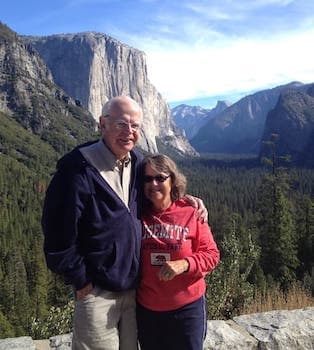
Curated with aloha by
Ted Mooney, P.E. RET
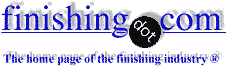
The authoritative public forum
for Metal Finishing 1989-2025
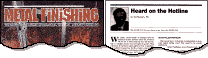
-----
Hot dip galvanizing flux Q & A's, Problems and Solutions

< Prev. page (You're on the last page of the thread)
Q. We have a continuous steel wire galvanizing line here in Kampala, Uganda. We are facing the following problems:
High dross formation and An acid flux bath.
We try to neutralize the flux bath by adding an ammonium solution but the rate of contamination is high.
Yes we have a rinse tank but still it's not enough!
Sir, what is your advise on the above?
- Kampala, Uganda
July 11, 2012
July 18, 2012
A. Collins:
Are you "wet" or "dry" kettle? What is too high of rate of dross? How long do your kettles last?
Regards,
Galvanizing Consultant - Hot Springs, South Dakota, USA
Q. Dear Dr. Cook:
I have a serious problem with bare spot because of Chinese raw material. I produce steel tower angle and plate, our flux is double salt acn 0.8 and fe+2, 0.28%, so, my supervisor tries to solve the bare spot problem by brushing the angles with ammonium chloride solution for 45 minutes, then immersing in zinc kettle. The result became okay but as per my little experience the dross will increase too much. I read an article before that every additional gm of ammonium chloride causes 20 gm of dross, is it right or not? And what's the side effects of doing it my supervisor's way?
Thanks.
Regards,
technical manager - Yingkou Anshan China
September 23, 2012
![]() |
A. Sir: Galvanizing Consultant - Hot Springs, South Dakota, USA September 25, 2012 A. Dear Ahmed; - Ankara, TURKEY September 25, 2012 |
Q. Hi Ozge,
Sorry, I forget to tell you that our kettle is dry and we have preflux double salt with temperature 50 °C and in our kettle we never use lead; we can use nickel and aluminum and bismuth alloys.
And I have good friends in Turkey, Mrs. Isik Spaci. They are good galvanizing consultant.
Thanks
Regards
Bye
- Liaoning, China
September 26, 2012
September 26, 2012
Q. Dear Dr. Cook /Mr. Ozge.
Thanks a lot for your kind support.
1st, I suggested the shot grit blasting since the sand blasting will increase the silica in the degreasing and pickling.
Regarding the ammonium chloride, does it really only cause white fumes, or increase the dross & ash also?
Also, I think that one mole or gram from iron gives you 25 mole or grams. Am I right?
Dr. Cook, you kindly suggested me to use quadraflux, can you give me the best specifications (composition ratios, pH, temperature, etc.] Please advise.
Thanx
Regards
- Liaoning, China
![]() |
September 27, 2012 A. Sir: Galvanizing Consultant - Hot Springs, South Dakota, USA September 28, 2012 A. Dear Ahmed; - Ankara, TURKEY |
September 29, 2012
A. Ozge:
35 °C (95 ° F) is too hot to heat 17% HCl. The fumes will destroy the roof and the building, which will happen anyway if a good inhibitor at the right concentration is not used.
Regards,
Galvanizing Consultant - Hot Springs, South Dakota, USA
A. Dear Mr. Cook;
Of course I am assuming inhibitor, good ventilation system and moreover an enclosed pretreatment unit. Thanks for mentioning about all these.
galvanizer - Ankara, TURKEY
October 2, 2012
October 2, 2012
A. Sir:
HCl is a gas which is heavier than air. It fills a galvanizing plant from the floor upward. This gas along with water vapor is terribly corrosive. I have seen steel corrosion in warmer climates for areas around a galvanizing plant corrode to orange black dust over the years. The best HCl fume control that I saw exhausts the HCl gas down through the floor. Simply put the best HCl temperature range in my experiences is between 70 and 85 °F. Above 85 °F the workers and the cranes suffer.
From which country do you purchase your HCl inhibitor and at what concentration do you use it? Also do you test its effectiveness in the HCl pickle tank?
Regards,
Galvanizing Consultant - Hot Springs, South Dakota, USA
![]() |
A. Dear Dr. Cook; galvanizing - Ankara, TURKEY October 4, 2012 A. There's a lot to be said about having a good inhibitor, as Tom has said. ![]() Geoff Crowley Crithwood Ltd. Westfield, Scotland, UK ![]() October 4, 2012 |
Q. Dear Geoff;
Do you mind if I ask about your average pickling time during "winter" (for fresh acid and for 30 baumé)?
galvanizer - Ankara, TURKEY
October 5, 2012
A. Ozge,
You answered my question of where you get your inhibitor EXACTLY AS I EXPECTED. Regarding this supplier I respond "NO COMMENT."
Incidentally 30 °baumé FRESH HCl is NOT available, the highest concentration is 20 ° baumé (e.g. about 35.5% HCl). After being fresh the dissolving of iron and zinc causes the baum é to rise to the 30 to 40 ° baum é range. Some iron is required for good pickling in HCl.
