminum content. Another way is to use the back titration with CuSO4 and EDTA but that may be overkill. Really all you need is Al between 2-12 g/l for anodizing and the simpler analysis should give you that.
Lee BranchRichmond, Virginia
2000
Multiple threads merged: please forgive chronology errors and repetition 🙂
Anodizing bath with no dissolved aluminum
Q. What happens if anodizing bath has nil dissolved aluminum ?
Dado Macapagal- Toronto
2002
A. If nil Al+3 is present in your anodizing tank you find you will consume more electrical energy to create anodic oxide film on aluminum substrate. It is advisable to have 5-15 g/l, preferably 10 g/l Al(+3) in the sulfuric acid anodizing solution. If more Al(+3), then your electricity consumption will be higher resulting in difficulty for cooling the solution. It is advisable to use ion-exchange equipment to have constant Al(+3) in the solution.
Timur Ulucakaluminum extrusions & finishing - Istanbul, Turkey
2002
A. Aluminum oxide will always dissolve in sulfuric acid anodizing solution, thus, it's impossible to have NO ALUMINUM once the first part is immersed in the bath and power is turned on!
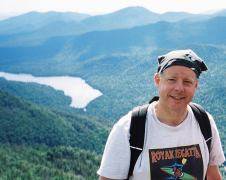
Milt Stevenson, Jr.
Syracuse, New York
2003
A. You should keep the aluminum around 12-16 g/l. if the aluminum gets too high you can decant half the tank then fill it with water, mix it good with air, run test, and then add sulfuric to g/l you require to run. Make sure you let the tank cool to the temperature you want to run at. Running with no or too low aluminum will give you too shiny a finish and you will not get the coating you need.
Kris Heim- Walkerton, Indiana
2003
How do I obtain 5-15 g/l dissolved aluminum in my electrolyte?
Q. Hello all you wonderful people at finishing.com. Long time, no chat! Things are progressing slowly after a small personal setback but things are good; it looks as though I am back in the aluminum anodizing race. All of the equipment is in place and I am working on mixing my initial bath batches. Exciting stuff! It has been a long journey and is sure to only get longer; however, I have prepared myself on many levels and invite the challenges and obstacles (I have so much more to learn). It should be an amazing learning experience and hopefully with proper judgement I can build a lasting small business.
This past week, the batch mixing has progressed without a hitch, up until this morning. Regarding the electrolyte, I fully understand that by volume the batch is to be made up of 9.3% H2SO4 and 90.7% H20, however, I am unclear on the dissolved aluminum content within the tank. I realize these are elementary questions for most of you so please bare with me. In the past I would always mix my H2SO4 into my H20 and disregard the dissolved aluminum piece of the puzzle. Though I never ran into any complications (that I recognized anyway) I feel that this is something I must understand before I move forward.
- How does one get the dissolved aluminum into the solution?
- How does one analyze the solution down the road to determine the dissolved aluminum content?
Lastly, I would like to thank Drew Nosti at AnodizeUSA [a finishing.com supporting advertiser]. I obtained my cathodes from Anodize USA and would like to mention the outstanding product that Mr.Nosti stands behind. The engineering behind Anodize USA's cathodes provided me with a simple to use, high quality product. Thank you for your support and advice Drew, and thank you for making such a product available, particularly to a small fry such as myself. Cheers!
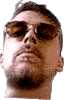
Daniel DeGueldre
anodizing shop entrepreneur - Ste. Anne, Manitoba, Canada
2006
A. To get 15% aluminium content into your bath, just dissolve the required weight in a beaker [beakers on eBay or Amazon [affil links] of sulfuric acid and add it to the tank. You may need to gently heat it to ensure it is all dissolved. Analysis can be done by titration, so look in a good analytical chemistry book.
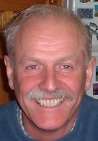
Trevor Crichton
R&D practical scientist
Chesham, Bucks, UK
2006
2006
A. With regards to the aluminum, it is my understanding that (on a theoretical level) the bath won't work without some dissolved aluminum. On a practical level, the minute you put parts in the acid you start getting some dissolved aluminum present and it starts no longer being an issue.
With regard to maximum concentrations: before beginning work for my company, it had been established that letting the dissolved aluminum get up to about 3 oz per gallon (22 g/l) resulted in really poor anodizing with the aluminum settling out of the bath and onto the parts. We then, for a while, just started a brand new bath with no dissolved aluminum whenever we went over 2 oz/gallon. Now we use a Anopur unit to filter out the dissolved aluminum and try to keep it at about 9 g/l (1.2 oz/gallon).
For testing purposes, see letter 38674.
You may also want to check out letters
30612,
22036,
12274,
5032. According to my notes you might find them interesting.
Good luck!
