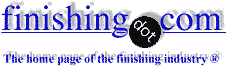
-----
Reduce Iron (Fe) in Galvanizing flux

Q. I have some concerns about the Fe2+ oxidation with hydrogen peroxide. One of them is related with the influence of Fe2+ determination by titration using permanganate, since hydrogen peroxide will compete with Fe2+ ions on the reduction of MnO4- to Mn2+. Anther concern is about the toxicity of hydrogen peroxide when inhaled by workers, considering that the flux solution is always heated and the mist of these solutions is always present in the workplace.
Could you give us some ideas about alternatives to peroxide?
R Gimenes
- Itajuba Minas Gerais, Brazil
April 26, 2023
A. Some people bubble air through flux. It's very slow, but works.
Peroxide is difficult to "inhale", being a liquid. Did you mean to take it into the body by any means? (like drink, etc.)
It is successfully used by many plants in liquid form for this purpose. The safest way is buy a machine that cleans up the flux and removes Fe. It uses peroxide but under very controlled conditions, and by means of an automated dosing pump.
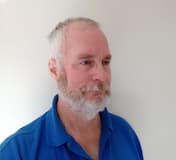
Geoff Crowley, galvanizing consultant
Crithwood Ltd.

Bathgate, Scotland, UK
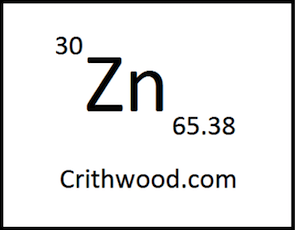
May 4, 2023
⇩ Related postings, oldest first ⇩
Q. Can anyone advise what pH I'd need to attain in my rinse tank prior to Flux tank in a galvanizing plant lineup? Pretreatment is by hydrochloric acid, then static water rinse, then double salt zinc chloride/ammonium chloride flux prior to zinc at 450 °C.
Fe carryover to the Zn tank means increased dross production (waste), so eliminating the Fe carryover will save money. Rinse tank runs at pH 1-2 but at some point, perhaps pH7? Fe carried over as FeCl2 might precipitate as Fe(OH)2 as a sludge, preventing its further carryover to Zn.
Any ideas?
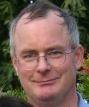
Geoff Crowley
Crithwood Ltd.
Westfield, Scotland, UK
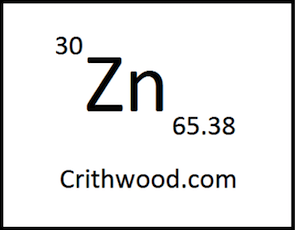
2006
A. Sir: In 1972 I spent several hundred hours in lab determining the best methods to remove iron (Fe+2) from flux. Over the last 34 years I have purified many, many flux baths.
Briefly, Fe+2 is titrated using standard dichromate solution, simple formulas are used to determine the volumes of aqua ammonia
⇦ on
eBay or
Amazon [affil links] (also called 26 deg Be' ammonium hydroxide) and 35% H2O2 to add, with airline mixing. For best yield (and least sludge), higher temperatures (above 160 °F (71 °C) are used and a filter press (precoated with diatomaceous earth) can reduce sludge ten-fold. Only a pH between 5 and 5.5 can be used (pH meters and pH papers do not work). A 48 hour minimum is required for settling without a filter press. If oil is present extra peroxide is required. After purification the pH is readjusted to 4.2 (not using a pH meter or pH paper).
The hydrogen peroxide oxidizes Fe+2 to Fe+3 and the ammonium hydroxide provides OH-1 groups to form insoluble Fe(OH)3. Without the ammonium hydroxide, the hydrogen peroxide decomposes to oxygen and water (as shown by bubbling and foam going over the tank.
I tried many methods to deal with Fe+2 in rinse and none worked. Raising the pH of the rinse causes the newly pickled steel to corrode. Also I tried continuous flux purification but the chemical problem that I had was the best "working" pH is 4.2 while the purification pH is 5 to 5.5 (can't have two pH's at the same time).