In my inhibitor testing of 38 years ago (now published in the magazine METAL FINISHING) I did all my testing at 3 parts inhibitor/10,000 parts mixed acid (e.g. 3 liters inhibitor/10,000 liters mixed acid). For sulfuric acid I used 10% acid, 2% iron, 1% zinc and 160 °F. Only one inhibitor (produced in the USA) did everything I wanted, including NOT slowing the pickling (in a separate test). For HCl I used 1:1 HCl/water 3/10,000 and the same iron and zinc and at 90 °F. Again only one (produced in the USA) did what I wanted.
About 10 years ago I was called into a new start-up plant using sulfuric acid, which previous to my arrival had 3 (55 gallon) barrels of fume suppressant plus inhibitor put into each of three 20,000 gallon pickle tanks. The fumes were so bad that I could NOT walk across the plant floor crosswise. Simply put, my lungs closed up and I could not take a breath. The workers were having nose bleeds and quitting. I drove to a nearby galvanizer and obtained two 5 gallon buckets of the good inhibitor and put one gallon into each acid tank. The next morning I came into the plant and the workers all came up to me and were thanking me for the clean air that they could take a breath. The supplier blamed the first product on a "bad batch." RIGHT!!! With the good inhibitor the air in the plant was the same as clean outdoor air.
A few months ago I went to the East Coast of the USA and noted that the HCl was not properly pickling. A test confirmed that the acids were over-inhibited (same supplier) as the case 10 years ago. This was quite unusual because the plant manager said they had not added any inhibitor for the last 5 months. To increase pickling they had heated up the HCl tanks and the guy was there getting ready to remove and replace the roof. All the acid tanks were then hauled away and new acid brought in and inhibited with the good inhibitor. It was a pleasure having acid that pickled very well and with almost NO fumes. Thus the combination of a good inhibitor and with proper testing, fast pickling, very low fumes, and very long acid tank lifetimes are easy to attain.
Geoff has very good experience.
Regards,
Galvanizing Consultant - Hot Springs, South Dakota, USA
![]() |
A. Pickle time? ![]() Geoff Crowley Crithwood Ltd. Westfield, Scotland, UK ![]() October 9, 2012 October 9, 2012
- Ankara, TURKEY |
October 9, 2012
Q. Dear Sirs:
I am really enjoying with such technical discussion, I really feel proud to be involved. Regarding my conditions --
Our acid pickling concentration always was kept between 8.0 up to 12.0 to avoid acid fumes; we have same acid suction unit as explained by our friend Ozge but from a Chinese supplier.
Regarding the inhibitors, I am a little bit worried since we are using Chinese brand and I can't trust it. It may be causing poor pickling. I hope that Dr. Tom can recommend a good brand for us from local market (China) if available. Otherwise, give us the way how to test it. Final solution we can import from international market as per his suggestion.
Thanks
Regards
Rashad
- Liaoning, China
----
Ed. note: Thanks, Rashad, proud to know you. Dr. Cook has contributed several articles on fluxes, surfactants, and other galvanizing issues to our on-line library which you may wish to review. I think you'll find the technical answer there.
We'd like to be all things to all people, but have learned from decades on line and tens of thousands of threads that we can't post recommendations particular brands or suppliers in a public forum ( huh? why?).
A. Ozge:
30 some years ago I found a wetting agent for flux that I liked. I used vacuum (water aspirated) and reduced the volume of this wetting agent by 95%. I then added water back and got the same good results as a wetting agent. I contacted the maker of this wetting agent and indeed he admitted that he took 2 gallons of the concentrated wetting agent and then added 50 gallons of water to it and sold it by the barrel at about $2,000/barrel. I chose NOT to deal with this guy who liked to dilute a good material and sell it for a huge profit. Later I found a concentrated material that works extremely well at 1 to 3 parts/10,000 parts of tank volume. (e.g. 0.01% to 0.03%). Thus from this posting you should note and understand that if an inhibitor company recommends much higher concentrations it is likely the inhibitor is not very effective or watered down. Also realize that the more inhibitor an inhibitor company sells the more money the inhibitor company makes. Also some inhibitor makers do not disclose on MSDS sheets what is in their products which should make you question why not? In the USA disclosure on MSDS sheets is a requirement of law. An acid inhibitor MUST nearly prevent additional attack of the bare steel after the mil scale is removed, and it MUST NOT slow down pickling (removal of mil scale). Thus two types of testing are required: 1)acid attack on steel in a stressed condition and 2)pickling speed tests on steel with a mill scale coating. Less fumes in the plant come automatically with a good inhibitor. There are fume control agents (which are NOT inhibitors) as well but I rarely use them except in special cases.
My article in the magazine METAL FINISHING about inhibitors is titled something like: "Testing and Use of Acid Inhibitors." From this article you can test and evaluate inhibitors to find the one or two (from many) that suits your needs.
Regards,
Galvanizing Consultant - Hot Springs, South Dakota, USA
Q. I am an employee at one of the construction companies that manufacture scaffolding and formwork.
Most of our products are galvanized, therefore we set up a galvanizing process. It's been running 75%, but I am still confused as to the determination of the proper usage of fluxing solution because I'm new in this issue. Whether mono salt, salt double, triple or quad salt?
I need help to determine which fluxing solution I will use in my company now.