Compton, California, USA
A. I have recently started up a line here in Westminster and after running for almost 3 months I have finally reached 4.5 g/l AL in the sulfuric tank.
I had little to no startup issues, but then again Bob Probert and myself plated 10-15 runs of scrap 6061 and 2011 alloy aluminum before plating production parts the next day.
Purification systems are extremely expensive and I am shying away from that style right now although it is by far the best way to keep the Aluminum level at 9 g/l. I will decant my bath in half when I reach 11 g/l and then add fresh sulfuric and remake the bath.
This is only an option. Please make sure you have proper disposal methods before decanting the tank this way.
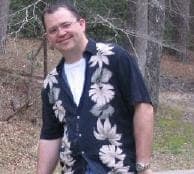
Ryan Cook
Toccoa, Georgia
2006
Multiple threads merged: please forgive chronology errors and repetition 🙂
"What happens if I let the aluminum concentration grow in the anodizing vat?"
Q. Or in other way, why must I decant my vat all the time?
My optimum parameters of operation are 145-160 gr/lt of sulfuric acid and the aluminum must be < 15 gr/lt. but you know?.. I have 6 months without any decant, the aluminum now is higher than 26 gr/lt and I don't see any visual problems in my finish... then why? (all of this under the commands of my boss who doesn't want to spend much money buying enough sulfuric to decant)
Maybe in a microscopic vision my coating isn't appropriate? or what?
employee - Quer´taro, Quer´taro, Mexico
August 23, 2011
A. Usually the solution does not show significant differences in behaviour until the Aluminium content has crossed 30g/l (i.e.: in my experience), BUT, after that, the time taken to achieve the same coating thickness starts to INCREASE and if you still continue to take no action, then the desired coating thickness becomes difficult to achieve (especially for higher thicknesses in the range of 80 microns or so ) - if your desired coating thickness is smaller say in the range of 25-50 microns , then it may take even longer to show any difference in behaviour.
Quality of coating may not be seriously affected, if we continue to maintain the coating thickness by prolonging the process for a longer time.Only a Salt Spray test ( or suitable tests as prescribed in the relevant standard or specification to which your coating is being carried out ) can verify the quality of the coating
I am not an Expert, like you find many of on this site, but the above is from my experience. I would be happy if some experts could also comment and maybe verify my opinions.
- India
August 29, 2011
A. Visual inspection by the unaided eye is not good enough for high reliability work. Boeing tops the dissolved aluminum at 21 gm/L and they are never dyeing. Dye suppliers limit the aluminum to 15 gm/L. The more "stuff" you trap in the tiny pore, then the less hydration (seal) takes place, then you lose corrosion protection.
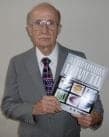
Robert H Probert
Robert H Probert Technical Services

Garner, North Carolina
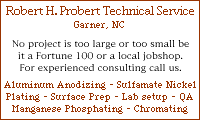
August 29, 2011
A. To add to the list of potential problems in letting your Al content exceed maximum recommended range would be adequate rinsing of the work (which is where Robert's comment comes into play), especially when it comes to subsequent dyeing steps. Anodized coatings are much more difficult to thoroughly rinse when the Al content in the anodizing bath is high.
At my operation, we set the limit at 12 gr/lt (albeit, we do mostly hardcoat)
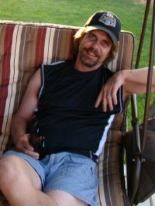
Marc Green
anodizer - Boise, Idaho
August 31, 2011
Q. Dear Friend,
How much should be the Aluminium concentration in Sulfuric acid anodizing bath? Does the aluminium in Sulfuric acid bath have any role?
- Abu Dhabi, UAE
January 22, 2014
January 23, 2014
A. Opinions will vary, but in my experience:
Hard Coat bath < 10gr/lt
Conventional anodizing < 20 gr/lt
Build up of Al causes rinsing issues, and also will begin to decrease the bath conductivity. Also keep in mind that as you're building up Al in the bath, you're also building up a lot of other unwanted elements that the aluminum is alloyed with. (Fe, Cu, Zn, Si, etc, etc)
At the same time, I believe it's a good practice to start with at lease 2-3 gr/lt in the bath. For a good consistent product, with repeatable results, decanting and replacing with fresh solution on a regular basis (keeping your Al content at a fairly consistent level) is the way to go.
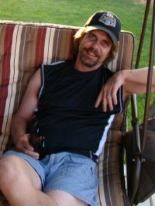
Marc Green
anodizer - Boise, Idaho
A. Hi Aijazullah,
I agree with Marc, except if you are working in the Aerospace industry the levels tend to be lower, usually between 5 and 8 g/l for hard and 12 to 15 g/l for conventional, dependent on who the customer is.
