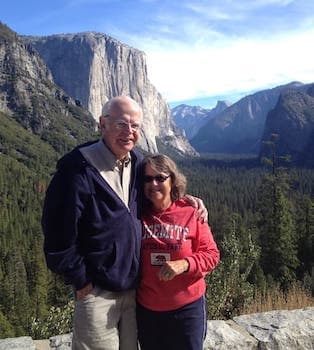
Curated with aloha by
Ted Mooney, P.E. RET
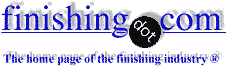
The authoritative public forum
for Metal Finishing 1989-2025
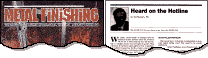
-----
Galvanizing flux bath has iron contamination

for Engineers, Shops, Specifiers
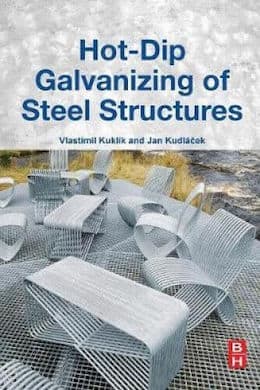
avail from eBay, AbeBooks, or Amazon
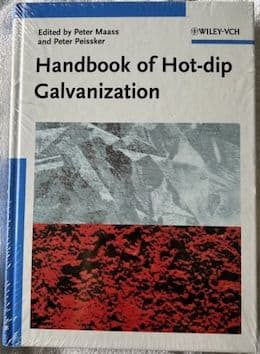
avail from eBay, AbeBooks, or Amazon
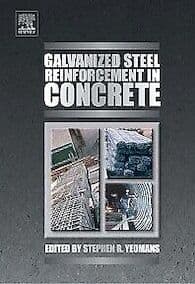
avail from eBay, AbeBooks, or Amazon
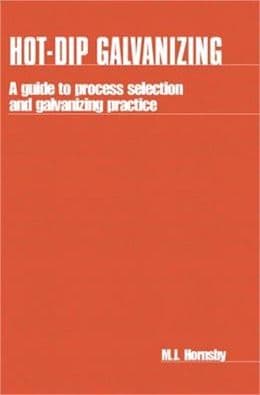
avail from eBay, AbeBooks, or Amazon
avail from Amazon
"User's Guide to Hot Dip Galvanizing for Corrosion Protection in Atmospheric Service" by NACE (1997 only rarely avail.)
avail from AbeBooks, or Amazon
(as an Amazon Associate & eBay Partner, we earn from qualifying purchases)
Q. Dear sir , I am facing problem with iron content in water flux -- 40 to 50 gm per litre. But we are doing treatment of water flux every week with ferokike, but not getting better result. So please suggest what should I do now?
First we add ferokike in water flux and put an air pressure for 1 hr inside the flux and leave it for 16 to 20 hrs to settle the iron on the bottom, but iron comes at 35 gms.
- ajman uae
January 7, 2023
A. Hi Adam
Google comes up empty for "ferokike". So I assume it's a typo, but I don't know what the correct reference would be. Some sort of proprietary hydrogen peroxide? Maybe Ferrokill? I also can't successfully google what 'water flux' is, maybe water-soluble flux? More words please.
Luck & Regards,
Ted Mooney, P.E. RET
Striving to live Aloha
finishing.com - Pine Beach, New Jersey
A. You might be referring to a product called Ferrokill?
Fe in your flux is a problem for several reasons:
1. It slows down or even prevents the steel drying easily after dipping in the flux.
2. The Fe in solution gets deposited on the surface of the steel and then comes off as free Fe in the zinc, which will form dross, so losing Zinc, and potentially causing heat distribution restrictions that can lead to kettle failure.
To remove the Fe it's necessary to make it insoluble first, allow it to precipitate (usually as iron hydroxide) and then separate it from the liquid flux. The ways to separate it include filtering, and settling. Settling can only be done in a tank without activity, so for many galvanizers having the flux tank out of action is production down time, and undesirable.
By far the best results are obtained by a flux cleaning machine - many manufacturers make them - which remove some flux, perhaps 1000 litres at a time, adjust the pH (using ammonia), oxidize the Fe (with hydrogen peroxide) adjust the pH again (more ammonia) and then filter out the iron hydroxide, and return the cleaned flux to the operations tank and start again. It's possible to get to less than 0.5 grams per litre Fe. In the case of such a machine in use, a reasonable target is to never have Fe > 1%.