- Cikupa, Tangerang, Indonesia
November 15, 2012
Q. How do you purify triple salt flux which is contaminated by hydrochloric acid? Test procedure to determine the iron content in a flux solution?
Psalm Velardeproduction - Dubai, UEA
November 17, 2012
Q. Dear Sir,
Please give me details of flux (% ammonium chloride, zinc chloride, & other )
Thanks & regards
- Pune, India
February 3, 2013
Q. Hi sir
I am responsible of qc in galvanizing factory. I have an article about flux. Please guide me what should I do?
Best regards
responsible of qc - iran-khorasan-mashhad
February 17, 2013
February 20, 2013
Q. Dear sirs,
I've just started working in a company that galvanizes steels for power transmission towers. The problem is, it doesn't have any knowledge about the chemical of the process and I'm in this field only for 5 months. We're making some tests to prove what is good for us and what is not, but we're still facing some difficulties
One of the problems we have is about the preflux additives, we've just prepared a new preflux bath because the old one had 50 g/L of iron contamination. Some suppliers told us about some additives and I'd like to know if they really work or are just people trying to sell their products. The additives are:
-Additive for complexing of iron: a product that maintains the iron concentration low by complexing the iron contamination;
-Additive containing nickel: some said that nickel in the preflux bath help the homogeneity of the zinc layer, but others say that this nickel only oxidizes in the heating before the zinc kettle, forming ashes;
-Additive to make the steel more wettable.
These additives really work? Is there another kind of additives I can use in the preflux bath?
Regards,
Chemical Engineer - Belo Horizonte, Brazil
![]() |
A. See some people even add acid to the flux but they tend to miss it that this would go to the GI tank.Better way is to change the water after pickling on a regular basis and check the iron content of it.If the water after pickling is clean you wont see iron content in your flux increasing.Changing of Flux is an Expensive part but changing of water after pickling is relatively cheaper;) nitesh agarwal- Mumbai, India February 23, 2013 February 23, 2013 A. Daniel, Galvanizing Consultant - Hot Springs, South Dakota, USA |
Best ACN for my case
Q. Dear sirs,
My company sent the flux samples of different suppliers to a lab. The two samples had different ACNs and I still don't know which one is the best for my case.
We galvanize about 80% angle steel and the other 20% are sheets. We are not able to heat the preflux more than 40 °C, but we have an oven.
What is the best for me? An ACN of about 0.4 (MONOSALT) or is there another good composition for my case? I've read that the best for sheet is the monosalt, why is this? Is it because of the low ammonium concentration?
Thanks!
Chemical Engineer - Belo Horizonte, Brazil
July 8, 2013
July 29, 2013
Q. Dear.Dr.Cook,
I run plating business in South Korea.
I read your posting on finishing.com and I would like to ask some questions, if you don't mind.
1. In your posting, there's a direction that 'Add some wetting agent during fluxing process'. So I added made-in-Korea wetting agent over 2%, but only resulting 40 dyne/cm of surface tension.
2. Is it ok to get less zinc consumption, less ash and less bottom dross effect with surface tension 40 or so?
3. I would like to know correlation between zinc consumption and surface tension.
4. And, is there any negative effect in flux cistern, pouring some addition agent of 2% - 4% of total amount?
- Ulsan, Daun-Dong, South Korea
July 30, 2013
A. Sir:
There is no way I can answer your questions because I have no idea what your wetting agent is. I do not know if it would be beneficial or bad.
Regards,
Galvanizing Consultant - Hot Springs, South Dakota, USA
At what point does recirculating waste water ruin the flux?
December 27, 2013Q. Dear Dr Cook and other readers,
I am working as a chemist in an HDG plant.
My question considers the effect of washing water on flux. We are using HCl for pickling. As we don't have canalization, waste water for rinsing has to be sent to authorized companies and thus we were forced to deal with this problem in a way that our waste water is circulating. It goes from washing tub in to neutralizer (NaCl is added) and it is neutralized at 8,1 pH; some coagulants and flocculants are added for precipitation and after that water goes to precipitation tank where the sludge is pulled out. "Clean" water goes back in the wash tub and it is used again.
The only problem now is that the water currently contains 83% of NaCl (100% corresponds to 36 g/l), total dissolved solids are 19 g/l, conductivity is 36mS at the temperature of 13,2 °C.
I am aware that at some point we will contaminate flux with Na+ ions. Do you know what other problems I can expect? What can I expect in the dipping process, more smoke, ungalvanized areas?
We are using our type of flux for 8 years now where the ratio of ZnCl2:NH4Cl is 2:1, flux is 21 baumé, temperature 25-35 °C, content of Fe2+ lower than 1 g/l, and we don't have any problems in production -- black spots are really rare.
Does anyone else have the same experience with rinsing of goods in salted water? At what level/concentration of NaCl /conductivity do you send it out? At what concentration of salt can I expect that the material after rinsing and before fluxing, although it takes few seconds, will start to corrode? Is it possible that material goods will corrode after fluxing? Do you have any suggestions for me?
Really looking forward to your answer.
- Zagreb, Croatia
December 27, 2013
Q. Dear Sir,
Currently we are buying flux from a local supplier. It's giving us a lot of problems. When I ask the supplier whether it's:
1)Monosalt
or
2)Triple salt
He is unable to answer. According to him, this type flux is specially designed for my plant.
