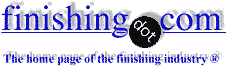
-----
Zinc Chromate Plating Surface Corrosion
Can anyone comment on the effects of humidity and exposure to harsh environments and the formation of what I believe to be zinc oxide on the surface of plated sheet metal components. I am calling for a Zinc with Chromate conversion per ASTM B633/98, Type III, Class Fe/Zn5-SC1, Trivalent Clear with mixed results. The finished assemblies are packaged with foam end caps and placed into boxes for shipment to locations around the globe. They can sit in warehouses and on shipping docks for several weeks before finding their way into a controlled environment. Problem is when they are unpackaged they have formed what I believe to be Zinc Oxide in the area that are under and in contact with the foam end caps. Some have suggested a thicker coating such as Fe/Zn8-SC2 or Fe/Zn12-SC3 will correct he situation but I believe the humidity and environmental pollutants are the major issues to be dealt with and the coating weight has little effect on preventing the formation of the oxidation. Can anyone provide some advice.
Steve Vargo- Lewisville, Texas
2006
First of two simultaneous responses --
Plating spec doesn't seem to be the problem. If the parts are packaged immediately after plating, the packaging material isn't allowing the zinc to cure properly. I understand if that happens the zinc will start its sacrificial design almost immediately. Try letting the parts in open air for 24-72hrs (if you can).
JEFF W LENTZPlating Co. - Lancaster, Pennsylvania
2006
Second of two simultaneous responses -- 2006
Hi Steve,
The 'zinc oxide' is almost certainly zinc hydroxide, Zn(OH)2, aka white rust. It occurs due to trapped moisture; lack of air exposure prevents drying and the absorption of CO2 (which leads to a more protective hydrated carbonate surface). White rust is prevented by chromating or supplemental sealers; the zinc thickness is irrelevant
(until red rust appears). Clear chromate (Type III per ASTM B633) is required to withstand 12 hours salt spray testing w/o white rust.
Verify the chromate test results and that parts and foam caps are thoroughly dry before packing. Check the foam for moisture by microwaving in a closed glass container (watch for condensate).
letter 42659 and many others have more info on white rust; search the site.
- Goleta, California

Rest in peace, Ken. Thank you for your hard work which the finishing world, and we at finishing.com, continue to benefit from.
Q, A, or Comment on THIS thread -or- Start a NEW Thread