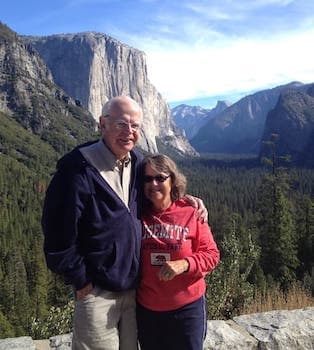
Curated with aloha by
Ted Mooney, P.E. RET
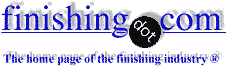
The authoritative public forum
for Metal Finishing 1989-2025
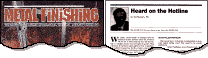
-----
"Two-step" black anodizing w/tin sulphate & other metal salts: Q&A

Quickstart:
Anodized aluminum can be left aluminum colored, but it's common to dye it. The anodized coating has millions of tiny "drill hole" pores. It can be colored by putting the freshly anodized item into a tank of dye, absorbing the dye into the pores, then "sealing" it with boiling water or other processes to hydrate/swell the aluminum to close the pores.
Organic dyes are subject to fading. So, architectural anodizing may instead be colored by electrocoloring or two-step anodizing, plating tin, nickel or cobalt into the pores with AC current.
Sometimes electrocoloring is done, and then followed by organic dyeing.

Ed. update: The above link, like most links, was quickly allowed to break. Thankfully, the Internet Archive preserved a copy here
Please consider a donation to The Internet Archive, our best defense against disappearing technical resources.
Q. Hello,
I am looking to perform an electrolytic colouring on Aluminium series 6061. I need to reach a matte black finish using this process.
The steps that I follow in the process are the following:
1. Degreasing
NaOH (10 g/L) + Na2CO3 (15 g/L)
60 °C / 10 min.
2. Chemical etch
Solution containing 15 % H2SO3 and 5 % HNO3
45 °C / 10 min.
3. Polishing
Solution containing 60% H3PO4 and 5% HNO3.
85 °C / 2 min.
4. Sulfuric acid anodization
Concentration: 200 g/L
Temperature: 22 °C.
Current density : 1.2 A/dm².
Anodization length : 60 minutes (to obtain a 20 microns layer).
5. Electrolytic coloring
I have tried different bath composition : (using either a stainless steel electrode or a Titanium with MMO one)
• 'Copper sulfate / 40 °C / 20 Volts (AC) / 55 minutes. Result: light brown but the oxide layer went from 24 microns to 4 microns during the process!
• Cobalt acetate / 40 °C / 16 Volts (AC) / 55 minutes. Result: Non-uniform brown color.
From what I have read in the literature, the problem might be that the pore diameters of the Aluminium pieces are not large enough to perform electrolytic colouring.
Therefore, I tried to perform a second anodization (using phosphoric acid to widen the pores of the Aluminium piece) after the sulfuric acid-anodization.
The solution I used for the phosphoric acid anodization is the following : Phosphoric acid (80 g/L) and sulfuric acid (10 g/L). However, given the low conductivity of the phosphoric acid I wasn't able to perform the anodization.
I also tried to widen the pores of the Aluminium piece by heating the piece in a 5% solution of phosphoric acid for two minutes. The thickness of the oxide layer went from 28 microns to 18 microns. After that I tried to perform en electrolytic coloring using the following conditions :
• Nickel sulfate / 40 °C / 25 Volts (AC) / 12 minutes.
But I did not get any coloration at all.
Has anyone experienced similar issues when trying to perform electrolytic colouring on an aluminium piece series 6000 that had been subjected to a sulfuric acid anodization process before?
Could anyone who have some experience using phosphoric acid anodization on aluminium series 6000 give me some good advices on how to perform the process to be able to make the electrolytic reaction work afterwards?
Also, does anyone have some suggestion regarding the best conditions/metal to use in the electrolytic reaction in order to reach a matte black finish on the Aluminium piece?
Thank you very much for your help!!
Merry Christmas!