Your 35 g/l is a poor result and will be costing a lot of zinc in the form of both splash (ash created, by poor drying) and by dross production. The high cost of this makes investing in the right equipment to do the job well.
To save money some chemicals suppliers sell a brew that claims to do the job in the process tank, but in my experience it rarely works well, and sometimes not at all. Air bubbling through flux to oxidize the Fe doesn't work well, but does some of the job.
So, you're getting a result, but not a good result as only half the job is being done by doing it with a low investment, poor performing technique.
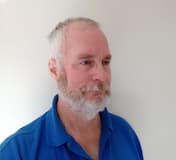
Geoff Crowley, galvanizing consultant
Crithwood Ltd.

Bathgate, Scotland, UK
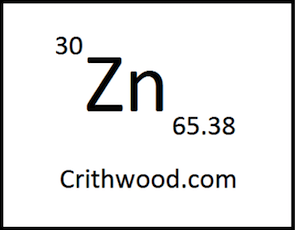
⇩ Related postings, oldest first ⇩
Q. Dear sir,
I am from galvanizing industry and presently facing problem with my flux bath (zinc ammonium chloride), It has developed iron contamination. Can you suggest a method to remove iron from the bath? Is it possible to treat with Hydrogen peroxide or KMnO4?
Please guide me.
Galvanizing job work - Dammam, Saudi Arabia
2006
A. Sir: KMnO4 cannot be used. The residual Mn(+2) would contaminate the flux. The proper materials (both liquids) are: Hydrogen Peroxide and aqua ammonia
⇦ this on
eBay
or
Amazon [affil links] (ammonium hydroxide). Needed information includes:
(1) volume of flux solution,
(2) % iron (Fe+2) in flux or grams/liter of Fe+2,
(3) density of flux at room temperature (either baumé or g/mL).
Do you have a filter press? Do you know how to use diatomacious earth with the filter press? Do you know about flocculating agents and have a source? Can you test the Fe+2 during purification so you will know when to stop adding the aqua ammonia and hydrogen peroxide? Do you pickle with HCl or H2SO4? How many rinses between acids and flux do you have? What flux do you use? (e.g., double salt, triple salt, quadraflux, etc.?) There are much better ways to deal with bad flux than to purify out the iron +2.
Regards,
Galvanizing Consultant - Hot Springs, South Dakota, USA
Multiple threads merged: please forgive chronology errors and repetition 🙂
Removing iron and sulphate from quad pre-flux
Q. A company will be starting-up a hot-dip galvanizing plant later this year (kettle and other tanks each 9 x 2 x 2.5 meters - tanks are 40,000 litres).
Pickling will be done with hot 12% sulfuric acid, with a spray rinse over the pickle tank followed by a separate rinse tank.
Nevertheless the preflux will pick up iron and sulphate from the pickle through the rinse. The flux will be quad, with the pH dropped to 4.3-4.5 by hydrochloric acid. To maintain quality of the end product, we need to limit the preflux contamination to about 0.5% iron and about 0.8% sulphate.
I am familiar with the iron removal procedure using ammonia to raise the pH then hydrogen peroxide to oxidise the iron to ferric, so it precipitates as ferric hydroxide. This takes two or three days to allow for coagulation and filtering.
Also, I am familiar with the sulphate removal procedure using barium chloride dihydrate to precipitate most of the sulphate as barium sulphate. This also takes a couple of days.
At last we get to the question!
Because of the use of sulfuric acid pickle, the iron and sulphate contaminants will tend to reach their limits at the same time. Can we therefore do one of those precipitations and then IMMEDIATELY do the other, so that there would be only one subsequent filtering, which would remove a mixture of the two precipitates?
I can see no problem from a strictly chemical aspect, but is there a problem with actually doing it?
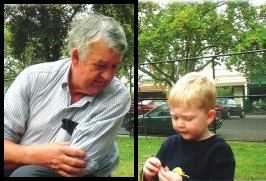
Bill Reynolds [deceased]
consultant metallurgist - Ballarat, Victoria, Australia
We sadly relate the news that Bill passed away on Jan. 29, 2010.
2007
A. Sir:
No problem, do the iron first because the barium sulphate makes it easier to filter press.
