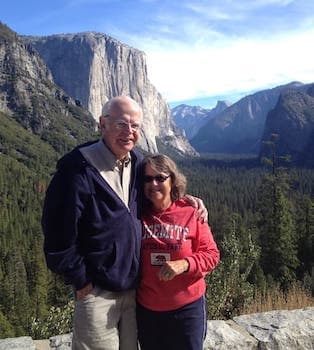
Curated with aloha by
Ted Mooney, P.E. RET
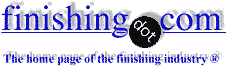
The authoritative public forum
for Metal Finishing 1989-2025
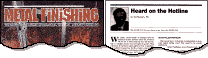
-----
Plating of tungsten, mica, or graphite powders
RFQ We are looking for a toll source of plating W powder with Ni. If Ni is not possible we would consider these other coatings: Cu, Ag, or Au.
Peter Sextonconsultant - Cohasset, Massachusetts
September 14, 2021
Ed. note: This RFQ is outdated, but technical replies are welcome, and readers are encouraged to post their own RFQs. But no public commercial suggestions please ( huh? why?).
A. Hi Peter. Your RFQ is posted but electroplating onto tungsten powder may be more of a development process than a commercially available service.
Plating onto powder proceeds differently than most electroplating because of the huge surface area. Some reactions are nearly explosive in their heat evolution. Many years ago while David Lashmore was operating Materials Innovation I visited and saw some of their work on electrodeposition onto powders. He is right in your neighborhood and probably can at least advise you of a good next step if no toll coater responds . See his profile on Linked In or elsewhere.
Luck & Regards,
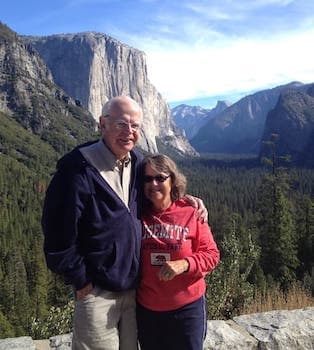
Ted Mooney, P.E. RET
Striving to live Aloha
finishing.com - Pine Beach, New Jersey
September 2021
⇩ Related postings, oldest first ⇩
Q. Is it in the realm of practicality to gold plate a coarse tungsten powder?
The tungsten granules I would like to hard gold plate are between 100 and 400 microns in size such that one pound of this coarse powder would have about 1,000 square inches of surface area. I assume that this plating operation would be beyond most do-it-yourselfers, but might an experienced plating shop be able to do this? I'm guessing that the tungsten granules could be spread thinly on a conductive plate such that the sides of the granules exposed to the plating solution could be plated. Perhaps the conductive plate could also be vibrated so as to agitate the granules exposing all surfaces to the plating solution randomly during the plating processes.
Next question: Are there any durable fluorescing agents, dyes or pigments, that can be added to a plating solution such that in darkness, or low light, and with illumination by ultra-violet light the plated metal (hopefully gold) would visibly fluoresce?
Why am I asking these questions? I want to create a functionally equivalent gold tracer for the testing and evaluation of gold mining recovery and concentration equipment. Tungsten has almost the same specific gravity as gold and will tend to concentrate similarly as gold in mining wash plants, but the problem is that tungsten is difficult to see (dull or dark gray in color). Plating tungsten powder with gold will help mining equipment operators to see it during the adjustment and evaluation of the equipment. The purpose of the fluorescent marker would be to help prevent gold plated tungsten granules from being confused with or peddled as genuine gold.
gold mining - Missoula, Montana, USA
2007
A. A long time ago, somebody like GE sold diamond dust that had been nickel plated, so someone in the world can do what you want, but it will be tough to find that company.
As far as the fluorescent material bonding to the gold, I doubt it, and definitely not in the gold. Low level radioactive is possible, but that opens a kettle of worms that you do not want to even start to think about.
- Navarre, Florida
2007
A. If you train your employees to look for nickel color, it will be a lot less expensive and can not be mistaken for and sold as gold. If the lighting is good, a nickel coating on a powder as large a what you are speaking of will show up very well. As you say, the biggest mistake would be confusing the tungsten for gold because of the appearance, malicious or otherwise. Plus, if gold plated tungsten is accidentally mixed in with gold, it will be nearly impossible to separate without melting, and then straining the tungsten out.
If you must have a gold color, you can use electroless gold plating, or gold or titanium nitride chemical vapor deposition (CVD) coating by fluidized bed, but these will not glow under UV or otherwise. Without doing some checking I can't tell you what might look like.
- Cleveland, Ohio
2007
A. Mr. McNulty,
Maybe you should talk to Mike Feldstein of Surface Technology Inc. He used to offer a fluorescent composite electroless nickel plating for identification or authentication purposes. I'm not sure if he could or would plate on Tungsten powder.
Monterrey, NL, Mexico
2007
Third of three simultaneous responses --
A. If you are looking for color only, How about gold immersion process. Use hot plate, with magnetic stirrer in a glass beaker [beakers on
eBay
or
Amazon [affil links] .
Good luck,
- Mays Landing, New Jersey
2007
2007
Gentlemen, thank you for your responses and your help. Of course you understand the need and the demand we have in the gold mining industry for an inexpensive gold tracer to both quantify and improve our gold recovery operations.