John
- Quebec
December 20, 2024
⇩ Related postings, oldest first ⇩
Q. I do LASER engraving on anodized aluminum for botanical plates that are used outside. My supplier says that this material is for exterior use. However, after a few years the color on the plates seems to fade, especially on the ones facing south. I would appreciate your thoughts. Could this be UV rays causing the problem, and is this normal for anodized aluminum? I've sent a sample to my supplier for evaluation.
Thank you,
Bill KramerLECOR Enterprises, Inc.
1998
A. Sir,
Every anodize dye has a different lightfastness rating, meaning how well it hold up to outdoor light. Some dyes are not suitable at all for outdoor use.
Also, a poor seal could cause color fading.
- Long Island City, New York
A. Bill,
You may want to look into electrolytic or the 2-step color anodizing. Light fastness is excellent.
A. Anodizers specializing in architectural applications will be most likely able to help you. They will need a 2-step (anodize then inorganic dye) process. The organic dyes just don't last as long in UV light.
F.A. Sandy Donaldson- Minneapolis, Minnesota
A. Colors can only come from two sources; chromophores in organic chemicals that result from double bonds or triple bonds or a few other special bonds; in inorganics they come from metal ion complexes. UV light adds sufficient energy to break double or triple bonds so organic dyes are more susceptible to sunlight degradation. Try the inorganic metal dyes for outside use.
Dave Fairbourn- Sandy, Utah
Multiple threads merged: please forgive chronology errors and repetition 🙂
for Shops, Specifiers & Engineers
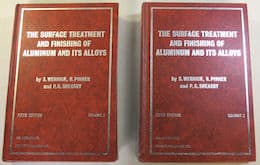
avail from eBay, AbeBooks, or Amazon
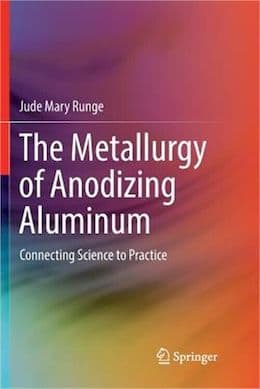
avail from eBay, AbeBooks, or Amazon
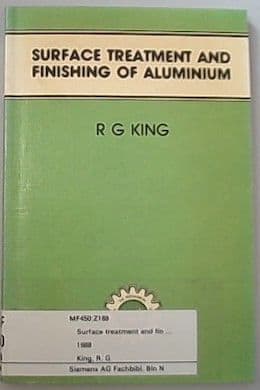
avail from eBay, AbeBooks, or Amazon
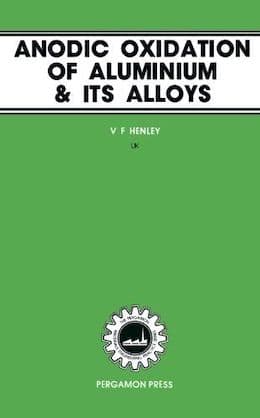
avail from eBay, AbeBooks, or Amazon
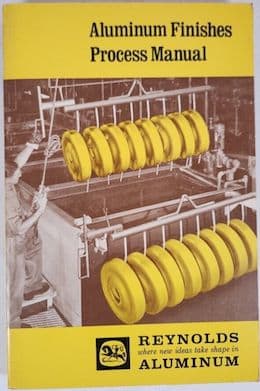
avail from eBay, AbeBooks or Amazon
(as an Amazon Associate & eBay Partner, we earn from qualifying purchases)
Q. Accelerated test of light fastness of colored anodized aluminium seems to be made by ISO 2135
The Blue scale for evaluation is not easy to find anywhere and it is different from that one used for textile light fastness Could somebody tell me where can I find this special Blue scale to make this ISO 2135 test?
Many thanks
Gianmarco Rizzotti- Busto Arsizio -Italy
2000
Q. DC/AC equipment for colour anodizing? I am looking for information on how to specify ripple, control, etc.to get the best choice for electro coloring anodizing in tin sulphate solutions.
Thank you, very much.
