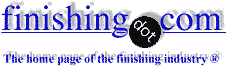
-----
Phosphoric acid & sulfuric acid electropolishing of stainless steel Q&A

Q. I am currently conducting my undergraduate thesis on effects of parameters of electropolishing stainless steel. I would just like to ask what exactly does the phosphoric acid and the sulfuric acid in the electropolishing bath do to the stainless steel?
Anna Bautistastudent - Manila, Philippines
2006
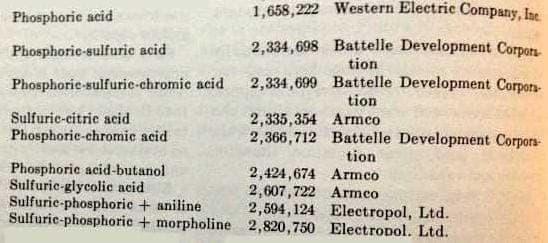
A. Hello Anna. Please try to find a library that has the Electroplating Engineering Handbook ⇦ this on eBay, AbeBooks, or Amazon [affil links] ; the process is described there, and for a thesis you'll be better off relying on published works than internet responses. But it is not the acid that does the electropolishing, it is the current, as you probably already know. The acids that work well are probably in many cases simply the result of trial-and-error testing rather than development from first principles, and many combinations of acids, and even single acids can work.
Although I'm not sure you will be able to develop (at the undergraduate level at least) a defensible theory of why the process works best at a particular concentration or temperature, one possible approach would be to go to the old patents referenced in the EEH, and read the claims as to why they assert that a particular mix is best and see if your experiments support or refute the claims..
Best of luck.
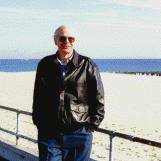
Ted Mooney, P.E.
Striving to live Aloha
finishing.com - Pine Beach, New Jersey
Mirror Electropolishing of 2205 Duplex Stainless
Q. I am building some trays in Duplex 2205.
I had some small sheets of 2205 electropolished but the quality was not very good?
What is the best solution/concentration/ratio of Phosphoric acid to sulfuric acid and temperature for electropolishing Duplex 2205?
Is there a better or different acid combination or addition that would make the electropolishing quality better. We will be using Mirror polished sheets.
Please elaborate as much as possible.
Thank you
Cy
Stainless Trays - Zhejiang province China
April 11, 2019
A. Hello Cy. Your question implies that the reason the quality was not good is that you did not make the necessary adjustments to concentration & temperature which are necessary for electropolishing Duplex 2205 as opposed to electropolishing other stainless steels.
My own electropolishing experience is very limited -- I have never done it myself. But I designed equipment for electropolishing shops who used a wide selection of different proprietary and non-proprietary electropolishing solutions, and none to my knowledge ever dumped their process solutions and reformulated them to run different alloys; I don't think they even changed the operating temperature.
So I tend to doubt that tweaking the temperature and concentration is the secret to successfully electropolishing this alloy. The question I have to ask is: Do you routinely make the same trays from various other stainless alloys and have them successfully electropolished by the same shop? When you say the quality was not very good can you characterize any particular defect or shortcoming? Heanjia Super Metals at
https://super-metals.com/industrial-resources/duplex-stainless-steels-complete-guide/
advises that electropolished 2205 will be sufficiently smooth to meet specifications, but it may not be as shiny and mirror-bright as 316L because of the greater amount of ferrite which must be dissolved. Good luck.
Regards,
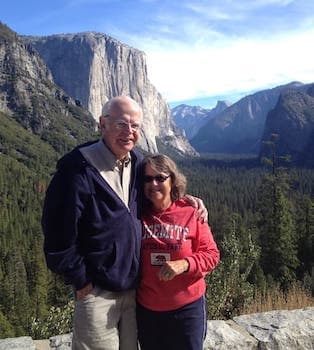
Ted Mooney, P.E. RET
Striving to live Aloha
finishing.com - Pine Beach, New Jersey
A. As Ted said: "2205 will be sufficiently smooth to meet specifications, but it may not be as shiny and mirror-bright as 316L because of the greater amount of ferrite which must be dissolved. Good luck."
The phosphoric/sulfuric acid electropolish solution as used for 300-series stainless will work as well as any, but may not be mirror bright.
You can mechanically polish to whatever appearance you want, then passivate with citric acid which will not alter the cosmetics.
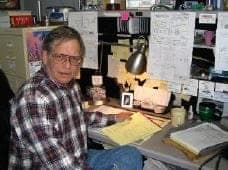
Jeffrey Holmes, CEF
Spartanburg, South Carolina
Q. Thank you for your response to my question about mirror polished 2205. That brings up a few more questions.
There are a few research papers on electropolishing, one that I found the link in your website. It suggests that a 3:1 ratio of Phosphoric acid to sulfuric acid at 70 degrees would be the most suitable for 2205.
A little background, the trays I am building are used in aquaculture for display purposes, so the idea is to make it as aesthetically pleasing as possible for as long as possible. The trays and tanks are filled with water all the times and there is a good chance of rusting over the 20 or 30 years life of the product. That is why we want to change over to 2205, and the fact that is magnetic, helps in the sense that we can attach lights and other things to the sides or bottoms of the tray. The material would be mirror polished on both sides.