Specific gravity of neat solution of fresh flux is: 1.15
Temperature of flux is: 51 °C.
I am suspicious of the supplier because the quality of flux he is supplying us is causing us a lot of problems.
After dipping the product into flux solution, we will have corrosion line on the surface of the product and it creates a lot of ash during dipping in the zinc pot.
Thanks
Param
galvanizing - Selangor , Malaysia
January 12, 2014
A. Sirs:
In hot dip galvanizing fluxes certain non-volatile chemical compounds may be present (even in brand new fluxes). These may include calcium chloride (CaCl2), magnesium chloride (MgCl2), manganese chloride (MnCl2), sodium chloride (NaCl), and potassium chloride (KCl).
About 30 years ago I found 13% sodium chloride in a flux from Iceland and the galvanizer had 13% rejects. A reject being product that had to go through the kettle twice. When the flux was replaced with a flux having no sodium chloride the rejects went away. Same thing happened in Madrid except it was 20% sodium chloride in a pipes galvanizing plant with 20% rejects and again rejects disappeared when flux with no sodium chloride was put in the flux tank.
I now know that if the solid flux contains about 3% total non-volatiles (or about 8 grams/liter in the working flux), then the rejects will be about 5%.
I recommend that you have your working fluxes tested by icp/ms and post the results. The results should be in mg/liter of the chlorides of the various metals.
Vedrana-- You cannot neutralize with sodium chloride (NaCl), you must mean sodium hydroxide (NaOH). The proper pH of rinse before flux is 5 or lower, otherwise the product will corrode before you can get to the zinc kettle. Your current procedure is bad and you will contaminate the flux.
Jeet-- Have your incoming (new) flux tested and post the results.
Regards, Dr. Thomas H. Cook, Hot Springs, South Dakota, USA
Galvanizing Consultant - Hot Springs, South Dakota, USA
Q. Dear Dr. Thomas.
Which flux salt (mono, double, triple, quadra) you recommend me to use in my batch galvanizing plant since my dryer is not really effective. Also what can I add to my flux tank to stop the zinc spattering or scattering from my kettle since my dryer is not effective as I told before.
Thanks,
Regards,
Rashad
hot dip galvanizing - borjal arab, Alexandria, Egypt
May 12, 2014
A. If you would like to try a flux extremely low in non volatile salts I suggest you try PREACT. We manufacture our flux at our plant in Freeport, TX USA from virgin raw materials to insure the lowest possible level of non-volatile salts.
Thorn Baccich, PresidentMineral Research and Development - Harrisburg, North Carolina USA
May 13, 2014
Thanks for your participation Thorn! We don't recommend one proprietary product over another in this forum, nor can we ask our supporting advertisers who are making this forum possible to bear the costs of postings which steer the potential customers away from them and to non-advertisers unwilling to share in the costs, so we had to abbreviate your posting a bit.
But you are implying that low-volatiles in flux is an important issue, and it sounds to me like a valid technical point. Thanks!
Regards,
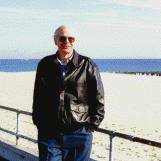
Ted Mooney, P.E.
Striving to live Aloha
finishing.com - Pine Beach, New Jersey
May 2014
A. Ted, I can appreciate your comments. The best expert to ask regarding the problems of high levels of non-volatile salts in a galvanizing flux can cause is Dr. Thomas Cook. He has done a great deal of work testing fluxes. He is by far the best expert I know on this topic.
Regards,
Mineral Research and Development - Harrisburg, North Carolina USA
May 15, 2014
A Guide to process Selection & Galvanizing Practice"
by M. J. Hornsby
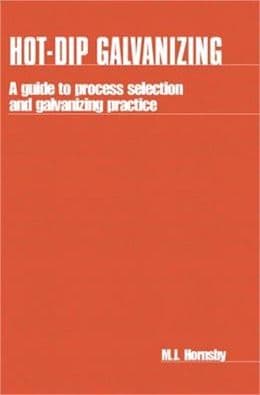
on AbeBooks
or eBay or
Amazon
(affil links)
Hi again. No question about Dr. Cook's expertise, which has been demonstrated countless times on this site, let alone in many other venues. However, unless there are several suppliers of fluxes with low non-volatiles, the topic becomes a public discussion of a single proprietary product -- which is always a disaster for a dozen reasons ( huh? why?).
I am quite certain that if a responder offered a scathing review of a proprietary product we'd quickly hear from that company's lawyers, whereas all would be well if the readers heard only one side :-)
Thanks.
Regards,
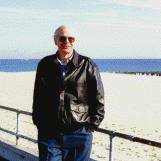
Ted Mooney, P.E.
Striving to live Aloha
finishing.com - Pine Beach, New Jersey
May 2014
May 15, 2014
A. Dear Mr. Rashad Ahmed;
Generally double salt flux is used among batch galvanizers. However you can use higher ammonium chloride content but it will cause excessive fume.
If you don't have a dryer you can:
1- Heat up your flux to 60 °C with a simple boiler and heat exchanger coils
2- Use flux surfactants (will be cheap and easy to use)
3- Soprin has an flux additive for exactly that purpose
But please keep in mind that nothing will be as advantageous as a good drying system.
- Doha, Qatar
May 16, 2014
Q. Hi friends,
Mr. Ozge. Thanks for your existing reply and I appreciate your help a lot. Regarding fumes, no problem; we have our effective fume suction unit.
