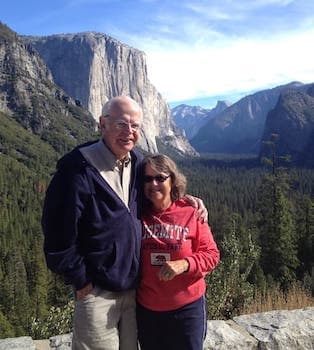
Curated with aloha by
Ted Mooney, P.E. RET
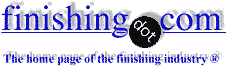
The authoritative public forum
for Metal Finishing 1989-2025
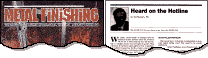
-----
White rust issue
We are facing White rust issue in Steel Sheet FeP01 (NF EN10130) Thickness 3 mm with Zinc Coating Blue Passivation. Supplier is saying that he is maintaining 11 to 15 micron coating thickness. Is there any standard chart available which says for this much thickness the part may withstand these many hours in salt spray test?
HS Pavan- Bangalore, Karnataka, India
2006
Your zinc plating thickness sounds reasonably generous, Pavan, but white rust comes from inadequate chromate conversion coating (or lack of good rinsing and drying) rather than inadequate zinc thickness. Thus there will not be a chart of zinc thickness vs. hours to white rust. Traditional blue hexavalent chromates are probably good for 24 hours, but you can specify 24 hours to white rust, or 96 hours, or whatever spec you wish, and the plater can adopt a technology to achieve it.
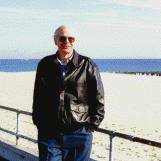
Ted Mooney, P.E.
Striving to live Aloha
finishing.com - Pine Beach, New Jersey
2006
Ted is correct!
Thickness will only help for corrosion protection to red rust. Therefore thickness can be related to red rust.
But, if you are looking for protection to white rust, you must look at the chromate (hexavalent) or the passivate (trivalent) and/or a sealer and/or nano-particles.
Start with the specification that you want or need for your products
(e.g. 96 hours to white rust or 240 hours to white rust etc...).
Give your products and specification to various plating shops and ask them to recommend a process that fullfills the requirements.
CRC Specialist - Budapest, Hungary
2006
Pavan,
Adding to Ted and Tom's comments, if you are interested on delaying the appearance of coating corrosion products (white rust) you have to be looking at the overall system itself. 1.- Base plating system: using a base plating alloy of Zn-Ni would produce fewer white rust because of the corrosion mechanism is different to that of pure Zinc.This of course comes at a price and you should only consider if you want to increase corrosion performance overall. For straight Zn plating you should have at least 5 micron thickness for the next step (conversion coating) to work properly. 2.- Conversion Coating: Indeed, the nanoparticle formulas do a very good job at providing up to 240 hrs even without a sealer. There are some other companies that offer proprietary high chromium passivates that offer excellent corrosion resistance. 3.- Sealers: Sealers can delay the white rust appearance while providing an initial barrier. There are some formulas that allow for "some healing" of the sealer by diffusing if there is mechanical damage. Processing parts in barrel will always have lower performance to white rust than parts processed by rack, because of the mechanical damage imposed by barrel.
- Dubuque, Iowa, USA
June 24, 2011
Q, A, or Comment on THIS thread -or- Start a NEW Thread