Aerospace - Yeovil, Somerset, UK
January 24, 2014
Q. Dear Friends,
Can you tell me how to eliminate the Aluminium content from the sulfuric acid anodizing bath?
- Abu Dhabi, UAE
January 30, 2014
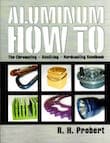
Aluminum How-To
"Chromating - Anodizing - Hardcoating"
by Robert Probert
Also available in Spanish
You'll love this book. Finishing.com has sold almost a thousand copies without a single return request :-)
A. Hi, Aijazullah. As you see, we appended your inquiry to a thread where it has been answered.
Some additional info on how to reduce dissolved aluminum: in Letter 52410 it is suggested that, short of inexpensive decanting, expensive ion exchange is the only alternative, and Eco-Tec is suggested as another possible source of the equipment. Robert Probert's "Aluminum How-To" includes a worksheet for adjusting dissolved aluminum. Good luck.
Regards,
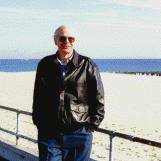
Ted Mooney, P.E.
Striving to live Aloha
finishing.com - Pine Beach, New Jersey
January 2014
Anodizing Solution Concentration and Monitoring Questions
February 3, 2016Q. Hello Sir,
I write to this community regarding my doubt about the basic set up to start an anodizing plant. I'm aware of the equipment but I lack the knowledge of the composition of the chemicals. I'm interested in Sulfuric acid anodizing. PLEASE GUIDE ME THROUGH AND KINDLY PROVIDE ME WITH THE BEST EXPLANATION FOR UNDERSTANDING. My doubts are as follows:
1) What is the ratio of DM water: Sulfuric acid (98% grade) in liters to be added? How to determine it?
2) The amount of Aluminium to be present in the electrolyte: should we add Alum powder manually initially or just maintain the Al2SO4 concentration as the process goes on?
3) Can you please tell me where can I find detailed procedure for titration analysis for determination of Al?
4) What are the essential quality maintenance practices to be ensured and how often to check the liquid?
5) What is the best ratio of composition for obtaining the most efficient and best results of anodizing?
6) Does the voltage of play a major role in the output? How do determine the necessity voltage for the process?.
- BENGALURU, KARNATAKA, INDIA
February 2016
A. Hi Lalith. Please start with our Anodizing FAQ for a quick intro.
1). Is answered in topic 4.3 of Robert Probert's "Aluminum How To", with warnings about using only Electronic Grade sulfuric acid. It is also mentioned in the FAQ.
2). Just maintain the aluminum content; do not add alum.
3). The titration procedure you seek is p.74 of "Aluminum How To". But as you will see in the discussion above, many people have limited confidence in such titrations.
4). Please tell us whether you are talking about just the anodizing tank per se, or are including other processes like etching and the very critical sealing step. What anodizing books and/or standards do you have available to you, that we can refer you to?
5). I'm not sure how this questions differs from Q1 -- perhaps I'm misunderstanding it -- but about 15% be weight (10% by volume) is the approximate correct ratio.
6). Yes, the voltage is critical and depends on the alloy, and is about 15 V for most 1xxx, 5xxx, 6xxx alloys, 16 V for 7075, and 20-21 V for 2xxx alloys. Good luck.
Regards,
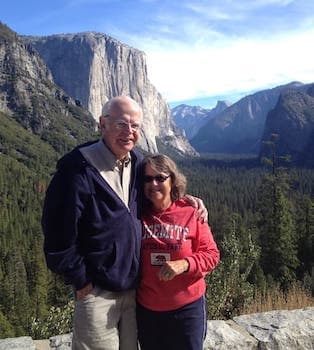
Ted Mooney, P.E. RET
Striving to live Aloha
finishing.com - Pine Beach, New Jersey
A. The best method for anodising aluminium is to make bath consisting of sulfuric acid 10% by volume and 90% water; the temperature of the bath must be 0-4 °C, that is, cold bath in order to have hard enough layer of oxide. Above this temperature the oxide layer tends to dissolve in the bath but at this low temp the oxide layer accumulates with high thickness and you can use higher amperage without a problem. No need to add aluminium powder to the bath as it ages the bath. The layer looks dark grey and is very resistant.
Thanks
- cairo,egypt
March 20, 2016
April 29, 2016
A. Here's the classic titration for a sulfuric anodize bath, it is very easy to do, and does not require much equipment.
You will need:
- a 50 mL capacity buret (looks like a graduated cylinder with a rotating stopcock at the base, and it is numbered upside down)
- A 5 mL pipet which you can buy off Amazon for about $30. The 'sure-pette' from accu bio tech is a lot better than I expected for the price.
