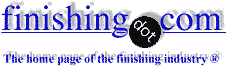
-----
Metal plating cost calculation
Q. How to calculate electroplating cost?
Andy- Jaipur, India
December 22, 2024
Tip: This forum was established to build camaraderie among enthusiasts through sharing tips, opinions, pics & personality.
The curator & some readers who publicly share their info will be less likely to engage with those who don't.
A. Hi Andy.
In addition to this thread which you posted your inquiry on, we have at least 4 other rather long threads on the subject.
• Thread 43852 about Nickel Plating
• Thread 53013 about Gold, Silver & Jewelry Plating
• Thread 23629 about General Issues
If you need help after reviewing them. please introduce yourself (student, buyer, plater, regulator, etc.), your situation, the type of components, substrate, type of plating, etc. You're not likely to make a lot of progress by simply starting over with an abstract question 🙂
Luck & Regards,
Ted Mooney, P.E. RET
Striving to live Aloha
finishing.com - Pine Beach, New Jersey
⇩ Related postings, oldest first ⇩
Q. I'm a Brazilian chemical engineer in charge of a galvanic zinc plating line, and I must find out how to calculate precisely the zinc plating process cost based on A/dm2 (or A/sq. ft.) Most of our local companies charge the service based on the weight of the finished pieces, which is a rather empirical and imprecise way. Does anyone know some kind of software or spreadsheet that could help me on this quest?
Process specification: Rotary, 20 kg, acid zinc based on potassium chloride, without ammonia
⇦ on
eBay or
Amazon [affil links] or cyanide.
Dirtiness kind: Several base metals contaminated with oil or grease.
Applied layer: 20 microns
Finishing: Trivalent passivation.
Top-coat: Synthetic resin with water solvent
Thanks for the attention.
Plating shop employee - São Paulo, SP, Brazil
2006
A. Short of a fairly impressive 3D measuring machine slaved to a computer, I doubt you can find a piece of software that make it much simpler than just setting up your own in Excel. There is a file in the Library here that shows the formulas for most simple shapes ... breakdown your parts into combinations of these shapes and start measuring.
There are a couple of letters in the archives that pertain to the same issue - and that may tip you off to a simpler method - but I believe all the advice breaks down to what I said.
Good luck!
Compton, California, USA
![]() |
A. ELECTROPLATING DATA BASED ON 100% CURRENT EFFICIENCY IS AVAILABLE ON ANY ELECTROPLATING BOOK. ![]() Ajay Raina Ludhiana, Punjab, India A. First things first, measure the area of your current products. You can use Autocad, and model the products in 3D, then the software can calculate the area. Jobshop - San Luis Potosí, México |
A. Hi Marc Dal'luce,
To add up to what Guillermo said, I would like to mention that Autocad is a simpler method to solve your concern. When you make the profile in cad, use a Pedit command and close the loop. Also extrude the same where you mention the thickness. This becomes a solid section. Use a Matprop command and you get the Total surface Area. Just to verify you can also mention density and you will find that you get the exact weight also which you can check on the part also.
But for your information, in cases like Zinc, it is that the conversion cost is higher that the material cost. So better to look at how you can ask the supplier to reduce on time rather than directly negotiating on price in line with Surface area.
Good Luck.
Supply Chain - Bangalore, India
Multiple threads merged: please forgive chronology errors and repetition 🙂
Q. Hi there,
I have recently joined a company as Works Manager that produces strip and wire formed components as well as some dye casting and the plating thereof.
The company has been around for 40+ years now and I have been given the task of solving the age old costing problem around plating with a focus on Zinc. This is all new to me as I am from Textiles.
Our formula is as follows: Zinc Metal 12-15 g/l, Sodium cyanide 24-30 g/l, and Sodium Hydroxide 70-90 g/l
We plate small items like nails, buckles and coat hanger hooks, etc.
Could someone help me with calculating the usage of chemicals per kg plated? or any other advice to get to an accurate RM usage per Kg?