Gustavo C. GiraudoArgentina
1998
A. I think such specifications are confidential information of manufacturers of AC/DC equipment who have spent a lot of money to develop them.
The best way to have such equipment is to contact with the AC/DC power suppliers' manufacturers and buy a suitable one.
aluminum extrusions & finishing - Istanbul, Turkey
A. I very respectfully disagree with Mr. Ulucak just a bit, because there are also people who feel that complicated & expensive proprietary waveforms are a waste of money in tin-based electrocoloring, and that all that is required is low voltage AC. So I think that readers should hear that side of the issue as well as listening to sales pitches about the benefits of special waveforms.
In addition to the previously linked article on the Finishing and Coating website, and the Talat lecture, readers may also review "Electrolytic Coloring of Anodized Aluminum Using Tin Electrolytes" by Gohausen & Schoener (Plating & Surface Finishing, Feb. 84) and "Electrolytic colouring of anodized aluminium on tin basis" by Sopová & Zemanová for more great intros to the topic.
Best of luck.
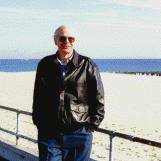
Ted Mooney, P.E.
Striving to live Aloha
finishing.com - Pine Beach, New Jersey
Multiple threads merged: please forgive chronology errors and repetition 🙂
Q. I was reading your response above and I'm interested in know more about electro coloring anodizing, at this time I'm coloring with Tin solution, but I have doubts about output voltages, I have an 3000 amp 30 volts AC coloring power supply by Dynapower, with five steps:
1.-dwell time
2.-pretreatment
3.-stage # 1
4.-stage # 2
5.-add
Where can I get "Electrolytic Coloring of Anodized Aluminum Using Tin Electrolytes" by Gohausen & Schoener (Plating & Surface Finishing, Feb. 84)? Or a newest ?
- Guadalajara, Jalisco, Mexico
2000
A. You may be able to get a copy from the publisher of Plating & Surface Finishing, the Nat'l Assoc. of Surface Finishers. Contact their publications department at www.nasf.org. If not, there are many very similar articles available by googling.
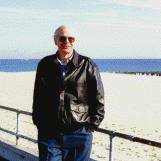
Ted Mooney, P.E.
Striving to live Aloha
finishing.com - Pine Beach, New Jersey
QUICKSTART:
Yasar and Harmanto seem be speaking of true BLACK coloring. But readers should know that the dark gray to charcoal color we see on hard anodized pans isn't dye -- it's just the natural consequence of hard anodizing (thick anodizing) on aluminum alloys which contain other metals which discolor it.
Courtesy of Drew Nosti and Anodizing USA, here is a typical hard anodized component:
Q. Could Tin sulphate be used for coloring (black) aluminum utensils (AA3003 alloy) in hard anodizing process? If yes, is it harmful for health.
Yasar Bayraktar- Seydisehir, Konya, Turkey
2003
A. Salam:
tin sulphate is a green chemical, not harmful. But blackening with that is not an easy technique.
It's better to trial first according to additional chemical, concentration, timing and current density used.
- bangka island, indonesia
Anolok Finish for Aluminum Extrusions?
Q. I am into selling Aluminum Extrusions for architectural projects. I would like to know the process how to color an aluminum extrusion, preferably from a mill-finished aluminum extrusion into an Anolok (color) finish.
Thank you.
Allan JavierAluminum Extrusions Trading - Pasig, Metro Manila, Philippines
2004
A. That process involves first anodizing the parts and then transferring immediately to a plating tank containing usually tin or nickel salts. A.C. is passed to the parts by ramping up the current slowly and usually bronze or black colors are obtained.
Leeleongtee [last name deleted for privacy by Editor]- Malacca, Malaysia
A. Thanks Leeleongtee.
Hi Allan. Leeleongtee's answer is right is one sense but incorrect in another sense :-)
You can get a UV-stable inorganic black color (similar in color to Anolok) through the method which he describes. However, that is not how Anolok obtains the color in their process.
