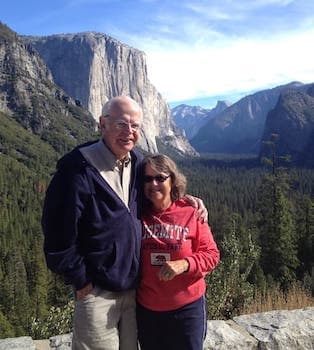
Curated with aloha by
Ted Mooney, P.E. RET
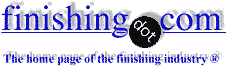
The authoritative public forum
for Metal Finishing 1989-2025
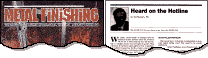
-----
Nickel Sulphamate Electroforming Problems
Q. Hello Ladies and Gentlemen!
We are working on the embossed hologram project at National Laboratory. One of the processes is Electroforming Process. We have used Nickel Sulphamate Bath as electrolyte, Nickel S-round, SNAC (Sulphamate Nickel Acid Compound), SNAP (Sulphamate Nickel Anti-Pit), Boric Acid. We had bought these chemicals from a company supplier.
Now, the problem is that we don't know about SNAC and SNAP, what are chemical names? Is SNAC a Sulfamic Acid or another? And can we use the other chemicals for the lower pH instead of SNAC. What is chemical for SNAP? We want to buy them in easy way.
For Boric Acid Bag, Why the bag is so hard and crystal hold outside around? How do we know that we should to add or change the boric acid in the bag?
Would you like to help us? Have you another comments? We are waiting for your HELP at all time.
Million Thanks, A little researcher.
Nisaporn Kiettipaisalsophonelectro-optics lab - Bangkok, Thailand
1999
![]() ![]() |
A. I don't know what the chemicals are, but most likely they are proprietary mixtures of surfactants, etc. specifically developed for the sulphamate baths. In that case you won't have much luck trying to track down the actual chemicals used. Don PiettINCO Ltd - Thompson, mb, Canada 1999 A. SNAC IS JUST A MORE PURIFIED SULFAMIC ACID. YOU CAN USE GENERIC KIND IF YOU WANT. CHEAPER TO USE. AS FAR AS THE SNAP, NOT SURE OF ALL THE INGREDIENTS, SURE ITS A SACHARIN BASE. I STILL USE THE VENDORS. THEN YOU KNOW ITS THE RIGHT BLEND. I HAVE USED A DILUTED SULF (25%) IN SULF NI STRIKE BATHS. IT TAKES A LOT OF SNAC TO LOWER PH UNLESS ITS JUST A LITTLE OVER 1.5, AND I'VE NEVER HAD ANY PROB WITH IT. BUT I RECOMMEND STILL USING SNAC IN THE SULF PLATING BATH. DOESN'T TAKE MUCH TO LOWER PH WITH IT. DEPENDS ON THE SIZE OF THE TANK, BUT I'VE SEEN FOR EVERY 100 GAL OF BATH, TAKES AROUND AND OUNCE OF SNAC TO LOWER PH ABOUT .2 AS FAR AS THE BORIC, SOUNDS LIKE YOU HAVE LOTS OF BORIC IN THE BATH ALREADY.I RUN 6 OZ/GAL OF BORIC IN THE BATH, AND NEVER HAD A PITTING PROBLEM. MORE THAN THAT, IT WILL CRYSTALLIZE WHEN THE BATH IS COLD. FOR SULF NI STRIKE, I RUN AROUND 3-4 OZ/GAL, CANT GET ANYMORE THAN THAT IN SOLUTION AT THE RUNNING TEMP OF 90-100 DEGREES ANYWAY. I TRY IT KEEP AT LEAST 3.3 OZ/GAL, BUT HAS GOT AS LOW AS 2.8 AND NO PROB. TOO HIGH CAN GIVE YOU ROUGHNESS, CAUSE IT CANT DISSOLVE ANYMORE AT THAT TEMP. IF YOU HAVE NO WAY OF TESTING THE BORIC, JUST HAVE A NAPPED POLY BAG IN THE BATH WITH BORIC IN IT AND IF IT STARTS TO CRYSTALLIZE WHEN THE BATH IS COOLED DOWN AT ROOM TEMP, YOU KNOW YOU HAVE ENOUGH IN IT JOHN [last name deleted for privacy by Editor]PLATING Shop - FRIDLEY Minnesota 1999 A. Hi, Nisaporn. You may be able use sodium lauryl sulphate as your wetting agent (anti-pit). If anyone knew exactly what SNAC and SNAP were, it might be unethical for them to tell you, depending on how they came to know, since these are proprietaries. The boric acid dissolves up to its solubility limit at the temperature in question, and if you keep the tank a consistent temperature I don't think it will build the hard crust you describe. Normally you don't replace the bag until it is empty. But many people choose to NOT operate the way you describe, and rather to put only the required amount of boric acid into the bag in the first place. Good luck. ![]() Ted Mooney, P.E. Striving to live Aloha finishing.com - Pine Beach, New Jersey 1999 |
Q. To: Nisaporn Kiettipaisalsophon
Help me please! As well as you we are trying to make a Laboratory emboss hologram. Can you help me sending me a guide step by step to make the silvering and the electroform?