So what is the best flux to give us best quality and consumption?
As well do you an idea about pickling accelerator?
By the way what do you do in Doha?
Thanks
Regards
Rashad
- egypt , cairo
A. Dear Mr. Rashad Ahmed;
For quality issue, actually I have never noticed any difference between double salt and triple salt. Moreover if you can eliminate fume, and I am assuming that your pickling is not perfect (as you want to accelerate your pickling) triple salt can give you a better solution. Although the consumptions are nearly the same, triple salt is cheaper than double.
I have seen a chemical supplier is offering pickling accelerators, but I have never used it or seen any plant using it. I am not sure chemical approach to accelerate pickling can efficiently work. Maybe Dr. Cook can explain that subject to us.
But, kinetic approach for accelerating works perfectly. You can heat up your acids to 30 °C, and give some agitation by a mixer or blowing air in. By applying both, you can double your pickling efficiency. But be careful not to exceed 30 °C much. It will cause excessive acidic gas extraction, and also it makes Dr. Cook so much angry :-)
I am currently installing a galvanizing plant (14.5 x 1.8 x 3 m kettle dimensions) and a fabrication unit (fully automated pole production line and road barrier line). Actually main equipment installation is finished; we are doing the auxiliary fabrications and waiting for governmental approvals.
- Doha, Qatar
May 22, 2014
Q. To reduce the Fe from flux bath I put in H2O2 . how can I remove the foam that appears on the bath surface? Because in this foam is very much Fe and I want to get it away from the flux bath .
Best regards,
- Bucharest , Romania
May 27, 2014
A. Dear George,
Didn't you filter your flux after adjusting pH and adding peroxide?
- Doha Qatar
June 1, 2014
June 18, 2014
A. Dear Sir...
Better you do continuous flux filtering system which helps to remove Iron content from Flux bath.
Gunatit Builders

Manjalpur, Vadodara, Gujarat
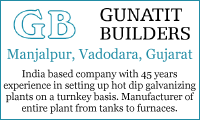
July 4, 2014
A. George,
The reason you got so much foam when you added H2O2 to the flux was that your pH is too low. You must also FIRST add aqua ammonia
⇦ this on
eBay
or
Amazon [affil links] (ammonium hydroxide) to provide OH- groups for the Fe+3 that is formed to make Fe(OH)3. Without the ammonia, peroxide self destructs to oxygen (the foam) and water.
Regards,
Galvanizing Consultant - Hot Springs, South Dakota, USA
June 18, 2014
Q. Dear sir
I need the method to analyse flux solution (Hot dip galvanizing) for iron content. The method which I have is by using KMnO4 with pink end point.
My problem is the pink end point never comes while analysing flux. It's found the the solution turns greenish black which cannot assure the end point.
Please help and guide which method to be used for analysing iron in flux which can show clear endpoint.
Awaiting response soon.
Regards
Dharampal
- Jeddah, KSA
July 3, 2014
A. Sir,
Best titrant for Fe+2 is potassium dichromate with sulfuric acid/phosphoric acid buffer and sodium diphenylamine sulfonate. End point is from light green to deep blue.
Regards,
Galvanizing Consultant - Hot Springs, South Dakota, USA
Q. Dear Dr. Thomas
Thanks for response regarding Fe+2 analysis.
Can you describe a complete method to analyse hot dip galvanizing flux for iron content using potassium dichromate?
Thanks awaiting reply
- Jeddah, saudi arabia
July 5, 2014
Dear Sirs,
for flux treatment (Fe reduction) we made lots of experiments and one of the results is that the amount of chemicals (both H2O2 and NH4OH) is reduced when first adjusting the pH value by adding NH4OH and the oxidate the Fe(II) to Fe(III) and with this, Fe(III)hydroxide precipitates. But it is highly advised to "stop" oxidation and precipitation when the pH value decreases <3. For lower pH values the floc becomes bad and the separation of Fe(III) hydroxide with chamber filter press is much more difficult. There is a De-Iron-Unit on the market which considers all these items and treats the flux in parallel to the HDG process
- Recklinghausen, NRW, Germany
September 19, 2014
Q. We are using nickel base Flux chemical and the baumé is 14 only. I need to increase the baumé. How can I increase it?
Elango Edison- Tamil nadu, India
November 21, 2016
November 22, 2016
A. Sir:
Nickel in the zinc is effective ONLY with silicon semikilled steels (e.g. silicon between about 0.04% and 0.14% Si). There is very little steel like this in the USA and nickel in the zinc at 0.05% nickel is not so popular as it was some years ago.
I am not aware of any proof that nickel chloride in the flux is effective in controlling silicon semikilled steels.
I did some experiments with auto catalytic nickel plating (a few microns before a regular flux) and it did work on silicon semikilled steels. There were problems in controlling the nickel content in the auto plating solution depending on temperature, pH, and some other variables. A flux company in Germany said they did not make nickel containing flux because after it was contaminated there was no way to get rid of it.
Because nickel causes lung cancer, I NEVER recommend the use of nickel in galvanizing because it is quite likely to become airborne.
Regards,
Galvanizing Consultant - Hot Springs, South Dakota, USA
December 17, 2016
Q. Good day for all,
My chemical analysis on flux solution is:
Zinc(zn) total = 8.5
Chloride (Cl) = 17.8
Total Iron (Fe) = 1.67
Ammonium Ion (NH4) = 0.32
CALULATED VALUES
- Ammonium as Ammonium Chloride (NH4Cl) =0.95
- Zinc as Zinc Chloride (ZnCl2) = 17.71
What do you think of this Analysis,
And what is the advice to get the best results?