- A liter of Sodium Hydroxide 1.0N which you can get at any lab supply house
- A small bottle of phenolphthalein indicator, also a common lab item
- A bottle of Potassium Fluoride 50%w/v. You can also buy it as solid and make it yourself with deionized water.
- 2 glass beakers
If you don't want to sit there swirling your beaker during the titration a magnetic stir plate and stir bar are very useful!
Start by pH stabilising your KF. Just put a couple drops of PTH indicator in the bottle. Shake it. It will turn pink. Add one drop of very diluted sulfuric acid- Like put a couple drops of the fresh 98% in 10 mL deionized water to use for this- NOT out of the tank. Shake the potassium fluoride
⇦ this on
Amazon [affil links]
bottle again. Repeat until it goes clear. You only have to do this once, it is now ready for use.
Next label your beakers "A" and "B". One will give you JUST your Sulfuric value, and the other will give you the value of the Sulfuric and Aluminum combined. There's a calculation later for that.
In beaker A, add 5 mL of your plating bath, 10mL of your KF solution, some DI water, and a couple drops of PTH indicator. You will see the solution get cloudy as the KF reacts with the free Aluminum and makes it fall out of solution. This is how you get ONLY your sulfuric number.
In beaker B, add everything EXCEPT the KF. Here, you WANT to titrate the Aluminum out as hydroxide.
Start with beaker A. Fill the buret to the 0 mark all the way at the top with NaOH 1.0N [1N NaOH on
Amazon [affil links]
. While you are swirling the beaker, open the stopcock and let it slowly drip into the solution. For a while, nothing will happen. Then you will see pink trails forming with each drop. You are nearing the end point of the reaction so slow down. When the solution does not turn clear again with the addition of one drop of NaOH, read the buret and write down that number as value "A" in your log book.
Repeat with beaker B.
You now can calculate your concentrations!
9.807A= g/L H2SO4 in solution
(B-A) x 1.797 = g/L Aluminum in solution.
One thing to note is that if your Aluminum is so high that it is out of limits, you may need to add more KF at first to get a true Sulfuric value, but if your aluminum is high, you need to decant and re-test the tank first anyway before taking any other action.
To test your titration skills, make up a mock tank sample of just sulfuric of known concentration, and see if you can hit it within ±5% accuracy.
Hope this helps, and good luck!
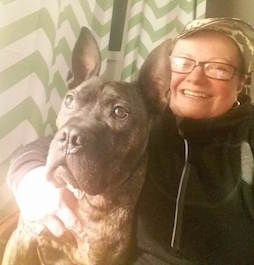
Rachel Mackintosh
lab rat - Greenfield, Vermont
Thanks for the great response, Rachel!
Regards,
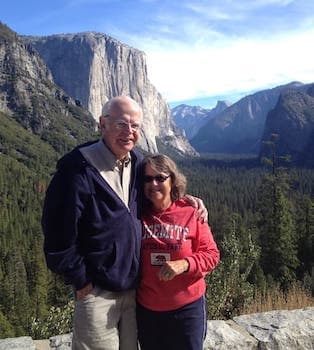
Ted Mooney, P.E. RET
Striving to live Aloha
finishing.com - Pine Beach, New Jersey
January 2018
How to make alum from anodizing solution
Q. Sir, I have some problems in anodizing bath since two weeks, so I would like to make alum from anodizing bath acid (H2SO4) so please help me. What is the best procedure for making of alum; I am trying many experiments but there is a critical problem in solubility. Please help me in this purpose.
My anodize bath concentration is H2SO4 170 g/L & Aluminum Content 35 g/L.)
Chemical analyst employee - Karachi, Pakistan
January 20, 2018
February 1, 2018
A. Hello Mr. Mehmood,
You haven't given any information on how exactly you are attempting your experiments so far, or to what purpose you intend to put the resultant Alum. I have some VERY general information to share, though.
Let me just get this out of the way... 35g/L Aluminum?!! That's like, sky high. Were you doing any tests on your baths along the way? You're almost 3x the upper limit for effective and efficient anodizing.
Here's a link to a quick and informative paper about Alum formation, which has some good background:
http://www.mesacc.edu/~paudy84101/CHM151LL/6B%20Alum.pdf
Anecdotally, we treat our rinse waters, which of course contain both Sulfuric acid and Aluminum, by initially pH adjusting them with a doser run right out of our Etch tank, which contains Sodium hydroxide (and of course more Aluminum, keeping it from building up in that tank). If you refer to the linked paper, this chemical cocktail contains all the 'ingredients' for Alum. I'm not going to get too much into details, but a neat side benefit is that our pretreated, alum-bearing, water is welcomed by the municipal water treatment facility, where Alum must be added as an initial flocculant for the settling of sewage solids. We precipitate out heavy metals and have our effluent tested by a State-certified lab every two weeks to maintain license to discharge to the sewer, so they know all they're getting is the good stuff.