James Watts: Low-level radioactive gold tracers are currently the standard in our industry, but as you guessed correctly, using them can be expensive and their shelf-life is very short. Radioactive gold tracers are not out of the reach of larger mining operations but for small to mid-sized mining companies their use can be prohibitively expensive.
As all of you are aware, gold plating tungsten powder if practical may be able to make a gold tracer highly visible, but it may also lead to unethical use by unscrupulous individuals should such a gold plated tungsten powder be produced inexpensively enough to be within the reach of small-scale mining operations. After talking with some other mining people about this dilemma we've come to the nearly unanimous conclusion that a gold plating tungsten powder would not be a good idea due to the potential for abuse and due to the inability to differentiate between it an naturally occurring gold in the ore being being evaluated.
But regardless of whether we can find some other bright plating finish such as nickel, rhodium, or whatever, I'm not as yet willing to dismiss the idea of a fluorescent marker in addition to a bright visible finish.
Guillermo: I appreciate your mention of Mike Feldstein of Surface Technology Inc. and the fluorescent composite nickel product he had available at one time. This type of product may be exactly what I'm looking for. The reason fluorescent identification would be so important is because it would allow for a method to optically quantify the percent of the tungsten tracer present in an ore concentrate without the need to separate it from the naturally occurring gold that was already present in the ore, just like radiation can be used to estimate the weight or percentage of a gold tracer after it has been diluted in other gold from the ore.
A bright and fluorescent nickel plating might be just the thing I need to plate on my tungsten, and if it is an electroless process, my question would be whether this operation might be something within the reach of my in-shop efforts?
My only other consideration might be whether there could be other plating formulations that would achieve visibly different finish colors. A bright green copper plating or some other distinctive color for example. I'm not looking for designer gold tracers, I'm hoping that I can differentiate the color of various mesh sizes of tungsten powder so as to keep track of our equipment's efficiencies for various sizes of gold. The differentiation between very fine, moderately fine, and coarse gold efficiencies is very important in determining the effectiveness of gold mining equipment, although having different colors for gold tracer particle sizes is not critical, it would be a plus.
Thank you again gentlemen!
Timothy McNulty
- Missoula, Montana
Q. How to plate Cu or Ni well on mica powders?
Hongbin daiauto designer - Shenyang, Liaoning, China
2005
A. Hi Hongbin. Your question is very broad but if you can limit it by giving us an idea of the application requirements, what size the powder is, and whether you need a thimbleful or a tank car full, we can probably make at least a little progress. Also please tell us of your successes and failures to date, and your plating skills and experience level.
If you are experimenting with this, please remember that powders act differently than solid materials because of their huge surface area. Dusts of many sorts can be flammable or explosive in air; for the same reason, fine powders can react extremely exothermically or even explosively with oxidizing agents and plating solutions. Thanks!
Dr. David Lashmore, last time I saw him, was running an intellectual property plating facility in New Hampshire, and one thing they were doing was plating powders.
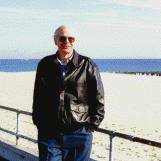
Ted Mooney, P.E.
Striving to live Aloha
finishing.com - Pine Beach, New Jersey
2005
Q. Electroless process for copper coated graphite particles? Please let me know the procedure and percentages by weight of the ingredients for obtaining coating of copper on particles with electroless process.
Deep Thi- Karnatka, India
December 1, 2012
A. Graphite can be easily coated by PVD processes. We have coated copper on graphite components up to a thickness of several microns. However coating on powders poses different problems.
H.R. Prabhakara - ConsultantBangalore Plasmatek - Bangalore Karnataka India
December 4, 2012
----
Ed. note: Thanks, H.R. While it's clearly not possible to deeply explain those "different problems" when doing PVD processes on powders, since you've put the proposition on the table, a sentence or two about their general nature would be enlightening. Thanks.
A. Well, there are several issues. Most important problem is to coat all the grains on all faces. PVD being a line of sight process, it is not possible to coat surfaces shadowed by other objects or the object's own shadow. Common practice is to rotate the objects and in some cases have multiple sources. In the case of powders this is not possible. When you expose some powder to the incoming flux from a target only the grains on the topmost layer would be coated albeit partially due to shadowing effect. One way is to agitate the powder so that all faces of all grains are exposed to the flux at least for some time. This is easier said than done particularly when the large quantities are involved. Another possible way is to make the grains continuously move up and down in front of the target in the vacuum chamber. This is not easier either. Other issues would be out gassing of gases trapped in the dust pile. Dust contaminating the chamber could also be an issue.
But, in spite of all these problems there are some people who do coat on powders!
Bangalore Plasmatek - Bangalore Karnataka India
Thanks for the great exposition! Certainly electroplating of particles poses similar special problems, too, and per my earlier response on this thread.
Regards,
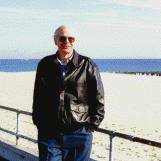
Ted Mooney, P.E.
Striving to live Aloha
finishing.com - Pine Beach, New Jersey
Q, A, or Comment on THIS thread -or- Start a NEW Thread