Regards,
- Saudi arabia
December 17, 2016
A. Sir:
I presume your numbers are percent?
How was the Zinc determined? ICP or AA
How was the ammonium ion determined? Kjdahl or Specific Ion Electrode
How was the iron determined?
IF!! your numbers are correct?? There is not nearly enough ammonium chloride for good galvanizing. The iron is a bit high.
Regards,
Galvanizing Consultant - Hot Springs, South Dakota, USA
December 20, 2016
Q. Dr.Cook,
Thanks for your kind reply.
This is the result from the report; we use double salt flux.
What is your opinion in this analysis, and what precautions should I take?
Zinc(zn) total = wt% 8.5
chloride (Cl) = wt% 17.8
total iron (Fe) = wt% 1.67
Ammonium ion (NH4) = wt% 0.32
CALULATED VALUES
- Ammonium as Ammonium Chloride ( NH4Cl) = Vol% 0.95
- Zinc as Zinc Chloride (ZnCl2) = Vol% 17.71
Your guidance is always appreciated.
- Saudi arabia
Q. Dear sir,
My flux gravity is 1.18 and its temperature is 40 °C, and I'm also doing online flux filtration. Iron content in flux is 4.5 gm/lit.
Now I am struggling from more ash formation in zinc bath and also heavy ash marks on material.
I am using platinum flux.
Please advise me how can I solve the problem?
Thanks.
- davangere, Karnataka, India
March 17, 2017
Q. Hi,
I prepared the flux solution from the reaction of zinc chloride with ammonium chloride. When analyzing the solution, the ratio of zinc chloride was 21.66% while ammonium chloride was 15%. When the solution was left for a period of time, a precipitate was formed. I do not know what is the reason? It also gives little adhesion. I hope you will help me to give the exact proportions of the reactive materials.
- baghdad, Iraq
June 13, 2017
Q. Dear Sir
I want to use only NH4CL for new fluxing tank. What will happen? Please answer me? We galvanize all kinds of structures and towers.
Myanmar Economic Corporation - Yangon, Myanmar
June 15, 2017
A. You will certainly get a lot of fume.
It might work, but it could also be that you don't get full wetting and fluxing and that results in bare patches.
You could try it in a small batch on some sample plates and see what happens, that way you don't waste a whole flux tank of materials.
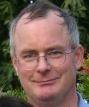
Geoff Crowley
Crithwood Ltd.
Westfield, Scotland, UK
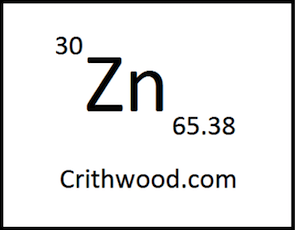
June 16, 2017
Q. Thanks sir
I also want to know the ratio. How much NH4Cl to use in 1 liter?
Please advise me.
myanmar economic corporation - yangon, myanmar
June 23, 2017
by NACE
[only rarely available]
on AbeBooks
or eBay or
Amazon
(affil links)
Hi cousin Thaw. I am not a galvanizer, but I try to listen and learn -- and I think in your eagerness to get started you have not slowed down to listen closely :-)
I think the answer was essentially: "It's a bad idea and liable to not work well for several reasons; but if you insist on trying it, then run some experiments on a few small parts". Demanding that people provide the details on exactly how to do what they've repeatedly suggested that you not do might be considered badgering, but good luck :-)
Regards,
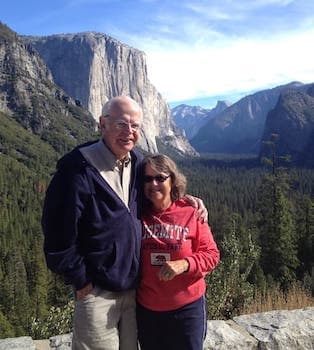
Ted Mooney, P.E. RET
Striving to live Aloha
finishing.com - Pine Beach, New Jersey
June 2017
June 23, 2017
A. Sir:
45 years ago I did experiments using NH4Cl alone and ZnCl2 alone for hot dip galvanizing fluxes. NH4Cl dried very quickly on the steel but corroded the steel very badly. ZnCl2 never dried and the steel did not corrode. The NH4Cl flux gave much skimmings (ash) and smoke. The ZnCl2 spattered badly when going into the molten zinc. In the end both steel samples galvanized fairly well with about 3 mils of zinc (75 microns). Do not expect good results from ammonium chloride alone or zinc chloride alone.
Experiments with hot 160 °F (71 °C) triple or quadraflux dried quickly and did not corrode and gave an excellent result. The steel must be in the hot triple salt solution long enough to heat the steel completely so the heat of the steel dries the flux from the inside.
Regards,
Galvanizing Consultant - Hot Springs, South Dakota, USA
Q. I'm a process engineer at a hot dip galvanizing plant in Morocco. We are facing a problem with the flux solution: the ACN is going up and we can't explain the ZnCl2 consumption.
We use a double salt flux with temperature 45 °C. Our ACN went from 0,8 to 1 in about 4 months.
I would be very thankful to you if you can help us out on this issue.