If you have TWO rinse tanks and use counter-current rinse (using contaminated rinse water for evaporation make-up in the hot sulfuric acid tanks) you would NEVER have to purify flux. I have clients running 20+ years without needing flux purification. In fact, I just tested one today and it has the following: ACN=1.60 (exact quadraflux); pH=4.2; baumé=12.9; sulphate =0.7%; Iron (Fe+2)=0.2%.
I discovered quadraflux and named it. Oh what a joy. Thank you for knowing it works the best and thank you for knowing the realistic limits on sulphate and iron.
Regards,
Galvanizing Consultant - Hot Springs, South Dakota, USA
A. Sir:
Using the right flocculating agent and a filter press pretreated using a suspension of diatomaceous earth, galvanizing flux solution can be fully purified in 24 to 48 hours depending on conditions (mainly being able to pump hot flux).
I have some questions on the new galvanizing plant:
1) Do you have a hot caustic tank and caustic rinse?
2) How many sulfuric acid tanks are there?
3) How will the spray rinse be done? By hand? Attached to the racks? Attached to the crane? Attached to the roof?
4) What water will be used for the spray rinse? Tap? or from the acid rinse tank?
5) Do you have an off-line 40,000 liter lined holding tank?
6) Is this a captive or job-shop plant?
7) What types of products?
8) When is melt down?
9) Will you use and acid recovery unit?
10) Is the kettle high-velocity end-fired or flat-flame side-fired?
11) Will you use a zero, one, or two tank quenching system?
New plants are so much fun, I just had to ask some questions? I am getting over my operation. Thank goodness.
Regards,
Galvanizing Consultant - Hot Springs, South Dakota, USA
Q. Hi Dr Cook,
Some of your previous posts on this site have been most helpful to us in deciding some of the operating details, so the least I can do is answer your questions!
We've tried to pick the best aspects out of many different reported operations and combine them into this one plant.
In answer to your questions...
1) No. Work generally will be coming from shotblast, or as-hot-rolled (scaled) with minimal handling in fabrication, so we believe a degreaser tank will not be necessary. If outside jobbing work comes in that needs it, it can be added with a bit of extra length on the building.
2) One
3) By hand. The crane will be fitted with vibrators primarily to clear the ash on the kettle by means of wave action generated by vibrations in the work, and the same vibrators are expected to help with draining the pickle acid from the work (we are not relying on this - we just think it will be an incidental help)
4) Water from the acid rinse tank
5) No. That raises interesting questions about cleaning the flux. But the principal business of the company is steel fabrication, so a 40,000 litre steel tank with a not-too-expensive lining of moderate durability for occasional short-term use won't be a problem to knock together if it turns out it's needed. We wouldn't expect to use a holding tank for cleaning the pickle acid because we'd put a plate heat exchanger between the tank and the refrigerator to get pre-cooling on the way to the refrigerator and pre-heating on the way back to the tank, but maybe experience will show that use of a holding tank is better.
6) Initially captive, but with good quality work coming out of it, we expect plenty of outside work. The plant is economically justified without outside work.
7) Mainly long, heavy beams, columns, roof girders and trusses for industrial buildings that are put up by the company.
8) Don't have an exact date yet. Late October probably.
9) Yes, we'll refrigerate the ferrous sulphate out of the acid. We have no idea at all at this stage how often that will be needed. The acid will be inhibited, so the iron buildup will be essentially from scale removal.
10) End pulse-fired, dual burners. The combustion engineering has been done by a Melbourne company very experienced in firing galvanizing kettles. The kettle will run with a lead bottom, with dross-detecting thermocouples about 5 or 6 inches up from the bottom.
11) One. The in-house work doesn't really need quenching, let alone chromate, because of its nature and the fact that it goes into building structure very soon after galvanizing. But we can easily add something like 20-50 parts per million sodium dichromate if the type of work requires it.
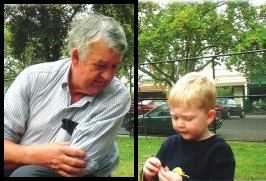
Bill Reynolds [deceased]
consultant metallurgist - Ballarat, Victoria, Australia
We sadly relate the news that Bill passed away on Jan. 29, 2010.
A. Couple of comments on the above...
Degreasing: remember cutting lubricants, punching oil, mig welder antispatter, and marker crayon/paint. All these interfere with pickling, and degreaser will help with them all. Its not only general fabricators work that needs degreasing. And what you don't put in on day one might never get done. Its often the way.
Vibrators: Watch for crane shaking. If the vibs are not designed for the job, they can shake the crane to bits. In the zinc, they can cause surface ripples that make the ash worse.