Please feel free to correct my assumptions when necessary and I have a few questions at same time. I am a novice in this business. By no means am I stating facts, just what I have read and seen with my limited experience, I am eager to learn more and improve on my processes of handling of the production of these trays.
It seems to me from all the things that I have read, in mirror polishing process, to eliminate all or most of the streaks, pits and make buffing the sheets easier, until you have a perfect mirror surface. Electropolishing the surface first and then mirror polishing could make the process faster, more efficient and improve the quality of mirror polish.
2205 because of dual crystalline structure seems to not behave as well as 304 or 316, but still electropolishing seem to remove quite a bit of rough surfaces to smooth it out after electropolishing.
So setting up an electropolishing line before Mechanical mirror polishing process should create a better product.
The trays I am building are laser cut, but I notice where the cuts happened, I have a bit of rust happening with 304,
especially in inside of the welded corners. The outside where it was welded, looks nice and clean, but inside wedge has some rust. I am guessing my problem should be less visible with 2205, but is there a certain way I should treat the cut edges to decrease the chances of rusting spots showing off.
Is it possible to setup a continuous electropolishing line to do a whole roll of stainless sheets before mirror polishing. Without having to cut it to pieces. I don't want to do the whole roll at one time. Just do one segment then move the roll along. until the whole roll is done?!
- Since during the process of electropolishing there are wide variety of metals dissolved into the Acid mixture, how to clean or filter the metals out? Is there a process of recycling or filtration system to remove those additional metals? Or does the whole solution gets discarded or sent to recycling center after a certain amount of time.
- At what point do you replace the acid mixture in the electropolishing bath. How do you know it is time to change the mixture? Is there a test or breaking point beside, things don't seem to be looking good so you change the solution?
- What would passivating with citric acid accomplish. I am not sure I understand the passivation process, except that it is used to clean the oils and grimes from the surface before electropolishing, to make it more effective. Does it accomplish another purpose.
- I need to electropolish My trays after the welding process, either TIG welding or laser welding eventually and to clean up and get rid of the weld burn marks. The welded area on 304 electropolishes very nicely, and I am wondering if the is 2205 going to be better, or do I need to worry about anything around the weld lines on the 2205 trays as we transition.
Thank you so much for your help and insight in the matter.
Cy
Agriculture - Zhejiang China
A. I don't know the answers to all your questions, but will make a few comments.
I would think SS 316 will do everything you want. It will electropolish well in the 3:1 phosphoric/sulfuric solution. And will retain it's luster, rust free unless your water is corrosive - low pH, high chloride, etc.
As to fabrication questions, it's difficult to envision just what those surfaces will look like. I can only suggest that you make cut edges smooth before electropolishing.
Unless you are going to make many, many of these items, you will probably be better off to spend your efforts on smooth, clean fabricating, and have an existing and experienced shop do the electropolishing.
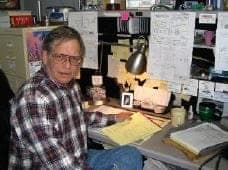
Jeffrey Holmes, CEF
Spartanburg, South Carolina
Yes we are hoping to make lots of these in the near future.
Yes 316 is pretty good. But I was looking for a magnetically permeable surface. 2205 provides that ideal magnetic permeability, with the added bonus of additional hardness. Except it does not seem to electropolish as well.
Agriculture - Zhejiang china
A. Cy,
Passivation for stainless steel is defined as removing free iron from the surface to enable a better chromium oxide layer to form, thereby increasing the corrosion resistance.
Cleaning the oil and grime is just "degreasing".
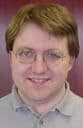
Ray Kremer
Stellar Solutions, Inc.

McHenry, Illinois
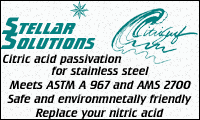
RFQ: I have SS 202 Electrochemical polishing plant, we are using Phosphoric 70% and sulfuric acid 30%. But after some days my solution gets thick please suggest how to thin our solution and any chemical name available in the market to remove iron and other contaminants to settle in electropolishing solution bath
Shop - Mumbai, India
April 3, 2023
privately respond to this RFQ
Ed. note: As always, gentle readers: technical replies in public and commercial replies in private please (huh? why?)
Q. Please reply fast.
Niraj Mali [returning]Shop - Mumbai, India
April 7, 2023
Ed. note: Hi, Niraj. Apologies, but this is not a consulting service; it's a public forum. Knowledgable responders respond when and if they feel like it, sorry. One good way to encourage other readers to treat you as a V.I.P., however, is to respond to questions from others :-)
A. With these types of "homebrew" phosphoric acid baths, the usual procedure to control iron content is to periodically dump (dispose) part of the spent bath and refill to operating level with fresh acid mixture.
If you are using any additives to the bath, such as defoamers or throwing power enhancers, those will also need to be replenished in proportion to the amount of bath replaced.
There also exist proprietary electrolyte formulations which are "partially sludging" or even "fully sludging", meaning that most or all of the dissolved iron (and other metals) eventually drops to the bottom of the bath in the form of insoluble sludge, from where it can be removed by mechanical means.
I am not aware of any generic/"homebrew" formulations which accomplish such sludging effect, but with the greatly extended life of these baths it's quite likely more economical to buy one of the commercial products instead. Good luck.
- Czestochowa, Poland
September 17, 2023
Q, A, or Comment on THIS thread -or- Start a NEW Thread