Luck & Regards,
Ted Mooney, P.E.
Striving to live Aloha
finishing.com - Pine Beach, New Jersey
Multiple threads merged: please forgive chronology errors and repetition 🙂
Can't get black finish in electrolytic tin method
Q. Hi, My name is Richard Martinez. I work in anodize plant in Mexico.
My problem is that our black isn't black... to make the color we use a vat containing tin, water and a little sulfuric acid like conductor. Our current capacity of electricity is 21 Volts. our electrocolor goes from d-100 (champagne) to d-400 (black) but our 400 looks like coffee when is soaked.
We also do some works for the electronic industry, but in that industry generally use a hard alloys like 5052 and others which can't take the black color...
so.. how can we achieve the black color? what other methods or solutions exists to do that finish when the mil-a-8625 type II is used?
Quality Control - Guadalajara, Jalisco, Mexico
April 6, 2009
A. Hi Richard,
There are many possible reasons for not being able to get black and probably a combination of several of these.
1) Anodising.
To get sufficient tin in the film the anodic film should be at least
15 microns thick. The anodising bath should be held at 20 °C. The current density should be 12 - 15 amp/sq.ft. These conditions are those use in good anodising practice.
2) Electrocoloring
The tin concentration for black needs to be higher than for pale shades. Tin should be 10 - 15 g/l and sulfuric acid 10 ml/l.
To minimise the loss of tin due to atmospheric oxidation use an antioxidant such as cresol sulfonic acid. This also significantly improves rate and depth of coloring.
Allow the work to soak the tin bath before applying the power which should be raised from zero to full voltage slowly.
Harry Parkes
- Birmingham, UK
Q. DEAR SIR,
WE HAVE PLATED BLACK ANODISED COMPONENTS. WHEN CUSTOMER USES THIS COMPONENTS EXPOSED TO SUNLIGHT COLOUR OF EXPOSED TO SUNLIGHT FADES TO BROWNISH AND SOME COMPONENTS COLOUR TOTALLY FADES. CAN YOU THROW SOME LIGHT ON IT.
THANKS,
PLATING MANAGER - PUNE, MAHARASTRA, INDIA
May 23, 2009
? Hi, Kamlesh. What does the vendor of the dye rate the lightfastness at?
Regards,
Ted Mooney, P.E.
Striving to live Aloha
finishing.com - Pine Beach, New Jersey
![]() |
A. SEALING is required. While the fastness of the dye is of concern, there aren't that many dyes available to our industry that are that poor that they fade within weeks UNLESS the sealing is bad or altogether skipped. Sealing is the final process used in anodizing following the dye step to swell the tops of the aluminum oxide pores shut by hydrating the Al2O3 with 6 waters of hydration Al2O3.6H2O. This swelling locks in the dye and retains the colorfastness (and heat and chemical fastness). A. Other possibilities are the coating is too thin, or poor seal. Both of these can cause premature fading in sunlight. |
A. It sounds like it may be a poor or non-existent seal. Double check that your seal is operating properly, and administer a few of the standard seal quality tests (one of the easiest rule of thumb measurements for black is to mix up a little 30% nitric and either dip the part in it or brush it on the part - depending on size. If the part looses a significant amount of color in a minute or two, your seal is bad).
Although hardcoat anodize is typically not sealed, anything dyed MUST be, or you'll see fading exactly as you've described.
Good luck!
Jim Gorsich
Compton, California, USA
A. Any organic dyes do not have good lightfastness, when in outdoor application the colour fades because UV in sunlight, the black colour is most sensitive to this, lightfastness is better with electrolytic coloring usually using tin, nickel or cobalt salt; It is possible to use a electrolytic coloring first and a organic dying in sequence;
The fade-O-meter method (a modification on the weathering test without water in the cycle) is used to evaluate the lightfastness of the anodic colored coating with a high-intensity ultraviolet mercury-arc lamp.