I prefer quadraflux to double salt.
My experience is that iron in the flux for dry-kettle galvanizing does NOT cause extra dross at the kettle but does give thicker zinc on the product. Also iron in the flux causes extra dry ash. In a wet-kettle, iron in the flux DOES cause extra dross. There are several ways to deal with bad flux and still get an excellent and economical galvanized product.
For more information see my 25+ past publications in the journal METAL FINISHING.
Regards,
Galvanizing Consultant - Hot Springs, South Dakota, USA
Q. Thomas,
thanks for interesting comments.
We have tried with moderate success using magnesia granules where we pump the rinse water through a bed of these granules, and they neutralise the acid in the water, and so the Fe precipitates out as hydroxide sludge in the granules. But it's a messy arrangement and requires some engineering to make into a suitable commercial scale operation.
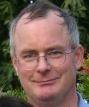
Geoff Crowley
Crithwood Ltd.
Westfield, Scotland, UK
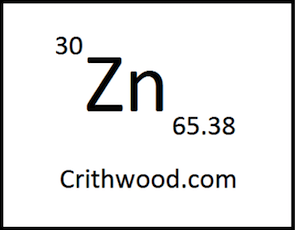
A. Geoff,
Magnesia (magnesium oxide) is soluble in acid. Thus magnesium chloride will be carried into the flux solution on the product. Unfortunately magnesium chloride is hygroscopic (collects moisture from the atmosphere). Thus great zinc spatter results as the product enters the molten zinc. Also magnesium chloride is non-volatile (m.p.708 °C (1306 °F) and b.p.1412 °C (2574 °F) which causes many, many "black" (bare) spots on the product. Also a neutral pH corrodes the freshly pickled steel during draining of the product out of the rinse. Continued use of magnesia predictably permanently destroys the flux solution.
Regards,
Galvanizing Consultant - Hot Springs, South Dakota, USA
Q. Thomas,
thanks for continuing dialogue.
While magnesia is hygroscopic, that's hardly a problem in that it is immersed in water! Yes it reacts with the acid and raises the pH. As you say a neutral rinse might tend to corrode the steel, but that is relative to the corrosion of a low pH rinse, which is worse. Without the magnesia the pH is very low causing continued pickling in the rinse tank. Neutral rinse reduces this. If the rinse might be alkaline then it might stop, but the system cannot drive it to alkalinity, it struggles to remove acid.
Magnesium chloride build up in the rinse is diluted by the fact that the rinse water is used for making up new acid. The fresh HCl is bought at high strength, and diluted for use, using the rinse tank water. This is then made up with fresh water. In this way, the concentration of Magnesium chloride never gets very high, though we have not measured it.
Zinc spatter is not an issue. In this plant, there is only air drying (no heated drying of the work) before immersion in zinc. There is already considerable spatter. Any increase as a result of the minuscule moisture attracted to any magnesium chloride is undetectable.
In over a decade of operation, in this one plant, no quality problem in the galvanizing has been detected. There are no black (bare) patches.
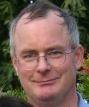
Geoff Crowley
Crithwood Ltd.
Westfield, Scotland, UK
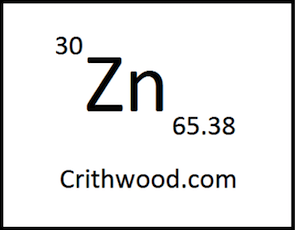
A. Geoff,
A neutral rinse does corrode freshly pickled steel. A low pH rinse keeps the steel pickled (corroded steel IS worse than the slight acid attack of the steel in the rinse). Just above about 2% magnesium chloride (dry weight/weight basis) in the flux greatly increases the inability of the flux to dry and greatly increases "black" (bare spots). I recommend that you measure the magnesium chloride in your flux. Using hot quadraflux there is near zero molten zinc spatter for 99%+ of the product. In some plants the kettle-men use T-shirts and no shield. I suggest that "black" (bare) spots are avoided in your plant by leaving the product in the molten zinc longer (workers do this so as to avoid bare spots which would be their fault). By leaving the product in the molten zinc longer, much thicker zinc coatings result and the operation becomes non-economical (due to high zinc costs).