Also be aware that Alum has a solubility at RT over 300g/L (which is why it remains in our effluent) so if you are trying to reclaim it, you're going to have to concentrate by evaporation.
And due to the alloying constituents from all the stuff going through your plating tank, if you haven't managed to remove all the heavy metals and nasties by hydroxide precipitation first - and can prove it was effective!- your Alum product isn't going to be much use to anyone. The municipal waste treatment plants won't take it with heavy metals, and you certainly can't use it as food preservative! If your plant has a permitted waste treatment facility you will *hopefully* already know a lot of this stuff.
In summary, before you try to get too fancy reclaiming Alum from your tanks, I would strongly suggest working on maintaining better control of your process. See above for how to determine Aluminum in the plating baths, and try to hover around 10g/L.
I apologize if this sounds harsh, and wish you success in bringing your dissolved Aluminum to within the acceptable range for anodizing.
Cheers.
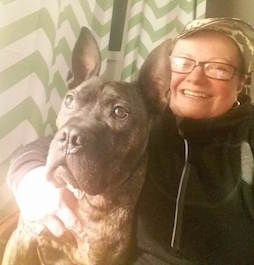
Rachel Mackintosh
lab rat - Greenfield, Vermont
Q. Dear Rachel Mackintosh,
Thanks for your reply. Actually I am trying to get alum from excess aluminium in our tank bath -- Solution (170 g/L H2SO4+35 g/L Al) so please can you tell me which suitable reagent can we add there that precipitates it and grows crystal in it? Your suggested pdf document is best and I can try it but I want to grow alum crystal in my tank, not separately. For this purpose I lack knowledge; please can you guide me step by step; please tell me about your first step. I am waiting your kind answering.
Chemical analyst employee - Karachi, Pakistan
February 6, 2018
A. There is nothing that I know of that will decrease the solubility of Alum in aqueous solution to a point where you can reclaim it at low concentrations. Crystals will not form until at or near saturation. Also, adding reagent directly to your bath will ruin the bath for anodizing use.
Also be aware that the term 'alum' does not describe one specific compound, but rather a FAMILY of compounds of similar basic structure. For example, in the waste pretreatment method described above, we are actually making an even MORE soluble 'sodium alum', or more precisely, aluminum sodium bisulfite dodecahydrate, and leaving it in solution through the pretreatment process. Its formation in our waste is entirely incidental and we do not take steps to intentionally create Alum. Note that this form can't be even used for non-food-crop fertilizer, you'd want potassium alum, as sodium is toxic to most plants at a pretty low level, whereas potassium is a botanical macronutrient. I'm not sure what else to really do with potentially contaminated alum.
This form of alum has solubility over 2 kg/L!
Figuring the weight of the water molecule in the hydrated form, you've got a molar weight of about 460 g/mol, with Al at 27 g/mol contributing under 6% of the total. This means that you need close to 120 g/L Aluminum to bring your solution to saturation.
I'm sorry I can't help more; I fear this is a hopeless endeavour due to the high natural solubility, and suggest investing in a commercially available aluminum scrubbing system for your plating tanks (or just decant like the rest of us still stuck in the late 90s lol)... and attempting any alum manufacture entirely separately from your anodizing process.
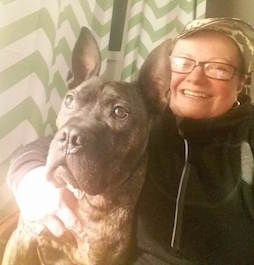
Rachel Mackintosh
lab rat - Greenfield, Vermont
February 6, 2018
A. Hi Kamran. Although I don't fully understand your question (Why do you want to make alum crystals? What application will you use them for? Why is it important to try to make it within an anodizing tank of all places?), I certainly have to agree with Rachel that trying to grow alum crystals within a functioning anodizing tank would probably render successful anodizing impossible.
Questions should usually be longer than the answers you want. So please try to precisely explain what you want to do, feeling free to use as many or more words than Rachel did. Thanks!