- Blumenau, Santa Catarina, Brazil
Q. DEAR SIR,
WE ARE DOING ANODISING BLACK AND AFTER 48 HRS IN ULTRAVIOLET RAYS EXPOSED TO SUN COLOUR GOES AWAY.SO IS THERE ANY TEST TO CHECK WHETHER DYE OR SEALANT IS PERFECT. HOW MANY HRS OF ULTRAVIOLET TEST PERIOD.WHAT IS COST OF UNIT. IF WE WILL GO FOR COLOUR DYE OTHER THAN BLACK SAME PROBLEM DO WE FACE OR IT IS THE CASE WITH BLACK DYE ONLY. PL. GUIDE FOR THE SAME.
THANKS,
K.M.BHATT.
PLATING MANAGER - PUNE, MAHARASTRA, INDIA
June 18, 2009
Q. What is Anolok finish? Is that the same as Natural Anodized or powder coated?
Foong YLDesign - Malaysia, KL
February 25, 2012
Treatment &
Finishing of
Aluminium and
Its Alloys"
by Wernick, Pinner
& Sheasby
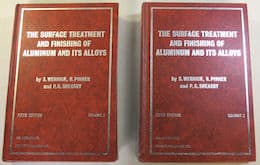
(note: this book is two volumes)
on eBay or
AbeBooks
or Amazon
(affil links)
A. Hi, Foong.
It's often desirable for anodized coatings to have color rather than being left aluminum color. While simple organic dyes are often used in anodizing, these are usually not considered robust enough for architectural work. In that case, colors are applied via metallic salts; Anolok is a proprietary name for a licensed way of doing this; "two-step electrolytic coloring" with these salts, and described by Leeleongtee, above, is another way.
Regards,
Ted Mooney, P.E.
Striving to live Aloha
finishing.com - Pine Beach, New Jersey
A. Anolok is an anodised finish primarily used in architectural applications, and a registered trademark of United Anodisers in the UK.
peter wattsUnited Anodisers - huddersfield england
Multiple threads merged: please forgive chronology errors and repetition 🙂
Q. I purchase an anodizing service loosely described as "two step" in my specifications, which also refer to tin sulphate in the process. The anodizer who currently provides this service tells me that the tin sulphate is the second step and provides the black finish my parts have after processing (the first step is merely a clear anodize). I am not familiar with this process and would like to know:
a) if it is commonly known by another name,
b) if it's a relatively common process that can be found globally (my primary machining supplier is in Singapore and I would like to see if he can provide parts complete) and
c) if the minimum lot charge of nearly double what I pay for my other anodizing jobs is justified. Thanks in advance for any assistance that might be provided.
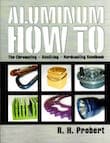
Aluminum How-To
"Chromating - Anodizing - Hardcoating"
by Robert Probert
Also available in Spanish
You'll love this book. Finishing.com has sold almost a thousand copies without a single return request :-)
Fred Tafel
- Mentor, Ohio, USA
2006
A. Anodizing without subsequent dying produces "clear" aluminum colored parts, Fred, assuming the aluminum is quite pure. If the alloy is rich in copper or silicon, even clear anodizing will come out gray to charcoal.
Anodized parts can be dyed with organic dyes (rather similar to clothes dye but optimized for aluminum), but such colors are not completely lightfast . . . sometimes not very lightfast at all. For greater lightfastness, metal salts can be electrolytically deposited at the base of the anodizing pores, and this is called two-step anodizing. And yes, most anodizing shops will have at least a general understanding of the concept but most probably don't offer two-step anodizing.
Two-step anodizing involves this second electrolytic process and it may also involve a subsequent organic dye to get a fully saturated color as well. It is a premium process, and only some shops are set up to do it, so it will be more expensive. It's hard to say from a distance whether "nearly double" is the right price, but it's not a manifestly wrong price.
Anodizers apply their decades of experience to get you a good finish, so don't make the mistake of thinking anybody can do it, and easily. That is not to assert that there are no shops in and around Singapore with the requisite experience, but it is to say that you shouldn't let a shop "try their hand" at it. You need to find a shop which already does two-step anodizing and you should have sample parts that they produced in hand before making commitments. Good luck!