In our dialogue we both think we are right. I suggest that the real test is how near the zinc coating thicknesses are to the desired zinc thicknesses and how low the by-products can be (dry ash and dross). Also low zinc clean-up and low rework are obviously important. There are many North American plants with gross zinc usages in the 5% to 6% range (no credits for ash and dross), even though the weighted average thickness of the steel is normally less than in Europe (more surface area in North America).
If you would care to give your average zinc thickness on the steel, your %GZU, your dry ash and dross numbers, the baumé and temperature of your flux, say for 2006 YTD, then a greater understanding of your operation could be determined.
Regards,
Galvanizing Consultant - Hot Springs, South Dakota, USA
Q. Thomas,
thanks for your continuing interest in this topic.
I cannot share some of the info you requested in a public forum.
But for general info:
It's not a matter of "thinking that I'm right". I'm genuinely seeking some help with lowering Fe in flux/rinse.
We have achieved some reasonable results.
Our zinc coating thickness is slightly over the standard (ISO 1461). If there was a way to achieve no spread of thickness (zero standard deviation from mean) then I'd be happy!
Our ash and dross make is similar to what you've quoted.
We have one plant with a mix of structural material (lower area per weight ratio) and another with no structural (high area to weight ratio). The ash/dross make is similar.
Immersion time to avoid black spots is not a good technique in my opinion. Anything less than 5 dips per hour is unacceptable for us.
Environmental regulations here enforce the use of a canopy over the kettle to collect fume. This doubles as a splash shield, though that is not its prime purpose. The weather in Scotland is not suitable for Tee shirts! But your point understood.
To achieve 2% Magnesium chloride in the flux would need a quite high percentage in the rinse. (only source of Mg2Cl in flux is from carry over from the rinse). We have not measured either concentration directly.
I'm not advocating the use of magnesia for removal of acid and Fe in rinse. It is difficult to arrange, and the control not easy either. What I said is that I've used it to some success, but seeking an alternative.
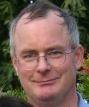
Geoff Crowley
Crithwood Ltd.
Westfield, Scotland, UK
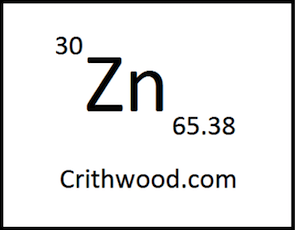
A. Geoff:
Certainly there are ways to achieve a narrow spread of thickness.
For ash it seems I now have evidence that it can be again lowered. Recently I went to a center-pivot irrigation company doing steel averaging 0.126 inches thick. The yearly zinc reduction was 1 million pounds. Along with this came a surprise of reducing ash by 1/2 (even from what I expected). Their GZU is now about 6%. You will likely find this hard to believe but the lower ash seems to be from a lower zinc temperature of 828 °F. They do not even need to skim before going in. This is certainly new to me. The kettle is 12 feet deep so it can keep up thermally with the work load at 828 °F.
30 years ago I used aqua ammonia in lab experiments to raise rinse pH and thus take out Fe+2. What I got for my trouble was a lot of rusted steel (out of the rinse).
I saw today your answer to Atul Mishra from India. My first thought was a leaking kettle which I responded to Ted. I expect he will not include my response because you have already covered it.
My final comments about the center pivot galvanizer-- Initially they had 4.2 mils (107 microns average on their product). By three items:
(1)Lowering the zinc temperature to 828 °F; (2)converting to quadraflux at 160 °F (71 °C)and (3)using IQM, the average zinc on the product was reduced to 2.9 mils (74 microns). Also including the ash improvement the %GZU became 6.0%. The product quality is second to NONE. Their zinc spatter is nil. These excellent results occurred for several months and then the %GZU increased to 8%. The only change was that the flux temperature went down (boiler problems) to about 120 °F average. Their quadraflux baumé is 13. INTERESTING to say the least.