Thank you for all.
A little Argentinean researcher.
Alan Gomeztechnical solutions - Bs. As., Argentina
2001
A. Hi Alan. It's not that people don't want to help, but I have 2 full bookcases of plating books -- it just isn't possible to tell people how to do silvering and electroforming in a paragraph. Sorry. All anyone can try to do is try to respond to individual detailed questions, and suggest that you hook up with a supplier of electroforming solutions as they can often give you tech data sheets and provide guidance and analysis services for you.
To start with step 1 though, study the brashear process used for making mirrors, as applying this 2-component silvering solution to metallize the master is the first step. You probably have to spray it while your master is on a spin table because you have to hold the layer very thin. If you are associated with a university, it is also possible to apply the metallization layer by evaporation. After you have confidence that you can properly metallize a master you can move on to the next step. Good luck!
Regards,
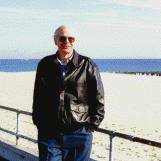
Ted Mooney, P.E.
Striving to live Aloha
finishing.com - Pine Beach, New Jersey
June 30, 2014
Q. Hi
We are a growing Flexible Printing Factory and would like to expand our business in holography processing material.
We use the electroplating tank to make a copy of the holography master shim.
We have the following problems during duplication process
1. Severe pitting problem on the edge of the duplicated shim.
2. Extreme adhesion between master shim and duplicated shim for the second to third electroplating process using the same master shim.
3. Thick layer deposit (50-70 micron) on the edge of duplicated shim while thin layer deposit occurs (20-30 micron)on the center of duplicated shim.
For your information we have taken the following action.
1. Added powdered active carbon and peroxide into the tank and let agitated for about 12 hours.And the next day we filtered the tank.
2. Checked the electrical contact and wiring
- Semarang, Central Java, Indonesia
Nickel sulphamate bath to make hologram
Q. Hello,
In my nickel sulphamate bath (60 L) I make nickel shims of a nickel master. The shims are bursting when I put them in the machine and tighten them with screws. I thought they could be very hard so I put sulfamic acid (300g) but the problem continued and then the plates got very weak. So I put saccharin sodium (2.5g) to harden it but the problem still persisted.
I think it could be the stress of the shim that would be causing this but I'm not sure.
Please help me.
Thank you
- Maringa.parana, Brazil
February 13, 2017
Ed. note: This RFQ is outdated, but technical replies are welcome, and readers are encouraged to post their own RFQs. But no public commercial suggestions please ( huh? why?).
A. Joao,
It's hard to say exactly what is causing the failure based on your post. Is this a process that had worked fine for a period of time then suddenly started to fail? Or is it a newly implemented process that never worked well from the start? How thick is your finial form and what sort of stress is it being subjected to? Stamping? heat? where are the "screws" being set and why? without the details we can't begin to determine a cause to your problems.
It sounds like you reduced your Ph with sulfamic acid to soften the deposit then tried to reverse this by adding sodium saccharin? Again don't know the composition of your sulfamate but in most sulfamate baths hardness, as well as tensile strength decreases with a drop in Ph. Watch your Ni metal content as well as the chloride. These constituents tend to weaken the deposit once they swing above the higher end of the operating window. Keeping your temperature and Ph on the high side of the recommended operating window can help with strength.
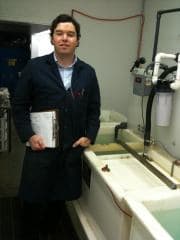
Chance Dunstan
Electroplating/Forming/Coating Manager
Placerville, California USA
February 14, 2017
Q, A, or Comment on THIS thread -or- Start a NEW Thread