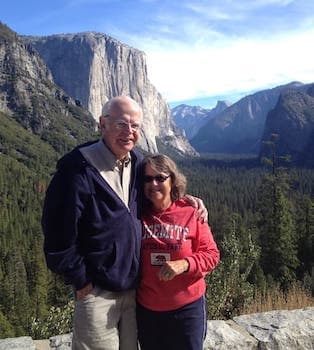
Curated with aloha by
Ted Mooney, P.E. RET
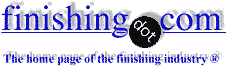
The authoritative public forum
for Metal Finishing 1989-2025
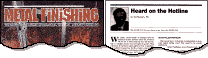
-----
Anodizing of Aluminum Screws and Threads
Q. Hi,
here is a question that I wasn't able to find any answer yet.
I have small aluminum plates which have 10 threaded holes in them. After anodizing, when I do the continuity test with my two meter probes on the flat surface, the circuit shows open, which is good. When I put my probes on the threaded openings there is continuity. For what reason the anodizing process hasn't coated these openings?
Thanks
- Quebec, Canada
September 3, 2021
A.
Hi Leo,
There are at least 2 possible explanations for the lack of coating on the threads in the holes. One is if the holes are too small the anodize solution is not able to enter and do its job be it because the hole is simply too small or if air does not allow for entry of the solution.
A second reason can be because anodic coating does not generally build up on a threaded surface. The edge of the thread basically is sharp or comes to a point as opposed to the flat surface of the plate. an edge does not usually pick up the coating that is unless it has been radiused. A coarse flat thread however will pick up anodize.
Hope this helps.
supervisor - Cicero, Illinois
Saporito Finishing Co.

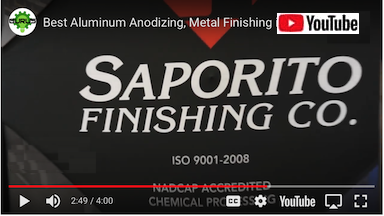
September 14, 2021
Hi Philip,
Thanks for your input.
My holes are M2.5, 2.4mm deep. I believe the electrolyte is reaching inside without problem, there is enough space. Next time, I will do some closer test. Some same parts in my lot anodized the threads. I may not had a good connection on some and the anodize had some facility to deposit on large surface but not on the threads. It requires more tests from me and I will get back later with more details on the outcome. I will be looking more closely on your second suggestion.
Thanks for your kind help.
Regards,
Leo
- Quebec, Canada
September 19, 2021
⇩ Related postings, oldest first ⇩
2002
RFQ: I need to source an aluminum screw supplier.
Aluminum screws should be anodized or finish treated desired material for screw 6061-T6 aluminum.
Screw sizes:10-24 UNC x 2 inches long(5000 pieces) 1/4-20 UNC x 1 1/2 inches long(1200 pieces.
Screws must be able to withstand a torque of 11.4 ft lbs for the 1/4-20 screws and 6.6 ft lbs for the 10-24 screws. Head of screw can be hex head, would prefer socket head cap screw.
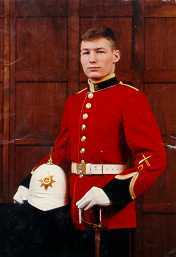
Rob Connor
- St. Catharines, Ontario, Canada
Ed. note: This RFQ is outdated, but technical replies are welcome, and readers are encouraged to post their own RFQs. But no public commercial suggestions please ( huh? why?).
Q. I am an engineer dealing with a problem of M3 threads stripping. The threads are tapped into an aluminum plate with an extrude feature. There are only about 3 full threads in the extrude feature. The part is black anodized after the extrude & tap operation and I am wondering if the black anodize is embrittling the threads to weaken them causing a high percentage of failures (stripping).
Mahesh Mistrytelecom equipment - Pearl River, New York
2006
A. No. But, you are removing some of the metal in the pre anodize steps and then growing aluminum oxide so it will actually be slightly smaller diameter than original. Your problem is the bolt is crushing the anodize leaving a larger diameter which allows the bolt to pull thru. Consider using helicoils after anodizing (a non tapped hole).
3 threads is a minimum for good strength in optimum conditions and you do not have optimum. Alternatively, you could use a torque clutch to tighten to a torque that would hold and would not strip until the first time that the bolt is removed and reinstalled. PEM fittings is an unattractive but functional alternative for black anodized.
- Navarre, Florida
2006
A. It can happen, especially with thicker anodic coatings (which black dye often requires).
Many regular responders to this site have stated before that when possible you should avoid anodizing threads, a few state that you should never do it at all. I am one of the exceptions in that I will say it can be done and that my company does it on a regular basis - but we specialize in bulk anodizing and our process is tweaked a bit as a result. One of the beneficial results of how we run our process is that we have NEVER had a customer reject an order or even complain about thread brittleness. I haven't done sufficient testing to know exactly WHAT aspect of our process it is that allows this, but I have my suspicions. Unfortunately, a lot of the things that we do aren't applicable to most other anodizers and the few that are I am not at liberty to share.
Try, if at all possible, to use a thinner anodize - that seems to help. Otherwise, look into masking the area with the thread. I don't know for certain, but I suspect that alloy selection plays a role as well; you may want to see if it is possible to choose a different alloy for the parts. Also, more threads would help spread the force around - is it possible to increase the number of threads?