Regards,
- rabat, rabat, morocco
December 11, 2017
A. Sir:
If you are using ammonium hydroxide (aqua ammonia) to raise the pH of your flux then this is the same as adding ammonium chloride. Each U.S. gallon of ammonium hydroxide is the same as adding 11 pounds of ammonium chloride.
If this is not the "problem", then perhaps whoever is dong the testing may be doing it incorrectly.
Regards,
Galvanizing Consultant - Hot Springs, South Dakota USA
December 21, 2017
Q. Thank you sir for your quick reply.
Actually we are using ammonium hydroxide 25%, and for each 1000 l of ammonium hydroxide we're adding 275 kg of zinc chloride to correct the ACN.
- Rabat, Morocco
December 22, 2017
December 24, 2017
A. Sir:
By adding 1,000 liters of 25% aqua ammonia (expressed as percent NH3), and 275 Kg of zinc chloride, you are indeed increasing your ACN.
The Kg of ammonium chloride in 1,000 liters of 25% NH3 is:
0.25 * 1,000 L * 0.91 * (53.45/17) = 715 Kg ammonium chloride.
The resulting ACN of your additions are:
ACN = (715 Kg/275 Kg) ACN = 2.60
In the above calculation: 0.25 is the % NH3.
The 0.91 g/ml is the density of the NN3 solution.
The 53.45 is the molecular weight of ammonium chloride.
The 17 is the molecular weight of ammonia
The real question here is WHY would you need to add 1,000 liters of NH4OH to neutralize excess acid in your flux? This is enough ammonia to neutralize about 2,000 liters of 17% HCl. You must not have a rinse tank between your HCl tanks and your flux OR you have an old rinse solution that is stagnant for many years? Perhaps clean water is costly in your country.
I do not normally give any advise without knowing more about a plant, however skimmings or ash possibly could be added to your flux to both neutralize acid carry-over and to keep your ACN down.
What is the density (in Be' units or g/ml) of your flux.
Your operation is not in control.
And by the way I do not like double salt.
Regards,
Galvanizing Consultant - Hot Springs South Dakota USA
Q. I want to know which type of flux used in tower galvanising unit, and tell me solution used in flux?
gopal dwivedi- New Delhi, India
July 21, 2018
A. Sir:
The best results that I have found for flux is: 12 to 14 degrees baumé (measured at room temperature; 4.2 pH; temperature 160 °F (71 °C); below 1% sulphate; non-traditional non-volatiles below 7,000 (Ca, Mg, Mn, K, Na expressed as chlorides). The ACN which should be 1.6.
Unfortunately, many commercial fluxes sold in India, China, and Europe are made from recycled materials or poor starting materials and give poor results in galvanizing. Only by testing the actual process flux can suitability be determined. Fortunately in the USA there is one excellent flux manufacturer.
Galvanizing Consultant - Hot Springs, South Dakota USA
July 27, 2018
Q. Sir galvanizing plant running in every type of material. purlin start the production 2 mm this material is red in 5 min flux ph 2 and specific gravity 1.17 g/ltr
yashwant ashok patil- sangli Maharashtra
September 22, 2018
Hi Yashwant. Can you please post more words, so we can be clear exactly what the problem is before the waters get muddied by people misunderstanding your question? :-)
You're saying that after 5 min in the flux tank (why that long?), purlins (bare steel? what grade?) made of 2 mm thick material turn red (bright red or the color of rust?) for some unknown reason? Then they galvanize correctly anyway, or they galvanize unsatisfactorily, or you stop the process and don't even attempt to galvanize them? Thanks!
Regards,
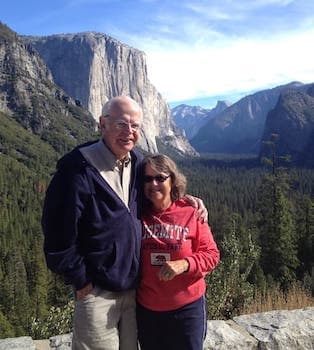
Ted Mooney, P.E. RET
Striving to live Aloha
finishing.com - Pine Beach, New Jersey
September 2018
Q. Dear sir, I would like to ask that why the flux color is red and what's the chemical reaction in this process?
I would like to ask what's the correct chemical addition of flux.
Mohd TariqGalvanizer - Ghaziabad,uttar pradesh, India
September 5, 2019
A. Sir: The red color is Fe(OH)3 and is likely from too high of pH. Check the on-line library on this website for a better understanding.
Regards,
Galvanizing Consultant - Hot Springs, South Dakota
September 15, 2019
Q. Respected Dr. Cook: Sir I would like to know whether this is the correct chemical addition to preparing the new preflux if we are using ready made flux. Also with respect of this standard, i.e., pH is 4 to 5, specific gravity is 1.16 to 1.25 and addition is 1 litre water+ 275 grams ZnCl2 + 715 grams NH4Cl + 250 ml aqua NH3. Give your comment soon.
MOHD Tariq [returning]Salasar techno engineering ltd - Ghaziabad india
September 17, 2019
Q. Our company is involved in HDG of Lighting Poles.
What Kind of Flux & Degreasing solution would suit us?
Our products have hardly any oil & paints on them.