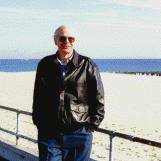
Ted Mooney, P.E.
Striving to live Aloha
finishing.com - Pine Beach, New Jersey
Q. We are designing a new production line to produce mirror image of nickel finish for aluminium profile . So far I have been unable to find out the chemical that needed for nickel finish and the way of doing it. We able to produce the mirror image by using three chemicals which are H3PO4, H2SO4 and HNO3. But we have difficulty in getting the nickel finish color (some sort like light champagne color). Seeking for expertise here.
Thanks in advance.
process engineer - Klang, Selangor, Malaysia
February 24, 2011
A. Hi, Jay.
There should be plating and anodizing process suppliers or consultants in your area who can help you get started; you do not need to independently re-invent these technologies. It sounds like you are doing brite-dipping of aluminum. To my knowledge this process will not by itself produce any coloration. After that, I think you will need to anodize the sheet, dye it with a nickel or light champagne dye, and then seal it.
Regards,
Ted Mooney, P.E.
Striving to live Aloha
finishing.com - Pine Beach, New Jersey
Q. I agree with you that brite-dipping of aluminum will not produce any coloration. Our lines do have anodizing process. But I do not have any ideas on how to produce the nickel finish after anodizing process (We have no problem on the anodizing process).
What is the chemical solution that needed (nickel sulphate)? What is the concentration and the process parameter (eg. temperature, pH...). Is this process called nickel plating? Hope that someone can give me a hand on this.
Thanks..
- Klang, Selangor, Malaysia
![]() |
A. Jay, if you are looking to give a champagne color (similar to ENP shade) to the anodized aluminum, you would have to electro color the articles in a tin sulphate solution for a few seconds. You would have to add the electro color bath to your anodizing line for this purpose.Please understand that the bath has to be regularly maintained to give consistent color. Color can also vary depending on the aluminum alloys. Winston D'Souza- Bombay, India A. Jay, Electrolytic coloring deposits metal salts into the anodized pores, usually, salts of nickel, cobalt, tin etc., using AC voltage. Yes, nickel sulphate is one of the metal salts used. Instead of re-inventing the wheel, you'll be better off getting the coloring solutions from suppliers which comes along with tech support. SK Cheah- Penang, Malaysia |
Tin sulphate concentration in electrolytic coloring bath jumps up & down
Q. Dear finishing team ,
I am a laboratory technical in aluminum extrusion company
I want to ask about coloring bath , it must be (17-19)g/l concentrated of SnSO4 ,and we reach this level of concentration but suddenly it dropped down to 13 and can't make it rise to 17 anymore , we added a lot of gallons to repair it but it still 13-14 g/l
After two months it repair it self and give us 17-19 g/l concentration without we do any thing to it !
Now a days we have this problem again , the concentration dropped to 14 g/l, we added 10 gallons which is 25kg for each gallon then the concentration rise to 16
next day we add 6 gallons and it still 16 ! we added another 6 gallons in the next day and it still 16 !
I hope to find justification for this and what should we do !
Best regards,
engineer - Amman, Jordan
June 16, 2017
Why does electrolytic coloring use AC current?
Q. I have a question about electrolytic coloring on anodized aluminium. Why this process use AC to deposit color? In my understand I think this technique like a electrolytic deposition technique that use DC to do. And I would like to tell you that I very new in this field especially about electric so I would like to apologize you if my question is like a stupid question. And the second is if I do some experiment what is the criteria to choose AC or DC to do? Because I'm very confuse about that like a electrolytic coloring technique that I mention above.
Thank you everyone to suggest me ^^.
- Bangkok. Thailand
June 19, 2017
Chalking after electrocolor dying process on anodized aluminum
Q. Good am sirs,
we have a problem about our aluminum finished product, the surface becomes powdery after our electrocoloring process and it has an effect on the color appearance of the aluminum, I hope you can help me -- we are using a tin bath and the temp. of the solution ranges from 20-25 °C, std stannous concentration is 5-15 g/L actual: 7g/L
Nickel Sulphate: 26 g/L
Thank you in advance!