Quenching: Its not all about passivation. Your work mix (structural steel) will take along time to air cool. Where will you build this stack of cooling steel? Quenching allows your guys to fettle and de-jig straight away as all the steel is now at about 90C or lower temp. In addition, you now have a tank of hot "water", from which you can extract a lot of low grade heat. That energy recycling is not only a green thing to do, it saves money if you use it for something useful.
If you use plain water, you'll have dull finish with likely white rust. Evene if this is inhouse, you have to sell the building, and who wants to buy one with dull, white rusty structural steel?
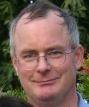
Geoff Crowley
Crithwood Ltd.
Westfield, Scotland, UK
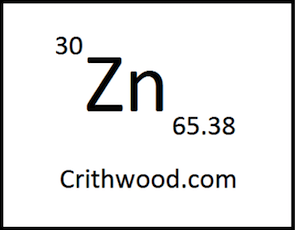
Sir:
1)30 years ago I did lab experiments in which I pickled 1/4 inch thick, hot rolled (without any oil or grease) steel in hot sulfuric acid. It took 30 minutes using only acid, but took only 10 minutes by using 2 minutes of hot caustic first. At the time I telephoned the local galvanizer and told him of my great "discovery." He said oh yes we had a hole in our caustic tank and could not pickle to save our butts. They worked night and day to fix their caustic tank to get production back up. Without caustic the "spent" acid is three times greater. Also the first tank that the steel is put into gets 6 to 12 inches of dirt in it each year. Thus your single acid tank will be contaminated with dirt and lead from zinc stripping. Also iron sulphate crystals will be contaminated with dirt and lead.
2)To keep up with the kettle it takes a MINIMUM of three sulfuric acid tanks (usually one strip tank and two pickle tanks).
3)I have never seen a hand rinse system. I think it will slow production and be messy. Vibrators are very rare and if the lifts are heavy they tend to shake and damage the crane.
4)Yes. Tap water is too high of pH. A single acid tank will not evaporate enough water to enable proper rinsing.
5)Actually I had in mind a vertical cylindrical tank to hold contaminated rinse water to feed back to the acid tank but you will not have enough evaporation anyway.
6)For your size kettle, economically you need 20,000,000 pounds/year of steel.
9)If you cool acid in a tank you will form large, very hard crystals contaminated with mother liquor (acid) and in your case dirt, mill scale, and very fine lead powder. Modern, excellent crystallizers with centrifuges are in the market place that produce granular, dry, and commercial iron sulphate crystals. 30 years ago I tested many, many acid inhibitors. Only 2 or 3 were any good. Recently I went to a plant start-up and they had already put 100 gallons of inhibitor and 50 gallons of very expensive extender into each of three 20,000 gallon sulfuric acid tanks. The acid fumes were horrific. Workers were coughing up blood. I drove a few miles down the road and borrowed 5 gallons of the best inhibitor that I had tested 30 years ago. I put one gallon in each tank. Acid fumes were reduced by more than 99.9%. The workers, the plant manager and the plant owner were extremely happy.
10)Is this a total of two or a total of four burners? How thick of insulation under the kettle and in the furnace shell? Viewed from above do the hot gases from the burners go around and around the kettle? Is there protective insulation or stainless stand-off on the kettle corners? A simple probe determines easily dross and a long hand-held type K thermocouple is used to map the kettle to avoid hot spots and give longer kettle life.
11)To avoid workers burning themselves it is usually best to quench everything or nothing. Your longer structures may distort if quenched while too hot. Hex chrome is usually used at higher concentrations. What pH would you use in hex chrome solutions and how would you test and control the pH?
I have some more questions:
A)What coil material will you use in the acid and flux tanks?
B)Will you use extraction and a bag house for your kettle smoke? Is the plant in a residential area?
C)How far down is the water table?
D)What baumé and temperature will you use in your flux?
E)How will you test for ACN (ammonium chloride (numerator) over your zinc chloride (denominator))? And how will you adjust the ACN?
F)How will you test and control the pH of your flux solution?
G)Your depth/width ratio of your kettle is only 1.25 (2.5/2=1.25). This depth to width ratio should be at least 1.5 and much better if it were 2. A larger depth/width ratio holds the temperature more constant and reduces, substantially zinc usage. Also a larger depth/width ratio gives much longer kettle life. A larger depth/width ratio also provides higher production.