Regards,
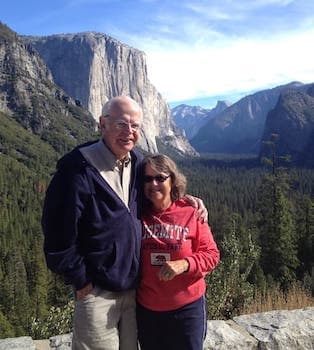
Ted Mooney, P.E. RET
Striving to live Aloha
finishing.com - Pine Beach, New Jersey
February 2018
A. Mr Mehmood, in response to your inquiry as to 'what is the first step'... Our first step is REMOVING THE CONTAMINATED SULFURIC ACID FROM THE PLATING TANK. Full Stop. This is in the form of process dragout. As I have previously stated, our Alum formation is COMPLETELY INCIDENTAL TO THE PROCESS. We take no steps to intentionally make Alum. We certainly don't try to reclaim it, by crystallization or otherwise. Nor do we ever attempt to measure how much Alum we have ACCIDENTALLY made.
In my humble opinion as a plating chemist with over a decade of experience in analytical method development work in an academic setting prior to coming into the Manufacturing world, and a license to operate a wastewater treatment plant, as long as your plating tanks are being allowed to accumulate Aluminum beyond the absolute maximum upper limit of 12-15 g/L agreed upon by, well ... EVERYONE ... You are barking up entirely the wrong tree. As long as you are in the business of anodising, and not trying to become a major Alum manufacturer, fixing your primary process should be your first concern, and you should not even be running product through those tanks until you are within correct operating parameters. If we let our Aluminum get as high as you have, we would be SHUT DOWN by our accreditation bodies. I am dead serious about this. Our product would fail all outside performance testing. It would be nothing but very pricey scrap metal. Our certifications would be suspended and we would lose all of our customers, who would probably sue us to recoup costs of a massive recall. If I were a customer of yours reading this, I would fall out of my chair, and then pick myself off the floor and pick up the phone and ring your boss demanding an explanation.
Please, for the sake of the quality of the product coming out of your shop, PLEASE redirect your resources to process control.
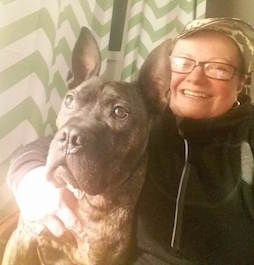
Rachel Mackintosh
lab rat - Greenfield, Vermont
February 7, 2018
Q. Dear Rachel Mackintosh & Ted Mooney,
Thanks for your replies. Actually I would like to get ammonium aluminum sulphate Dodecahydrate (NH4)Al(SO4)·12H20. from excess aluminium from my anodize bath acid (170 g/L H2SO4+35 g/L Al). I add ammonium sulphate
⇦ this on
eBay or
Amazon [affil links]
in it about 35 g in 1 L bath solution after 24 hours there is some residue laid down which I have filtered and taken 5 g filtrate and mixed with 1M NaOH [1N NaOH on
Amazon [affil links]
. After the reaction some ammonia and Iron III Hydroxide brownish ppt appears but no crystal grow in it. So please can you tell me how I can make ammonium alum from my anodize bath acid by Crystallization technique -- this is my assignment and I am trying since 2 weeks. I am waiting your kind answering.
Best Regards,
Lucky Aluminium Industry Pvt Ltd - Karachi, Pakistan
February 9, 2018
? Hi Kanran. I'm afraid that we won't make much progress until we fully understand your question and we are still very far from that point ... 1. Why are you trying to do this within your anodizing tank instead of moving the waste solution to another vessel? I do not think here is any way you can put ammonium sulphate into a working anodize tank without ruining your anodizing solution. 2. There is also no way you can allow dissolved aluminum to reach 35 g/l without ruining your anodizing in the first place. 3. Where is this iron coming from, which you have precipitated as Fe(OH)3
I am not a chemist, and once your question is understood, perhaps a chemist will jump in and help us. Meanwhile, I am not familiar with any processes which crystallize into hydrated salts until you reach approximately a saturated solution. Have you double-checked your formulas to insure that the quantities you have added will result in a critical solution?
Regards,
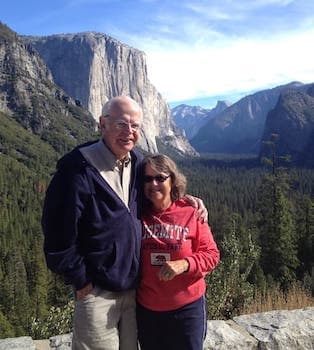
Ted Mooney, P.E. RET
Striving to live Aloha
finishing.com - Pine Beach, New Jersey
February 2018
February 9, 2018
A. "I add ammonium sulphate in it about 35 g in 1 L bath solution after 24 hours there is some residue laid down."
I don't think that residue is Alum. Again, remember the solubility of alum is VERY high. Have you decanted the supernate, rinsed and dried the residue, and had it sent out for lab testing? On that note, have you had your ano tanks tested so you have a good profile of what's actually in there? Not like that would help all that much since ano tanks are by their very nature rather dynamic in that relative levels of acid and contaminants fluctuate with use, no matter how carefully we try to control them.