Regards,
Galvanizing Consultant - Hot Springs, South Dakota, USA
Q. Sir,
I followed discussion between you and learnt very much from it. I am also struggling with heavy dross formation. What I think necessary to reduce the dross is continuous overflow of water in rinse tanks. A pipe of 2" or 1.1/2" should run through the entire length of tank at the bottom so that fresh water will enter at bottom and iron particles will move up and go to the drain with overflowing water. If possible clean alternate water tank everyday.
Next process is regular flux filtration in which I have failed to get desired result. I need to know if I have a flux bath of approx. 10,000 ltrs and iron content is 3% then how should I calculate the quantity of hydrogen peroxide and ammonium hydroxide to be added in to the bath to effectively reduce the fe content. What should be the temperature and pH during the process and what should be the reaction/settling time before filtering through filter press.
Another query is that if I continuously pass the flux solution throgh the filter press then what amount of above chemicals should be added per day to effectively remove fe particles.
regards
pipes manufacturing - Murbad, Maharashtra, India
2006
A. Atul,
Continuous rinse or daily dumping of rinse is not allowed in North America. A wetting agent that reduces surface tension from 80 dynes/sq cm to 30 dynes/sq cm at a 0.03% concentration will reduce carried over acid and carried over rinse (to flux tank) down to 1/4 of its original volume. I doubt if this wetting agent is available in India. Using this wetting agent greatly slows iron build up in flux and greatly reduces flux usage. Most carry over is from the 12 inclined planes on the outside of the bundled pipes due to capillary liquid where the pipes touch.
For 10,000 liters of flux and assuming the iron (Fe+2 only) was titrated with dichromate (not permanganate), the %iron based on a density of 1.14 grams/mL, then the amounts of aqua ammonia (ammonium hydroxide at 26 deg. Be', lighter than water) and 35% hydrogen peroxide are: 900 liters of aqua ammonia and 300 liters of hydrogen peroxide.
Unfortunately this flux is too contaminated to purify and recovery will be very low (likely only 10% to 20% for gravity settling which will take at least 48 hours). With a filter press coated first with diatomacious earth (as a slurry) recovery could approach 80%. pH must be between 5 and 5.5. Portions of the ammonium hydroxide and hydrogen peroxide would be added, one at a time with the ammonium hydroxide always going first. I do not think you will be successful without training, although you might be if you worked on a small volume in the lab first. Best temperature is 70 °C or above. A pH meter or paper do not work in flux.
I recommend a flux change out and attaining the wetting agent you need. Virtually all local wetting agents are NOT compatible with galvanizing.
Regards,
Galvanizing Consultant - Hot Springs, South Dakota, USA
Q. Dr. Cook and others,
In a number of threads, the statement has been made that "pH meters or papers do not work in flux solutions" - and a few other solutions -- but nevertheless a quite narrow pH range has been specified for whatever process is under discussion.
Will you advise what other technique is available for determining pH if neither pH meters nor indicator papers are satisfactory, please?
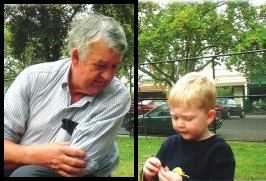
Bill Reynolds [deceased]
consultant metallurgist - Ballarat, Victoria, Australia
We sadly relate the news that Bill passed away on Jan. 29, 2010.
2006
A. Bill,
Certain organic dye indicators work very well in zinc ammonium chloride flux solutions. The exact colors depend heavily on the ammonium chloride/zinc chloride ratio (ACN) and to a minor extent the concentration. By extensive experience the best working pH can be determined as defined by these organic dyes. That pH is 4.2. After 33 years experience these dyes show a great deal about the composition of the flux.