H)With only one acid tank, evaporation is insufficient and one rinse tank, counter current rinse will be inadequate. By producing iron sulphate crystal, the acid tank will be about 29% sulphate. Thus flux contamination will be very high and many purifications/year will be required (the first contamination will take a longer time and then they will rapidly occur). IQM tolerates 3.5% sulphate in combination with 1.5% iron (+2), but ash production is excessive. What is your plan to deal with so many required purifications? A second rinse tank would greatly reduce this problem.
Bill, Thank you for responding to my first questions. In time you will find that most of what I have posted is true.
Regards,
Galvanizing Consultant - Hot Springs, South Dakota, USA
Q. Please give down question answer 1 How many free HCl contain in preflux solution max or minimum required
Datta shindegalvanizing shop - Poona India maharastra
January 1, 2010
Q. What is role of FLUX for white rust, what is the combination of standard flux solution, is it flux quality is responsible for white rust, please reply
VINAY AKULWARpower transmission structurals - Mumbai, India
July 20, 2010
Multiple threads merged: please forgive chronology errors and repetition 🙂
Q. Dear sir
Regarding flux we use Hydrochloric acid 20% in the pickle acid, followed by two water rinses changed every week. Please note we do not have water overflow system.
The flux develops iron in the course of time and we use the method of H2O2 +Liquid ammonia for the iron removal treatment.
My question is what is the size of the iron particle in this flux solution?
During lab trials I found that We could actually filter these iron particles after H2O2 treatment by using "Whatman Filter Paper No. 42 but it takes time.
If we know exact size of particle in microns we can use relevant filter paper to filter out the iron particles formed and carried out in the filtrate after the settling process using the filter pump.
Sir please suggest me if this is OK. If so, please tell me about the size of iron particles so that we can arrange for the appropriate filter paper for the same.
Hot Dip Galvanizing Cable Trays - Jeddah, Saudi Arabia
February 10, 2014
A. Hi Dharampal. I am only the site curator, not an expert in the filtration of galvanizing flux for removal of iron particles ... but Whatman (GE Healthcare) No. 42 filter paper is their finest, and has a pore size of 2.5 µm. Can you either look at the used paper under a microscope or, better yet, analyze the filtrate from a couple of courser grades like No. 40 & 41 to get a feeling for what is going on and what the most practical pore size would be for filtration in production? Good luck.
Regards,
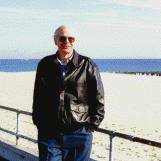
Ted Mooney, P.E.
Striving to live Aloha
finishing.com - Pine Beach, New Jersey
Iron content in triple salt flux
Q. I read an article (the paragraph below) that iron doesn't matter in triple flux, however, I have read common posts stating that reducing iron content can reduce coating thickness and dross formation. In need of clarification.
Would also like to ask if I were to treat my flux solution with ammonia for iron removal while the pH exceeds 6, after removing the sludge then only adding HCL to reduce the pH again back to 4.2. I have read somewhere else where it states if pH exceeds 5, the zinc chloride will be decomposed. This is my concern.
Kean Wong
- Selangor, Malaysia
January 31, 2018
A. I don't agree with that quoted paragraph.
Fe in the flux, in solution, will move to the kettle. It reacts with zinc to form dross.
The difference between triple salt, double salt (and quadraflux for that matter) is only the ratio of the two components, zinc chloride and ammonium chloride. Usually stated as a molecular ratio. In practice, the ratio is rarely an integer value, and if you think you are running double salt, the ratio might wander from 1.5 to 2.5, and if you are testing the flux, the result might indicate additions of only one of the components to adjust the ratio. But the main supply of the flux will be the target ratio (double, triple, etc.)
To think that the chemical reactions suddenly alter at triple salt compared with double is a bit misleading.
Iron oxychloride is stated as being "FeO·HCl". I think that's a typing error, and that it's FeOCl. I have never seen purple ash on a galvanizing bath (as FeOCl is). The formation of this is often Fe2O3 + FeCl3 => 3 FeOCl. There's certainly some FeCl3 around, from pickling and carried over. But Fe2O3? Where did that come from? By the time the steel has been pickled, all the Fe2O3 should be gone, and is now FeCl3.
I don't think you can remove Fe from flux with only ammonia. That would raise the pH, and perhaps precipitate some dissolved things, but don't you need to oxidise the Fe also? Most removal of Fe from flux results in iron hydroxide as a solid which can be removed by settling or filtering.