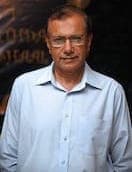
Mukhtar Ahmad
pvd process engineer
- Lahore, Pakistan
January 25, 2021
A. Degreasers: It's quite possible to galvanize clean steel without a degreaser, but if quality of finish is important, not advisable. A good degreaser will remove oils that you hardly thought were there. but which will inhibit the acid from cleaning the steel. Sources include: MIG welding sprays, lubricant in a bandsaw, drilling fluid, and lastly one often not thought of - dirty hands handling the steel. Degreasers come in several formats. Perhaps most common and low cost is an alkali tank of say NaOH heated to about 40-60 °C, and full immersion for 203 minutes. The downsides of this are energy cost (though recovered heat from the kettle might be used), the need to rinse off the alkali before putting the steel into acid, and the space in the shop. Advantages: perhaps lowest cost degreaser. Improvements include chelates and surfactants, available as proprietary brand degreasers.
Next are acidic degreasers. Reputed to not work as well, but often sufficiently, this removes the acid-base problem requiring rinsing.
And perhaps lastly, in acid degreasers. Additives to add to acid tanks to remove a little oils. Downside here is the oil has to go somewhere, and often concentrates on the surface of the tank, and then on the upper tank walls as something that looks like road tar. And that can then come off, onto the steel, and stay there until the zinc, where it burns off, and the smoke causes problems in the fume filter.
Fluxes: usually a mixture of zinc chloride and ammonium chloride. The ratio of these two is varied, and you will find as many opinions on what this should be as people you ask. Common ratios are double salt (2:1 ammonium to zinc chlorides), triple salt, and quadruple salt. The ammonium causes the fume, so higher the ratio, more fume. Probably the most common is double salt, but this varies by region and continent (which really means is habitual and gets copied in local areas).
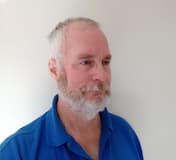
Geoff Crowley, galvanizing consultant
Crithwood Ltd.

Bathgate, Scotland, UK
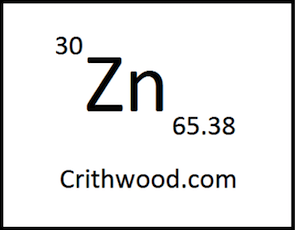
January 26, 2021
Q. Hello!
Our hot dip galvanizing experience is approximately 2.5 years. We use a double salt solution as a flux. We started working at a density of 28 Baume and a temperature of 40 °C. However, we later decided to switch to a lower concentration of double salt: 18-20 Baume at 60 °C.
After some time, problems with the flux began: the ash on the surface of the zinc melt acquired a black resinous appearance (please see the photo). And black sludge remains on galvanized parts (please see photo).
According to the results of spectral analysis, the presence of metallic zinc, zinc chloride, iron, silicon and aluminum was found in the composition of these black residues on the products. And if the ash gradually acquires a normal appearance, then we still cannot get rid of the black sludge on the products.
Maxim Matiuschinprocess engineer - Russian Federation
January 30, 2023
Ed. note: your e-mail bounces
A. The black resinous stuff on the zinc surface is flux. If you take straight flux powder and sit it on the zinc it will go like that.
You were at 28 Be, but that's too strong and too cold; and then you went to 18-20 and 60 °C and that's too weak but temperature OK. A good target is 23-27 Be, or 1.19 to 1.22 SG.
The black deposits on the job are flux residues. It can be washed off with water.
But its presence there in those places on the job indicates poor skimming practice.
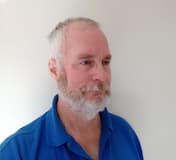
Geoff Crowley, galvanizing consultant
Crithwood Ltd.

Bathgate, Scotland, UK
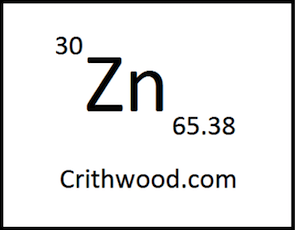
February 3, 2023
Q. Dear Geoff,
Do I understand correctly that if the presence of flux residues on the parts is due only to incorrect skimming, then their formation during the combustion of the flux is the norm and is not associated, for example, with an incorrect balance of zinc chloride and ammonium chloride concentrations?
- Russian Federation
February 13, 2023
Ed. note: your e-mail bounces.
A. Not quite. That is gets onto the steel and left there like that can be avoided by better skimming. But the formation on the zinc surface of the black sludge (molten flux) is probably also avoided.
The ratio of the ammonium chloride to zinc chloride is important, and should be somewhere between 2:1 and 3:1 (double salt, triple salt as they are called).
Most galvanizers can't tell the difference between double and triple salt in operation. Triple salt makes more white fume (its the ammonium chloride that makes it and higher concentration of that means more fume). But get beyond those limits especially towards the 1:1 range and more black deposit on the kettle. Have you had this measured in your flux? If it gets out of ratio, its easy just to add the low component until back to specification.
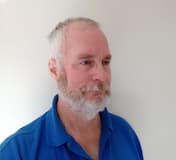
Geoff Crowley, galvanizing consultant
Crithwood Ltd.

Bathgate, Scotland, UK
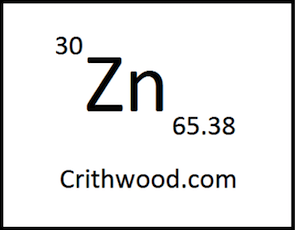
February 15, 2023
Q, A, or Comment on THIS thread -or- Start a NEW Thread