The problems with papers are that they are not intended for these types of solutions and the zinc chloride tends to turn the paper black. Various mfgrs. of paper use combinations of organic dyes that respond to pH and to zinc chloride and to ammonium chloride and to iron chloride, etc.
pH meters quickly "plug up" their membranes and in no way represent "pH" of a flux solution. In fact the very definition of pH is "lost" because often flux is so concentrated. pH meters are useful in very dilute solutions only and even then often suffer from diffusion problems or precipitation problems inside the electrodes. I tried very hard for five years and finally gave up because the pH electrodes simply were destroyed even by being put into a flux solution one time.
30 years ago a galvanizer had 1.4% sulphate and 0.4% iron (Fe+2) in his flux and he was having many black (bare) spots. This captive galvanizer was in his main "season" and did not have time to purify his flux. At the time I was doing research on pH and found his flux was about pH 5.5 (a pH meter showed 4.5). Using the organic dye I titrated with 1:10 HCl and determined that he needed 25 gallons of conc. HCl in his 5,000 gallon flux tank. Black (bare) spots stopped immediately and did not reappear for the full season. Case Closed.
Regards,
Galvanizing Consultant - Hot Springs, South Dakota, USA
Q. Dr Cook,
Thanks for your comprehensive explanation.
Can you tell us the name of the organic dye that you found to be satisfactory?
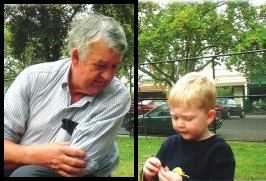
Bill Reynolds [deceased]
consultant metallurgist - Ballarat, Victoria, Australia
We sadly relate the news that Bill passed away on Jan. 29, 2010.
A. Bill,
You are very knowledgeable in stainless steels. Do you also do work in hot dip galvanizing?
In this instance I must respectfully decline your request for the identification and specific uses of the organic dyes that I have found work for galvanizing fluxes. I also use some of these dyes to control the pH of hex chrome solutions. Now that trivalent chrome is being more widely used, I look forward to using some of these dyes for pH control in trivalent chrome or other post treatment solutions. Most galvanizers control the pH of their flux and chromate every day.
Regards,
Galvanizing Consultant - Hot Springs, South Dakota, USA
Thanks Dr. Cook. All of us can afford to share some of what we know, as you have generously done. Few of us can afford to share everything we know :-)
Regards,
Ted Mooney, P.E. RET
Striving to live Aloha
finishing.com - Pine Beach, New Jersey
Q. Dear Sir,
I think I will be immensely benefitted from this discussion, I have already initiated the procedure for lab trials. I will get the 35% hydrogen peroxide easily but it is difficult to specify 26 deg be' ammonium hydroxide. Please explain specification of ammonium hydroxide in simpler way or explain current specification.
regards
ERW pipes - Maharashtra, India
2006
A. Atul,
Ammonium hydroxide and aqua ammonia are two names for the same chemical. 26 degree baumé (lighter than water) has a specific gravity of 0.900 (28 percent W/W expressed as NH3 in a water solution). The CRC Handbook of Chemistry & Physics
[adv: on
Amazon &
AbeBooks &
eBay affil links]
gives details of this solution.
Hydrogen peroxide is extremely dangerous, producing white, extremely painful and dangerous burns on human flesh. It REQUIRES rubber protection clothing and shoes. Ammonium hydroxide produces extensive fumes of lighter than air ammonia gas and proper respirators are REQUIRED. No one can be working on the cranes during flux purification.
You have no way to measure or control pH. Iron III hydroxide is extremely difficult to settle or filter press. An industrial, continuous centrifuge possibly could work. If you have a high baumé flux (likely this is the case), then yield of usable flux could be zero. I expect that chemically, economically, and safety-wise trying to purify this flux is a BIG mistake. There are many essential flux purification "details" that I have not disclosed. I recommend that you concentrate on using means (suitable draining agent in acid, rinse, and flux) to EXTEND the lifetime of future flux solutions. Also there are ways to make a contaminated flux solution perform much better.