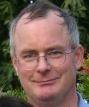
Geoff Crowley
Crithwood Ltd.
Westfield, Scotland, UK
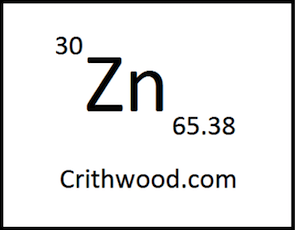
February 6, 2019
A. Kean/Geoff:
45 Years ago I removed the iron (+2) from many galvanizing fluxes. Not a single galvanizer said his dross production was reduced. All of these galvanizers said their % GZU was lowered.
25 years ago I went to Troyes (pronounced Twa) in France. I installed a motorized ash machine directly on the kettle to recover zinc from the ash. It reduced the ash by 75%. The company was happy except they noticed the dross was increased by 10%. They asked me to come back and explain why the dross increased. The newly formed dross was directly under the motorized ash machine. I went back to France and went through the economics showing that reducing ash by 75% was far more economical even with a 10% increase in dross.
I have a USA wet kettle client (does not have space for an acid rinse tank) who had 9.5% iron (+2) in his flux. When he dumped his flux tank and got new flux, his dross did not change from 1.1% of production. He did notice that he consumes 20% less new top flux and his dry skims are reduced by 33%.
Recently the dynamic angle tests were applied to two fluxes. The first a very clean quadraflux the second to a flux having 1.5% iron and 4,500 ppm (e.g. 0.45%) NaCl (sodium chloride). The tests were video taped and the quadraflux gave excellent results, whereas the 1.5% iron and 0.45% NaCl flux gave very excessive white smoke and very excessive ash. Also the iron contaminated flux showed many small bare spots in the 20 second dynamic flux test.
The idea as expressed in the quoted paragraph presented by Kean, that FeCl2 in the flux is GOOD is WRONG. I am interested to know where that paragraph came from.
Because most all drosses are about 0.4% to 0.6% of production for dry kettles, I do not think iron +2 in the flux is all that important in terms of dross production. I do however know that iron +2 and other impurities in the flux is VERY important in terms of skims/ash production. For lower smoke a good flux is also very important. A good flux gives skims (unworked) that can give 85% zinc recovery in an MZR machine. A properly operated quadraflux can provide 0.10% ash/production after passing through an MZR machine.
I do not think that Fe+2 or Fe+3 chlorides react with molten zinc to form dross. If however, in an ash box or MZR machine the atmosphere is reducing (chemical term) enough then perhaps these iron IONS can convert to metallic iron then it certainly could produce dross.
I cannot imagine where FeOCl is coming from and where oxy acids are coming from?
Regards,
Galvanizing Consultant - Hot Springs, South Dakota, USA
February 7, 2019
Q. Dear sir, what will be impact of Fe available in the flux solution on ash and dross generation. What is the calculation to know the exact impact of Fe, suppose if we are maintaining the Fe 0.05 and 0.1 then what will be the difference on ash dross generation.
Harjinder singh- Indore- Madhyapradesh India
November 21, 2021
Q. Good Day,
My name is Mutshidzi Mulelu, I am a Laboratory Manager. I am currently experiencing problems with my flux tanks.
I am getting Low Zinc and Ammonium Chloride content and low pH (less than 1) and High Fe Content of 4%.
Can low pH or a high Fe content have an effect on Zinc Chloride and Ammonium Content in the Tank?
- Gauteng, So. Africa
August 24, 2022
A. Low pH and high iron indicates contamination of the flux tank by pickle acid. That dilution will reduce the apparent concentrations of ammonium chloride and zinc chloride.
If the flux has changed from brown to green, that helps confirm that its acid contamination.
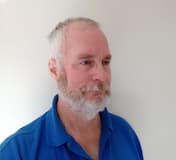
Geoff Crowley, galvanizing consultant
Crithwood Ltd.

Bathgate, Scotland, UK
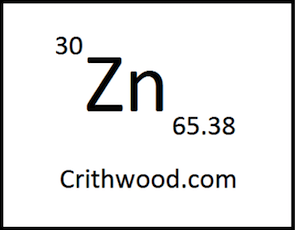
Readers: please see also --
• Topic 41209 "Reduce Iron (Fe) in Galvanizing flux"
Q, A, or Comment on THIS thread -or- Start a NEW Thread