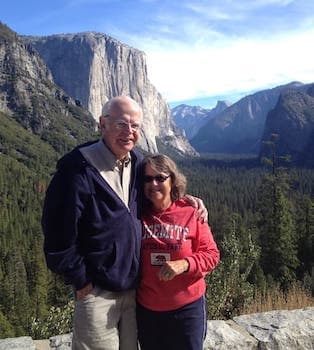
Curated with aloha by
Ted Mooney, P.E. RET
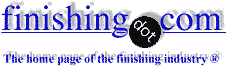
The authoritative public forum
for Metal Finishing 1989-2025
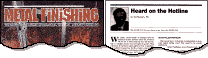
Thread 430/77
Carbide polishing
Q. Hi.
Dear reader I need some help on carbide polishing. I grind carbide that has shear angles on it. My problem is that I need something that I can polish by hand for taking the grinding marks out. I was thinking that I might have to make a fixture that meets the shear angles and diamond lap it, but that's time and money required. Got any solutions on certain hand stones that I can use for hand polishing carbide? Also the finish that I'm looking to obtain is a mirror finish.
Thanks for reading. Have a great day. Dave Preston
Tool and die - Brampton, Ont, Canada
2006
publicly reply to Dave Preston
A. All the hand stones that I know of are either aluminum oxide or silicon carbide, none of which has enough hardness to effectively polish your substrate. You'll have to use diamond in successively finer grits with suitable backings, enough pressure and SPEED. Brass, wood, wool or plastic are some examples of low cost backings. Nickel or cobalt are tougher and better. The selection will depend on shape, ease and fixturing.
Guillermo MarrufoMonterrey, NL, Mexico
2006
publicly reply to Guillermo Marrufo
A. This doesn't exactly answer your question. I have worked with and developed some processes for another carbide company that puts a mirror finish on small carbide parts. We do use small vibratory deburring mills and some exotic media. Because of the hardness of carbide, these are long time cycles and there is no problem with removing too much material.
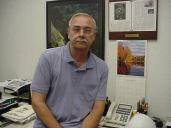
AF Kenton
retired business owner - Hatboro, Pennsylvania
2006
publicly reply to AF Kenton
Mirror Polish ID of 0.3 mm hole in Carbide
Q. I wish to polish carbide rod inner hole with ID 0.3 mm, length 26.5 mm. The finishing needs to be mirror finishing.
KL Peh- Malaysia
November 26, 2018
publicly reply to KL Peh
Ed. note: This RFQ is outdated, but technical replies are welcome, and readers are encouraged to post their own RFQs. But no public commercial suggestions please ( huh? why?).
A. I would think a process similar to the old one used for instrument jewels would work.
Basically it's just using a rolling cylindrical cradle with holes on ether end. Stainless wire close to the required diameter is passed through the cradle and the parts are strung onto it like beads on a necklace. About the distance of one part is left without parts on it.
The stainless wire is pulled back and forth with a stroke length about four to five times the length of the cradle.
The wire is rubbed with diamond paste.
- North Carolina, US
December 16, 2018
publicly reply to Robby Hewitt
Q, A, or Comment on THIS thread -or- Start a NEW Thread