I am very concerned that your workers may be injured because of lack of full knowledge on how to protect themselves from the hazards of these very dangerous flux purification chemicals. I now regret giving out very limited information that is likely to be incorrectly used. You need extensive help from a qualified person.
Regards,
Galvanizing Consultant - Hot Springs, South Dakota, USA
![]() |
One reason that everyone constantly suggests haz-mat training for all chemical workers is to reinforce the simple concept that if you are not trained in the specific chemistry and the specific operation, and are not wearing the appropriate personnel protective equipment, and do not have appropriate safety equipment and personnel on hand, and have not prepared proper contingency plans, you don't do it! And it's not that a quick haz-mat training course teaches you how to do anything & everything safely ... it's exactly the opposite; it teaches you NOT to do it UNLESS you are trained to do that specific operation safely :-) I taught "Safety in Electroplating" for many years and would always start the class with this simple question: "A well-trained worker (will) (will not) ever do unsafe things?". Perhaps readers of this thread will mull over the question and realize that if they do not instantly know the answer to the first & simplest safety question with 100% certainty, they should take a Haz-Mat safety course before risking life & limb :-) Regards, ![]() Ted Mooney, P.E. RET Striving to live Aloha finishing.com - Pine Beach, New Jersey ---- |
Q. Hi
Calculating of Al% for charge in zinc pot. We have a galvanizing line and we want to know how to calculate exactly aluminum that has to charge.
- Isfahan, Iran
2006
A. Sir:
I do not fully understand your question. If you run a "dry" kettle (no top flux) then the dry skimmings will contain 100 times more aluminum than the aluminum content of the zinc bath. Thus you will need almost daily additions of small amounts of aluminum to your zinc bath. I prefer rather low aluminum in zinc in general galvanizing of only 0.001%. I get brightness by other means. This gives excellent product that resists "white" rust.
Regards,
Galvanizing Consultant - Hot Springs, South Dakota, USA
Q. Dear sir,
We are testing our flux daily by titration method and the test is telling us to add ammonia. Our flux is zinc ammonia chloride and heated to 75 deg. The pH reading by machine is 5.3. What happens if this level is around 6, and does adding ammonia only reduce the levels of HCl?
galvanising - Melbourne, Victoria, Australia
June 21, 2013
Iron Content Calculation for Galvanizing Preflux
Q. Dear Sir,
My iron content of preflux solution is 1.68 gm/lt. but still the dross generation is very high.
I think I made some wrong calculation for iron content. Kindly provide the calculation steps for iron content in Preflux solution.
Thanks
Quality Engineer - Rajasthan, India
June 6, 2015
Hi VJ and other posters.
Chemical analysis isn't my strong suit and I know little about galvanizing. But from posting a quarter million reader questions & monitoring the results they draw as my full time job for over 20 years now, my advise is: take the time to explain what procedure you used to obtain that result :-)
When readers see something in error, they quickly get very interested!
But when they are asked to post a procedure, and they know it will draw ongoing requests for clarifications, leaving them holding the bag, they usually ignore the request. Thanks!
Regards,
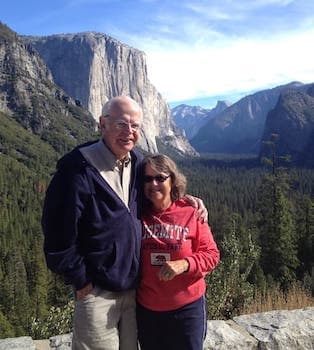
Ted Mooney, P.E. RET
Striving to live Aloha
finishing.com - Pine Beach, New Jersey
Q. We are using double salt flux. How can I calculate the zinc chloride and ammonium chloride concentration in the flux? Can you tell me some titration process for flux? I need your help for this.
ANKUSH HARDE- ABU DHABI,UAE
July 13, 2016
A. Hi Ankush. Titration methods are available, but the question is whether they are of value, or only generate random results :-)
Please see Dr. Thomas Cooks' entry on this subject on letter 51513, then read the rest of that thread and decide. Good luck!