"which I have filtered and taken 5 g filtrate and mixed with 1M NaOH. After the reaction some ammonia and Iron III Hydroxide brownish ppt appears but no crystal grow in it."
Why is there that much Iron in your tank that you suspect you have iron settling out? Again, have you had your tank tested for precise Iron levels before starting? Are you determining ammonia concentration by odor? At what pH is the settling taking place, measured at the point where you have JUST added the NaOH and then the pH of the supernate after the settling has been allowed to happen over a few days? I ask these questions not because your answers will bring us to a magical solution, but because these are things you should be recording in any experiment such as this so that you may have repeatability in future experiments. The pH of the supernate will generally fall a bit as metals are precipitated out by hydroxide formation. Eventually an equilibrium will be reached between pH/concentration remaining in solution/mass of precipitate, all depending on solubility curves, and changing pH or concentration, or adding additional reagent(s), intentionally or in the form of contamination, changes this.
As I have already said, there are other alloying metals and silicates and stuff in a dirty anodizing bath, many of which WILL form hydroxides and fall out of solution. And Aluminum itself is perfectly easy to form hydroxides from, so if you see stuff settling out, it's most likely to be a mixture of metal hydroxides.
Again: Alum is EXTREMELY soluble in water and this assignment seems a wild goose chase.
All I can really help with is general theory here. I do wastewater, and we waste treatment folks like to lump contaminants into 'groups of things that kinda act the same under kinda similar conditions'. There's a LOT of very involved chemistry and math you will have to work out yourself to see what sort of equilibria the various compounds will form throughout the stages of your experiments. Even back in University, if a professor had said, 'Hey, here's a solution that I can only generally tell you what's in it, and how much, probably mostly just sulfuric acid and aluminum, and there might be some other stuff, but I'm not sure what... GO MAKE ME SOME ALUM!!" that would be considered cruel and unusual punishment and most probably would have caused a mutiny.
I'm gonna come right out and say it again: This isn't going to work. One contaminant you have forgotten about (for example, Copper from flight bars and whatever goes into whatever alloy of bronze you might have as contact cradles) will throw everything out of whack and invalidate all that calculation!
Trying to precipitate or otherwise separate and then reclaim a specific compound from a mystery cocktail such as a dirty ano tank is a combination of waste treatment chemistry and chemical manufacturing. Anyone trying to make Alum for its own sake will be using precise quantities of known-pure substances under controlled conditions of temperature, pH, and dissolved gases.
You may prefer to step back and spend some time learning about industrial waste treatment methods. Courses are easy to find in the States, not so sure about your area, but there is a lot of information on the internet as well. Much of it is non-specific to any single contaminant, but will help give you a better instinct for what is and is not practical, or even possible, to accomplish ... and where your skills & ambition might be put to more effective use.
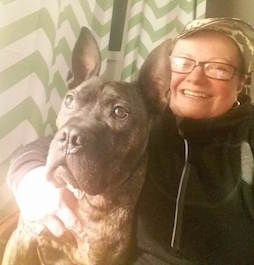
Rachel Mackintosh
lab rat - Greenfield, Vermont
February 13, 2018
Q. Dear Rachel Mackintosh & Ted Mooney,
According Mooney, 1 "Why are you trying to do this within your anodizing tank instead of moving the waste solution to another vessel? I do not think here is any way you can put ammonium sulphate into a working anodize tank without ruining your anodizing solution."
....almost ruined our anodizing solution so I can try to make ammonium alum from this ruined acid,
"Where is this iron coming from?"
... actually we used 6063 alloy of aluminum so I think iron come from it.
According Rachel Mackintosh,
"Are you determining ammonia concentration by odor?"
yes determine by odor ... pH 13,
Before adding Ammonium sulphate pH is 3.5,
after adding Ammonium sulphate then acid has been allowed settling about 3 days & then add some mL 1M NaOH in 5g settled product pH reached 13, ammonia & Brownish ppt has appeared.
(pH/concentration remaining in solution/mass of precipitate; how I can measure it?)
Lucky Aluminium Industry Pvt Ltd - Karachi, Pakistan
Q. In anodizing aluminium industry, how to calculate amount of Al3+ in sulfuric & phosphoric acid tank (electrolysis bath)?
Tri Yuliani- Bekasi, West Java
January 6, 2021
A. Hello Tri. We appended your inquiry to a thread which explains what dissolved aluminum content to shoot for in sulfuric acid anodizing baths and how to analyze for it.
Please tell us about the specific phosphoric acid anodizing process you have in mind. Thanks!