Thanks
Regards
Stuart Aitken- Sacks Circle, Bellville South
February 13, 2010
![]() |
A. 1.Analyse the plating bath constituents (Metal,Cyanide & caustic soda ⇦liquid caustic soda in bulk on
Amazon [affil link]
) and adjust to your formula mentioned in your letter.Tabulate. ![]() T.K. Mohan plating process supplier - Mumbai, India A. For accurate calculations you need to know the surface being plated and the thickness. According to this all dosing amounts per Ah and therefore re-calculated on the parts. As well an complete analysis of your production must be done to have also an accurate number of labour, tooling costs and energy costs. - Sydney, Australia |
A. Stuart
I would use an amp-hour meter if you are not already. It is good for surface area plated as opposed to kg processed, such as in a barrel operation. Costs per barrel might be more appropriate in those operations as dragout can be a significant factor in chemical usage. Compare production logs with the additions log.
- Colorado Springs, Colorado
A. It's good to know the surface area, the average thickness plated, and to get a good estimate of the dragout volume per rack and per barrel in order to estimate the chemical use.
the kg can be converted to surface area if the average thickness of the part is known. To estimate dragout, a common method is to start with a still rinse with clean water and carefully measured volume. Then to rinse 10 racks or barrels in it, mix it, and analyze the solution in the tank. From this you can calculate the dragout volume. With this and the thickness being plated, you can estimate your material costs.
It is usually best to do this test on a solution that does not precipitate in the rinse tank, like and acid dip rinse. In this case you can use conductivity instead of a full analysis if you first make a graph of the conductivity of 0.2, 0.5, 1 and 2% solutions of the acid (it should be a straight line if there is no precipitation).
Typical dragout volumes for racked parts are 1.5 to 2 gallons of dragout per 1,000 square feet. For barrels, it varies with size of the barrel, but numbers in the 0.25 to 0.5 gallons per barrel are common for a 24" x 48" barrel.
This may sound complicated, but it should take < 1 hour. Add the metal plated out, and the difference between the cyanide additions and the amount of cyanide calculated by dragout is how much cyanide is lost due to decomposition.
consultant - Cleveland Heights, Ohio
How to make ballpark cost estimate for general electroplating processes?
Q. I am working on cost model for Powertrain components.Could somebody help me to understand (or refer to a right source of data) how I can make rough estimate of Zinc plating, e-coating, anodizing, chroming and impregnation.
I am looking for some industry standards:
- $/per kg of part's weight or - $/per sq.m of part's surface.
Thanks in advance for your professional assistance.
Tatyana
automotive cost engineer - Detroit, Michigan, USA
June 29, 2010
A. Hi, Tatyana. I've seen estimating handbooks for many different industries, especially the construction industry, but regrettably have never seen one for electroplating services. In earlier times a fakebook like that would be a good enterprise for a semi-retired metal finisher to develop but I don't think there's a sufficient market for anyone to undertake this :-)
I think you'll have to rely on quotes from plating shops or hire a plating consultant to put together such figures for you. Good luck.
Regards,
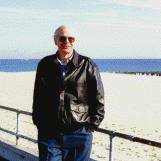
Ted Mooney, P.E.
Striving to live Aloha
finishing.com - Pine Beach, New Jersey
A. The auto industry is the last place that this will work as companies will cancel a contract for as little as a tenth of one cent per part. It is a cut throat industry with JIT being a costly driving force for the vendor.
James Watts- Navarre, Florida
A. Tatyana ... Unfortunately for you James and Ted are right. I spent 10 years in the estimating department of a good sized metal finisher. There are so many variables that come into play in job costing that I could probably write several hundred pages on the subject. Maybe I will...if someone would buy it. I can tell you this though....the main drivers of finishing costs are cost of chemistry, the cost of waste treatment of that chemistry and of course labor. They all change depending where the finishing shop is located. The only way to determine what you are looking for is to shop around. After a while you will get a good idea of your costs.