Regards,
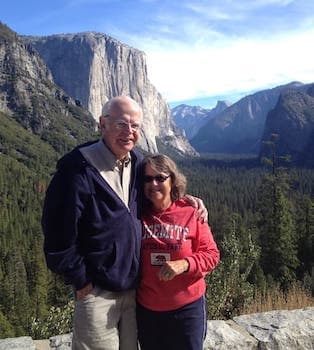
Ted Mooney, P.E. RET
Striving to live Aloha
finishing.com - Pine Beach, New Jersey
Q. Thanks sir for your help. We want titration method for the value that we can get proper value for the flux composition.
Ankush Harde [returning]- abu dhabi ,UAE
Q. Hello honourable gentlemen,
I went to get rid of iron in a Flux bath as commonly well known, H2O2, NH4OH etc. It worked pretty well but by the time of transferring the clean flux to the new container, the worker just fell asleep or something happened that he pumped out the sludge containing the Fe2O3 and pp products ... mixing it again with the clean FLUX! It looks like clay with water!
Now, due to the workload, it is just possible to stop until weekend and as I read, Dr. Cook suggest to let it at least 48 hours in order to settle the iron again! it has been done but just 30 hours but the time was not enough to settle the iron again.
What can we do now? How long do we have to proceed?I am worried about the reversibility of the reaction!
the Thicknesses and the material quality is fine.
Thanks a lot in advance for your time and help!
Asociacion Mexicana de Galvanizadores - Mexico City, Mexico
August 30, 2017
Q. Dear Sirs,
I need info: does anyone know about flux filtering iron machine. We are planning to buy a unit to filter our current flux. Does this filtering system really work? What are the percentage of filtering the flux?
Thanks/Regards
Param
- Subang, Selangor, Malaysia
February 1, 2018
Ed. note: This RFQ is outdated, but technical replies are welcome, and readers are encouraged to post their own RFQs. But no public commercial suggestions please ( huh? why?).
Q. A flux cleaning machine will likely benefit your operation in several ways. It will reduce Fe in the flux resulting in lower zinc consumption. Drying the work after fluxing will be easier, and that also reduces consumption through splash oxidation. Wetting will be better in the zinc, so improving quality, flux ratio will be better (ratio of ammonium chloride to zinc chloride) as will be the pH. But while the chemistry of such machines is easy, building a robust one that will be easy to operate will not be easy, so make sure you see one that's been operating a few years before you buy.
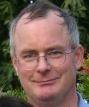
Geoff Crowley
Crithwood Ltd.
Westfield, Scotland, UK
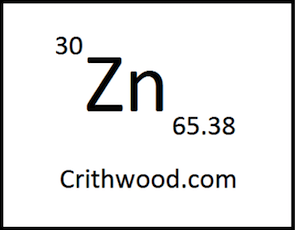
Q. Sir How to Reduce iron content in the flux, other than addition of H2O2.
I Am MR ARJUN VAIDYA WORKING IN A BAJAJ ELECTRICALS LTD AS A MANAGER GALVANIZING. WE HAVE HOT DIP GALVANIZING PLANT FOR THE GALVANIZING TRANSMISSION LINE TOWER AND OCT POLES AND HIGH MASTS.
WE ARE USING TRIPLE SALT FLUX WITH 46% ZINC CHLORIDE AND AMMONIUM CHLORIDE 54%. TRYING TO MAINTAIN IRON CONTENT BELOW 5 GM/LTR BUT VERY DIFFICULT CAN YOU PLEASE SUGGEST THE SOLUTION TO MINIMIZE THE IRON CONTENT?
BAJAJ ELECTRICALS LTD - RANJANGAON ,SHIRUR , India
August 31, 2019
A. Sir, there is a new method to oxidize Fe+2 to Fe+3 in flux that does NOT use peroxide.
Regards,
Galvanizing Consultant - Hot Springs, South Dakota
Q, A, or Comment on THIS thread -or- Start a NEW Thread