- philippines
August 28, 2019
Q. Hello.
What is your opinion for black colour for anodizing aluminum in the electrocolouring bath?
What is the advantage and disadvantage?
aldoran - mosel.iraq
December 24, 2019
Bleed out problem with black anodize on a tin sulphate electro color process
Q. Hi! I'm a chemical engineer in charge of an anodizing plant of aluminum profiles for architectural purposes (6061).
We are having an issue with our darker finishings like dark bronze and black. The color "bleed out" after the cold sealing. We tested removing one profile of the rack before the submersion in the sealing bath. The difference is overwhelming.
We decided to change the sealing bath, cause we knew it was contaminated with Al, but after that there were no improvements.
After an analysis we can not ensure if the problem is the sealing or a bad deposition of tin into the pores.
Process info:
Anodize: 150g/L sulfuric, 20-21 °C, <10 g/L Al, 15 microns.
Electrocolor: 9,5 g/L tin sulphate product, 20 g/L sulfuric.
Sealing: Nickel base product.
I hope someone had dealt with some similar problem.
Thanks!
- Corrientes, Argentina
March 19, 2020
Q. Hi everyone, can someone give me information about Inorganic Black Coloring of aluminum alloys,
RFQ: ... and also some companies that process it.
Thank you.
- Forlì Italy
October 22, 2020
Ed. note: This RFQ is outdated, but technical replies are welcome, and readers are encouraged to post their own RFQs. But no public commercial suggestions please ( huh? why?).
A. Hi Paolo. We appended your inquiry to a thread which explains it. For most applications, aluminum is dyed with organic dyes, but they can be subject to UV bleaching and other causes of fading. Inorganic or metallic dyeing is done via integral color anodizing or, probably more commonly these days, two-step electrolytic anodizing which deposits a tin, nickel, or other metal in the anodizing pores.
Luck & Regards,
Ted Mooney, P.E. RET
Striving to live Aloha
finishing.com - Pine Beach, New Jersey
A. Paolo
The European Cooperation for Space Standardization has an interesting document that may get you started:
"Black-anodizing of metals with inorganic dyes, ECSS-Q-ST-70-03C"
- Green Mountain Falls, Colorado
Q. Hello,
What would be the Best Anode to cathode ratio for Anodising Bronze to Black Tin base Electrocolour.
What would be the effect on Dark colours especially Black if the Stabiliser organic additives are higher or lower.
Praveen Kumar
plating process supplier
Mumbai, India
May 30, 2021
Q. I have a problem with electrolytic coloring ...
(1.) In the past it took 15 minutes for black color, but now it takes 20 minutes
(2.) The acid concentration was increased from 20 g/L to 30 g/L without adding H2SO4, but I added Stabilizer 0.8 times of SnSO4.
I don't know what is the reason.
Standard for electrolytic coloring :
- SnSO4 ~12 g/L
- Stabilizer 0.8 times of SnSO4
- H2SO4 16-20 g/L
Chemist - Thailand
August 22, 2023
Q. I have Two Colouring Tanks for 2-step Colouring by Tin.
1st Tank is OK.
In 2nd tank, We found that the Current Density of AC step is Drop from 25A/m^2 to 10A/m^2 (AVG but MAX Current is OK) resulting in Colour too light Defect (off-shade).
DC Volt and AC Volt is in control, Chemical Concentration is in control.
I have changed the program; Increased Voltage;
I have made up 20% Chemical.
I also checked electric wires but I still found the defect in Tank No.2
Engineer - Thailand
September 15, 2023
Q. Hello everyone,
I am working in a anodizing company, we are using tin sulfate for black coloring. But we have reddish powder on black colors. What can we do to solve it?
Anodiser - Arak Iran
February 14, 2024
Q, A, or Comment on THIS thread -or- Start a NEW Thread