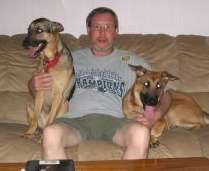
Tim Hamlett, CEF
- West Palm Beach, Florida, USA
Q. I have heard that there is a software which regulates the plating thickness and also calculates the areas too, does anybody know about it.
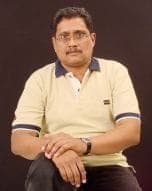
Ravi Chandavarkar
plating shop employee - Mumbai, India
October 14, 2013
A. Hi Ravi. There are several brands available, but we don't make commercial suggestions in this forum (why?). Google terms like "electrochemical modeling software for plating". They often involve calculating exact placement of anodes, parts, virtual anodes, and plastic shields to try to achieve a more even thickness distribution. Generally this software is presently for the more exotic needs rather than something you see in many shops.
Regards,
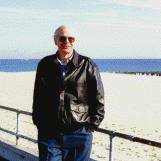
Ted Mooney, P.E.
Striving to live Aloha
finishing.com - Pine Beach, New Jersey
How to do a quotation?
Q. Hi, good day everybody.
Today I am here because I have a couple of doubts; I got a new job in a plating plant and one of my responsibilities is to do a quotation of the cost to process different pieces.
I have 3 lines conversion chrome trivalent (C.C.T), electroless nickel and stainless steel passivate.
On nickel line I have
Soak cleaner
Electrocleaner
Acid dip
and Mickel
on C.C.T. I have a soak cleaner
deoxidize solution
and finally C.C.T.
on [stainless] steel passivate line
soak cleaner
citric acid
⇦ on
eBay
or
Amazon [affil links]
sodium dichromate
My problem is I how I can know how much chem I am using on my pieces in the nickel bath; I don't have problems on nickel because the nickel metal is fixed on the metal base, and same with C.C.T.
But how I can know on soak, electro, acid dip, sodium dichromate and deoxidize?
I am processing pieces and doing the respective concentration analysis but the concentration doesn't change. I am pretty sure that my analysis is okay -- so somebody know how I can get these quotations?
Could I have it with the size of the pieces?
- agua prieta, Mexico
September 12, 2019
![]() |
A. No one can even make a guess until you get some basic information together. Start here: ![]() Jeffrey Holmes, CEF Spartanburg, South Carolina A. Hi Aaron, ![]() Rachel Mackintosh lab rat - Greenfield, Vermont |
Thanks both for your answers. Rachel, I will take your advice to search the history of purchases and see how many parts we worked in last year; thanks for that, hope you be fine, best regards,
- AP , Mexico
Plating Chemical Usage Estimation
Q. Hello All,
I have been assigned the task to estimate the consumption of chemical utilized in my surface finishing shop.
There is a diverse range of chemical processes in our industry.
How can I estimate chemicals quantity required for the Nickel, Cu & Zn Plating.
SHOP EMPLOYEE - PAKISTAN
October 19, 2019
A. Hi Syed. We appended your inquiry to a thread with 4 good answers. Please get back to us with your follow-up questions.
Regards,
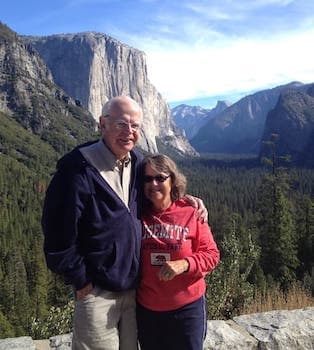
Ted Mooney, P.E. RET
Striving to live Aloha
finishing.com - Pine Beach, New Jersey
Q. Dear sir,
My name is Kumar. I am working on bright steel chrome plating. How to calculate chrome plating area, and cost, and chemical consumption, and how to add chemicals. Tell me about it sir
Regards
- Hosur, Tamil Nadu, India
June 22, 2023
Q, A, or Comment on THIS thread -or- Start a NEW Thread