Luck & Regards,
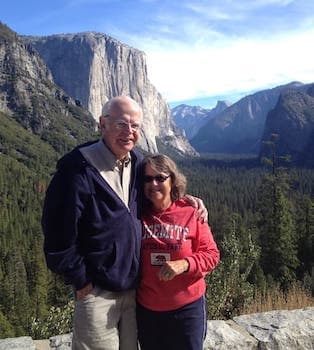
Ted Mooney, P.E. RET
Striving to live Aloha
finishing.com - Pine Beach, New Jersey
January 2021
A. Regarding dissolved aluminum in a plain sulfuric acid anodizing solution: Boeing allows 21 g/L but they are not dyeing. Dyeing suppliers top off at 15 g/L. In my book I recommend a top of 12 g/L. It is too long here to list the analysis procedure, it too, is in the book. I have not seen any published work on dissolved aluminum in the phosphoric anodizing system.
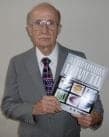
Robert H Probert
Robert H Probert Technical Services

Garner, North Carolina
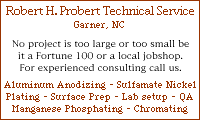
January 8, 2021
August 7, 2021
Q. When does the anodizing electrolyte solution need to be replaced?
Hi,
I have a Type-II anodizing setup of about 25 gallons as sulfuric acid electrolyte. I've read that the anodizing solution must be replaced each time some conditions are met: 100 Square Feet at 1 mil (0.001").
But I am not sure about the relationship between the previous conditions and the quantity of solution. Let's say, if hypothetically both of the conditions applies for 6 gal of solution, would it be directly proportional to 25 gal?
Doing the math, if I have 25 gal, then instead of 100 SQF, would the solution work for 416 gal ((25/6)*100)?
According to your knowledge and/or experience, what parameters do I have to take into account in order to determine the lifespan of my solution, given the anodizing width (in mil), the quantity and whatnot?
Thanks in advance!
- Dominican Republic
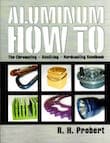
Aluminum How-To
"Chromating - Anodizing - Hardcoating"
by Robert Probert
Also available in Spanish
You'll love this book. Finishing.com has sold almost a thousand copies without a single return request :-)
A. Hi Pedro, you are correct that the volume of anodizing solution makes all the difference, because what you are actually trying to do is to maintain the solution within an acceptable range of dissolved aluminum. But it is more typical to regularly replace a portion of the solution, like 10%, rather than dumping & replacing the whole tank.
The answers you want are probably in this discussion and related threads but if you'd prefer a good tutorial with worked examples and a worksheet, you may be interested in Robert Probert's book.
Luck & Regards,
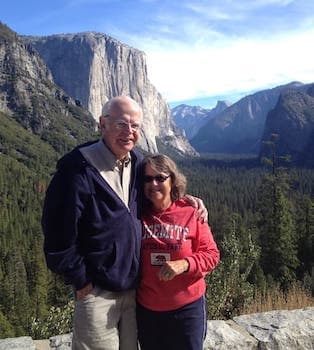
Ted Mooney, P.E. RET
Striving to live Aloha
finishing.com - Pine Beach, New Jersey
August 2021
Q. Hi Ted,
Thanks for the reply! Interesting, from my 25-gal tank, it is better to replace 10% of the solution rather than the entire setup.
I suppose the same rule I mentioned (the 100 SQF @ 1 mil) applies on this portion of solution. I will take it into account in my anodizing record sheets.
Also, I appreciate your past replies on previous threads. Glad to talk with you again!
Mechatronics Engineer - Dominican Republic
August 14, 2021
Hi again Pedro. You are certainly welcome, but don't let my silence be interpreted as confirming the "100 ft2 @ 1 mil" guideline you are quoting. I have no idea how valid it is or isn't.
Luck & Regards,
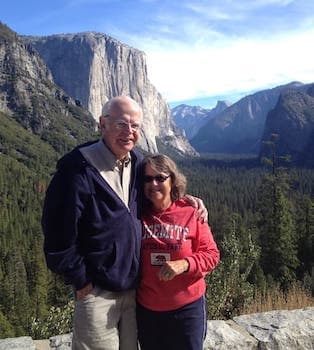
Ted Mooney, P.E. RET
Striving to live Aloha
finishing.com - Pine Beach, New Jersey
August 2021
Worry not :), I will keep producing results in order to confirm this statement. The way I'm planning to do it is to check any variations in the anodizing process after the end of the effective area's lifespan.
If anything of interest occurs, I will let you know!
Mechatronics Engineer - Dominican Republic
August 15, 2021
Q, A, or Comment on THIS thread -or- Start a NEW Thread