Sorry I couldn't offer more clear advice, but in short - yeah, the anodize could be causing it.
Good luck!
Compton, California, USA
2006
A. In all actuality YES the anodic coating Can (under the right conditions) embrittle the threads of an aluminum extrusion.
-Depends on the thickness that was applied to the surface.
Being that the buildup of the anodize is perpendicular to the aluminum surface, if a Full mil was plated onto the part then there was .5 mil of penetration and .5 mil of buildup on the surface.
the .5 mil on the surface is Aluminum Oxide.. Very hard and has great lubricity however the structure of the coating is Porous. meaning millions of micro sized holes.
The answer is YES under the right conditions Anodizing can embrittle threaded holes and Lead to stripping out of holes. However If someone is over tightening the bolt/etc. well.. You get the Idea.
I would suggest going with a Hard Coat (type 3 anodize) or explore other options in regard to the Tapped holes.
I hope you find what you are looking for.
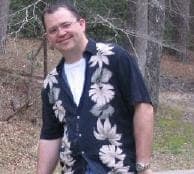
Ryan Cook
Toccoa, Georgia
2006
Q. Ryan, you would go with a hardcoat (thicker) anodize? I would think that the increased amount of aluminum oxide would exaggerate the problem, not relieve it... or am I missing something (like the type III conditions resulting in a denser oxide)?
Jim GorsichCompton, California, USA
2006
A. I'm thinking that the denser oxide would hold up better under a threaded hole condition. smaller pores.. more surface area for the bolt to hold onto. Thickness would definitely come into play and could be tricky BUT I think the parts are being over etched.
If they are removing to much material in the etch, it is likely you could have them reduce the etch time or eliminate it all together and the type 2 buildup would suffice .
I may have shot my Idea out too fast about the type 3..
But it would work either way.
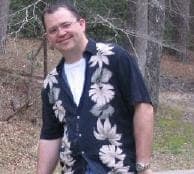
Ryan Cook
Toccoa, Georgia
2006
A. According to my experiments, M3 thread should be masked before anodizing. It is too delicate and can be damaged while coating. Larger threads (M5 and above) are ok for anodizing. Also it is recommended to use helicoil on such small Aluminum threads like M3.
eran yaniv- PETACH TIKVA, ISRAEL, ISRAEL
September 16, 2013
Hard anodic coating before inserting Helicoil?
May 3, 2017Q. We are trying to design a system which would periodically (there isn't a certain period) goes under sea water and stays for about 3 months at maximum (it could be only 1 day depending on the job). Customer wants the same black color for all products. Material is 6061-T6. We are discussing about corrosion protection of the system. We read through MIL-A-8625 and searched the web and come to a conclusion with some questions in our minds. Our solution would be Type-3 coating with two step electrolytic dying" and sealing and then inserting helicoils.
1- Is it possible to make Type-3 coating with "two step electrolytic dying" (architectural anodizing) for fade-resistant black color and with sealing afterwards. If not what would you suggest?
(reference site: http://www.omwcorp.com/understandingano/anoindex.html)
2- How could we protect the helicoil mounting holes from corrosion, if we put the helicoil in its position and mask it before anodizing? This way there would be some bare aluminum surface within the hole directly in contact with sea water. Is it possible to first anodize complete part with holes included without helicoils in position and put helicoil then?
3- If it isn't possible to anodize the mounting thread of helicoil, what kind of helicoil can we use to avoid galvanic corrosion? I found a helicoil with phosphor bronze material or primer free II coating. Could these be a solution?
(reference site: http://www.stanleyengineeredfastening.com/brands/heli-coil/screw-thread-inserts/materials-coatings-platings)
Thank you very much for your responses, in advance
Product designer - Istanbul / Turkey
A. My personal opinion is that no anodizing process will solve your problem, since the process of the insertion of the helicoil itself has a potential to damage the anodizing layer, and then, during normal use, when you tighten a bolt in that hole, the bolt will pull on the coil and the coil on the anodizing coating, which will result in the oxide layer cracking and will lead to corrosion.
So you either have use some special type bolt that can provide a seal using some type of o-ring, or you can try loctite thread sealing products, they will most likely work pretty well (there even was one type that could be applied after the bolt has been tightened), but are a bit of a hassle to work with, especially if the bolt in that hole has to be removed and reinstalled multiple times during the service life of the part, which is why one would actually use a helicoil in a threaded hole in aluminum.
That being said, I've seen parts in motorsport applications (sometimes they drive on snow/ice roads sprayed with salt, and other times they drive on tracks that use salt/water mixes as a dust prevention measure, so - salt is present) that survive in such an environment without any difficulties, of course some corrosion is present around the threaded hole because of repeated loosening/tightening that is damaging anodizing, but no one expects those parts to last for decades anyway.
This is just my personal opinion
- Riga, Latvia
May 4, 2017
A. Threading soft material should always be done with course thread. This may help. Another consideration could be torque spec may have to be tested on an anodised hole. Since the surface is more slippery it may be the same torque but will be providing a lot more thrust on the threads than only three threads can handle. A threaded hole should be as deep as the diameter of the bolt in like materials for maximum hold if used once. If the base material is softer it needs more threads, and if it is for repeated use it needs more threads.
MARCEL TOEWS- Saskatoon Sask., Canada
December 17, 2017

Q, A, or Comment on THIS thread -or- Start a NEW Thread